아래에 관리 공작 기계를 이러한 메커니즘이 처리의 기술 주기를 수행하도록 하는 메커니즘에 대한 일련의 영향으로 이해하는 것이 일반적입니다. 제어 시스템- 이러한 효과를 구현하는 장치 또는 장치 세트.
수동 관리는 작업주기의 특정 요소를 사용하기로 결정한 사람이 기계 운영자라는 사실에 기반합니다. 운영자는 내린 결정에 따라 기계의 해당 메커니즘을 켜고 작업 매개 변수를 설정합니다.
수동 제어 작업은 다양한 목적을 위한 비자동 범용 및 특수 기계와 자동 기계 모두에서 수행됩니다. V 자동 기계수동 제어는 작업 주기의 조정 모드 및 특수 요소를 구현하는 데 사용됩니다.
자동 기계에서 수동 제어는 종종 집행 기관의 위치 센서에서 오는 정보의 디지털 표시와 결합됩니다.
자동 제어 작업주기 요소의 사용에 대한 결정은 운영자의 참여없이 제어 시스템에 의해 이루어진다는 사실에 있습니다. 그녀는 또한 기계의 메커니즘을 켜고 끄는 명령을 내리고 작동을 제어합니다.
처리 주기 각 공작물을 처리하는 동안 반복되는 작업 몸체의 이동 세트라고합니다. 기계 사이클에서 작업 본체의 복잡한 움직임은 특정 순서, 즉 프로그램에 따라 수행됩니다.
제어 프로그램 - 이것은 특정 공작물을 처리하기 위한 기계의 기능을 위해 주어진 알고리즘에 해당하는 명령 세트입니다.
연산 구현 절차에 대한 명확한 설명과 함께 목표(문제 해결)를 달성하는 방법의 이름을 지정합니다.
기능적 목적에 따라 자동 제어는 다음과 같이 나눌 수 있습니다.
일정한 반복 처리 주기의 제어(예: 다중 스핀들 파워 헤드의 이동 주기를 수행하여 밀링, 드릴링, 보링 및 나사 절삭 작업을 수행하는 모듈식 기계 제어);
개별 재료 모델의 형태로 설정된 가변 자동 사이클의 제어 - 각 사이클(복사기, 캠 세트, 정지 시스템 등)에 대한 아날로그 등
프로그램이 하나 또는 다른 매체에 기록된 정보 배열의 형태로 지정되는 CNC. CNC 기계에 대한 제어 정보는 개별적이며 제어 프로세스에서의 처리는 디지털 방식으로 수행됩니다.
순환 프로그램 제어(CPU)
사이클링 시스템 프로그램 제어(CPU)를 사용하면 기계 주기, 처리 모드 및 도구 변경을 부분적으로 또는 완전히 프로그래밍할 수 있을 뿐만 아니라 기계의 집행 기관의 이동량을 설정(정지 사전 조정 사용)할 수 있습니다. 이것은 아날로그 폐루프 제어 시스템(그림 1)이며 충분히 높은 유연성을 가지고 있습니다. 주기.
그림 1– 주기적인 프로그램 제어 장치
싸이클 프로그래머는 프로그램을 설정하기 위한 블록 1과 단계별 입력을 위한 블록 2를 포함합니다(프로그램 단계는 제어 시스템에 동시에 입력되는 프로그램의 일부입니다). 블록 1에서 정보는 기계의 사이클을 제어하기 위한 블록 3과 제어 신호를 변환하기 위한 블록 4로 구성된 자동화 회로로 들어갑니다. 일반적으로 전자기 릴레이에서 수행되는 자동화 회로는 사이클 프로그래머의 작업을 기계 및 센서의 집행 기관과 조정합니다. 피드백; 팀을 강화하고 증가시킵니다. 여러 논리적 기능을 수행할 수 있습니다(예: 고정 주기 실행 보장). 블록 3에서 신호는 프로그램에 의해 지정된 명령의 처리를 보장하는 액추에이터에 들어가고 액추에이터 5(기계의 집행 기관, 전자석, 클러치 등의 드라이브)를 포함합니다. 후자는 프로그램의 단계를 수행합니다. 센서 7은 처리의 끝을 제어하고 블록 4를 통해 블록 2에 프로그램의 다음 단계를 켜도록 지시합니다. 센서 7은 처리의 끝을 제어하고 블록 4를 통해 블록 2에 프로그램의 다음 단계를 켜도록 지시합니다. 프로그램 단계의 끝을 제어하기 위해 여행 스위치 또는 시간 릴레이가 자주 사용됩니다.
수치 형태의 순환 제어 장치에서 프로그램에는 처리 모드의 주기에 대한 정보만 포함되며 작업체의 이동량은 정지를 설정하여 설정됩니다.
CPU 시스템의 장점은 설계 및 유지 관리가 간단하고 비용이 저렴하다는 것입니다. 단점은 스톱과 캠의 치수 조정이 복잡하다는 것입니다.
단순한 기하학적 모양의 부품을 대량으로 대량 생산하는 조건에서는 CNC 기계를 사용하는 것이 좋습니다. CNC 시스템에는 터릿 터닝, 터닝 밀링, 수직 드릴링 머신, 모듈러 머신, 산업용 로봇(IR) 등이 장착되어 있습니다.
CPU 시스템(그림 2)에는 사이클 프로그래머, 자동화 회로, 액추에이터 및 피드백 장치가 포함됩니다. CPU 자체는 사이클 프로그래머와 자동화 회로로 구성됩니다.
그림 2 -
사이버네틱스, 전자공학, 컴퓨터 기술 및 계측의 성과를 기반으로 근본적으로 새로운 소프트웨어 제어 시스템, 즉 공작 기계 제작에 널리 사용되는 CNC 시스템이 개발되었습니다. 이러한 시스템에서 기계 집행 기관의 각 스트로크 값은 숫자를 사용하여 설정됩니다. 각 정보 단위는 CNC 시스템의 해상도 또는 충동의 가격이라고 하는 일정량만큼 집행 기관의 개별적인 움직임에 해당합니다. 일정 한도 내에서 집행 기관은 결의의 배수인 금액만큼 이동할 수 있습니다. 필요한 변위 L을 수행하기 위해 드라이브 입력에 적용해야 하는 펄스 수는 다음 공식에 의해 결정됩니다. N = L/q, 어디 큐충동의 대가이다. 정보매체(펀칭테이프, 자기테이프 등)에 일정한 부호체계로 쓰여진 숫자 N은 차원정보의 양을 결정하는 프로그램이다.
CNC 기계에서 기계 집행 기관의 움직임, 이동 속도, 처리 사이클 순서, 절단 모드 및 다양한 보조 기능에 의한 제어(영숫자 코드로 지정된 프로그램에 따라)를 이해합니다.
CNC 시스템 공작 기계로 CNC를 구현하는 데 필요한 특수 장치, 방법 및 도구 세트입니다. CNC 장치(CNC)는 제어 프로그램(CP)에 따라 기계의 집행 기관에서 제어 작업을 실행하도록 설계된 CNC 시스템의 일부입니다.
CNC 시스템의 블록 다이어그램은 그림 3에 나와 있습니다.
상세도 (BH), CNC 기계에서 처리하기 위해 동시에 시스템에 입력 프로그램 준비에스 (SPP)및 기술 준비 시스템 (STP). STP제공 SPP개발된 기술 프로세스, 절단 모드 등의 데이터를 기반으로 제어 프로그램을 개발합니다. (위로).조정자는 에서 개발된 문서에 따라 기계에 고정 장치 및 절단 도구를 설치합니다. STP.공작물의 설치 및 완성품의 제거는 작업자 또는 자동 로더에 의해 수행됩니다. 리더 (SU)프로그램 캐리어에서 정보를 읽습니다. 정보가 갑니다 CNC, 대상 메커니즘에 제어 명령을 발행합니다. (센티미터)가공의 주요 및 보조 운동을 수행하는 기계. 피드백 센서 (도스)정보(작동 장치의 실제 위치 및 이동 속도, 처리된 표면의 실제 크기, 기술 시스템의 열 및 전력 매개변수 등)를 기반으로 이동량을 제어합니다. 센티미터. 기계에는 여러 센티미터,각각은 다음을 포함합니다: 에너지의 원천인 엔진(DV); 옮기다 피,에너지를 변환하여 엔진에서 집행 기관으로 전달하는 역할( 그리고 약); 실제로 그리고 약(테이블, 슬레드, 캘리퍼, 스핀들 등) 사이클의 좌표 이동을 수행합니다.
그림 3– CNC 시스템의 구조도
범용 CNC 시스템은 사용자와 작업자에게 큰 가능성을 제공합니다. 그들은 다른 기계를 포함하여 광범위한 객체 클래스에 프로그래밍하여 적용할 수 있습니다. 선형, 원형, 포물선 등의 모든 유형의 보간과 준비 및 디버깅을 동시에 제공 제어 프로그램대화식 모드에서 기계에 직접. 제어 프로그램은 메모리에 저장되어 처리 중에 읽을 수 있으며, 어떤 경우에는 프로그램 캐리어에서 프로그램을 읽어 프로그램의 예비 입력을 생략할 수 있습니다. CNC 시스템은 프로그램을 편집할 수 있는 충분한 기회가 있으며 콘솔 교정기를 사용하지 않고도 (메모리에서) 자동으로 교정할 수 있는 기능을 제공합니다. 오작동의 원인을 식별하기 위해 노드의 작동을 확인하는 특수 진단 프로그램과 운동학적 체인의 체계적인 오류에 대한 정보를 메모리에 저장하고 재생할 때 이러한 오류를 제거하거나 보상할 가능성이 있다는 점에 유의해야 합니다. 주어진 프로필; 기계의 결합이나 고장을 피하기 위해 처리 영역에 대한 제한을 시스템에 도입할 가능성; 처리가 중단된 지점으로 돌아갑니다. Universal CNC 시스템은 선형 및 극좌표에서 작동하여 예를 들어 수평 밀링 머신에서 수직 밀링 머신용으로 컴파일된 프로그램을 사용할 때 좌표축 변환을 제공합니다.
CNC 장치의 주요 작동 모드는 자동 모드입니다. 제어 프로그램의 자동 처리 과정에서 다양한 복잡성 수준의 광범위한 작업이 해결됩니다. 운영자 콘솔의 버튼 폴링; 운영자 콘솔에 표시하기 위한 데이터 배포 및 발행; 좌표에 의한 현재 위치 계산 및 운영자 콘솔에 대한 정보 발행; 처리 주기 계산; 등거리 오프셋 계산; 교정 도입; 오류 보상; 전자 자동 센서의 심문; 입출력 장치의 준비 신호에 대한 질문; 보간; 속도 계산; 가감속 모드 계산; 폴링 피드백 센서; 기술 장비에 대한 통제 조치 발행; 현재 시간 분석; 제어 프로그램의 시간 제어; 이 프레임에 포함된 프로그램 실행 분석 다음 프레임을 처리하기 위한 초기 정보 준비.
CNC 시스템은 프로그램 캐리어의 유형, NC에서 정보를 인코딩하는 방법 및 CNC 시스템으로 정보를 전송하는 방법에 따라 수정할 수 있습니다.
수치 제어(CNC)- 어떤 매체에 기록된 정보의 배열 형태로 프로그램을 설정하는 컨트롤입니다. CNC 시스템에 대한 제어 정보는 개별적이며 제어 프로세스에서 처리는 디지털 방식으로 수행됩니다. 기술 주기 관리는 거의 보편적으로 다음을 사용하여 수행됩니다. 프로그래머블 로직 컨트롤러, 디지털 전자 컴퓨팅 장치의 원리를 기반으로 구현됩니다.
프로그래머블 컨트롤러
프로그래머블 컨트롤러(PC ) - 장치의 메모리에 저장된 프로그램에 의해 구현된 특정 알고리즘을 사용하여 기계의 전자자동화를 제어하는 장치입니다. 프로그래머블 컨트롤러(커맨더)는 CPU 시스템에서 자율적으로 사용되거나 CPU 시스템의 일부가 될 수 있습니다. 공통 시스템제어 시스템(예: 유연한 생산 모듈 제어 시스템 (GPM)) 뿐만 아니라 자동 라인 등의 장비를 제어하는 데 사용됩니다. 블록 다이어그램은 그림 4에 나와 있습니다.
그림 4- 프로그래머블 컨트롤러의 구조도:
1 - 프로세서; 2 - 타이머 및 카운터; 3 - 재프로그래밍 가능한 메모리; 4 - 랜덤 액세스 메모리(RAM); 5 - 블록 통신을 위한 공통 버스; 6 - CNC 장치 또는 컴퓨터와의 통신 장치; 7 - 프로그래밍을 위해 리모콘을 연결하기 위한 블록; 8 - 입력 모듈; 9 - 입출력 스위치; 10 - 출력 모듈; 11 – 키보드와 디스플레이가 있는 프로그래밍 콘솔.
대부분의 PLC는 전원 공급 장치, 프로세서 장치, 프로그래머블 메모리는 물론 다양한 I/O 모듈을 포함하는 모듈식 설계를 가지고 있습니다. 입력 모듈(입력 모듈)은 다양한 주변 장치(리미트 스위치, 전기 장치, 열 릴레이 등)에서 신호를 생성합니다. 입력 신호에는 일반적으로 "O"와 "1"의 두 가지 레벨이 있습니다. 출력 모듈(출력 모듈)은 기계의 전기 자동화 제어 액추에이터(접촉기, 시동기, 전자석, 신호 램프, 전자 클러치 등)에 신호를 공급합니다. 출력 신호 "1"로 해당 장치는 켜기 명령을 수신하고 출력 신호 "O"로 끄기 명령을 수신합니다.
메모리가 있는 프로세서는 입력 모듈에서 수신한 정보와 메모리에 입력된 제어 알고리즘을 기반으로 출력 모듈을 제어하는 논리적 작업을 해결합니다. 타이머는 작업 주기에 따라 시간 지연을 제공하도록 설정됩니다. PC.카운터는 또한 작업 주기를 구현하는 작업을 해결합니다. PC.
프로그램을 프로세서 메모리에 입력하고 디버깅하는 것은 임시로 연결된 특수 휴대용 리모콘을 사용하여 수행됩니다. PC.프로그램 녹화 장치인 이 리모콘은 여러 기능을 수행할 수 있습니다. PC.프로그램을 녹화하는 과정에서 원격 제어 디스플레이는 제어 대상의 현재 상태를 릴레이 기호 또는 범례로 표시합니다. 프로그램 입력은 CNC 장치 또는 컴퓨터와의 통신 장치를 통해 수행할 수도 있습니다.
메모리에 저장된 전체 프로그램은 두 부분으로 나눌 수 있습니다. 하나는 객체 제어 알고리즘이고 다른 하나는 서비스 간의 정보 교환을 보장합니다. PC및 관리 개체. PC와 제어 대상 간의 정보 교환은 폴링 입력(제어 대상으로부터 정보 수신)과 출력 전환(제어 대상에 대한 제어 조치 발행)으로 구성됩니다. 이에 따라 프로그램의 서비스 부분은 폴링 입력과 스위칭 출력의 두 단계로 구성됩니다.
프로그래머블 컨트롤러 사용 다양한 유형의 메모리 , 기계의 전자 자동 프로그램을 저장합니다. 전기적 재프로그래밍 가능한 비휘발성 메모리; 무료 액세스가 가능한 RAM; 자외선으로 지울 수 있고 전기적으로 재프로그래밍할 수 있습니다.
프로그래밍 가능한 제어에는 입력 / 출력, 프로세서 작동 오류, 메모리, 배터리, 통신 및 기타 요소와 같은 진단 시스템이 있습니다. 문제 해결을 단순화하기 위해 최신 지능형 모듈에는 자체 진단 기능이 있습니다.
프로그래머블 로직 컨트롤러(PLC) 논리 제어 알고리즘을 구현하도록 설계된 마이크로프로세서 시스템입니다. 컨트롤러는 릴레이, 카운터, 타이머, 하드 논리 요소와 같은 개별 구성 요소에 조립된 릴레이 접점 회로를 대체하도록 설계되었습니다.
현대의 PLC개별 및 아날로그 신호, 제어 밸브, 스테퍼 모터, 서보 드라이브, 주파수 변환기를 처리하고 조절할 수 있습니다.
고성능으로 인해 사용할 가치가 있습니다. PLC센서의 신호에 대한 논리적 처리가 필요한 모든 곳. 애플리케이션 PLC장비 작동의 높은 신뢰성을 보장합니다. 제어 장치의 간단한 유지 보수; 장비 설치 및 조정 가속화; 제어 알고리즘의 빠른 업데이트(운영 장비 포함).
사용의 직접적인 이점 외에도 PLC,저렴한 가격과 높은 신뢰성으로 인해 간접적 인 것도 있습니다. 비용을 복잡하게하거나 증가시키지 않고 추가 기능을 구현하는 것이 가능합니다. 완성 된 제품, 장비의 기능을 완전히 실현하는 데 도움이 됩니다. 큰 구색 PLC간단한 작업과 복잡한 생산 자동화 모두에 대한 최적의 솔루션을 찾을 수 있습니다.
소프트웨어 캐리어
기계 집행 기관의 작업 프로그램은 프로그램 캐리어를 사용하여 설정됩니다.
프로그램 캐리어 제어 프로그램이 기록된 저장 매체입니다.
소프트웨어에는 다음이 포함될 수 있습니다. 기하학적, 그래서 기술 정보. 기술 정보 기계의 특정 사이클을 제공하고 다양한 도구의 작동 순서, 절삭 모드 변경 및 절삭유 켜기 등에 대한 데이터를 포함합니다. 기하학적 - 가공되는 공작물 및 도구 요소의 모양, 치수 및 공간에서의 상대적 위치를 특성화합니다.
최대 일반적인 소프트웨어 캐리어 이다:
카드 - 판지로 만들어졌으며 직사각형 모양이며 카드를 리더기에 삽입할 때 방향을 위해 한쪽 끝이 잘립니다. 프로그램은 해당 번호 대신에 구멍을 뚫어 기록됩니다.
8트랙 펀치 테이프 (그림 5) 너비 25.4mm. 전송 트랙 1은 리더에서 테이프(드럼 사용)를 이동하는 역할을 합니다. 정보를 전달하는 작업 구멍 2는 천공기라고 하는 특수 장치에 구멍이 뚫려 있습니다. 정보는 프레임 단위로 천공된 테이프에 적용되며, 각 프레임은 UE의 필수 부분입니다. 프레임에서 이러한 명령 집합만 기록될 수 있으며, 여기서 기계의 각 집행 기관에는 하나 이상의 명령이 제공되지 않습니다(예: 한 프레임에서 IO의 움직임을 모두 오른쪽으로 설정하는 것은 불가능합니다 그리고 왼쪽으로);
그림 5- 8트랙 펀칭 테이프
1 - 코드 트랙; 2 - 기본 가장자리; 3 - 코드 트랙 번호; 4 - 코드 조합의 비트 일련 번호
자기 테이프 - 플라스틱 베이스와 분말화된 강자성 물질의 작업층으로 구성된 2층 구성. 정보는 테이프를 따라 적용되는 자기 스트로크의 형태로 자기 테이프에 기록되고 지정된 IO 속도에 해당하는 특정 단계로 UE 프레임에 위치합니다. UE를 읽을 때 자기 스트로크는 제어 펄스로 변환됩니다. 각 스트로크는 하나의 펄스에 해당합니다. 각 임펄스는 IO의 특정(이산) 움직임에 해당합니다. 이 움직임의 길이는 자기 테이프 프레임에 포함된 펄스 수에 의해 결정됩니다. 이러한 IO 이동 명령 기록 디코딩된 .
디코딩은 보간기를 사용하여 수행됩니다. , 입력 된 공작물의 윤곽에 대한 인코딩 된 기하학적 정보 (펀칭 테이프 또는 컴퓨터에서)를 IO의 기본 움직임에 해당하는 제어 펄스 시퀀스로 변환합니다. 자기 테이프에 디코딩된 프로그램의 기록은 다음을 포함하는 특수 장치에서 수행됩니다. 기록용 출력이 있는 보간 장치; 지우기, 녹음 및 재생을 위한 자기 헤드가 있는 테이프 드라이브 메커니즘.
디코딩 된 형식의 정보는 원칙적으로 자기 테이프에 기록되고 인코딩 된 형식은 천공 테이프 또는 천공 카드에 기록됩니다. 자기 테이프는 프로그램의 디코딩된 보기가 필요한 스테퍼 모터가 있는 선반에 사용됩니다.
보간은 개별 섹션(프레임)에서 연속적으로 공작물 표면의 윤곽을 따라 작업 몸체(공구)의 이동을 위한 프로그램의 개발입니다.
Interpolator는 공구가 NC에 지정된 점 사이를 통과해야 하는 궤적의 중간 점 좌표를 계산하는 CNC 블록입니다. 보간기는 직선 세그먼트, 원호 등의 형태로 윤곽을 따라 시작점에서 끝점까지 공구를 이동하기 위한 NC 명령을 입력 데이터로 가지고 있습니다.
1 µm 정도의 궤적 재현 정확도(위치 센서의 정확도와 캘리퍼스의 위치 정확도 약 1 µm)를 보장하기 위해 보간기는 5-10ms마다 제어 펄스를 생성하므로 고속이 필요합니다. .
보간기의 알고리즘을 단순화하기 위해 주어진 곡선 윤곽은 일반적으로 직선 세그먼트 또는 원호로 형성되며 종종 다른 좌표축을 따라 이동하는 단계가 동시에 수행되지 않고 교대로 수행됩니다. 그럼에도 불구하고 제어 동작을 실행하는 빈도와 기계적 구동 장치의 관성으로 인해 끊어진 궤적이 부드러운 곡선 윤곽으로 매끄럽게 됩니다.
보간기 CNC 시스템의 일부인 은 다음 기능을 수행합니다.
UE가 지정한 처리된 윤곽선 섹션의 수치 매개변수(직선의 시작점과 끝점 좌표, 호의 반지름 값 등)를 기반으로 계산합니다(특정 불연속성) 등고선의이 부분의 중간 점의 좌표;
제어 전기 임펄스를 생성하며, 그 순서는 이러한 지점을 통과하는 궤적을 따라 기계 집행 기관의 움직임(필요한 속도로)에 해당합니다.
시스템에서 CNC는 주로 선형 및 선형 원형에 사용됩니다. 보간기; 전자는 모든 각도에 위치한 직선을 따라 인접한 기준점 사이에서 도구의 이동을 보장하고 후자는 직선과 원호를 따라 모두 이동합니다.
선형 보간- 이산 좌표 사이의 단면은 절삭 공구의 궤적에 따라 공간에 위치한 직선으로 표시됩니다.
원형 보간- 해당 반경의 호 형태로 처리 윤곽의 섹션을 표시합니다. CNC 장치의 기능을 사용하면 복잡한 대수 방정식으로 윤곽의 단면을 설명하여 보간을 제공할 수 있습니다.
나선형 보간- 나선은 한 평면의 원형과 이 평면에 수직인 선형의 두 가지 유형의 이동으로 구성됩니다. 이 경우 사용된 세 개의 기계 좌표(축)의 원운동 이송 속도 또는 선형 이송 속도를 프로그래밍할 수 있습니다.
CNC 시스템의 가장 중요한 기술적 특성 그녀는 해상도 또는 해상도 .
불연속- 이것은 하나의 제어 펄스에 해당하는 기계 집행 기관의 가능한 최소 이동량(선형 또는 각도)입니다.
대부분의 최신 CNC 시스템의 분해능은 0.01mm/펄스입니다. 0.001 mm / 펄스의 분해능을 가진 시스템 생산에 숙달되었습니다.
CNC 시스템은 실제로 다른 유형의 제어 시스템을 대체합니다.
CNC 시스템의 분류
기술적 능력과 작업 기관의 움직임의 성격에 의해 CNC 시스템은 세 그룹으로 나뉩니다.
위치 시스템 하나 또는 두 개의 좌표를 따라 기계 집행 기관의 직선 운동을 제공합니다. IO는 최대 속도로 위치에서 위치로 이동하고 지정된 위치에 대한 접근은 최소("크리핑") 속도로 이루어집니다. 이러한 CNC 시스템에는 드릴링 및 좌표 보링 머신.
등고선 시스템 처리 프로그램에 따라 주어진 속도로 특정 궤적을 따라 작업 이동을 수행하도록 설계되었습니다. 직사각형, 직선 및 곡선 모양을 제공하는 CNC 시스템은 윤곽을 따라 부품을 처리할 수 있기 때문에 윤곽(연속) 시스템에 속합니다. 직사각형 모양의 CNC 시스템에서 기계의 IO는 좌표축을 따라 교대로 이동하므로 도구 경로는 계단 형태를 가지며 이 경로의 각 요소는 좌표축과 평행합니다. 제어 좌표 수 그러한 시스템에서 5에 도달 , ㅏ 동시에 제어되는 축의 수 4 . 직선 모양이 있는 CNC 시스템에서 두 좌표 축(X 및 Y)을 따라 절단하는 동안 도구의 움직임이 구별됩니다. 이러한 시스템에서는 한 번에 두 개의 피드 드라이브에 제어 펄스를 발행하는 2좌표 보간기가 사용됩니다. 일반적인 제어 좌표의 수 2–5. 곡선 모양이 있는 CNC 시스템을 사용하면 복잡한 곡선 윤곽이 있는 영역이 포함된 평면 및 3차원 부품의 처리를 제어할 수 있습니다. CNC 윤곽 시스템에는 스테퍼 모터가 있습니다. 이러한 시스템에는 터닝, 밀링, 보링 머신이 장착되어 있습니다.
결합 시스템(범용) 위치 및 윤곽 시스템의 기능을 모두 가지고 있으며 다목적 기계(드릴링-밀링-보링)에 가장 일반적입니다.
CNC 시스템이 있는 기계에서 제어는 기하학적 및 기술 정보가 숫자 형식으로 입력되는 프로그램 캐리어에서 수행됩니다.
별도의 그룹에는 디지털 표시 및 사전 설정 좌표가 있는 기계가 할당됩니다. 이 기계에는 전자 원하는 점의 좌표를 설정하는 장치(좌표 사전 설정) 및 원하는 위치로 이동하도록 명령하는 위치 센서가 장착된 크로스 테이블. 어디에서 테이블의 각 현재 위치를 화면에 표시(디지털 표시) . 이러한 기계에서는 사전 설정된 좌표 또는 디지털 표시를 사용할 수 있습니다. 초기 작업 프로그램은 기계 작업자가 설정합니다.
PU가 있는 공작 기계 모델에서는 자동화 정도를 나타내기 위해 숫자가 있는 문자 F가 추가됩니다.
여 1- 디지털 표시 및 좌표 사전 설정 기능이 있는 기계
여 2– 직사각형 및 위치 CNC 시스템이 있는 기계;
여 3- 윤곽선 직선 및 곡선 CNC 시스템이 있는 기계;
여 4– 위치 윤곽을 위한 범용 CNC 시스템이 있는 기계.
또한 접두사 C1, C2, C3, C4 및 C5를 CNC 기계 모델 지정에 추가할 수 있습니다. 다양한 모델공작 기계에 사용되는 CNC 시스템 및 공작 기계의 다양한 기술 능력. 예를 들어 공작 기계 모델 16K20F3S1에는 CNC 시스템 "Kontur 2PT-71"이 장착되어 있고 공작 기계 모델 16K20F3S4에는 CNC 시스템 EM907이 장착되어 있습니다.
가 있는 기계의 경우 순환 시스템 PU 모델명에 입력 인덱스 C , 와 함께 운영 체제 – 인덱스 T (예: 16K20T1). CNC는 가공 사이클, 절단 모드 및 다양한 보조 기능의 순서뿐만 아니라 성형 중 기계의 작업 본체의 움직임과 움직임의 속도를 제어합니다.
CNC 기계를 특성화하기 위해 다음 지표가 사용됩니다.
정확도 등급 :시간- 정상 정확도, 피– 정확도 증가, V- 높은 정밀도, ㅏ– 특히 높은 정밀도, 와 함께– 초고정밀(마스터 머신);
기술 운영 , 기계에서 수행 : 터닝, 드릴링, 밀링, 연삭 등;
기계의 주요 매개변수 : 척킹 머신용 – 가장 큰 직경침대 위에 설치된 제품; 센터 및 척 머신용- 캘리퍼스 위의 공작물의 가장 큰 직경; 바 터닝용공작 기계 - 가공 막대의 가장 큰 직경; 밀링 및 보링용공작 기계 - 테이블 작업 표면의 전체 치수 (길이, 너비), 원형 회전 테이블 작업 표면 직경; 드릴링을 위해공작 기계 - 가장 큰 드릴링 직경, 개폐식 스핀들의 직경 등;
기계의 작업 몸체의 움직임의 크기 - 두 좌표의 캘리퍼스, 두 좌표의 테이블, 선형 및 각 좌표의 스핀들 어셈블리 등
이산 값 (구분 가격) 프로그램을 따라 이동하는 최소 작업(단계);
제어된 좌표에 의한 포지셔닝의 정확도 및 반복성 ;
메인 드라이브 – 유형, 공칭 및 최대 출력 값, 스핀들 속도 제한(단계식 또는 무단계), 작동 속도 수, 자동 전환 속도 수
머신 피드 드라이브 - 좌표, 유형, 공칭 및 최대 모멘트, 작업 이송 속도 제한 및 작업 이송 속도 수, 빠른 이동 속도
도구 수 - 툴 홀더, 터렛, 툴 매거진에서;
공구 교환 유형 – 자동, 수동;
기계의 전체 치수 및 무게 .
제어 프로그램의 작성 및 입력 방법에 따라 구별하다:
운영 CNC 시스템(이 경우 제어 프로그램은 배치에서 첫 번째 부분을 처리하거나 처리를 시뮬레이션하는 과정에서 기계에서 직접 준비되고 편집됩니다);
적응 시스템, 부품이 처리되는 위치에 관계없이 제어 프로그램이 준비되고 있습니다. 또한 제어 프로그램의 독립적인 준비는 이 기계의 CNC 시스템의 일부인 컴퓨터 기술을 사용하거나 외부에서(수동으로 또는 프로그래밍 자동화 시스템을 사용하여) 수행할 수 있습니다.
기술력 수준에 따라국제 관행에서 다음과 같은 수치 제어 시스템 지정이 허용됩니다.
체크 안함(컴퓨터 수치 제어) - CNC;
HNC(수동 수치 제어) - 키, 스위치 등을 사용하여 원격 제어에서 작업자가 처리 프로그램을 설정하는 일종의 CNC 장치.
에스엔씨(Speiher Numerical Control) - 전체 제어 프로그램을 저장하기 위한 메모리가 있는 CNC 장치(프로그램은 내부 메모리에 저장됨).
CNC- CNC 장치를 사용하면 하나의 CNC 기계를 제어할 수 있습니다. 장치는 제어 미니 컴퓨터 또는 프로세서의 구조에 해당합니다. 프로그램 제어 기능 확장, 작업장에서 UE 저장 및 편집 가능, 운영자와의 대화, 광범위한 수정 가능성, 작동 중 프로그램 변경 가능성 등이 됩니다.
DNC(직접 수치 제어) – 시스템 이상 높은 레벨, 제공: 공통 컴퓨터에서 한 번에 기계 그룹 제어 매우 많은 수의 프로그램을 메모리에 저장합니다. GPS의 보조 시스템(운송, 창고)과의 상호 작용; 특정 부품 처리를 위한 시작 시간 선택; 작동 시간 및 장비 가동 중지 시간 등을 고려합니다.
정보 스트림의 수로 CNC 시스템은 폐쇄형, 개방형 및 적응형으로 나뉩니다.
개방형 시스템독자에서 기계의 집행 기관으로 오는 정보의 한 흐름이 있는 것이 특징입니다. 이러한 시스템의 메커니즘에는 스테퍼 모터가 사용됩니다. 예를 들어 토크 부스터를 사용하여 신호가 다양한 방식으로 증폭되는 마스터 장치이며 샤프트가 피드 드라이브의 리드 나사에 연결되어 있습니다. 개방형 시스템에는 피드백 센서가 없으므로 기계 액추에이터의 실제 위치에 대한 정보가 없습니다.
폐쇄 시스템 CNC는 판독기 및 경로를 따라 피드백 센서의 두 가지 정보 스트림이 특징입니다. 이러한 시스템에서는 피드백의 존재로 인해 집행 기관 변위의 주어진 값과 실제 값 사이의 불일치가 제거됩니다.
적응 시스템 CNC는 3가지 정보 흐름으로 특징지어집니다: 1) 리더로부터; 2) 도중에 피드백 센서에서; 3) 기계에 설치된 센서와 절삭 공구의 마모, 절삭 및 마찰력의 변화, 공작물 재료의 허용량 및 경도 변동 등과 같은 매개변수의 관점에서 처리 공정을 제어합니다. 이러한 프로그램을 통해 다음을 수행할 수 있습니다. 실제 절단 조건을 고려하여 처리 프로그램을 조정하십시오.
특정 유형의 CNC 장비의 사용은 제조 부품의 복잡성과 연속 생산에 따라 다릅니다. 연속 생산이 적을수록 기계가 가져야 하는 기술적 유연성이 커집니다.
단일 소규모 생산에서 복잡한 공간 프로파일이 있는 부품을 제조할 때 CNC 기계를 사용하는 것은 거의 기술적으로 정당한 솔루션입니다. 이 장비도 빠르게 장비를 제작할 수 없는 경우 사용하는 것이 좋습니다. 연속 생산에서는 CNC 기계를 사용하는 것도 좋습니다. 최근에는 자동화된 CNC 기계 또는 이러한 기계의 시스템이 재구성된 대규모 생산 조건에서 널리 사용되고 있습니다.
CNC 기계의 기본 기능은 특정 부품을 처리하기 위한 장비 작동 주기 및 기술 모드가 기록되는 제어 프로그램(CP)에 따른 작업입니다. 기계에서 처리되는 부품을 변경할 때 프로그램을 변경하기만 하면 수동 제어가 가능한 기계에서 이 작업의 수고에 비해 전환 수고가 80 ... 90% 줄어듭니다.
기본 CNC 기계의 장점:
기계의 생산성은 수동 제어가 가능한 유사한 기계의 생산성에 비해 1.5….2.5배 증가합니다.
범용 장비의 유연성은 자동 기계의 정확성 및 생산성과 결합됩니다.
숙련 된 작업자의 필요성 - 기계 작업자가 감소하고 생산 준비가 엔지니어링 작업 분야로 이전됩니다.
하나의 프로그램에 따라 만들어진 부품. 그들은 상호 교환이 가능하여 조립 과정에서 피팅 작업 시간을 줄입니다.
프로그램의 예비 준비, 더 간단하고 다양한 기술 장비로 인해 준비 및 새 부품 제조로의 전환 기간이 단축됩니다.
부품 제조 주기가 단축되고 진행 중인 작업 재고가 줄어듭니다.
통제 질문:
기계 제어 소프트웨어란 무엇입니까? 어떤 종류의 PU 공작 기계를 알고 있습니까?
CNC 기계는 무엇을 의미합니까?
CNC 공작 기계 란 무엇입니까? 어떤 CNC 시스템을 알고 있습니까?
CNC 기계의 기본 기능은 무엇입니까?
CNC 기계 사용의 주요 이점을 나열하십시오.
CNC 기계의 좌표축 및 동작 구조
모든 CNC 기계의 경우 ISO 표준 - R841:1974에서 권장하는 단일 좌표 표기법이 사용됩니다. 좌표는 기계 스핀들 또는 공작물의 회전 축 위치와 도구 또는 공작물의 직선 또는 원형 이동을 나타냅니다. 먹이다. 이 경우 좌표축의 지정과 기계의 이동 방향은 가공 작업의 프로그래밍이 도구 또는 공작물의 이동 여부에 의존하지 않도록 설정됩니다. 기본은 고정 공작물의 좌표계를 기준으로 한 도구의 이동입니다.
표준 좌표계는 축이 기계의 직선 가이드와 평행한 공작물과 관련된 오른쪽 직사각형 시스템입니다.
모든 직선 운동은 좌표계에서 고려됩니다. 엑스 , 와이 , 지 . 각 좌표축에 대한 원운동 라틴 알파벳의 대문자로 표시 : A, B, C (그림 6) 모든 기계에서 Z 축은 주 이동의 스핀들 축, 즉 공구를 회전시키는 스핀들(드릴링 밀링 보링 그룹의 기계에서) 또는 스핀들 공작물을 회전시킵니다(선삭 그룹의 기계에서). 여러 개의 스핀들이있는 경우 공작물이 부착 된 테이블의 작업 표면에 수직 인 스핀들이 주요 스핀들로 선택됩니다.
그림 6- CNC 기계의 표준 좌표계
축 이동 지 긍정적인 방향으로 방향과 일치해야 합니다 공작물에서 도구 제거 . 드릴링 및 보링 머신에서 공구가 Z축을 따라 음의 방향으로 이동할 때 가공이 발생합니다.
중심선 엑스 바람직하게는 수평이어야 합니다 공작물 장착 표면과 평행합니다. 회전하는 공작물(선반)이 있는 기계에서 X축 이동은 공작물의 반경을 따라 가로 방향 가이드와 평행합니다. 양의 축 이동 엑스 도구가 , 크로스 슬라이드의 메인 툴 홀더에 설치된, 회전축에서 멀어짐 공백.
회전 도구가 있는 기계에서 수평 Z축이 있는 (밀링, 드릴링) 양의 축 이동 엑스 주공구 스핀들에서 공작물 쪽으로 보았을 때 오른쪽으로 향합니다. 수직 Z축을 사용하면 X축을 따라 단일 열 기계의 경우 오른쪽으로, 2열 기계의 경우 주 도구 스핀들에서 왼쪽 랙으로의 포지티브 이동.
양의 축 방향 와이 Z 및 X축과 함께 Y축이 오른쪽 직교 좌표계를 형성하도록 선택해야 합니다. 이렇게 하려면 오른손 법칙을 사용합니다. 엄지손가락은 X축, 집게손가락은 Y축, 가운데 손가락은 Z축( 그림).
X, Y 및 Z 축을 따른 주요(1차) 직선 이동 외에 이들에 평행한 2차 이동이 있는 경우 각각 U, V, W로 지정되며, 3차 이동이 있는 경우 지정됩니다. P, Q 및 R.
기계의 작업 몸체의 1 차, 2 차 및 3 차 움직임은 주축에서 이러한 몸체의 거리에 따라 결정됩니다.
축 A, B, C와 평행 여부에 관계없이 2차 회전 운동은 D 또는 E로 지정됩니다.
좌표의 방법 및 원점
CNC 기계를 설정할 때 각 집행 기관은 특정 초기 위치로 설정되며, 여기서부터 엄격하게 정의된 거리에서 공작물을 처리하는 동안 이동합니다. 이렇게 하면 도구가 경로의 정의된 참조점을 통과할 수 있습니다. 집행 기관이 한 위치에서 다른 위치로 이동하는 크기와 방향은 UE에서 설정되며 기계 및 CNC 시스템의 설계에 따라 기계에서 다양한 방식으로 수행될 수 있습니다. 최신 CNC 기계에서는 절대 및 상대(증분)의 두 가지 변위 계산 방법이 사용됩니다.
좌표계산의 절대적 방법 – 전체 공작물 처리 프로그램에 대해 좌표 원점 위치가 고정(고정)됩니다. 프로그램을 컴파일 할 때 원점에서 지정된 연속적으로 위치한 점 좌표의 절대 값이 기록됩니다. 프로그램을 처리할 때 좌표는 이 원점에서 매번 계산되어 프로그램 처리 과정에서 변위 오차의 누적을 제거합니다.
좌표계산의 상대적인 방법 – 다음 기준점으로 이동을 시작하기 전에 점유하고 있는 집행 기관의 위치는 매번 0 위치로 간주됩니다. 이 경우 점에서 점으로 도구를 순차적으로 이동하기 위해 좌표 증분이 프로그램에 기록됩니다. 이 참조 방법은 CNC 윤곽 시스템에서 사용됩니다. 주어진 기준점에서 집행 기관의 위치 정확도는 초기 기준점에서 시작하여 모든 이전 기준점의 좌표를 처리하는 정확도에 의해 결정되며, 이는 프로그램 처리 중에 이동 오류가 누적되게 합니다.
프로그래밍 및 CNC 기계 설정의 편의를 위해 경우에 따라 집행 기관의 스트로크 내에서 좌표 원점을 선택할 수 있습니다. 이 좌표의 원점을 플로팅 제로" CNC 포지셔닝 시스템이 장착된 드릴링 및 보링 머신에 주로 사용됩니다.
제어 프로그램 개발
제어 프로그램을 개발할 때 다음이 필요합니다.
절단 및 보조 도구 및 장치를 선택하여 일련의 작업 형태로 경로 처리 기술을 설계합니다.
절삭 조건 계산 및 절삭 공구 이동 궤적 결정으로 작동 기술 개발
절삭 공구의 궤적에 대한 기준점 좌표를 결정합니다.
정착 및 기술지도와 기계 설치를위한지도를 작성하십시오.
정보를 인코딩합니다.
프로그램 캐리어에 정보를 넣고 CNC 기계의 메모리로 보내거나 CNC 장치의 제어판에 수동으로 입력하십시오.
확인하고 필요한 경우 프로그램을 수정하십시오.
프로그래밍을 위해서는 부품 도면, 기계 설명서, 프로그래밍 지침, 절삭 공구 카탈로그 및 절삭 데이터 표준이 필요합니다.
GOST20999-83에 따르면 프로그램 요소는 프레임 시퀀스와 해당 기호를 사용하여 특정 순서로 작성됩니다(표 1 참조).
표 1 제어 문자 및 기호의 의미
상징 |
의미 |
X축에 대한 회전 각도 |
|
Y축을 중심으로 한 회전 각도 |
|
Z축을 중심으로 한 회전 각도 |
|
도구의 두 번째 기능 |
|
두 번째 피드 기능 |
|
첫 번째 기능(속도) 피드 |
|
준비 기능 |
|
도구 길이 오프셋 |
|
각도 보간 매개변수 또는 X축에 평행한 나사 리드 |
|
각도 보간 매개변수 또는 Y축에 평행한 나사 리드 |
|
Z 축에 평행한 각도 보간 매개변수 또는 나사 리드 |
|
도우미 기능 |
|
프레임 번호 |
|
X축에 평행한 3차 이동 길이 |
|
Y축에 평행한 3차 이동 길이 |
|
Z축을 따라 빠른 이동 또는 Z축에 평행한 이동의 3차 길이 |
|
메인 무브먼트의 기능(스피드) |
|
첫 번째 도구 기능 |
|
X축에 평행한 보조 이동 길이 |
|
2차 이동 길이, Y축에 평행 |
|
Z축에 평행한 보조 이동 길이 |
|
X축에 평행한 기본 이동 길이 |
|
Y축에 평행한 기본 이동 길이 |
|
Z축에 평행한 기본 이동 길이 |
|
제어 프로그램 블록의 끝을 나타내는 기호 |
|
제어 프로그램의 시작을 나타내는 기호 |
|
수학 기호 |
|
수학 기호 |
|
소수점 기호 |
프로그램 블록(구)- 특정 순서로 배열되고 하나의 기술 작업 작업에 대한 정보를 전달하는 일련의 단어(그림 8).
프로그램 워드- 전체적으로 특정 연결에 있는 일련의 문자.
그림 8– 프로그램 블록
제어 프로그램의 각 블록에는 다음이 포함되어야 합니다.
"프레임 번호"라는 단어;
정보 단어 또는 단어(사용하지 않는 것이 허용됨);
기호 "프레임 끝";
탭 문자(사용할 수 없음). 이러한 기호를 사용할 때 "프레임 번호"라는 단어를 제외하고 UE 프레임의 각 단어 앞에 배치됩니다.
단어 (또는 단어) "준비 기능";
"차원 운동"이라는 단어는 X, Y, Z, U, V, W, P, Q, R, A, B, C 문자 순서로 작성하는 것이 좋습니다.
단어 "보간 매개변수" 또는 "나사 피치" I, J, K;
특정 축만을 참조하고 해당 축을 따라 "차원 이동"이라는 단어 바로 뒤에 와야 하는 "피드 기능"이라는 단어; 2개 이상의 축을 나타내는 "피드 기능"이라는 단어는 "차원 이동"이라는 단어 뒤에 와야 합니다.
"메인 운동의 기능"이라는 단어;
단어(또는 단어) "도구 기능";
단어 (또는 단어) "보조 기능".
허용되는 값 이외의 값에 사용되는 주소 D, E, H, U, V, W, P, Q, R이 있는 쓰기 단어의 순서와 다중도는 특정 CNC 장치의 형태로 표시됩니다.
하나의 UE 블록 내에서 "차원 변위" 및 "보간 매개변수" 또는 "나사 피치"라는 단어가 반복되어서는 안 됩니다. 동일한 그룹에 포함된 "준비 기능"이라는 단어를 사용해서는 안 됩니다.
"메인 프레임"(:) 기호 뒤에 UE는 처리를 시작하거나 재개하는 데 필요한 모든 정보를 포함해야 합니다. 이 문자는 데이터 캐리어에서 프로그램의 시작을 식별하는 데 사용됩니다.
NC 프레임의 각 단어는 주소 기호(표에 따른 라틴 알파벳의 대문자), 수학 기호 "+" 또는 "-"(필요한 경우), 일련의 숫자로 구성되어야 합니다.
NC의 단어는 소수점을 사용하지 않고(소수점 위치가 암시됨) 소수점을 사용(소수점의 명시적 위치)하는 두 가지 방법 중 하나로 작성할 수 있습니다. 명시적 소수점은 "DS" 기호로 표시됩니다. 소수점의 내재된 위치는 특정 CNC의 사양에 정의되어야 합니다.
소수점을 사용하여 단어를 작성할 때 소수점이 없는 단어는 CNC에서 정수로 처리해야 합니다. 이 경우 부호 앞(또는) 뒤의 중요하지 않은 0은 생략할 수 있습니다. X.03은 크기가 X축을 따라 0.03mm임을 의미합니다. X1030 - X축을 따라 1030.0mm 크기입니다.
현재는 프로그래밍할 때 천공 테이프에 정보를 기록하는 주소 방식이 더 많이 사용됩니다. 각 프레임의 정보는 두 가지 유형으로 나뉩니다. 1) 문자(주소)는 명령이 주어진 CNC 시스템(또는 기계)의 집행 기관을 나타냅니다. 2) 주소 뒤에 오는 숫자로 기계 집행 기관의 이동량("+" 또는 "-" 기호 포함) 또는 코드 입력(예: 사료량 등). 숫자 뒤에 오는 문자는 단어입니다. 프로그램 블록은 하나, 둘 또는 그 이상의 단어로 구성됩니다.
워크피스를 처리하기 위한 다수의 UE 프레임의 인코딩된 기록 선반다음과 같이 보일 수 있습니다.
003 X +000000 - 커터를 X 축을 따라 영점으로 이동합니다.
№ 004 Z +000000 - 커터를 Z 축을 따라 영점으로 이동합니다.
번호 005 G26 - 증분 작업 명령
번호 006 G10 X -006000 - G10 - 선형 보간(직선
여행 경로)
번호 007X-014000 F10080
번호 008 Z +000500 F10600
번호 009 X +009500 F70000
번호 010 X +002000 Z -001000 F10100
………………………………………………………..
…………………………………………………………….
아니…….M102
문자 뒤의 숫자는 주어진 단어의 숫자 부분의 자릿수를 결정합니다. 주소 괄호 X,Z,I,K는 다음과 같은 경우 기하학적 정보를 표현할 수 있는 숫자를 나타냅니다. 다양한 모드 CNC 작업. 이 정보는 펄스 수(IO 이동의 밀리미터 수를 처리의 불연속성으로 나눈 값)로 기록됩니다.
단어 (또는 단어 ) "준비 기능" 표 2에 따라 코드 기호로 표현해야 합니다.
표 2 - 준비 기능
지정 기능 |
기능 값 |
포지셔닝. 주어진 지점까지 고속으로 이동합니다. 이전에 설정된 절단 피드가 취소되지 않습니다. |
|
선형 보간. 한 점까지 직선으로 프로그래밍된 이송으로 이송 |
|
방향 및 시계 반대 방향으로 각각 원호 보간 |
|
제어판 또는 프레임에서 설정한 특정 시간 동안 처리 지연 |
|
임시 정지. 정지 시간은 제한되지 않습니다. 버튼을 누르면 기계가 작동됩니다 |
|
포물선 보간. 프로그래밍된 피드를 사용한 포물선 이동 |
|
오버클럭 이동 시작 시 프로그래밍된 값으로 이송 속도를 부드럽게 증가 |
|
프레임 끝에서 제동. 이송 속도를 고정 값으로 부드럽게 감소 |
|
보간 평면 각각 XY,XZ,YZ |
|
각각 일정한 피치, 증가 및 감소 피치로 나사 가공 |
|
G41-G52 기능 중 하나로 지정된 공구 옵셋 취소 |
|
윤곽 제어에서 공구 직경 또는 반경 보정. 절단 도구는 부품의 왼쪽과 오른쪽에 각각 있습니다. |
|
공구 직경 또는 공구 반경 오프셋 각각 양수 및 음수 |
|
직선 성형의 공구 직경 또는 반경 오프셋: G45+/+, G46+/-, G47-/-, G48-/+, G49 0/+, G50 0/-, G51 +/0, |
|
G54-G59 기능 중 하나로 지정된 선형 이동 취소 |
|
선형 이동 좌표 X, Y, Z XY,XZ,YZ 평면에서 각각 |
|
태핑 |
|
기능 G81-G89 중 하나로 지정된 고정 주기 취소 |
|
일정한 주기 |
|
절대 크기. CNC의 영점을 원점으로 하여 절대 좌표계에서 움직임을 계산합니다. |
|
증분 크기. 이전에 프로그래밍된 포인트를 기준으로 이동 계산 |
|
절대 위치 누적기 설정 |
|
시간 역전의 이송 속도 |
|
각각 분당 및 회전당 이송 단위 |
|
절삭 속도 단위(m/min) |
|
메인 모션 단위(rpm) |
참고: G07, G10-G16, G20, G32, G36-G39, G60-G62, G64-G79, G98, G99는 예약 코드입니다.
모든 치수 이동은 절대값 또는 증분으로 지정해야 합니다. 제어 방법은 준비 기능 중 하나로 선택해야 합니다.: G90(절대 크기) 또는 G91(증분 크기) ).
각 단어 "차원 이동"의 주소 뒤에는 두 자리가 옵니다. 첫 번째는 숫자의 정수 부분을 분수와 구분하는 암시적 소수점 앞의 자릿수를 나타내고, 두 번째는 소수점 이하 자릿수를 나타냅니다. 가리키다. "Dimensional Movements" 단어에서 첫 번째 유효 숫자 앞과 마지막 숫자 뒤에 0을 생략할 수 있는 경우 주소 "Dimensional Movement" 뒤에 세 자리 숫자가 와야 합니다. 첫 번째 유효 숫자 앞에 0이 생략되면 첫 번째 숫자는 0이어야 합니다. 유효 숫자 뒤에 0이 생략되면 마지막 숫자는 0이어야 합니다.
모든 선형 이동은 밀리미터와 그 소수로 표현되어야 합니다. 모든 각도 치수는 라디안 또는 도 단위로 제공됩니다. 회전의 소수로 각도 치수 표현이 허용됩니다.
CNC에서 좌표계의 원점에 따라 절대값(양수 또는 음수)으로 치수를 지정할 수 있는 경우 수학 기호("+" 또는 "-")는 "치수 이동"이라는 단어의 필수 부분입니다. " 및 각 차원의 첫 번째 숫자 앞에 와야 합니다.
절대 차원이 항상 양수이면 주소와 그 뒤에 오는 숫자 사이에 부호가 없고 양수 또는 음수이면 부호가 붙습니다.
CNC에서 증분 치수를 허용하는 경우 이동 방향을 나타내기 위해 수학 기호가 각 치수의 첫 번째 숫자 앞에 와야 합니다.
복잡한 궤적을 따라 도구의 움직임이 제공됩니다. 특수 장치- 보간기.선형 및 호 세그먼트의 보간은 주어진 궤적의 섹션에 대해 별도로 수행됩니다. 각 섹션은 제어 프로그램의 하나 이상의 프레임에 기록될 수 있습니다.
궤적(직선, 원, 포물선 또는 더 높은 차수의 곡선)의 보간된 섹션의 기능적 특성은 해당준비 기능(G01 - G03, G06). 보간 매개변수를 설정하려면주소 I, J, K, 곡선의 기하학적 특성을 결정하는 데 사용합니다(예: 원호의 중심, 반지름, 각도 등). 수학 기호("+" 또는 "-")를 보간 매개변수와 함께 작성하려면 주소 문자 다음에 숫자 문자 앞에 와야 합니다. 기호가 없으면 "+" 기호로 간주됩니다.
각 보간 구간의 시작점은 이전 구간의 끝점과 일치하므로 새 블록에서 반복되지 않습니다.이 보간 섹션에 있고 특정 좌표를 갖는 각 후속 지점은 이동 주소가 있는 별도의 정보 프레임에 해당합니다. X, Y 또는 Z.
최신 CNC에는 소프트웨어에 "내장" 기능이 있어 가장 간단한 보간을 수행합니다. 따라서 CNC 선반에서 45 ° 각도의 모따기는 주소로 제공됩니다. 와 함께모따기 전에 부품이 처리되는 좌표를 따라 부호와 최종 크기가 있습니다. 주소 아래 표시 와 함께 X 좌표를 따라 처리 부호와 일치해야 합니다. (그림, a). Z 좌표를 따른 방향은 음의 방향으로만 설정됩니다.
호를 지정하기 위해 호의 끝점 좌표와 주소 R 아래의 반경은 시계 방향으로 가공할 때 양수 기호로, 시계 반대 방향으로 가공할 때 음수 기호로 지정됩니다(그림 9).
그림 9- CNC 선반에서 모따기(a) 및 호(b) 프로그래밍
주요 이동의 피드 및 속도는 숫자로 인코딩되며 그 숫자는 특정 CNC 장치의 형식으로 지정됩니다. 선택피드 유형 G93(역시간 이송 기능), G94(분당 이송), G95(회전당 이송).
선택메인 무브먼트의 종류 준비 기능 중 하나로 수행해야 합니다.G96(일정한 절삭 속도) 또는 G97(rpm).
직접 표기법은 피드를 인코딩하는 주요 방법으로 사용되며,다음 단위를 사용해야합니다. 분당 밀리미터 - 피드는 주요 움직임의 속도에 의존하지 않습니다. 회전당 밀리미터 - 피드는 주요 움직임의 속도에 따라 다릅니다. 초당 라디안(분당 각도) - 피드는 원운동만을 나타냅니다. 주이동 속도를 직접 코딩할 때 숫자는 스핀들의 각속도를 나타냅니다.(초당 라디안 또는 분당 회전수) 또는 절단 속도(분당 미터 단위). 예를 들어 프로그램에서 스핀들 속도를 S - 1000으로 지정하면 스핀들이 1000rpm의 속도로 시계 방향으로 회전한다는 의미입니다.(마이너스가 없으면 스핀들이 시계 반대 방향으로 회전합니다).
"공구 기능"이라는 단어는 공구를 선택하는 데 사용됩니다. . 도구를 수정(또는 보정)하는 데 사용할 수 있습니다. 이 경우 "공구 기능"이라는 단어는 두 개의 숫자 그룹으로 구성됩니다. 첫 번째 그룹은 도구를 선택하는 데 사용되고 두 번째 그룹은 수정에 사용됩니다. 공구 옵셋(보상)을 쓰기 위해 다른 주소를 사용하는 경우 권장 기호 D 또는 H를 사용합니다.
다음 자릿수 주소 T, D 및 H , 특정 CNC 장치의 형식으로 지정됩니다.
단어 (또는 단어) "도움말 기능"표 3에 따라 코드 번호로 표시됩니다.
표 3 - 보조 기능
지정 기능 |
기능 값 |
프로그래밍된 정지. 스핀들 정지, 공급 및 냉각 끄기 |
|
확인하고 중지합니다. M 00과 동일하지만 먼저 작업자 콘솔에서 해당 버튼을 눌러 수행됩니다. |
|
프로그램 종료. 스핀들 정지 및 냉각수 꺼짐 |
|
스핀들 회전은 각각 시계 방향 및 반시계 방향 |
|
스핀들 정지 효과적인 방법 |
|
도구 변경. 공구 교환 명령이 수동 또는 자동으로 주어집니다. |
|
2호, 1호 냉방 켜기 |
|
냉각을 끕니다. M07, M08, M50, M51 명령 취소 |
|
클램프 및 해제. 클램핑 장치에 적용 기계 테이블, 공백 등 |
|
냉각을 켜는 동안 방향과 시계 반대 방향으로 스핀들 회전 |
|
"+" 및 "-"로의 빠른 이동 |
|
내장 메모리가 있는 CNC의 프로그램 종료 |
|
특정 각도 위치에서 스핀들 정지 |
|
반복적으로 읽는 프로그램 장인 프로그램 끝 |
|
정보의 끝 |
|
우회 차단. 잠금을 일시적으로 취소하는 명령 |
|
공급 범위, 각각 1번 및 2번 |
|
스핀들 회전 범위 각각 1번 및 2번 |
|
취소 M 49 |
|
수동 무시 취소 |
|
각각 3번과 4번 냉각 |
|
각각 위치 #1 및 #2의 공구 선형 오프셋 |
|
취소 M 59 |
|
일정한 스핀들 속도 |
|
공작물 교환 |
|
고정 위치 31 및 2로 각각 공작물의 선형 변위 |
|
공작물 클램핑 및 압착 |
|
테이블 클램핑 및 비틀기 |
나사산 피치 값은 스핀들 회전당 밀리미터로 표시되어야 합니다. 나사산 피치를 정의하는 단어의 자릿수는 특정 CNC 장치의 형식으로 정의됩니다. 가변 피치로 나사를 절단할 때 아래의 단어는 주소 I 및 K초기 나사 피치의 치수를 지정해야 합니다.
"피드 기능"이라는 단어는 일정한 나사 피치로 프로그래밍하면 안 됩니다.
각 제어 프로그램은 "프로그램 시작" 기호로 시작해야 하며, 그 뒤에 "블록 끝" 기호가 있어야 하고 그 다음에 해당 번호가 있는 블록이 있어야 합니다. 제어 프로그램을 지정해야 하는 경우 이 지정(번호)은 "프로그램 시작" 기호 바로 뒤에 "블록 끝" 기호 앞에 위치해야 합니다.
제어 프로그램은 "프로그램 끝" 또는 "정보 끝" 기호로 끝나야 합니다. "정보 끝" 기호 뒤에 배치된 정보는 CNC에서 허용되지 않습니다. 펀치 테이프의 "프로그램 시작" 기호 앞과 "프로그램 끝" 및 "정보 끝" 기호 뒤에 PUS 기호("비어 있음")가 있는 섹션을 남겨두는 것이 좋습니다.
프로그램 디버깅 및 수정
제어 프로그램을 작성할 때 중요한 점은 개발 부품을 기준으로 한 절삭 공구 경로 그리고 이것을 기초로 - 기계의 해당 기관의 움직임에 대한 설명. 이를 위해 여러 좌표계가 사용됩니다.
주요 결제 시스템 – 기계 좌표계 , 이는 작업 본체의 변위와 위치를 제한합니다. 이러한 위치는 기준점 , 기계의 디자인에 따라 선택되는 . 예를 들어, 스핀들 조립용기준점은 스핀들의 끝면과 회전 축의 교차점이며, 크로스 테이블을 위해는 대각선의 교차점이며, 턴테이블용- 테이블의 거울에 대한 회전 중심 등. 표준 좌표계에서 축의 위치와 방향은 위에서 논의되었습니다.
표준 좌표계의 원점은 일반적으로 공작물을 운반하는 노드의 기준점과 정렬됩니다. 이 경우 어셈블리는 기계의 작업체의 모든 움직임이 양의 방향으로 발생하는 위치에 고정됩니다.(그림 10). 이 기준점에서,제로라고 공작 기계 , 작업 기관의 위치가 결정되고,위치에 대한 정보가 손실된 경우(예: 비상 정전으로 인해). 작업 본체는 제어판의 해당 버튼을 누르거나 제어 프로그램의 명령을 사용하여 기계의 0으로 이동합니다. 각 좌표에 대한 영점 위치에서 작업 바디의 정확한 정지는 영점 위치 센서에 의해 제공됩니다. 예를 들어, 회전할 때 사고를 피하기 위해 기계의 영점을 오프셋으로 설정합니다.
공작물 좌표계이 시스템과 기계 좌표계의 상대적인 위치를 결정하기 위해 기계에 공작물을 고정할 때 기준점이 고려됩니다(그림 9). 때때로 이 연결은 설비의 기준점을 사용하여 이루어집니다.
도구 좌표계마운트를 기준으로 작업 부품의 위치를 설정하도록 설계되었습니다. 공구는 홀더와 함께 조립된 작업 위치에 설명되어 있습니다. 이 경우 도구 좌표계의 축은 표준 기계 좌표계의 해당 축과 평행하고 같은 방향을 향합니다. 기준점은 도구 좌표계의 원점으로 간주됩니다. 도구 블록기계에 설치하는 기능을 고려하여 선택되었습니다.
공구 팁의 위치는 반경으로 지정됩니다. 아르 자형및 설정 포인트의 X 및 Z 좌표. 이 점은 일반적으로 요소가 좌표축에 평행한 도구 경로를 정의할 때 사용됩니다. 곡선 궤적을 사용하면 도구 끝의 라운딩 중심이 설계 포인트로 사용됩니다.기계, 공작물 및 도구의 좌표계 간의 관계는 그림 9에서 쉽게 확인할 수 있습니다.
그림 9- 밀링(a) 및 터닝(b) CNC 기계에서 처리할 때 부품의 좌표계
제어 프로그램을 개발하고 부품을 가공할 때 프로그램 좌표계 사용. 해당 축은 기계 좌표 축과 평행하고 같은 방향으로 향합니다.
좌표의 원점(기계의 시작점)은 치수 측정의 편의에 따라 선택됩니다. 상당한 공회전을 방지하기 위해 가공이 시작되고 공구와 공작물이 변경되는 시작 위치는 공구가 공작물에 최대한 가깝게 설정됩니다.
기계 변위 측정 시스템의 공간에서 "바인딩"을 위해 0(기준) 기준점이 사용됩니다. 기계가 켜질 때마다 이 지점은 측정 시스템을 기계 영점에 "연결"합니다.
부품 가공 중 절삭공구 교환 시 가공결과와 요구사항의 불일치(정밀도 저하, 거칠기 증가, 진동 등)가 발생할 수 있습니다. 이 경우 신속하게 조치를 취해야 합니다. 프로그램을 수정합니다. 구멍을 드릴링할 때 수정이 필요한 가공 오류가 발생할 수 있습니다.
공구의 길이와 반경에 대해 두 가지 유형의 보정이 가능합니다.
첫 번째 경우 드릴의 길이 또는 커터 홀더의 오버행 수정은 다음을 사용하여 수행됩니다. 팀 H수정 값에 해당하는 일련의 숫자로 예를 들어, 프레임 N 060 T 02 H 15
도구 번호 2에 대해 15mm 길이 오프셋의 도입을 나타냅니다.
두 번째 경우는 공구 반경의 수정을 제공하며 윤곽을 밀링할 때 원추형 및 모양의 표면을 선삭할 때 공구의 반경 표면 중심의 궤적이 표면의 모양에 대해 등거리여야 하기 때문입니다( 그림 11).
다음은 커터 반경 보정을 위한 프로그램의 일부입니다.
N 035 G 81 X +25 Z +4 I +7 ………………………………………………………. 가공 루프에 대한 설명 ………………………………………………………. |
그림 11- 커터 반경 보정 |
등거리를 따라 밀링을 제공하는 프로그램의 일부(그림 12)
N 005 G 90 G 00 X 0 Y 0 S 1000 T01 M 03
N 006 G 41 G 01 X 220 Y 100 F 100
N 007 X 220 Y 430 F 50
N 008 G 02 G 17 X 370 Y 580 I 370 J 430
N 009 G 01 X 705 Y 580
N 010 X 480 Y 190
N 011 X 220 Y 190
N 012 G 00 X 0 Y 0 05M
블록 N 006의 기능 G 41(커터가 공작물 왼쪽에 있는 경우 커터 직경 보정)은 커터 중심이 가공할 표면에 대해 등거리로 이동하도록 합니다.
경우에 따라 가공면의 거칠기를 줄이고 진동을 없애기 위해 이송을 조정해야 하는 경우가 있습니다. 이를 위해서는 제어판에서 새 이송 값을 설정하고 메모리에 입력해야 합니다. CNC 장치의
그림 12- 외부 윤곽 밀링 시 등거리의 커터 이동
CNC 기계의 설계 기능.
CNC 기계는 높은 신뢰성을 유지하면서 첨단 기술 능력을 갖추고 있습니다. CNC 기계의 설계는 원칙적으로 조합을 보장해야 합니다. 다양한 종류가공(선삭 - 밀링, 밀링 - 연삭), 공작물 로딩 용이성, 부품 언로딩(산업 로봇을 사용할 때 특히 중요), 교환 가능한 도구의 자동 또는 원격 제어 등
같은 목적의 기존 기계를 능가하는 높은 제조 정밀도와 기계 강성에 의해 가공 정밀도의 향상이 이루어집니다. 왜 그들은 운동 학적 체인의 길이를 줄입니까? 가능한 경우 자율 드라이브를 변경하고 기계 기어 수를 줄입니다. CNC 기계의 드라이브도 고속을 제공해야 합니다.
피드 드라이브의 전송 메커니즘에서 갭을 제거하고 가이드 및 기타 메커니즘의 마찰 손실을 줄임으로써 정확도 향상도 촉진됩니다. 공작 기계의 피드백 센서를 사용하여 진동 저항을 개선하고 열 변형을 줄입니다. 열 변형을 줄이려면 예를 들어 기계 및 유압 시스템의 예열에 의해 촉진되는 기계 메커니즘의 균일한 온도 체제를 보장해야 합니다. 온도 센서 신호에서 피드 드라이브로 보정을 도입하여 기계의 온도 오류를 줄일 수도 있습니다.
베이스 부품(베드, 기둥, 베이스)은 추가 보강재를 도입하여 더욱 단단해졌습니다. 이동식 베어링 요소(캘리퍼, 테이블, 스키드)도 강성을 높였습니다. 예를 들어 테이블은 세로 및 가로 모양이 있는 상자 모양으로 구성됩니다. 기본 부품은 주조 또는 용접됩니다. 이러한 부품을 폴리머 콘크리트 또는 합성 화강암으로 만드는 경향이 있어 기계의 강성과 내진동성을 더욱 증가시킵니다.
CNC 기계의 가이드는 높은 내마모성과 낮은 마찰력을 가지므로 서보 드라이브의 출력을 줄이고 움직임의 정확도를 높이며 서보 시스템의 불일치를 줄일 수 있습니다.
마찰 계수를 줄이기 위해 프레임과 캘리퍼의 슬라이딩 가이드는 슬라이딩 쌍 "강철(또는 고품질 주철) - 플라스틱 코팅(형광체 등)" 형태로 생성됩니다.
롤링 가이드는 내구성이 높고 마찰이 적으며 마찰 계수는 이동 속도와 거의 무관합니다. 롤러는 롤링 요소로 사용됩니다. 예압은 가이드의 강성을 2 .. 3배 증가시키며 조정 장치는 예압을 생성하는 데 사용됩니다.
CNC 기계용 드라이브 및 컨버터. 마이크로프로세서 기술의 발전과 관련하여 컨버터는 완전한 마이크로프로세서 제어(디지털 컨버터 또는 디지털 드라이브)가 있는 피드 및 메인 무브먼트 드라이브에 사용됩니다. 디지털 드라이브는 직류 또는 교류로 작동하는 전기 모터입니다. 구조적으로 주파수 변환기, 서보 드라이브, 메인 스타트 및 리버스 장치는 별도의 전자 제어 장치입니다.
CNC 기계용 피드 드라이브. 드라이브로는 디지털 컨버터로 제어되는 동기식 또는 비동기식 기계인 모터가 사용됩니다. CNC 기계용 비수집기 동기(밸브) 모터는 희토류 원소를 기반으로 하는 영구 자석으로 만들어지며 피드백 센서와 브레이크가 장착되어 있습니다. 비동기식 모터는 동기식 모터보다 덜 자주 사용됩니다. 피드 모션 드라이브는 가능한 최소 간격, 짧은 가속 및 감속 시간, 큰 마찰력, 드라이브 요소의 감소된 가열 및 넓은 제어 범위가 특징입니다. 볼 및 유압식 스크류 기어, 롤링 가이드 및 유압식 가이드를 사용하여 짧은 운동 체인이 있는 백래시 기어박스 없이 이러한 특성을 보장할 수 있습니다.
CNC 기계의 주요 모션 드라이브는 일반적으로 모터입니다. 교류– 고전력 및 직류용 – 저전력용. 드라이브는 큰 과부하를 감지하고 공기 중 금속 먼지, 칩, 오일 등이 있는 상태에서 작동하는 3상 4극 비동기식 모터입니다. 따라서 외부 팬이 설계에 제공됩니다. 방향이나 독립적인 좌표를 제공하는 데 필요한 스핀들 위치 센서와 같은 다양한 센서가 엔진에 내장되어 있습니다.
비동기식 모터를 제어하기 위한 주파수 변환기의 제어 범위는 최대 250입니다. 변환기는 다음과 같습니다. 전자 기기마이크로프로세서 기술을 기반으로 구축되었습니다. 작업의 프로그래밍 및 매개변수화는 디지털 또는 그래픽 디스플레이가 있는 내장 프로그래머에서 수행됩니다. 제어 최적화는 모터 매개변수를 입력한 후 자동으로 이루어집니다. 소프트웨어에는 드라이브를 구성하고 작동시키는 기능이 포함되어 있습니다.
CNC 기계의 스핀들은 넥, 시트 및 위치 지정 표면의 내마모성이 증가하여 더 정확하고 단단해집니다. 스핀들의 설계는 도구의 자동 언클램핑 및 클램핑을 위한 내장 장치, 적응 제어 및 자동 진단에 사용되는 센서로 인해 훨씬 더 복잡합니다.
스핀들 지지대는 다양한 작동 조건, 증가된 강성 및 작은 온도 변형에서 오랫동안 스핀들의 정확도를 보장해야 합니다. 스핀들 회전의 정확성은 주로 베어링의 고정밀 제조에 의해 보장됩니다.
스핀들의 베어링에서 가장 자주 롤링 베어링을 사용합니다. 클리어런스의 영향을 줄이고 지지대의 강성을 높이기 위해 베어링은 일반적으로 예압으로 설치되거나 전동체의 수가 증가합니다. 스핀들 베어링의 플레인 베어링은 축 방향 또는 반경 방향으로 주기적(수동) 또는 자동 간극 조정 장치가 있는 경우에만 덜 자주 사용됩니다. 정밀 기계에서는 압축 공기가 샤프트 넥과 베어링 표면 사이에 위치하여 베어링의 마모 및 가열을 줄이고 회전 정확도를 높이는 에어로스테틱 베어링이 사용됩니다.
포지셔닝 드라이브(즉, 프로그램에 따라 기계의 작업 본체를 필요한 위치로 이동)는 높은 강성을 가져야 하며 작업 본체의 저속에서 부드러운 움직임, 고속 보조 움직임(최대 10m/min 및 더).
CNC 공작 기계의 보조 메커니즘에는 공구 교환기, 칩 제거, 윤활 시스템, 클램핑 장치, 로딩 장치 등이 포함됩니다. CNC 기계의 이 메커니즘 그룹은 기존 범용 기계에 사용되는 유사한 메커니즘과 크게 다릅니다. 예를 들어, CNC 기계의 생산성이 높아짐에 따라 단위 시간당 하강 칩이 급격히 증가하여 처리 영역에서 칩을 제거하기 위한 특수 장치를 만들 필요가 생겼습니다. 로딩 중 시간 손실을 줄이기 위해 다른 공작물을 처리하는 동안 공작물을 동시에 설치하고 부품을 제거할 수 있는 장치가 사용됩니다.
자동 공구 교환 장치(잡지, 자동 작동 장치, 터렛)는 공구 교환에 소요되는 최소 시간, 높은 작동 신뢰성, 공구 위치의 안정성, 즉 공구 교환에 소요되는 시간을 최소화해야 합니다. 매거진 또는 터렛에 필요한 용량을 갖기 위해 반복적인 공구 변경 중 오버행 크기와 축 위치의 일정.
터렛은 가장 간단한 도구 교환기입니다. 도구의 설치 및 클램핑은 수동으로 수행됩니다. 작업 위치에서 스핀들 중 하나는 기계의 메인 드라이브에 의해 구동됩니다. 터렛은 터닝, 드릴링, 밀링, CNC 다목적 기계에 설치됩니다. 4~12개의 도구가 헤드에 고정되어 있습니다.
통제 질문:
주요 무엇 디자인 특징 CNC 기계.
기본 부품의 설계 특징, 주 이동 및 이송 이동의 드라이브, 그리고 CNC 기계의 보조 메커니즘을 나열하십시오.
CNC 선반.
CNC 선반은 실외 및 내부 처리회전체와 같은 복잡한 공작물. 그들은 CNC 기계 공원에서 가장 큰 제품 그룹을 구성합니다. CNC 선반에서는 선삭, 절단, 드릴링, 스레딩 y 및 기타.
CNC 선반의 분류는 다음 기능을 기반으로 합니다.
스핀들 축의 위치(수평 및 수직 기계);
작업에 사용된 도구의 수(하나 및 여러 도구 기계);
고정 방법(캘리퍼, 포탑, 공구 매거진)
수행된 작업 유형(센터, 카트리지, 카트리지 센터, 회전 목마, 바 기계;
자동화 정도(반자동 및 자동).
CNC 센터 머신은 직선 및 곡선 윤곽이 있는 샤프트와 같은 공작물을 처리하는 데 사용됩니다. 이 기계에서는 프로그램에 따라 커터로 실을자를 수 있습니다.
CNC가 있는 카트리지 탱크는 플랜지, 기어, 커버, 풀리 등과 같은 부품의 축 구멍에서 가공, 드릴링, 리밍, 카운터싱킹, 카운터싱킹, 태핑을 위해 설계되었습니다. 내부 절단이 가능하고 외부 스레드프로그램으로.
CNC 척 센터 머신은 회전 호이스트와 같은 다양한 복잡한 공작물의 외부 및 내부 가공에 사용되며 센터 터닝 및 척 머신의 기술력을 가지고 있습니다.
회전 목마 CNC 기계는 복잡한 몸체의 공작물을 처리하는 데 사용됩니다.
CNC 선반(그림 12)에는 터렛 또는 도구 매거진이 장착되어 있습니다. 터렛은 4, 6 및 12위치이며 각 위치에는 공작물의 외부 및 내부 처리를 위한 두 개의 도구가 장착될 수 있습니다. 헤드의 회전 축은 스핀들 축에 평행하거나 수직 또는 비스듬할 수 있습니다.
기계에 2개의 터렛을 설치하면 한쪽(1)에는 외부 가공용 공구가, 다른 한쪽(2)에는 내부 가공용 공구가 고정된다(그림 13 참조). 이러한 헤드는 서로에 대해 동축으로 위치하거나 다른 축 배열을 가질 수 있습니다. 포탑의 인덱싱은 일반적으로 헤드 인덱싱의 높은 정확도와 강성을 제공하는 경화 및 연마된 평평한 톱니면 커플링을 사용하여 수행됩니다. 기계 외부의 크기에 맞게 조정되는 터렛의 홈에 특수 장치에 교체 가능한 교체 가능한 도구 블록이 설치되어 생산성과 가공 정확도가 크게 향상됩니다. 포탑의 절단 블록은 프리즘을 기반으로 하거나 원통형 섕크 6(그림 14)의 도움을 받습니다. 커터는 클램핑 바 3을 통해 나사로 고정됩니다. 센터의 높이를 따라 커터를 설정하기 위해 라이닝 2가 사용됩니다.서로 45 ° 각도에 위치한 두 개의 조정 나사 5는 조정하는 동안 커터의 상단을 지정된 좌표로 이동합니다. 절삭 영역으로의 냉각수 공급은 몸체 1의 채널을 통해 이루어지며 노즐 4로 끝나며 냉각수 공급 방향을 조정할 수 있습니다.
공구 매거진(용량 8~20 공구)은 거의 사용되지 않습니다. 하나의 공작물을 선삭하는 데 실제로 10개 이상의 공구가 필요하지 않기 때문입니다. 공구 수명이 짧은 난삭재 선삭의 경우에는 많은 공구를 사용하는 것이 좋습니다.
선반과 밀링 머신 사이의 라인 지우기, 오프 센터 드릴링 추가, 윤곽 밀링(즉, 스핀들 회전이 프로그래밍됨)으로 인해 선반의 기술 기능 확장이 가능합니다. 경우에 따라 정렬되지 않은 공작물 요소의 나사산이 가능합니다.
통제 질문:
CNC 선반은 수행되는 작업 유형에 따라 어떻게 분류됩니까?
CNC 선반에는 어떤 도구 홀더가 사용됩니까?
절단 블록은 기계의 터렛을 어떻게 기반으로 합니까?
CNC 밀링 머신
CNC 밀링 머신은 복잡한 모양의 공작물의 평면 및 공간 표면을 처리하도록 설계되었습니다. CNC 밀링 머신의 디자인은 기존 밀링 머신의 디자인과 유사하지만 후자와의 차이점은 성형 중 NC를 따라 움직이는 자동화에 있습니다.
CNC 밀링 머신의 분류는 다음 기능을 기반으로 합니다.
스핀들 위치(수평 및 수직);
테이블 또는 밀링 주축대의 좌표 이동 수;
사용된 도구의 수(단일 도구 및 다중 도구)
기계 스핀들에 도구를 설치하는 방법(수동 또는 자동).
레이아웃별 밀링 머신 CNC 기계는 네 그룹으로 나뉩니다.
수직 - 크로스 테이블이 있는 밀링 머신;
콘솔 밀링 머신;
세로로 - 밀링 머신;
다목적 공구 기계.
크로스 테이블이 있는 수직 밀링 머신(그림 15, a)에서 테이블은 세로(X축) 및 가로(Y축) 수평 방향으로 이동하고 밀링 헤드는 수직 방향(Z축)으로 이동합니다.
콘솔 밀링 머신(그림 15, b)에서 테이블은 3개의 좌표축(X, Y 및 Z)을 따라 이동하고 주축대는 움직일 수 없습니다.
이동식 크로스바가있는 세로 밀링 머신 (그림 15, c)에서 테이블은 X 축을 따라, 스핀들 헤드는 Y 축을 따라, 가로 주축은 Z 축을 따라 이동합니다. 부재(그림 15, d)에서 테이블은 X축을 따라 이동하고 주축대는 Y 및 Z축을 따라 이동합니다.
범용 공구 밀링 머신(그림 15,e)에서 테이블은 X축과 Y축을 따라 이동하고 주축대는 Z축을 따라 이동합니다.
그림 15 – 밀링 머신의 다양한 수정에서 좌표계:
a) - 크로스 테이블이 있는 밀링 머신 b) 콘솔 밀링 머신; c) 움직일 수 있는 크로스 멤버가 있는 세로 밀링 머신; d) 고정 크로스바가 있는 세로 밀링 머신; e) 넓은 범용 밀링 머신.
밀링 머신에는 주로 직사각형 및 윤곽 CNC 장치가 장착되어 있습니다.
직사각형 제어( 상징기계 모델에서 - Ф 2) 기계 테이블은 좌표 축 중 하나와 평행한 방향으로 이동하므로 복잡한 표면을 처리할 수 없습니다. 직사각형 제어 장치가 있는 기계는 밀링 평면, 경사, 선반, 홈, 높이가 다른 보스 및 기타 유사한 표면에 사용됩니다.
윤곽 제어(기계 모델의 기호 - F 3 및 F 4)를 사용하면 테이블의 궤적이 더 복잡해집니다. 윤곽 제어가 있는 기계는 다양한 캠, 다이, 몰드 및 기타 유사한 표면을 밀링하는 데 사용됩니다. 제어되는 좌표의 수는 일반적으로 3개이며 경우에 따라 4개 또는 5개입니다. 모션의 윤곽 제어를 사용하면 적어도 두 좌표축을 따라 동시에 성형이 수행됩니다.
경우에 따라 CNC 시스템은 중대형 생산에서 단순한 모양의 공작물을 처리할 때 밀링 머신에도 사용됩니다.
CNC 밀링 머신에서는 비동기식 전기 모터(이 경우 기어박스가 있음) 또는 DC 전기 모터가 메인 무브먼트의 구동 장치로 사용됩니다.
직사각형 CNC가 있는 소형 밀링 머신에서는 하나의 DC 구동 모터와 자동으로 전환되는 전자기 클러치가 있는 기어박스가 사용되며 윤곽 제어가 있는 중장비에서는 각 제어 좌표 이동이 자동 DC 전기 드라이브에서 수행됩니다.
CNC 밀링 머신의 피드 이동 드라이브에는 엔진에서 직접 집행 기관으로 이동을 전달하는 짧은 운동학적 체인이 있습니다.
캔틸레버 수직 밀링 머신 모드의 장치를 고려하십시오. 6R13F3. 이 기계는 캔틸레버입니다. 그의 테이블은 수평면에서 (X 및 Y 좌표를 따라) 작업 이동이 있고 (콘솔과 함께) 수직 방향으로 (W 좌표를 따라) 설치 이동이 있습니다. Z 좌표를 따라 움직이는 작업에는 스핀들이 있는 슬라이더가 있습니다. 침대 8은 기계의 장치와 메커니즘이 장착되는 기반입니다. 전면에 프레임에는 케이스 9로 덮인 수직 가이드가있어 콘솔 1이 이동합니다.슬라이드 2는 테이블 3이 움직이는 세로 가이드를 따라 수평 가이드에 장착됩니다.안전 요구 사항에 따라 슬라이더는 보호 실드 4가 있습니다. 기계 뒤에는 전기 장비와 CNC가 있는 캐비닛 10이 있습니다.
그림 16 - 수직 밀링 머신 모드 6R13F3:
1-콘솔; 2인승; 3 테이블; 4-보호 방패; 5-스핀들: 6-밀링 주축대; 7-슬라이더; 8인실 9-케이스;
전기 장비가 있는 10개 캐비닛.
통제 질문:
CNC 밀링 머신의 어떤 레이아웃을 알고 있습니까?
밀링 머신이 장착된 CNC 시스템은 무엇입니까?
CNC 드릴링 머신
수직 - 수동 제어가 가능한 유사한 기계와 달리 CNC 드릴링 머신에는 X 및 Y 축을 따라 공작물을 자동으로 이동시키는 크로스 테이블이 장착되어 있으므로 도체 또는 예비 마킹이 필요하지 않습니다.
CNC 방사형 드릴링 머신은 X축을 따라 이동 가능한 컬럼, Y축을 따라 이동 가능한 슬리브와 드릴링 스핀들이 장착되어 Z축을 따라 이동하는 슬리브를 가지고 있습니다.또한 슬리브는 수직 방향으로 이동할 수 있습니다 적용시.
X 및 Y 축을 따라 드릴링 머신의 작업 바디가 자동으로 이동하여 구멍 만들기 및 밀링이 실행됩니다.
드릴링 머신에는 프로그램에서 지정한 위치로 작업 본체를 자동으로 설정할 수 있는 위치 CNC가 장착되어 있습니다. CNC 드릴링 머신의 절삭 공구는 스핀들의 원추형 구멍에 직접 고정되거나 중간 부싱과 맨드릴을 사용하여 고정됩니다.
CNC가 장착 된 수직 드릴링 머신 모델 2R135F2-1의 일반적인 모습은 그림 17에 나와 있습니다. 머신 1을 기반으로 지지대 4가 움직이는 직사각형 수직 가이드를 따라 기둥 10이 장착되고, 포탑 나르기 3. 기둥 10에 스피드박스 5와 피드 리듀서 장착 6. 크로스 테이블의 썰매 2가 베이스 1의 수평 가이드를 따라 이동하고, 테이블의 상부 11이 가이드를 따라 이동 썰매의. 기계의 오른쪽에는 전기 장비가 있는 캐비닛 8과 CNC 9가 있습니다. 기계에는 펜던트 7 제어판이 있습니다.
그림 17 – 수직 드릴링 머신 모델 2R135F2:
1 베이스; 2인승; 3-포탑; 4- 지원; 5단 박스; 6-피드 감속기; 7 펜던트 콘솔; 8- 전기 장비가 있는 캐비닛; 9-CNC; 10열, 11열 테이블.
통제 질문:
수직의 근본적인 차이점은 무엇입니까? 드릴링 머신 CNC 또는 비 CNC?
수직 드릴링 머신이 장착된 CNC 시스템은 무엇입니까?
CNC 연삭기
CNC 시스템에는 표면 연삭, 원형 및 센터리스 연삭 및 기타 기계가 장착되어 있습니다. CNC 연삭기를 만들 때 다음과 같은 이유로 설명되는 기술적 어려움이 발생합니다. 연삭 공정은 한편으로는 최소한의 크기 분산으로 높은 정확도와 표면 품질을 얻을 필요가 있다는 특징이 있으며 다른 한편으로는 연삭 휠의 치수 정확도가 급격히 손실되는 특징이 있습니다. 작동 중 심한 마모. 이 경우 기계에는 연삭 휠의 마모를 자동으로 보정하는 메커니즘이 필요합니다. CNC는 LED 시스템의 왜곡, 온도 오류, 공작물 허용치의 차이, 좌표를 따라 이동할 때의 기계 오류 등을 보정해야 합니다. 측정 시스템은 위치 정확도에 대해 엄격한 공차를 제공하는 분해능을 가져야 합니다. 예를 들어, 원형 연삭기에서 이러한 장치는 2 × 10 -5 mm 이하의 상대 오차로 가공 중 공작물의 직경을 연속적으로 측정합니다. 테이블의 길이 방향 움직임의 제어는 0.1mm 이하의 오차로 수행됩니다.
연삭기의 경우 3~4개의 좌표를 제어하는 CNC 방식의 시스템이 사용되지만 여러 원으로 작업하는 기계에서는 5, 6, 8개의 좌표까지 제어가 가능합니다. 작업자와 연삭기의 CNC 시스템 간의 관계는 대부분의 경우 디스플레이를 사용하여 대화식으로 수행됩니다. 제어 시스템은 기계의 신뢰성을 높이는 내장형 진단 시스템을 사용합니다.
CNC 원형 연삭기는 가장 일반적이며 스핀들, 전기 모터의 샤프트, 기어박스, 터빈 등과 같은 다단 부품을 하나의 설치에서 처리할 때 최대 효과를 제공합니다. 주로 공작물 세팅 및 완성품 제거, 다음 샤프트 저널 가공을 위한 재설정, 측정 등의 비생산 시간을 단축함으로써 생산성이 향상됩니다. CNC 원통형 그라인더에서 다단 샤프트를 가공할 때, 수동 제어에 비해 1.5~2배의 시간 절약.
센터리스 원통형 연삭기는 소형 및 큰 직경길이 제한이 없는 부품, 얇은 벽 부품, 복잡한 외부 프로파일(피스톤, 너클 등)이 있는 부품. 대량 생산 조건에서 이러한 기계는 높은 생산성과 가공 정확도가 특징입니다. 소규모 및 개별 생산에서 이러한 기계의 사용은 재조정의 복잡성으로 인해 제한됩니다. 센터리스 원통형 연삭기의 응용 프로그램 확장은 드레싱 서클에 소요되는 많은 시간과 기계 설정의 복잡성이라는 두 가지 요인으로 인해 방해를 받으며 상당한 시간 투자와 우수한 자격을 갖춘 인력이 필요합니다. 이것은 연삭 및 구동 원이 기계 설계에 사용된다는 사실에 의해 설명됩니다. 연삭 및 구동 원의 표면에 적절한 모양을 제공하는 드레싱 장치; 지원 나이프의 위치를 설정하는 기능; 공작물 및 드레싱에 대한 연삭 휠의 보상 피드 메커니즘과 공작물 및 드레싱에 대한 구동 원; 로딩 및 언 로딩 장치의 위치를 설정합니다.
CNC를 사용하여 센터리스 원통형 연삭기의 다중 좌표 작동을 제어할 수 있습니다. 공작 기계의 제어 시스템에서 도구의 궤적(원, 다이아몬드), 사람과의 상호 작용 수정을 계산하는 소프트웨어 모듈이 사용됩니다. 다양한 기하학적 모양(원뿔, 볼 등)을 가진 부품을 처리하기 위해 소프트웨어6 모드 관리자, 보간기 및 드라이브 제어 모듈이 생성됩니다.
처리 및 편집할 때 결합된 제어 좌표의 수는 연삭 및 구동 원을 드레싱하기 위해 별도로 두 개 또는 세 개의 좌표를 포함하여 최대 19개까지 도달할 수 있습니다.
연속 생산 조건에서 CNC를 사용하면 연삭 및 드레싱 주기를 유연하게 구성할 수 있으므로 다른 제품을 처리하기 위해 기계를 신속하게 재조정할 수 있습니다.
다축 CNC 시스템의 존재는 기계의 다용성, 소량의 휠 피드를 제공하여 연삭 및 드레싱 프로세스를 효과적으로 제어할 수 있습니다.
센터리스 원형 연삭기의 CNC는 집합 원리에 따라 제작됩니다(예: 일본 회사의 기계). 기계에는 CNC에서 기계를 제어하기 위한 4가지 옵션 중 하나를 설치할 수 있습니다.
하나의 제어 좌표는 연삭 휠의 가로 이송입니다.
두 개의 제어된 좌표 - 동기화를 위한 연삭 휠과 룰링 다이아몬드의 가로 이송;
세 가지 제어 좌표 - 연삭 휠의 가로 이송과 드레싱 중 다이아몬드의 가로 및 세로 이송;
5개의 제어된 좌표 - 연삭 휠의 횡방향 이송과 연삭 및 구동 휠을 드레싱할 때 다이아몬드의 횡방향 및 종방향 피드.
CNC를 사용하여 센터리스 원통형 연삭기를 제어하면 드레싱 장치(복사 눈금자, 다이아몬드 공급 메커니즘 등을 거부한 결과), 드레싱 장치의 길이 방향 이동을 위한 드라이브, 연삭 및 구동 휠용 미세 이송 메커니즘, 제어 및 제어 - 조정 장치 등
통제 질문:
CNC 연삭기 제작의 기술적 어려움은 무엇입니까?
연삭기가 장착된 CNC 시스템은 무엇입니까?
CNC 다목적 기계
복합 가공기(MS)에 CNC 장치 및 자동 공구 교환을 장착하여 가공 중 보조 시간을 크게 줄이고 전환의 이동성을 높입니다. 보조 시간의 단축은 좌표에 의한 공구(공작물)의 자동 설정, 사이클의 모든 요소 실행, 공구 교환, 틸팅 및 공작물 변경, 절삭 모드 변경, 제어 작업 수행 및 높은 보조 움직임의 속도.
목적에 따라 MS는 몸체 및 평면 부품의 공작물 처리와 회전 몸체와 같은 부품의 공작물 처리의 두 그룹으로 나뉩니다. 첫 번째 경우에는 드릴링-밀링-보링 그룹의 MC가 가공에 사용되고 두 번째 경우에는 선삭 및 연삭 그룹의 MC가 사용됩니다. 첫 번째 그룹의 MS를 가장 일반적으로 사용하는 것으로 간주합니다.
MS에는 다음이 있습니다. 형질: 터닝, 보링, 밀링, 드릴링, 카운터싱킹, 리밍, 스레딩, 품질 관리를 포함한 집중 작업(황삭, 반정삭 및 정삭)을 위한 다수의 절삭 공구를 장비에 제공하는 공구 매거진의 존재 처리 등; 마무리 작업의 높은 정확도(6…7등급).
MS 제어 시스템은 신호, 기계 노드 위치의 디지털 표시, 다양한 형태의 적응 제어가 특징입니다. MS는 기본적으로 터렛과 스핀들 헤드가 있는 단일 스핀들 기계입니다.
신체 부위의 공작물을 가공하기 위한 다목적 기계(머시닝 센터). 신체 부위의 블랭크 가공용 MS는 수평 및 수직 기계로 구분됩니다(그림 18).
수평 MS 모드. IR-500MF4, 신체 부위 가공용으로 설계되었습니다. 이 기계에는 랙 7의 수직 레일을 따라 움직이는 스핀들 헤드 4가 있습니다. 도구 매거진 6은 랙 7에 고정되어 있습니다. 공구는 주축대의 상부 위치에 있는 자동 작동자(5)에 의해 스핀들(3)에 설치됩니다. 공작물은 X 좌표를 따라 이동하는 테이블 1에 배치되고 프레임의 오른쪽 끝에는 공작물이 있는 두 개의 위성 테이블이 설치된 턴테이블 8이 있습니다.
그림 18 - 다목적 기계(머시닝 센터) 모드 IR-500MF4:
1 테이블 로터리; 2-장치; 3-스핀들; 4-스핀들 주축대; 5-자동 연산자; 6 도구 매거진; 7 이동식 랙; 8-회전 플랫폼; 9개 테이블 위성; 10-가이드; 11-CNC; 전기 장비가 있는 12개 캐비닛.
밀링, 드릴링 및 기타 CNC 기계에서 처리하는 것과 비교하여 MS에서 공작물 처리에는 여러 가지 기능이 있습니다. 공작물의 설치 및 고정은 한 번의 설치(가공할 표면에 대한 도구의 자유로운 접근)에서 모든 면에서 처리를 보장해야 합니다. 이 경우에만 재설치 없이 다각적 처리가 가능하기 때문입니다.
MS에서의 가공은 일반적으로 공작물이 정지 및 압정을 사용하여 고정되기 때문에 특수 장비가 필요하지 않습니다. MS에는 스핀들 헤드, 기계 옆 또는 다른 곳에 배치되는 공구 매거진이 장착되어 있습니다. 밀링 평면의 경우 작은 직경의 커터가 사용되며 가공은 선으로 수행됩니다. 얕은 구멍 가공에 사용되는 캔틸레버 공구는 강성이 높아져 지정된 가공 정확도를 제공합니다. 동일한 축에 있지만 평행 공작물 기계에 위치한 구멍은 양쪽에서 보링되어 공작물로 테이블을 돌립니다. 신체 부위의 블랭크에 동일한 표면과 구멍 그룹이 있는 경우 기술 프로세스 및 제조 프로그램의 편집을 단순화하고 처리 생산성을 높이기 위해(보조 시간 감소 결과) 일정한 주기 가장 자주 반복되는 움직임(드릴링, 밀링 시). 이 경우 첫 번째 구멍(표면)의 처리 주기만 프로그래밍되고 나머지는 해당 위치의 좌표(X 및 Y)만 지정됩니다.
예를 들어, 그림 19는 소프트웨어에 포함되어 있고 IR320PMF4 모델의 기계에서 처리할 때 사용되는 일부 고정 사이클을 보여줍니다.
그림 19 - 다목적 기계 모델 IR320PMF4의 미리 준비된 처리 주기:
1-외부 윤곽 밀링(원호 보간 포함), 칩 제거를 위한 드릴 출구가 있는 2-깊이 드릴링, 계단식 구멍의 3-보링; 스핀들 방향을 사용하는 4백 카운터보어; 특수 맨드릴을 사용하여 Ø 125mm의 구멍을 5-보링합니다. 내부 끝의 윤곽을 따라 6 밀링; 윤곽 밀링에 의한 7-카운터보어(원호 보간 포함); 8홀 드릴링 Ø 30mm; 9-스레딩(최대 M16); 디스크 커터로 내부 홈 10-밀링(원호 보간 포함); 11개의 카운터보어 구멍; 커터로 끝단을 12-밀링합니다. 13-회전체와 같은 표면 처리.
기계 모델 IR500MF4의 위성 (PS) 자동 변경 장치가 그림 20에 나와 있습니다. PS 11은 유압 실린더 10 및 13이 장착되는 플랫폼 7(용량 2 PS)에 설치됩니다. 유압 실린더에는 T자형 그립(14, 6)이 있습니다. 플랫폼에 설치될 때(화살표 B를 따라 이동) PS 컷아웃(12)은 로드의 캡(14)과 맞물립니다. 플랫폼에서 PS는 롤러 9를 기반으로 하며 롤러 8에 의해 중앙(측면에서)입니다(PS의 초기 위치는 대기 위치에 있음). 유압 실린더(10)의 로드의 이동은 위성을 (롤러 상에서) 구르게 한다.
그림 20 - 장치 위성 자동 변경 장치:
1-베이스 플레이트; 2-조정 볼트; 3- 기어 휠; 4-레일; 5, 13,16-유압 실린더; 6, 14-로드 캡처; 7-플랫폼; 8.9-롤러; 10, - 유압 실린더 로드; 11개 장치 위성; 12개 모양의 컷아웃, 15개 스탠드.
유압 실린더(13)의 로드가 움직일 때, 그리퍼(6)는 (가이드 로드를 따라) 이동하고 롤러(9, 8)를 따라 (화살표 A 방향으로) PS를 굴려서 위성이 자동으로 있는 기계의 턴테이블 위로 굴립니다. 클램프로 내렸습니다. 캡처의 결과 6은 PS에서 분리되고 기계 테이블(위성이 부착된)은 처리 영역으로 고속으로 이동합니다.
공작물은 이전 공작물 처리 중(PS가 대기 위치에 있을 때) 또는 사전에 기계 외부에서 위성에 고정됩니다.
공작물 처리 후 기계 테이블은 자동으로 (고속으로) 위성 변경 장치의 오른쪽으로 이동하고 PS의 형상 홈이 그립 6 아래에 있는 위치에서 정지합니다. 턴테이블 유압 실린더가 잠금 해제됩니다. 그 후 PS가 그리퍼 6과 맞물리고 오일이 유압 실린더 13의 로드 끝으로 들어가면 로드가 맨 오른쪽 위치로 이동하고 새틀라이트는 공작물에서 플랫폼 7로 이동합니다. 여기서 PS는 새 공작물이 있는 플랫폼 이미 있습니다. 위성을 교체하기 위해 플랫폼은 유압 실린더 5 및 16에 의해 구동되는 레일 4와 결합된 기어 휠 3에 의해 180° 회전됩니다(머신 15에서).
플랫폼 7은 기초에 고정 고정된 베이스 플레이트 1의 돌출부에 나사로 고정된 조정 나사 2와 7을 사용하여 기계의 턴테이블과 정확하게 정렬됩니다.
통제 질문:
터닝, 밀링, 드릴링 및 기타 CNC 기계와 다목적 CNC 기계의 차이점은 무엇입니까?
신체 부위의 공작물을 가공하는 다목적 기계의 주요 구성 요소에 대해 알려주십시오.
CNC 가공
금속 가공 장비를 위한 현대적인 수치 제어 시스템의 기초는 하드웨어 및 소프트웨어 분야의 첨단 기술 솔루션입니다. 정보 기술및 기술 구성 요소.
개방형 클래스 아키텍처의 CNC 시스템은 기계 수치 제어 장치의 역사에서 새로운 페이지를 열었습니다. CNC의 기본 플랫폼으로 표준 또는 산업용 개인용 컴퓨터를 사용하면 방대한 메모리 리소스, 컴퓨팅 성능, 표준화된 통신 도구(인터페이스), 모든 종류의 시스템, 도구 및 사용자 소프트웨어, 그리고 훨씬 더 빠르게 성장하는 정보 기술 산업에 의해 제공됩니다.
제안된 몇 가지를 살펴보자. 러시아 시장가장 인기있는 외국 시스템과 개별 국내 개발에 경의를 표합니다. 우리는 완전한 검토를 가장하지 않으며, 우리의 목표는 근본적인 결정에 대해 이야기하는 것입니다.
외국 시스템
지멘스
지난 30년 동안 Siemens는 CNC 공작 기계 시장의 트렌드 세터 중 하나였습니다. 오늘날 지멘스는 무엇을 상징합니까? CNC 분야에서 회사는 범위를 확장했으며 이제 대규모 시리즈에서 작업하는 복잡한 기계뿐만 아니라 CNC 시스템을 제공합니다.
단순 기계의 경우 이 회사는 CNC 제품군(선반용 2축 + 스핀들 및 밀링 머신용 3축 + 스핀들)을 제공합니다. 드라이브로 최신 3극 스테퍼 모터(CNC Sinumerik 802S 포함)와 아날로그 인터페이스가 있는 AC 서보 드라이브(CNC Sinumerik 802C 포함)를 모두 사용할 수 있습니다.
스테퍼 드라이브는 기계의 전체 비용을 크게 줄일 수 있으므로 일정한 수준을 유지하면서 대기업에 구성 요소를 공급하거나 자체 요구에 따라 작은 일련의 부품을 생산하는 소규모 회사에서 사용하는 가장 단순하고 작은 기계에서 특히 인기가 있습니다. 품질을 높이고 자격을 갖춘 전문가를 찾는 문제를 제거합니다.
아날로그 인터페이스(+/-10 V)가 있는 서보 드라이브를 사용하면 동일한 기계에서 표면 처리의 정확도를 높일 수 있으며, 이는 오늘날 CIS 시장과 매우 관련이 있으며 기계 현대화 작업에 Sinumerik 802C CNC를 사용합니다. , 오래된 드라이브를 그대로 둘 수 있어 현대화 비용이 크게 절감됩니다. 동시에 기계의 생산성은 다음과 같은 사실로 인해 증가합니다. 새로운 시스템 CNC는 작동 시 보다 안정적이며 새로운 CNC 기능을 통해 부품의 처리 시간을 줄일 수 있습니다.
수정 Sinumerik 802C를 사용하면 디지털 기계용 간단한 디지털 디스플레이로 사용할 수 있습니다. 게다가, 그 비용은 시장에 존재하는 고전적인 디스플레이 시스템과 비슷하거나 더 낮습니다.
이러한 CNC에 매우 인접한 Sinumerik 802D 시스템은 다른 축(예: 테이블 제어용)을 추가하고 Simodrive 611U 범용 서보 드라이브와 함께 작동합니다.
보다 복잡한 공작 기계를 위해 Siemens는 CCU1 및 CCU2가 탑재된 이미 신뢰받는 Sinumerik 810D와 NCU 571 및 NCU 572 프로세서가 탑재된 Sinumerik 840D를 제공합니다. 선삭 또는 밀링뿐만 아니라 연삭, 레이저 절단, 펀칭 및 로봇 제어. 이러한 시스템은 Simodrive 611D 디지털 드라이브와 함께 작동하여 기존 아날로그 드라이브에서는 얻을 수 없는 정밀성과 역동성을 달성합니다.
복잡한 성형 기술, 모델 준비 및 카바이드 부품의 고속 가공을 위해 Sinumerik Power 라인이 제공되며 현재 CCU3이 있는 Sinumerik 810D CNC와 NCU 573이 있는 Sinumerik 840D로 대표됩니다. 별도의 라인은 Sinumerik 840Di CNC 시스템입니다. 이것은 표준 산업용 PC를 기반으로 한 이른바 PCNC 제어 시스템입니다. 동시에 사용자 인터페이스와 CNC 코어는 소프트웨어로 구현되며 PLC 컨트롤러와 주변 장치와 드라이브를 연결하는 인터페이스는 단일 슬롯 보드에 있습니다. Sinumerik 802D와 동일한 범용 드라이브 Simodrive 611U가 드라이브로 사용됩니다.
CNC의 새로운 기능의 등장으로 오늘날 기계의 전환 시간을 크게 줄일 수 있습니다. 범용 기계전체 작업 시간의 최대 90%를 차지할 수 있습니다. 다른 기능은 값비싼 도구 파손 및 값비싼 부품 손상을 방지합니다. 공구 마모도 CNC 소프트웨어 기능으로 줄일 수 있습니다. Siemens의 CNC 시스템을 사용하여 표면 처리 품질을 개선하면 부품을 마무리할 필요가 없어져 생산 시간이 단축될 뿐만 아니라(즉, 생산성 증가) 값비싼 기계도 줄일 수 있습니다.
GE 화낙 자동화
GE Fanuc Automation CNC는 높은 작동 안정성과 성능을 요구합니다. 이 회사는 기계 자체의 정보 및 소프트웨어 도구에 대한 액세스를 제공하여 공작 기계의 생산성을 높이는 개방형 및 기존 유형의 CNC를 생산합니다. GE Fanuc CNC 시스템은 연삭, 드릴링, 절단, 밀링, 펀칭, 터닝, 목공 등과 같은 광범위한 작업을 위해 설계되었습니다.
CNC 전통적인 유형.
새로운 CNC 시리즈의 모든 모델에 있는 GE Fanuc CNC 제어 장치는 두께가 60mm에 불과합니다. 장치에 내장된 소형 CNC 인쇄 회로 기판을 통해 최신 LSI 및 표면 실장 기술의 기능을 최대한 활용할 수 있습니다. 기판은 액정 디스플레이 뒤에 장착됩니다. 이 회사는 또한 하나의 CNC 제어 장치와 여러 서보 증폭기를 단일 광섬유 케이블에 연결할 수 있도록 하는 고속 직렬 서보 버스와 소형 I/O 분배 모듈을 개발했습니다. 다양한 입출력 모듈을 기계의 조작반과 제어반에 장착할 수 있어 기계의 전기 자동화량과 크기를 크게 줄일 수 있습니다. CNC를 운영 체제의 최종 장치로 사용할 수 있는 Factolink로 생산 시스템을 향상할 수 있습니다.
CNC 개방형.
CNC의 전체 범위 개방형 GE FANUC는 16i, 18i 및 21i 시리즈에서 개발된 160i, 180i, 210i 및 160is, 180is, 210is 시리즈로 대표됩니다. "is" 시리즈 CNC는 개방형 CNC 중 가장 작고 얇은 제품입니다. MS Windows CE Pocket PC 기능과 호환되는 인쇄 회로 기판은 LCD 컬러 디스플레이 뒤에 장착됩니다. 패널은 최신 LSI 및 표면 실장 기술을 사용하여 설계되었습니다. 160i, 180i, 210i 시리즈는 독립형 CNC의 신뢰성과 GE Fanuc 스마트 터미널의 성능을 결합합니다. 개방형 CNC는 개인용 컴퓨터 기능 및 추가 확장 가능성과 동시에 GE Fanuc CNC 제어 기능의 고효율 구현을 제공합니다. 높은 신뢰성으로 인해 모든 수준의 산업에서 안심하고 사용할 수 있습니다. CNC 장치와 기계는 개인용 컴퓨터의 그래픽 사용자 인터페이스를 사용하여 제어할 수 있습니다. 또한 네트워크 기능을 사용하여 정보를 교환하고 데이터베이스 소프트웨어를 사용하여 서비스 프로그램을 관리할 수 있습니다. 개인용 컴퓨터의 가장 진보된 기능을 사용하여 가장 단순한 기계를 지능적인 기능을 가진 기계로 바꾸는 것이 가능합니다. 응용 소프트웨어는 "i" 시리즈 개방형 CNC용 Microsoft Windows 95/98, Windows NT4.0 및 Windows 2000, "is" 시리즈 개방형 CNC용 Microsoft Windows CE에서 지원됩니다. 역학은 기존 컴퓨터와 마찬가지로 기계용 응용 프로그램 소프트웨어를 개발할 수 있습니다. GE Fanuc 소프트웨어(CNC 라이브러리)는 내부 CNC 정보를 입력/출력하는 데 사용됩니다. 이러한 소프트웨어는 OLE/DDE를 통한 교환뿐만 아니라 Microsoft 프로그래밍 언어(Visual Basic 또는 Visual C++TM)의 표준 세트를 지원할 수 있습니다. 모든 응용 소프트웨어를 쉽게 설치할 수 있습니다.
이미 언급된 회사 외에도 러시아 시장에는 Heidenhain, Bosch Rexroth, IPA, Indramat, Andron GmbH, M&R Numeric(전체 독일), 이탈리아 Fidia, OSPI, Olivetti, 일본 Mitsubishi, Toshiba, Hitachi와 같은 외국 회사의 제품이 있습니다. , 미국 Allen- Bredley 및 기타.
협력의 이점에 대해
구소련 공화국에서 제조된 CNC 시스템 중 MSHAK CJSC(아르메니아)와 우크라이나 회사 West Labe의 제품을 주목할 수 있습니다.
PC 기반 클래스의 개방형 아키텍처를 가진 MSHAK-DELTA TAU CNC 시스템은 표준 또는 산업용 개인용 컴퓨터를 기반으로 구축되었습니다. Delta Tau Data System, Inc.의 강력한 프로그래밍 가능한 다축 컨트롤러 PMAC가 컴퓨터에 설치되어 있습니다. (미국), 실시간으로 기계의 모든 하위 시스템을 관리합니다. 이것은 ISA(또는 PCI) 버스에 설치된 하나의 보드에 불과하며 축의 이동(최대 32개)을 제어하고 전기 자동화(PLC 최대 2048 I/O)를 제어하는 기능을 수행합니다. 이 시스템은 8대의 기계를 동시에 제어할 수 있으며 동기(보간) 축의 수는 32개입니다.
West Labe의 WL4T CNC 시스템은 WL4 제품군의 2세대 2축 윤곽 제어 시스템의 기본 모델이며 기본 자동 제어 기능이 있는 수직 선반 및 선반에 사용하도록 설계되었습니다. 동시에 제어되는 좌표의 수 2 + 1(페이스플레이트). 보간 방법 - 선형 및 원형.
국내 솔루션
Balt-System Company(St. Petersburg)는 최신 세대 NC-110 및 NC-200의 두 가지 CNC 시스템을 제공합니다.
NC-110 시스템은 다용성과 신뢰성의 조합이 특징입니다. 시스템은 모듈식 기반으로 구축되며 추가 모듈을 설치하여 증가하는 소비자 요구 사항을 충족할 수 있습니다. NC-200 시스템은 컨트롤 유닛, 오퍼레이터 콘솔, 머신 콘솔이 하나로 결합된 소형 모노블록 장치이다. 이러한 시스템은 사용자에게 다음과 같은 광범위한 기술 옵션을 제공합니다. 매개변수 프로그래밍, 벡터 지오메트리 요소 프로그래밍, 두 개의 가상 축 프로그래밍, 치수 크기 조정, 부품의 영점 이동 및 가공 평면 회전, 회전 중 커터 팁 반경의 벡터 보정, 전동 공구 제어, 선삭 및 훨씬 더 많은 동안 밀링 및 보링 사이클 활성화 가능성.
CJSC "Mikros"(JSC TsNITI의 자회사)에서 제조한 CNC 장치 "Mikros" 시리즈 11, 12T, 12TV는 현대 컴퓨터 기술산업형이며 편리한 블록 배치를 가지고 있습니다. 산업용 컴퓨터와 빠른 제어 응답을 보장하는 하드 실시간 운영 체제를 기반으로 합니다. HDD 대용량프로세스 제어 프로그램에 거의 무제한 메모리를 제공합니다.
사용자는 수행된 기능과 작업, 기계 및 CNC 시스템의 상태를 완전히 제어할 수 있습니다.
내장 편집기를 통해 제어 프로그램을 입력하고 수정할 수 있습니다. 프로그래밍은 G 코드와 3자리 코드를 사용하여 수행됩니다.
사용 가능한 그래픽 지원 모드를 사용하면 도구의 실제 이동을 시각화하고 처리 시작 전에도 도구 경로의 프로그래밍된 요소를 확인할 수 있습니다.
또한 Mikros 시리즈의 CNC 시스템에는 기계 역학 오류를 보정하기 위한 고급 기능이 있습니다. ; 뿐만 아니라 커터의 절삭날 반경의 불일치를 보정하는 기능.
자율 시스템 자체 튜닝을 통해 각 축에 대한 최적의 위치 제어 매개변수를 결정할 수 있습니다.
Modmash-Soft(Nizhny Novgorod)의 범용 시스템 FMS-3000은 다음 위치에 설치하도록 설계된 고성능 수치 제어 시스템입니다. 다른 유형 기술 장비: 밀링 머신, 복사기, 머시닝 센터, 선반 및 기타 CNC 장비.
특정 유형의 기계에 대한 적응은 전자자동 프로그램과 FMS-3000 매개변수의 광범위한 시스템의 도움으로 수행됩니다.
FMS-3000의 기본은 다음과 같이 제조된 산업용 등급의 개인용 컴퓨터입니다. 최신 기술. 강력한 소프트웨어와 결합된 FMS-3000의 개방형 아키텍처는 컴퓨터 장비의 주요 제조업체의 컴퓨터 구성 요소를 구조에 쉽게 통합할 수 있도록 합니다.
시스템 소프트웨어는 RT-Kernel 라이브러리를 사용하는 하드 실시간 커널을 기반으로 구현되어 서보 드라이브 및 전기 자동화 사이클을 제어하기 위한 고품질 타이머 작업을 보장합니다. 개방형 구조시스템을 사용하면 시스템에 포함할 수 있습니다. 소프트웨어 모듈사용자.
Izhevsk NPP IZHPREST는 1992년부터 CNC Mayak-400(1992) 및 Mayak-500(1999)을 개발하여 양산하고 있습니다. 회사의 최신 개발은 CNC 시스템 Mayak-600입니다. Mayak-600 수치 제어 시스템은 새 기계를 완성하고 오래된 기계를 업그레이드하도록 설계되었습니다.
시스템 레이아웃 개념은 직렬 인터페이스로 연결된 별도의 CNC 장치와 별도의 운영자 콘솔입니다. CNC 장치는 기계의 전기 캐비닛에 내장되어 있으며 작업자 콘솔은 기계 콘솔 또는 전기 캐비닛에 설치됩니다. Mayak-600을 사용하면 8개의 좌표축과 스핀들을 제어할 수 있습니다. 피드 드라이브와 스핀들은 아날로그 신호(+/-10 V)로 제어됩니다. 광전 및 유도 피드백 센서를 측정 회로에 연결할 수 있습니다. 스테퍼 모터를 제어하기 위한 CNC 버전이 있습니다.
시스템의 일부 기능: 초기 조건(시작점 및 G-기능)의 자동 결정을 통해 모든 프레임에서 프로그램을 실행하는 기능, 작동 중일 때 및 작동 중 블록 진단, 머신 데이터 액세스를 위한 다단계 시스템 , 조작자 콘솔에서 제어 프로그램, 매개변수, 수정기 편집 , 30MB 이상의 볼륨으로 제어 프로그램을 작업하는 기능, 나선형 보간, 모든 축을 따라 동시에 선형 보간.
변위 변환기의 유형 - 유도 및 광전(원형 및 선형). CNC에는 통합 프로그래머블 컨트롤러가 포함되어 있습니다.
WinPCNC 시스템. WinPCNC 시스템(NCSYSTEMS.RU, 모스크바)은 운영 체제가 있는 개인용 컴퓨터의 강력한 플랫폼에 구축된 단일 컴퓨터 CNC 시스템입니다. 윈도우 시스템 NT 및 VentureCom의 RTX 4.1 실시간 확장. PCNC 클래스에 속합니다. 시스템은 단일 프로세서를 사용하여 전기 기능을 포함한 모든 기능을 처리합니다. 하드웨어 부분은 표준 개인용 컴퓨터 장비와 피드 및 메인 이동 서보 드라이브, 전기 자동화 드라이브, 운영자 패널과의 통신을 위한 추가 인터페이스 모듈로 대표됩니다. CNC 시스템은 시스템 블록과 조작 패널의 두 개의 독립적인 블록으로 구성됩니다. 시스템 장치산업용 컴퓨터 케이스에 들어 있습니다. 조작반 블록은 하우징에 내장되어 소비자에게 편리한 구조로 설계되었습니다. 시스템 장치는 PCI 버스의 기본 보드 세트입니다. 추가 보드를 설치할 수도 있습니다. 예를 들어 제어 좌표의 수를 늘리고 전기 자동화의 총 병렬 입력/출력 수를 늘리고 드라이브 및 전기 자동화를 제어하기 위해 Fieldbus 유형의 네트워크 인터페이스 보드를 설치합니다. .
운영자 인터페이스는 Windows 환경에서 개발된 모든 최종 사용자 응용 프로그램을 포함하도록 열려 있습니다. 동시에 광범위한 API 인터페이스 기능 세트가 최종 사용자에게 제공됩니다. 운영자 인터페이스(그의 모습, 모드, 페이지 및 메뉴 세트)는 특수 기능을 사용하여 가능한 한 최단 시간에 크게 재설계할 수 있습니다. 도구 시스템 State_Machine_Builder. CNC 시스템은 ISO-7비트 코드(DIN 66025)의 모든 버전의 가공 프로그램 언어로 설정할 수 있습니다. 맞춤형 버전은 제어 프로그램 디버거와 유연한 제어 프로그램 해석기(ISO 프로세서)에 의해 지원됩니다. 인터프리터는 임의의 (합리적인) 버퍼링된 프레임으로 설정할 수 있습니다. 편집기-디버거에는 시스템 입력과 인터프리터 출력에서 제어 프로그램의 그래픽 시뮬레이션을 위한 시스템이 있습니다. 즉, 등거리를 고려합니다. 시스템 보간기에는 유연한 독점 아키텍처와 고정 IPD(보간기 데이터) 입력 인터페이스가 있습니다. 특별한 보간 알고리즘을 포함할 수 있습니다. 제어 프로세스에서 사용 가능한 알고리즘의 모든 조합을 사용할 수 있습니다. 유연한 전자 자동 시스템은 SoftPLC 개념, 즉 CNC 시스템의 응용 프로그램 구성 요소의 일부로 컨트롤러의 소프트웨어 구현을 기반으로 구축되었습니다. CNC 시스템의 모든 모듈의 상호 작용은 시스템의 글로벌 서버 역할을 하는 다기능 소프트웨어 버스를 통해 수행됩니다. 이러한 조직은 시스템의 확장을 허용합니다.
CNC 시스템 4CKFF(CJSC 4C)는 Olivetti와 함께 상트페테르부르크에서 개발 및 생산에 투입된 4CK 시리즈의 대표 제품입니다. MC/TC 장치는 공작 기계, 머시닝 센터, 플렉시블 모듈을 제어하고 GP 장치는 특수 유형의 공작 기계, 로봇 및 자동 라인을 제어합니다. 5개(MSGGS) 및 무제한(GP) 기술 프로세스를 실시간으로 제어하면 CNC에서 여러 제어 프로그램을 동시에 실행할 수 있습니다. 예를 들어 하나의 장치에서 여러 기계의 부품 처리를 동시에 제어할 수 있습니다. 시각. 4CKFF는 이전 4CKFF보다 10배 빨라져 소프트웨어의 강력한 기능을 최대한 활용할 수 있습니다.
기능적으로 다른 총 8개의 하드웨어 모듈은 생산의 기술적 복잡성을 줄이고 서비스 유지 관리를 단순화하며 최신 및 이전에 생산된 4SK의 소프트웨어 및 하드웨어 호환성을 보장합니다. 2000년에는 품질과 신뢰성을 결정짓는 4CKFF에서 외국산 요소 베이스 사용으로 거의 완전한 전환이 이루어졌습니다. 관련 생산을 포함한 CNC 4CKFF 생산: 프린트 배선판, 금속 구조, 키보드 - 상트페테르부르크에 집중되어 있습니다.
5개 플랫폼용 소형 제어 장치(294x356x262mm)를 기반으로 하는 고도의 전자 통합 기능을 갖춘 새로운 CNC 시스템 "Mini 4CKFF"는 이전 4CK 모델과 호환되는 모듈식 및 소프트웨어로 6개의 좌표축(+2개의 스핀들)을 제어할 수 있습니다. ) 112/64개의 개별 입력/출력이 있습니다.
CNC 시스템 Arta NVP "Arta-Test"(모스크바의 Fryazino)는 최대 5개의 제어 좌표로 전기 부식 기계를 제어하도록 설계되었으며 최근 생산된 CNC "Arta" DAKSh3.035.002의 추가 개발품입니다.
독립형 CNC와 BERM-2M 생성기가 내장된 CNC가 모두 생산됩니다. 이 시스템은 Pentium 프로세서가 장착된 최신 Intel 아키텍처 컴퓨터를 기반으로 합니다. 자체 시리즈 생산 유닛으로 완성됩니다: 드라이브 스테퍼 모터, ADC, 작동 소프트웨어의 ROM이 내장된 전자 디스크 및 전원이 꺼졌을 때 매개변수 및 처리 좌표를 저장하기 위한 정적 메모리, 전원 공급 장치.
CNC와의 작업자 인터페이스는 15인치 컬러 그래픽 모니터, 작업자 콘솔의 개폐식 키보드 및 제어 패널에 의해 제공됩니다(BERM-2M 생성기가 내장된 CNC 버전의 경우 보완됩니다. 기술적 충동의 매개 변수를 조절하고 표시하는 요소 포함).
CNC는 새 장비와 이전에 제조된 EDM 및 레이저 장비의 현대화 모두에 대해 "플러그인 플러그" 원칙에 따라 제조됩니다.
LLC "Rus Avtomatika"(St. Petersburg)는 UNIC 제품군의 범용 다기능 CNC 시스템을 제공합니다. 운영 체제 Windows-98 이상을 사용하여 소비자의 특정 요구 사항에 최대한 적응할 수 있습니다. CNC 시스템 UNIC-23 - 좋은 결정머시닝 센터, 다기능 밀링 및 터닝 장비용. UNIC-22F,T CNC 시스템은 단순한 밀링 및 터닝 머신을 제어하도록 설계되었으며 금속 및 목공 및 절단 장비에 사용됩니다. UNIC-21 CNC 시스템은 복잡한 기술 장비를 제어할 수 있는 모듈식 시스템으로, 기술 프로세스여러 센서에 의해 모니터링됩니다. 경공업 및 식품 산업에서 가장 효과적으로 사용됩니다.
CNC 시스템 KRT4-00 NPO KRISTA(Rybinsk)는 산업 디자인의 컴퓨터를 기반으로 구축되었습니다. 시스템에는 다음이 포함됩니다. 그래픽 디스플레이, 영숫자 및 기능 키보드, 프로세서 유닛, 기술 장비가 있는 통신 보드, 전원 공급 장치. CNC는 기존 장비를 업그레이드하고 새로 개발된 시스템에서 사용할 수 있습니다. 제어되는 좌표의 수는 최대 6개이고 피드 드라이브의 제어는 드라이브 유형에 따라 결정되며 위치 센서 유형은 증분 광전입니다.
시스템은 다음 유형의 보간을 지원합니다. 선형 - 6개의 모든 좌표를 동시에, 원형 - 동시에 2개의 선형 좌표를 따라, 선형-원형 - 3개의 좌표를 동시에 따라, 반경 값 및 공구 길이에 의한 자동 윤곽 보정.
CNC의 영숫자 키보드에서 입력하여 제어 프로그램의 입력이 가능합니다. 텍스트 에디터), 제어 시스템의 내부 비휘발성 메모리에서 이전에 입력된 프로그램을 로드하거나 외부 데이터 캐리어(3.5인치 플로피 디스크, 휴대용 비휘발성 메모리 모듈, 컴퓨터 네트워크, 트위스트 페어 10Mbps).
일부 명세서개별 CNC 시스템이 표에 나와 있습니다.
그래도 지멘스는
보시다시피 CNC 시스템에 대한 러시아 시장은 매우 대표적이며 제안으로 가득합니다. 더욱이, 거의 모든 제조업체는 하나 또는 두 개에서 십여 개 또는 그 이상의 모델과 수정 사항을 제공합니다.
많은 제안이 있지만 무엇을 구입하고 어떤 CNC 시스템을 선호합니까? 다양한 소스정보는 대략 이러한 숫자에 수렴됩니다. 러시아에서 판매되는 외국 CNC 시스템의 점유율은 각각 60-70%이고 국내 제품의 점유율은 30-40%입니다. 정보 출처는 또한 확실한 영업 리더가 Siemens라는 데 동의합니다(해외 CNC 시스템 매출의 최대 90%).
이 자료의 저자도 유혹을 피하지 않고 러시아 시장에서 제공되는 새로운 금속 가공 장비에 어떤 CNC 시스템이 장착되어 있는지 평가하려고 했습니다. 50개의 제조업체가 인수되었으며 그 중 34개는 외국(미국, 독일, 스위스, 일본)이고 16개 러시아(예: St. Petersburg의 Sverdlov, Sterlitamak 및 Ivanov의 공작 기계 공장, 모스크바의 Krasny Proletarian 및 기타)입니다. 따라서 다음 50개 회사 중 28개 회사는 Siemens CNC 시스템이 장착된 장비를 제공하고 15개 - GE Fanuc, 8 - Heidenhain, 9 - 기타 외국 기업(자체 개발 포함) 및 4 - 국내 회사 (많은 제조업체가 공작 기계를 장비하기 때문에 합계는 50과 동일하지 않습니다. 다른 시스템).
또한 공작 기계 현대화를 제안하는 10개 회사(러시아 및 외국 모두) 중 거의 모든 회사가 이 장비에 설치된 CNC 시스템의 대안으로 Siemens 제품을 제공합니다.
따라서 현재 러시아 시장은 Siemens 제품이 지배하고 있다고 말할 수 있습니다(아쉽지만 사실입니다). 이 회사는 방대한 경험과 거의 무한한 엔지니어링 및 기술 역량을 기반으로 하는 CNC 시스템 생산의 선두 주자입니다. 러시아 개념에 따르면 "약점"이 하나뿐입니다.
최근에 러시아 시장에서 CNC 시스템의 미국 및 중국 제조업체의 존재가 눈에 띄게되었습니다. 그러나 Siemens와 달리 유지 보수, 수리 및 컨설팅 서비스를 제공할 수 있는 광범위한 대표 사무소 네트워크가 없습니다.
이 부인할 수 없는 전략적 산업의 발전에 대한 국가의 관심 부족을 유감스럽게 언급하면서, 그러한 제품 생산을 전문으로 하는 새로운 기업의 출현, 그럼에도 불구하고 새로운 현대 모델의 출현으로 조심스러운 낙관으로 미래를 내다본다.
1세대 CNC 시스템은 개별 반도체 소자(트랜지스터)를 기반으로 하는 소자 기반을 가졌습니다. 이 시스템의 프로그램 입력은 단일 코드 또는 위상 형식의 자기 테이프에서 수행되었습니다. 1세대 CNC 장치의 모델은 PRS1-58, PRS-ZK, K-4MI입니다. 동시에 1 세대 K2P-67, KZP-68, UMS-2의 CNC 장치에서 프로그램은 이미 5 트랙 천공 테이프 (코드 BCC-5)에 입력되었습니다.
2세대 CNC 시스템
2세대 CNC 시스템은 소형(시리즈 155) 및 중형(시리즈 176) 통합 정도의 요소 기반을 가졌으며 이를 통해 제어 알고리즘의 회로 구현이 수행되었습니다. 2세대 CNC 장치 모델에는 H22, NZZ, H55, P-33, "크기 2"가 포함됩니다. 2세대 H22, N3Z의 CNC 장치에서 프로그램은 8트랙 천공 테이프(코드 ISO 7)에 입력되었습니다.
3세대 CNC 시스템
3세대 CNC 시스템은 마이크로컴퓨터("Electronics-60", "Electronics NTs-03" 등), BIS(시리즈 589 등)를 기반으로 만들어졌습니다. 이 CNC 시스템에는 고급 기술 기능이 있었고 제어 알고리즘의 소프트웨어 구현이 수행되었습니다. 3 세대 CNC 장치의 모델에는 15MP, "크기 4M", 2S42, 2S85, 2U32, 2MCHZ, "Electronics NTs-31"이 포함됩니다. 3 세대 CNC 장치에서 프로그램은 천공 테이프와 키보드를 사용하여 입력되었습니다. CNC 시스템에는 화면에 부품을 그래픽으로 표시하여 NC를 설정하기 위한 표시 대화 상자 시스템이 장착되기 시작했습니다. 일반적인 사이클을 사용하여 기계에서 직접 간단한 부품 프로그래밍을 수행할 수 있는 작동 가능한 CNC 시스템이 있습니다.
4세대 CNC 시스템
4세대 CNC 시스템의 경우 블록 다중 프로세서 실행이 일반적입니다. 요소 기반으로 특수 LSI 및 마이크로 컴퓨터가 사용됩니다. 기술 기능 및 대화 모드 프로그래밍은 고급 언어로 수행됩니다. 4세대 CNC 장치에는 Elektronika MS2101, ZS100, ZS200이 포함됩니다. 4세대 CNC 장치에서 프로그램은 전자 카세트 또는 디지털 자구의 카세트로 입력되었습니다.
5세대 CNC 시스템
5세대 CNC 시스템은 산업용 개인용 컴퓨터를 기반으로 만들어졌습니다. 이러한 CNC 시스템은 프로그래밍 언어를 포함하여 개인용 컴퓨터에 내재된 모든 현대적 성과를 구현합니다. 소프트웨어 및 수학 지원; 정보의 입력, 저장 및 교환 시스템; 구조적 변화 가능성; 자체 조정 및 적응 기능 등을 수행하는 능력
CNC 기계는 다음과 같은 기술 그룹으로 나뉩니다.
- 선반 그룹;
- 드릴링 밀링 보링 그룹 기계;
- 연삭 그룹 기계;
- 기어 그룹 기계;
- 전기 물리학 그룹의 기계;
- 다목적 기계, OT:
악기와 관련하여
- 수동 도구 변경으로;
- 포탑에서 자동 도구 변경으로;
- 매거진의 자동 공구 교환 기능이 있습니다.
기계에는 다양한 CNC 시스템이 장착될 수 있습니다. 제어 시스템의 구성에 따라 금속 절단기의 명칭은 다음과 같을 수 있습니다.
- F1 - 예비 좌표 세트가 있는 기계를 포함하여 디지털 표시가 있는 기계;
- F2 - 위치 직각 좌표 제어 시스템이 있는 기계;
- F3 - 윤곽선 직선 및 곡선 좌표 제어 시스템이 있는 기계;
- F4 - 기계 보편적인 시스템위치 윤곽 처리를 위한 좌표 제어.
CNC 기계를 특성화하기 위해 다음 지표가 사용됩니다.
- 기계 정확도 등급
- H - 일반 정밀 기계
- P - 증가
- B - 높음
- A - 특히 높음
- C - 초정밀(마스터 머신)
- 카트리지 기계의 경우 - 베드 위에 설치할 제품의 가장 큰 직경, 베드 위의 공작물의 가장 큰 직경;
- 센터 및 척 기계의 경우 - 캘리퍼 위의 공작물의 가장 큰 직경;
- 바 터닝 머신의 경우 - 처리된 바의 가장 큰 직경;
- 보링 및 밀링 머신의 경우 - 테이블 작업 표면의 전체 치수(길이, 너비), 원형 회전 테이블 작업 표면 직경;
- 드릴링 머신용 - 가장 큰 공칭 직경드릴링, 개폐식 스핀들의 직경 등;
CNC 공작 기계를 기반으로 부품의 자동화된 처리를 위해 설계된 다음과 같은 기계 모듈 및 기계 콤플렉스가 생성되었습니다(시스템의 일반적인 국제 명칭은 대괄호로 표시됨).
GPM(FMM) - 유연한 생산 모듈- 부품 자동 로딩/언로딩 시스템, 로컬 스토리지, 부품 및 도구 컨베이어를 갖춘 기술 장비 유닛
GAL - 유연한 자동 라인- 여러 GPM을 포함하는 시스템 일반 관리컴퓨터, 운송 시스템 및 공란 창고. 컴퓨터는 제어 프로그램을 CNC 공작 기계에 저장 및 전송하는 기능을 수행하며 현재 일정 및 운영 계획도 수행합니다.
GPS(FMS) - 유연한 제조 시스템- 자동 전환의 특성을 가진 기술 장비 및 컴퓨터 기반 제어 시스템의 복합체;
GAD(FMF) - 유연한 자동화 작업장- 공통 운송 시스템, 창고, 다단계(계층적) 컴퓨터 제어 시스템과 함께 여러 HAL 및 GPM을 포함하는 시스템
A3 - 자동 감기- 자동 조립 공장 및 완제품 포장을 포함한 GAD로 구성된 시스템. 중앙 컴퓨터는 공장의 모든 부서와 장기 계획을 제어합니다.
CNC 장치의 설계, 높은 수준의 제어 시스템은 지속적으로 개발 및 개선되고 있습니다. 새로운 요소 기반이 나타나고 기술 기능이 확장되며 자동화 수준, 생산성 및 처리 정확도가 향상됩니다. 따라서 매뉴얼은 제어 시스템 개발에 대한 전망과 CNC 기계 작업자의 직업에 대한 새로운 요구 사항에 대한 정보를 제공합니다.
CNC 시스템. 용어 및 개념
프로그램 제어가 가능한 금속 가공 장비터닝, 밀링, 드릴링, 연삭, 보링, 다목적, 전기 침식 등과 같은 절단에 의한 금속 가공을 위한 모든 유형의 공작 기계 뿐만 아니라 금속 가공을 위한 기타 유형의 장비(판 벤딩 머신, 펀치 프레스 등) 공작물의 자동 처리를 위해 주어진 프로그램.
제어 프로그램(CP)- 특정 공작물을 처리하기 위한 기계의 알고리즘에 해당하는 프로그래밍 언어의 명령 세트.
공작 기계의 수치 제어- 처리 데이터가 디지털 코드로 지정되는 UE에 따라 기계에서 공작물의 처리를 제어합니다.
프로그램 캐리어- UE가 기록된 기하학적 및 기술적 데이터의 캐리어. 데이터 매체로는 종이나 플라스틱 천공테이프, 자기테이프, 자기디스크, 저장장치 등이 사용된다. 다른 유형및 유형.
기하학적 정보- 모양, 부품 및 도구 요소의 치수, 기계 테이블에서의 상대적 위치를 설명하는 정보.
기술 정보- 부품의 기술적 특성과 가공 조건을 설명하는 정보.
UE 프레임- 프로그램의 구성 요소로, 전체적으로 입력되고 작동되며 적어도 하나의 명령을 포함합니다.
프레임별 작업- UE의 각 프레임의 처리가 오퍼레이터의 영향 후에 발생하는 CNC 장치의 작동.
수동 데이터 입력을 통한 CNC 작업- 프레임 형식으로 제한되는 데이터 세트가 기계 제어판의 작업자에 의해 수동으로 수행되는 CNC 장치의 작동.
수동 제어로 CNC 작업- 조작자가 수치 데이터를 사용하지 않고 콘솔에서 기계를 제어하는 CNC 장치의 작동.
미러 처리- 작업 바디가 UE에 기록된 궤적의 미러 이미지인 궤적을 따라 움직이는 CNC 장치의 작동.
UE 진입- 가장 높은 순위의 컴퓨터 또는 작업자 콘솔에서 프로그램 캐리어에서 CNC 장치의 메모리로 데이터 입력.
그룹 CNC 기계- 기계의 요청에 의해 배포된 프로그램을 저장하기 위한 공통 메모리가 있는 컴퓨터에서 공작 기계 그룹의 수치 제어.
제로 파인 머신- 기계 좌표계의 원점으로 간주되는 기계 노드의 점.
동등 어구- 주어진 기준 또는 원점에 대한 공간상의 한 점의 위치를 결정하는 값.
기계 원산지- 기계 영점을 기준으로 정의되고 NC에서 작업을 시작하는 데 사용되는 기계 노드의 점.
기계 고정 소수점- 기계의 영점을 기준으로 정의되고 작업 본체의 위치를 결정하는 데 사용되는 점.
처리 시작점- 특정 공작물 처리 시작을 결정하는 지점.
부동 제로- CNC 장치를 사용하여 작업 몸체의 이동 원점을 영점을 기준으로 한 임의의 위치로 이동할 가능성.
변위 작업 해결- UE에서 설정할 수 있는 작업 본체의 최소 이동(선형 또는 회전 각도에 의한).
움직임 처리의 불연속- 제어 프로세스에서 제어되는 작업 본체의 최소 이동 또는 최소 회전 각도.
최대 프로그래밍 가능 여행- UE의 한 프레임에서 설정할 수 있는 작업체의 가장 큰 움직임.
등고선 속도- 지정된 가공 윤곽의 각 지점에서 접선 방향과 방향이 일치하는 작업 본체의 결과 이송 속도.
공구 위치 오프셋- 기계 작업 몸체의 프로그래밍 된 좌표의 제어판에서 변경하십시오.
이송 속도 무시- 작업자 콘솔에서 프로그래밍된 이송 속도 값 변경.
메인 모션 속도 보정- 메인 드라이브의 프로그래밍된 속도의 운전자 콘솔에서 변경.
CNC 고장- CNC 장치의 작동 가능성 위반으로 구성된 이벤트.
CNC 고장-CNC 장치의 작동 가능성에 대한 단기 자체 수정 위반으로 구성된 이벤트.
표시된 CNC 오류- 발생 시 콘솔에서 수정되어 기계 정지로 이어지는 오류, 즉 부품 처리가 종료되면 해당 정보가 운영자 콘솔에 표시됩니다.
표시되지 않은 CNC 오류- 발생 시 콘솔에서 감지되지 않은 오류.
CNC 기계 시스템- 서로 상호 작용하는 단위 및 어셈블리의 복합체.
CNC 장치의 일반적인 교체 요소(TEZ CNC)- 성능 손실의 경우 유사한 것으로 교체될 수 있는 CNC 장치의 일반적인 최소 구성 요소. 각 CNC 장치는 UE 및 제어 대상의 위치에 대한 정보에 따라 집행 기관에 대한 제어 조치를 발행합니다.
CNC 시스템의 분류
CNC 시스템의 국내 분류
국내 기계 공학에서 사용되는 CNC 시스템의 분류는 작업 동작의 유형에 따라 수행됩니다. 위치 및 윤곽 CNC 장치를 구별하십시오.
CNC 포지셔닝 장치- 작업체가 주어진 점으로 이동할 수 있는 장치로, 점에서 점으로의 이동 궤적은 직선 운동에 의해서만 설정됩니다. CNC 포지셔닝 장치는 하나의 공통 기능인 포지셔닝, 즉, 주어진 좌표의 한 지점에서 움직이는 작업체를 멈추는 정확성을 보장합니다. 포지셔닝 장치의 이동 속도는 프로그래밍되지 않으며 기계 드라이브의 역학에 의해서만 결정됩니다. CNC 포지셔닝 장치에는 드릴링, 지그 보링, 터닝, 밀링, 연삭 및 직사각형 사이클에서 작동하는 기타 기계가 장착되어 있습니다.
윤곽 직사각형(공선) CNC 장치- 하나의 좌표를 따라 움직임을 제공하는 장치. 대부분의 기계는 직교 좌표계를 사용하므로 이러한 장치를 직사각형이라고 합니다. 이러한 장치와 위치 장치에서는 이동의 최종 좌표가 프로그래밍되지만 UE에서는 작업 몸체의 이동 속도가 지정된 절단 모드에 따라 설정되고 이동이 교대로 수행됩니다 각 좌표축을 따라 직사각형 CNC 장치는 밀링, 터닝 및 연삭 그룹의 기계에 사용됩니다.
윤곽(연속) CNC 장치- 궤적을 따라 공간의 주어진 지점에서 작업 바디의 움직임을 보장하는 장치, 그 모양과 최종 좌표는 UE에서 지정됩니다. CNC 윤곽 장치에는 복잡한 모양의 부품 성형을 수행하는 밀링 및 터닝 그룹의 기계가 장착되어 있습니다.
적응형(자체 적응형) CNC 제어 장치- 특정 기준(절단 속도, 이송, 절삭력)에 따라 변화하는 가공 조건에 따라 가공 공정을 자동으로 조정하는 장치. 자체 적응형 CNC 장치에는 메인 무브먼트 모터 및 피드 드라이브의 과부하 보호를 허용하는 제어 및 조절 시스템이 있어 고품질 처리를 보장하고 기계 시스템을 고장으로부터 보호합니다. 적응형 CNC 장치는 밀링, 보링 및 다목적 기계를 갖추고 있습니다.
운영 제어 시스템(OCS)- CNC 장치와 작업자의 대화 모드에서 공작 기계에서 NC 준비가 있는 마이크로 컴퓨터 기반 CNC 장치. 작업자는 CNC 제어판의 키보드를 사용하여 부품 도면의 데이터를 제어 프로그램에 입력합니다. CNC 작동 장치에는 터닝 및 밀링 머신이 장착되어 있습니다.
CNC 장치를 분류할 수 있는 또 다른 특징은 기계-CNC 시스템에서 순환하는 정보 흐름의 수입니다.
개방 루프 시스템- 정보 스트림이 하나뿐인 CNC 장치. 이러한 시스템에는 작업체의 움직임을 제어하는 측정 장치(피드백 센서)가 없습니다. 이러한 시스템으로 작업체의 움직임을 재현하는 정확도는 낮고 피드 드라이브 엔진에 의한 처리 명령의 정확도와 작업체에 움직임을 전달하는 운동학적 체인의 정확도에 의해 결정됩니다.
폐쇄 루프 시스템- 두 가지 정보 스트림이 있는 CNC 장치: 하나는 프로그램 캐리어의 입력 장치를 통해 제어 장치에 입력되고 다른 하나는 작업 본체의 실제 위치를 결정하는 피드백 센서에서 CNC 장치로 입력됩니다. 이러한 흐름 사이에 불일치가 있으면 제어 장치가 피드 드라이브에서 작동하고 후자는 작업 본체를 올바른 방향으로 이동하여 불일치를 0에 가까운 값으로 변경합니다.
CNC 시스템의 국제 분류
에 따라 국제 분류기술 능력 수준에 따라 모든 CNC는 다음과 같은 클래스로 나뉩니다. 상수(NC 클래스) 및 가변(CNC 클래스) 구조의 CNC 장치가 있습니다.
CNC 클래스 NC(수치 제어)작업 알고리즘을 구성하는 모든 작업이 특정 기능을 구현하는 별도의 회로 또는 장치(집합 블록 구성)를 사용하여 병렬로 수행되는 컴퓨팅 장치의 원리를 기반으로 합니다. 이러한 장치는 견고한 구조의 CNC 장치라고도 합니다. 이러한 장치(H22 및 N3Z)의 기본 모델에는 마이크로 전자 장치가 포함되어 있으며 이를 사용할 때 처리 프로세스에 대한 작업자 개입이 매우 제한적입니다.
NC급 CNC 시스템은 각 공작물의 처리 주기 동안 천공 테이프의 프레임 단위 판독을 수행합니다.
NC 클래스 시스템이 가장 일반적입니다. 그들은 다음 모드에서 작동합니다. 기계를 켠 후 CNC는 프로그램의 첫 번째 및 두 번째 블록을 읽습니다. 읽기가 끝나면 기계는 첫 번째 프레임의 명령을 실행하기 시작합니다. 이 때 프로그램의 두 번째 블록의 정보는 CNC 시스템의 메모리에 있습니다. 첫 번째 프레임을 실행한 후 기계는 메모리 장치에서 출력되는 두 번째 프레임에서 작업을 시작합니다. 기계가 두 번째 프레임을 작업하는 과정에서 시스템은 프로그램의 세 번째 프레임을 읽고 두 번째 프레임의 정보에서 해방된 저장 장치에 입력됩니다.
고려된 작동 모드의 주요 단점은 배치에서 각 다음 공작물을 처리하기 위해 CNC 시스템이 천공된 테이프의 모든 프레임을 다시 읽어야 한다는 것입니다. 동시에 펀칭된 테이프를 읽는 과정에서 불충분한 안정적인 작동 CNC 리더기. 결과적으로 배치의 개별 부품에 결함이 있을 수 있습니다. NC 등급 시스템의 고장 확률 증가는 천공 테이프 프레임의 수가 매우 많기 때문에 설명됩니다. 이러한 시스템의 작동을 위해서는 기계의 각 기본 동작이 프로그램에 기록되어야 하기 때문입니다. 또한 이 작동 모드에서는 천공된 테이프가 빨리 마모되고 더러워져 판독 실패 가능성이 더욱 높아집니다. 마지막으로 블록에 기계가 매우 빠르게 수행하는 작업이 포함된 경우 CNC는 이 시간 동안 다음 블록을 읽을 시간이 없어 실패로 이어집니다.
CNC급 장치(Computer Numerical Control(가변 구조)는 컴퓨팅 장치(프로세서), 메모리 블록 및 정보 입출력 블록을 포함하는 제어 컴퓨터의 구조에 해당합니다. 동시에 기능의 범위, 수행되는 작업의 특성 및 순서는 메모리 블록에 입력되는 작업 프로그램에 의해 결정됩니다.
CNC 클래스 시스템은 마이크로프로세서를 기반으로 하는 미니컴퓨터의 존재로 인해 큰 잠재력을 가지고 있습니다. 프로그램은 준비된 천공 테이프에서 완전히 시스템의 저장 장치에 입력될 수 있을 뿐만 아니라 CNC 제어판에서 수동으로 개별 프레임으로 입력할 수 있습니다. 프로그램 블록에서는 작업 본체의 개별 이동에 대한 명령과 제어 시스템의 메모리에 저장되는 고정 사이클이라고 하는 전체 이동 그룹을 정의하는 명령을 모두 기록할 수 있습니다. 이로 인해 프로그램 프레임 수가 급격히 감소하고 그에 따라 기계의 신뢰성이 높아집니다. CNC 클래스 시스템을 사용하면 정보를 수동으로 입력하여 프로그램을 디버깅하고 디스플레이에 표시할 때 대화 모드에서 편집을 매우 쉽게 수행할 수 있을 뿐만 아니라 천공 테이프에 수정 및 작업된 프로그램을 수신할 수 있습니다.
CNC 클래스(또는 이에 가까운)의 여러 시스템은 가능한 직업"매트릭스 펀치" 모드, 미러 이미지 모드 등에서 서로 다른 스케일의 하나의 프로그램. 시스템은 작동 중에 다양한 유형의 수정을 도입할 수 있습니다.
비교적 저렴한 비용으로 작은 전체 치수그리고 높은 신뢰성, 마이크로프로세서의 CNC 시스템은 이전에 구현할 수 없었던 새로운 속성을 제어 시스템에 도입하는 것을 가능하게 합니다. 예를 들어, CNC 장치 "Electronics NTs-31"에는 기계의 일정한 오류를 고려하고 자동으로 수정하여 처리 정확도를 결정하는 일련의 요인에 영향을 줄 수 있는 소프트웨어가 있습니다. 시스템의 이러한 기능의 가장 간단한 형태는 좌표를 따라 이동하는 방향으로 드라이브의 백래시 또는 사각 지대를 보정하는 것입니다. 마이크로프로세서에 CNC 장치가 있는 공작 기계의 신뢰성과 성능은 모니터링 및 진단 시스템의 사용을 증가시킵니다. 이러한 시스템의 기능은 CNC 외부 장치의 상태 모니터링, 내부 장치 확인 및 CNC 자체 모니터링으로 나눌 수 있습니다. 예를 들어, 선반용 동일한 장치 "Electronics NTs-31"에는 시스템의 모든 구조적 부분의 성능을 확인하기 위한 특수 테스트 프로그램이 있습니다. 이 테스트 프로그램은 장치가 켜질 때마다 실행되며 모든 부품의 상태가 양호하면 시스템이 작동할 준비가 되었다는 신호가 생성됩니다. 기계와 CNC가 작동하는 동안 테스트 프로그램은 주 제어 프로그램의 개발을 방해하지 않고 소위 백그라운드 모드에서 부품으로 처리됩니다. 오작동이 발생하면 표시등 보드에 코드가 나타나며 표에 따라 오작동의 위치와 원인이 결정됩니다. 또한 시스템은 열 조건을 초과하는 장치의 부적절한 작동과 관련된 오류를 감지하고 전원 공급 장치 및 기타 매개 변수에 대한 전압을 제공합니다.
CNC 클래스의 장치는 프로그램 제어의 기능을 확장합니다. 이전에는 구현할 수 없었던 기능이 있습니다: NC의 저장 및 작업장에서의 편집, 디스플레이의 표시 확장, 작업자와의 대화 통신, 수정 가능성의 넓은 범위 , 기계 오류 포함, 고장 진단 시스템, 변경 가능 프로그래밍 방식으로작동 중 제어 시스템의 기능, 전기 자동화 기능의 구현 등
또한 다른 클래스의 CNC 시스템이 있습니다.
SNC(저장된 수치 제어)- 동일한 블랭크의 배치를 처리하기 전에 전체 펀칭된 테이프를 단일 판독하는 CNC 시스템;
SNC 클래스의 CNC는 NC 클래스 시스템의 단점이 없으며, 프레임 단위로 순차적으로 전체 프로그램을 읽고 정보를 대용량 메모리 장치(16KB 이상)에 저장합니다. 천공된 테이프는 동일한 부품의 전체 배치를 처리하기 전에 한 번만 읽혀지기 때문에 거의 마모되지 않습니다. 모든 블랭크의 처리는 저장 장치의 신호에 의해 제어되므로 고장 가능성과 부품 불량이 크게 줄어듭니다. SNC 시스템을 사용하면 천공 테이프 길이가 40~310m인 제어 프로그램을 한 번 입력할 수 있습니다.
DNC(직접 수치 제어)- 직접 시스템 수치 제어한 컴퓨터의 기계 그룹;
DNC 클래스 시스템의 생성 및 적용은 현대 복합 자동화 생산 개발의 일반적인 추세와 관련이 있습니다. 이러한 산업에서 CNC 기계, 운송 및 보관, 적재 시설로 구성된 섹션의 작동은 중앙 컴퓨터에서 제어됩니다. 그러나 중앙 컴퓨터가 있다고 해서 공작 기계용 CNC 장치의 필요성이 완전히 제거되는 것은 아닙니다. DNC 시스템 구축을 위한 가장 일반적인 옵션 중 하나에서 해당 지역의 각 장비 유형은 NC, SNC, CNC 클래스의 CNC 시스템을 유지합니다. 이러한 섹션의 정상적인 작동 모드는 모든 유형의 장비의 CNC에 대한 제어 명령이 판독 장치를 우회하여 컴퓨터에서 직접 전선을 통해 전송됩니다. 이것은 장비의 각 부분과 전체 현장의 신뢰성을 증가시킵니다. 동시에 컴퓨터의 도움으로 UE를 준비하는 프로세스가 자동화됩니다. 동시에 컴퓨터의 일시적인 고장 상황에서도 각 유형의 장비가 비상 사태에 대비하여 미리 준비된 펀칭 테이프에서 작동 할 수 있기 때문에 이러한 섹션은 계속 작동합니다.
HNC(수치 제어 처리)- 제어판에 수동 프로그램 세트가 있는 작동 가능한 CNC 시스템.
제어 프로그램의 준비 및 디버깅은 길고 힘든 과정입니다. 단순한 구성의 부품 제조에서는 이 과정을 제외하는 것이 좋습니다. 원칙적으로 현대 기계에서 이러한 가능성은 가능합니다. 수동 데이터 입력 모드를 사용하여 구현됩니다. 그러나 이 모드에 있는 대부분의 기계의 경우 기계에서 후속 처리와 함께 리모콘에서 프로그램의 한 블록만 입력할 수 있습니다. 너무 비생산적입니다. 따라서 CNC 콘솔에서 수동으로 프로그램을 입력하는 HNC 클래스의 수치 제어의 소위 운영 시스템이 최근에 개발되었습니다. 충분히 많은 프레임의 프로그램은 CNC 제어판의 키 또는 스위치를 사용하여 쉽게 입력하고 수정할 수 있습니다. 디버깅 후 동일한 공작물의 배치 처리가 끝날 때까지 프로그램이 고정됩니다. HNC 클래스 시스템은 공작 기계의 위치 및 윤곽 제어를 모두 제공합니다.
서지
- GOST R 50369-92. 전기 드라이브. 용어 및 정의. - M.: 표준 출판사, 1993. - 16 p.
- Zavgorodnev P. I. 프로그램 제어 기능이 있는 공작 기계 작업자 작업: 교과서. 기술에 대한 수당. 학교 / P. I. Zavgorodnev. - M.: 더 높다. 학교, 1981. - 136 p.
- 공작 기계 및 산업용 로봇의 소프트웨어 제어: 교과서 / [V.L. Kosovsky, Yu.G. Kozyrev, A.N. Kovshov et al.]. - M.: 더 높다. 학교, 1989. - 272 p.
- Sergievsky L. V. CNC 공작 기계 조정기 매뉴얼 / L. V. Sergievsky, V. V. Ruslanov. - M.: Masinostroenie, 1991. - 176 p.
- Solomentsev Yu. N. 유연한 생산 시스템 관리 / Yu. N. Solomentsev, VL Sosonkin. - M.: Masinostroenie, 1988. - 552 p.
- Sosonkin VL 공작 기계의 수치 제어 마이크로 프로세서 시스템 / V.L. 소손킨. - M. : 마시노스트로에니, 1985. - 288 p.
- Cherpakov B. I. 금속 절단기: 시작을 위한 교과서. 교수 교육 / B. I. Cherpakov, T. A. Alperovich. - M.: 출판 센터 "아카데미", 2004. - 368 p.
- 공작 기계의 수치 제어 / [V.L. Sosonkin, O. P. Mikhaylev, Yu. A. Pavlov et al.]; 에드. V. L. 소손키나. - M.: Masinostroenie, 1981. - 398 p.
- 추다코프 A.L. 공작 기계 및 기계 단지용 제어 시스템 설계: Ch. 1.8 // 엔지니어링: 백과사전. T. FV-7. 금속 절단 기계 및 목공 장비. - 남: 마시노스트로에니, 19
보신존 M.A. 현대 시스템 CNC와 그 작동: 시작을 위한 교과서. 교수 교육 / M. A. Bosinzon; 에드. B.I. 체르파코바. - 2nd ed., 삭제됨. - M.: 출판 센터 "아카데미", 2008. - 192 p. ISBN 978-5-7695-5184-0
수치 제어의 기본 원리
전자 및 컴퓨터 기술의 발전, 생산에 컴퓨터의 도입으로 인해 금속 절단 기계용 수치 제어 시스템(CNC) 및 기타 기술 장비의 공작 기계 제작이 개발되고 널리 사용되었습니다.
금속 절단기의 수치 제어는 영숫자 코드로 지정된 프로그램에 따라 제어라고 하며 위에 쓰여진 일련의 명령을 나타냅니다. 특정 언어및 기계의 작업 기관의 지정된 기능을 제공합니다.
CNC 시스템과 이전에 고려된 ACS의 근본적인 차이점은 기계의 작업 기관을 제어하기 위해 제어 프로그램과 전송을 계산 및 설정하는 방법에 있습니다. 세부 도면 정보는 아날로그-디지털 형식, 즉 숫자, 다양한 구두 지침, 기호 및 제한된 수의 의미를 가진 기타 기호의 형태로 표시되며 각각에는 매우 구체적이고 모호하지 않은 정보가 있습니다.
기존 ACS에서 제어 프로그램은 캠, 복사기, 정지 장치, 지그 플레이트 및 프로그램 캐리어인 기타 수단과 같은 물리적 아날로그로 구현됩니다. 이 방법작업 제어 프로그램에는 두 가지 주요 단점이 있습니다.
첫 번째디지털(이산) 및 모호하지 않은 부품의 도면 정보가 아날로그(캠 곡선, 복사기 형태)로 바뀌기 때문에 발생합니다. 이로 인해 캠, 복사기 제조, 눈금자의 이동 정지 배열 및 작동 중 이러한 프로그램 캐리어의 마모에 오류가 발생합니다. 초단점은 이러한 소프트웨어 캐리어를 제조하고 기계에 대한 노동 집약적인 조정이 필요하다는 것입니다. 그것은 높은 비용대부분의 경우 직렬 및 특히 소규모 생산의 자동화를 위해 기존 ACS를 사용하는 것이 비효율적입니다.
CNC 기계에 대한 제어 프로그램을 기계의 작업 본체로 전송할 때까지 준비할 때 부품 도면에서 직접 얻은 개별 형식의 정보를 처리합니다.
CNC 기계에서 가공된 공작물에 대한 절삭 공구의 이동 궤적은 일련의 연속 위치로 표시되며 각 위치는 숫자로 결정됩니다. CNC 기계에서는 운동학적 관계의 도움이 아니라 수치 형식으로 지정된 프로그램에 따라 이러한 작업 바디의 독립적인 좌표 움직임을 제어함으로써 작업 바디의 복잡한 움직임을 얻을 수 있습니다. CNC 기계의 질적으로 새로운 것은 동시에 제어되는 좌표의 수를 늘릴 수 있다는 가능성으로, 자동 제어로 광범위한 기술 역량을 확보하여 근본적으로 새로운 공작 기계 레이아웃을 생성할 수 있게 되었습니다.
제어 프로그램은 주어진 정확도와 기계 작업체의 필요한 운동 법칙으로 계산할 수 있습니다. 컴퓨터에서 직접 공작 기계를 제어하는 일이 점점 더 널리 보급되고 있습니다.
CNC 시스템의 분류
CNC 시스템은 다양한 기준에 따라 분류할 수 있습니다.
나. 처리 제어의 기술적 과제를 기반으로모든 CNC 시스템은 위치, 윤곽 및 결합의 세 그룹으로 나뉩니다.
위치 CNC 시스템제어 프로그램에 의해 지정된 위치를 결정하는 명령에 따라 기계의 작업 몸체의 움직임을 제어합니다. 이 경우 서로 다른 좌표축을 따라 이동이 동시에 수행될 수 있습니다(주어진 일정한 속도) 또는 순차적으로. 이 시스템은 주로 플레이트, 플랜지, 커버 등과 같은 부품을 가공하기 위한 드릴링 및 보링 머신을 갖추고 있으며 드릴링, 카운터싱킹, 보링 홀, 스레딩 등.
CNC 윤곽 시스템궤적을 따라 그리고 제어 프로그램에 의해 지정된 윤곽 속도로 기계의 작업 몸체의 움직임을 제어합니다. 윤곽 속도는 지정된 가공 윤곽의 각 지점에서 접선 방향과 일치하는 기계 작업 본체의 결과 이송 속도입니다. Contour CNC 시스템은 위치 제어 시스템과 달리 여러 좌표를 따라 하나씩 또는 동시에 연속적으로 도구 또는 공작물 이동을 제어하므로 매우 복잡한 부품을 처리할 수 있습니다(두 개 이상의 좌표에 대한 동시 제어). CNC 컨투어링 시스템에는 주로 터닝 및 밀링 머신이 장착되어 있습니다.
결합된 CNC 시스템, 위치 및 윤곽 CNC 시스템의 기능을 결합한 는 가장 복잡하지만 더 다양합니다. CNC 기계 (특히 다중 작업 기계)의 복잡성, 기술 능력의 확장 및 자동화 정도의 증가와 관련하여 결합 된 CNC 시스템의 사용이 크게 확대되고 있습니다.
Ⅱ. 피드백 기반모든 CNC 시스템은 개방형과 폐쇄형의 두 그룹으로 나뉩니다.
닫은 CNC 시스템은 다음과 같을 수 있습니다.
1) 기계의 작업 기관의 위치에 대한 피드백과 함께; 2) 작업 기관의 위치에 대한 피드백과 기계 오류에 대한 보상 3) 자기 적응(적응).
열려있는 CNC 시스템은 파워 또는 스텝 모터(SM)를 기반으로 구축됩니다. 후자의 경우 스테퍼 모터는 일반적으로 유압 부스터와 함께 사용됩니다.
III. 전자기술 수준에 따른 분류.
CNC 시스템의 사용 기간이 비교적 짧음에도 불구하고 전자 기술의 발전 수준에 따라 이미 여러 단계의 개발 단계를 거쳤습니다.
현재 업계에서 사용되는 CNC 시스템 클래스 NC디지털 모델을 기반으로 구축되었습니다. 이 시스템에서 프로그램(펀칭 테이프)은 보간기 3에 입력되고 추가 수정됩니다.
프로그램은 제어 시스템 2 기계 1에 입력됩니다. 이러한 CNC 시스템을 강성 프로그램이 있는 시스템이라고 합니다. 이러한 시스템에서는 프로그램 처리 과정에서 작업자가 개입할 가능성이 매우 제한적입니다.
시스템에서 클래스 SNC제어 프로그램을 읽기 위한 장치는 한 번만 사용됩니다.
저장 장치 4(메모리). 결과적으로 포토리더의 고장으로 인해 기계의 신뢰성이 높아집니다.
제어 시스템의 특징 CNC 클래스제어 컴퓨터의 구조에 해당하는 구조입니다. CNC 클래스 시스템의 출현으로 프로그램 제어 기능이 확장되었으며,
제어 프로그램의 저장 및 작업장에서 직접 편집, 고급 디스플레이 옵션, 운영자와의 대화 통신 등을 포함합니다. 제어 프로그램 입력은 펀치 테이프 또는 수동으로 수행할 수 있습니다. 두 번째 유형의 시스템을 시스템이라고 합니다. 클래스 HNC. 여기에서 제어 프로그램은 작업자가 키보드를 사용하여 입력하고 시스템 메모리에 저장됩니다.
게다가 자율 시스템업계의 CNC는 시스템이라고 하는 단일 컴퓨터에서 다양한 공작 기계 그룹에 대해 직접 수치 제어 시스템을 사용합니다. DNC 클래스.
이 시스템에서 중대형 컴퓨터(3)는 여러 CNC 기계에 대한 프로그램을 준비하고 개별 기계(1)의 CNC 시스템(2)으로 전송합니다. 컴퓨터의 매우 빠른 속도 때문에 시스템은 그룹의 모든 기계에 대한 프로그램을 준비합니다. 컴퓨터는 또한 반자동 장치 관리를 위한 추가 기능(예: 자동 운송 및 창고 제어)을 수행합니다. 공작 기계는 소량의 미니 컴퓨터에 의해 직접 제어됩니다. 랜덤 액세스 메모리개별 CNC 시스템에 포함됩니다.
CNC 시스템의 일반적인 블록 다이어그램
그림은 CNC 시스템의 일반적인 확대 블록 다이어그램을 보여줍니다. 여기에는 다음과 같은 주요 요소가 포함됩니다. CNC 장치; 각 제어 좌표에 설치된 기계 및 피드백 센서(DOS)의 작업 본체의 피드 드라이브. CNC 장치는 천공 테이프에 입력된 제어 프로그램에 따라 기계의 작업 본체에서 제어 작업을 실행하도록 설계되었습니다. 제어 프로그램은 메모리 블록에 저장되어 한 프레임 내에서 순차적으로 읽혀지며, 여기에서 기술 명령, 보간 및 이송 속도 블록으로 공급됩니다. 보간 블록은 제어 프로그램에 지정된 두 개 이상의 점 사이에서 도구 이동의 부분 궤적을 공식화하는 특수 컴퓨팅 장치(보간기)입니다. 이 블록의 출력 정보는 일반적으로 각 좌표에 대한 일련의 펄스로 표시되는 피드 드라이브 제어 장치에 입력되며, 주파수는 피드 속도를 결정하고 숫자는 이동량을 결정합니다.
정보 입력 및 읽기 블록제어 프로그램의 펀치 테이프에서 입력 및 읽기를 위한 것입니다. 포토컨버터를 구비한 포토리딩헤드(11)와 조명기를 포함하는 포토리더 앞에서 주기적으로 펀칭테이프를 잡아당겨서 한 프레임 내에서 라인별로 순차적으로 읽기가 이루어지며,
백열등 3과 렌즈 4로 구성됩니다. 8개의 광변환기는 정보 판독을 제공하고 2개는 전송 트랙의 구멍을 통해 동기 펄스를 형성하는 데 사용됩니다. 다른 장치에서는 파손을 제어하기 위해 천공 테이프의 가장자리를 따라 설치되는 다른 광 변환기가 사용됩니다.
펀칭 테이프 9를 당기는 것은 브로치 전자석(EMF)이 켜지고 전기자 6이 당겨질 때 롤러 10에 의해 눌려지는 구동 롤러 7에 의해 수행됩니다. 구동 롤러 7은 전기 모터 8에 의해 회전합니다. 펀칭 테이프를 당길 때 장력과 포토리딩 헤드(11)에 밀착된 테이프, 브레이크(1)에 의해 제동되고 클램프(5)에 의해 헤드(11)에 대해 눌려지며 천공된 테이프를 로드할 때 레버(2)에 의해 후퇴됩니다. 한 프레임에서 EMT 브레이크를 켜고 EMF 전자석을 끄면 천공된 테이프가 중지됩니다. 작업의 동기화는 제어 트리거(TG)에 의해 수행됩니다.
입력 장치에 수정 사항이 있습니다.
메모리 블록.펀칭된 테이프의 정보는 순차적으로 읽혀지고 한 프레임 내에서 한꺼번에 사용되기 때문에 읽을 때 메모리 블록에 저장된다. 여기에서도 펀칭된 테이프에서 오류가 감지되면 이를 모니터링하여 신호를 생성합니다. 정보 처리가 프레임 단위로 순차적으로 진행되고 한 프레임에서 정보를 읽는 데 걸리는 시간이 약 0.1~0.2초이므로 정보 전송에 갭이 발생하여 허용할 수 없습니다. 따라서 두 개의 메모리 블록이 사용됩니다. 첫 번째 메모리 블록에서 한 프레임의 정보를 처리하는 동안 두 번째 프레임은 펀칭된 테이프에서 읽어 두 번째 블록에 저장됩니다. 메모리 블록에서 보간 블록으로 정보를 도입하는 시간은 무시할 수 있습니다. 많은 CNC 시스템에서 메모리 블록은 입력 블록을 건너뛰고 컴퓨터에서 직접 정보를 읽을 수 있습니다.
보간 블록.이것은 제어 프로그램에 지정된 두 개 이상의 지점 사이에 부분 도구 경로를 형성하는 특수 컴퓨팅 장치입니다. 이것은 CNC 윤곽 시스템에서 가장 중요한 블록입니다. 블록의 기본은 제어 프로그램에 의해 지정된 윤곽 섹션의 수치 매개변수에 따라 기능 f(x, y)를 복원하는 보간기입니다. X와 Y 좌표 값의 간격에서 보간기는 이 함수의 중간 점의 좌표 값을 계산합니다.
보간기의 출력에서 시간적으로 엄격하게 동기화된 제어 펄스가 생성되어 해당 좌표축을 따라 기계의 작업 본체를 이동합니다.
선형 및 선형 원형 보간기가 사용됩니다. 이에 따라 전자는 선형 보간을 수행하고 후자는 선형 및 원형을 수행합니다.
선형 보간기는 예를 들어 주어진 윤곽에서 값만큼 편차가 있는 직선의 두 기준점 사이의 직경을 가진 커터로 작업 몸체의 이동을 제공합니다.
이 경우 보간기의 초기 정보는 좌표 증가의 크기와 직선을 따라 이동하는 처리 시간, 즉 , 여기서 S는 설정된 공구 이송 속도입니다.
선형 원형 보간기의 작동은 평가 기능 F의 방법에 따라 수행될 수 있습니다. 방법은 다음 제어 펄스가 생성될 때 논리 회로가 이 펄스가 발행되어야 하는 좌표를 평가한다는 사실에 있습니다. 공작 기계의 작업 몸체의 전체 이동으로 인해 지정된 윤곽에 최대한 가깝게 만듭니다.
보간된 선(그림 a 참조)은 그것이 위치한 평면을 두 개의 영역으로 나눕니다. 즉, 평가 함수 F>0인 선 위와 F가 있는 선 아래입니다.<0. Все точки, лежащие теоретически заданной линии, имеют F=0.
보간 궤적은 좌표가 있는 시작점에서 좌표가 있는 끝점까지 좌표축을 따라 기본 변위의 특정 시퀀스입니다.
궤적의 중간점이 F>0 영역에 있으면 X축을 따라 다음 단계가 수행되고 중간점이 영역 F에 있으면<0, шаг делается по оси Y. Аналогично происходит работа интерполятора при круговой интерполяции (см. рис. б).
피드 드라이브 제어 장치.보간 블록에서 정보가 피드 드라이브 제어 장치로 공급되고, 이 정보는 피드 드라이브를 제어하는 데 적합한 형식으로 변환됩니다. 후자는 각 펄스를 수신할 때 기계의 작업 본체가 CNC 시스템의 불연속성을 특징짓는 특정 양만큼 움직이는 방식으로 수행됩니다. 각 임펄스가 도착할 때 제어 대상은 임펄스 가격이라고 하는 특정 양만큼 이동하며 일반적으로 0.01 - 0.02mm입니다. 기계에 사용되는 드라이브 유형(폐쇄 또는 개방, 위상 또는 진폭)에 따라 제어 장치가 크게 다릅니다. 위상 시프터 모드에서 작동하는 회전 변압기 형태의 피드백 센서를 사용하는 폐쇄 루프 위상 유형 드라이브에서 제어 장치는 위상 출력에서 신호의 위상을 비교하는 펄스 대 위상 AC 변환기 및 위상 판별기입니다. 피드백 센서의 위상과 변환기를 변환하고 차동 오차 신호를 구동 전력 증폭기로 출력합니다.
이송 속도 블록- 윤곽을 따라 주어진 이송 속도를 제공할 뿐만 아니라 주어진 법칙에 따라 처리 섹션의 시작과 끝에서 가속 및 감속 프로세스를 제공하며, 대부분 선형이며 때로는 지수적입니다. 작업 피드 (0.5 - 3000 mm / min) 외에도이 블록은 일반적으로 증가 된 속도 (5000 - 20000 mm / min)로 공회전을 제공합니다.
제어 및 표시 패널.작업자는 제어 및 디스플레이 패널을 통해 CNC 시스템과 통신합니다. 이 패널의 도움으로 CNC 시스템이 시작 및 중지되고 작동 모드가 자동에서 수동 등으로 전환되고 이송 속도 및 도구 크기 수정 및 도구의 초기 위치 변경 전체 또는 일부 좌표. 이 콘솔에는 조명 신호 및 디지털 표시가 있습니다.
프로그램 수정 블록프로그래밍된 가공 매개변수를 변경하는 데 사용됩니다: 이송 속도 및 공구 치수(길이 및 직경).
고정 사이클 블록고정 사이클 블록이 사용되는 부품의 반복 요소(예: 드릴링 및 보링 홀, 스레딩 등)를 처리할 때 프로그래밍 프로세스를 단순화하는 역할을 합니다. 예를 들어, 완성된 구멍에서 빠르게 후퇴하는 것과 같은 움직임은 천공된 테이프에 프로그래밍되지 않습니다. 이는 해당 싸이클(G81)에 통합됩니다.
기술 명령 블록절삭 공구 검색 및 분석, 스핀들 속도 전환, 기계의 움직이는 작업 본체 클램핑 및 클램핑 해제, 다양한 인터록을 포함하여 기계 작동 주기 제어(주기적 자동화)를 제공합니다.
전원 공급 장치기존의 3상 네트워크에서 모든 CNC 장치에 필요한 정전압 및 전류를 공급합니다. 이 블록의 특징은 산업용 전력 네트워크에서 항상 발생하는 간섭으로부터 CNC 전자 회로를 보호하는 전압 안정기 및 필터가 있다는 것입니다.
피드백 센서(DOS)
DOS는 기계 작업 본체의 선형 움직임을 움직임의 방향과 크기에 대한 정보가 포함된 전기 신호로 변환하도록 설계되었습니다.
다양한 DOS는 조건부로 각도 (원형)와 선형으로 나눌 수 있습니다. 원형 DOS는 일반적으로 랙 및 피니언 기어를 통해 리드 스크류의 회전 각도 또는 기계 작업 본체의 움직임을 변환합니다. 원형 DOS의 장점은 기계 작업 본체의 이동 길이로부터의 독립성, 기계 설치 용이성 및 조작 용이성입니다. 단점은 작업체의 변위를 간접적으로 측정하는 원리와 그에 따른 측정 오차를 포함합니다.
Linear DOS는 작업체의 움직임을 직접 측정하므로 원형 DOS에 비해 가장 큰 장점입니다. 선형 DOS의 단점은 전체 치수가 작업 본체의 이동량에 의존하고 기계 설치 및 작동이 어렵다는 것입니다.
작동 원리에 따라 DOS는 펄스, 위상, 코드, 위상 펄스 등일 수 있습니다. 가장 일반적으로 사용되는 센서는 리졸버뿐만 아니라 원형 및 선형일 수 있는 인덕토신 유형입니다.
선형 인덕토신은 눈금자 1과 슬라이더 2로 구성됩니다. 눈금자의 길이는 측정된 변위 값을 약간 초과하고 눈금자는 2mm 피치의 인쇄 권선이 하나 있으며 여기에서 유도 전압이 제거됩니다. 솔리드(짧은 스트로크)이거나 여러 개의 플레이트(250mm 길이)로 조립될 수 있습니다. 슬라이더는 작업 본체에 설치되어 눈금자를 기준으로 움직입니다. ¼ 피치만큼 이동된 두 개의 인쇄된 권선이 있습니다. 10kHz 주파수의 교류 전류가 각 권선에 공급되고 첫 번째 권선의 전압은 , 그리고 두 번째에
, 여기서 은 지정된 오프셋 각도입니다.
슬라이더 2를 움직이면 라인 1의 권선 출력에서 전압이 유도됩니다.
여기서 는 작업 본체의 실제 움직임을 반영하는 실제 변위 각도입니다.
작업 본체가 미리 결정된 위치에 있으면 라인 권선의 출력 전압은 0입니다. 이 동등성이 없으면 피드 드라이브는 추가 이동을 위한 신호를 수신합니다.
회전 변압기 유형(VT)의 DOS는 CNC 기계에 널리 사용됩니다.
회전자가 회전할 때 고정자 2와 회전자 1의 권선 사이의 상호 유도가 높은 정확도로 사인파형으로 변경되는 2상 AC 전기 기계입니다. 전압은 고정자의 권선(a)과 권선(b)에 적용됩니다. 여기서 는 주어진 변위량을 반영하는 변위 각도입니다. 회전자 권선 1에서 전압이 제거됩니다. VT의 권선 수는 다를 수 있지만 대부분 VT는 고정자와 회전자에 서로 수직인 두 권선과 함께 사용됩니다. 이러한 사인-코사인 VT를 리졸버라고 합니다.
위치 CNC 시스템에서 코드 피드백 센서는 작업 바디 변위의 절대값을 측정하는 데 사용됩니다. 이러한 센서는 예를 들어 2진법 10자리의 원형 광전 센서의 코드 디스크를 사용했습니다.
유리 디스크의 각 동심 링은 광검출기에 빛을 전달하거나 전달하지 않는 어둡고 투명한 영역으로 구성됩니다. 링은 특정 숫자에 해당합니다. 외부 - 첫 번째, 내부 - 열 번째. 디스크는 전체 회전이 작업 본체의 최대 값으로의 이동에 해당하도록 설치됩니다. 이 경우 작업체의 각 위치는 하나의 조합(코드)에 해당합니다.
그림은 고정된 회절 격자(1)를 가진 펄스 선형 센서의 다이어그램을 보여주며, 이에 대해 가동 보조 눈금(2)이 이동합니다. 메인 격자에 대해 각도만큼 회전하므로 일정량 이동하면 모아레가 발생합니다. 수직 방향으로 이동하는 프린지(3)가 형성되어 빔 광(4)과 주기적으로 중첩되며 격자를 통과하여 2개의 광전지로 전달됩니다. 보조 눈금 2를 1획 이동하면 광전지에서 하나의 펄스가 나옵니다.
프로그램 코딩의 일반 원칙
CNC 기계에서 모든 프로그램 요소: 주어진 작업 및 보조 이동의 방향, 크기 및 속도 등 특정 순서로 배열되고 일부 코드를 사용하여 특정 방식으로 작성된 숫자의 형태로 디지털 형식으로 제공됩니다. 코드는 숫자 또는 동작의 조건부 레코드로, PU 시스템에서 사용하기 편리한 형식으로 이 숫자의 이미지를 매우 간단한 방법으로 얻을 수 있습니다. 일반적으로 프로그램 제어 시스템에 사용되는 모든 코드는 이동 코드와 보조 명령 코드의 두 가지 주요 요소로 구성됩니다. 인코딩하는 방법에는 여러 가지가 있습니다.
단일 코드.이 코드의 본질은 모든 숫자가 하나의 기호 1로 표현된다는 사실에 있습니다. 임의의 숫자를 나타내려면 주어진 숫자에 단위가 포함된 만큼 이 기호를 연속해서 반복해야 합니다. 프로그램 캐리어(펀칭 테이프)로 사용할 때 기호 1은 구멍을 펀칭하여 표시하고 자기 테이프는 자기 스트로크로 표시합니다. 주요 단점은 낮은 기록 밀도입니다.
10진수 체계 0 - 9의 10자리 숫자를 사용하여 숫자를 씁니다. 10진수 시스템에서 숫자를 쓰려면 각 문자에는 고유한 트랙이 있어야 하고 각 숫자는 한 줄이어야 합니다. 10진수 코드로 숫자를 작성하는 것은 번거롭습니다.
이진수 시스템쓰기에 0과 1의 두 문자만 사용합니다. 이진 코드로 숫자를 쓰려면 하나는 신호의 존재에 해당하고 0에서는 신호가 없습니다. 메커니즘이 두 개의 안정적인 상태를 가장 확실하게 구별하기 때문에 이것은 편리합니다. 예를 들어, 천공된 테이프에: 펀치가 있고 펀치가 없습니다. ;
CNC 기계에 사용되는 코드의 사용을 보장하기 위해 프로그래밍 언어의 통합이 대규모로 수행되었습니다. 이를 위해 ISO 표준의 국제 조직은 CNC 기계의 프로그래밍 처리를 위한 단일 국제 코드를 채택했습니다. 우리나라에는 유사한 코드(GOST 13052 - 74)가 있습니다. 코드는 숫자, 라틴 알파벳의 대문자 알파벳 및 그래픽으로 구분되는 특정 문자 집합을 설정합니다. 각 캐릭터는 종이 8 트랙 테이프에 구멍을 뚫어 얻은 고유 한 표정을 가지고 있습니다. 너비 25.4mm. 왼쪽에서 첫 번째 트랙(8번째)은 패리티 및 홀수 패리티 검사 기능입니다. 천공된 테이프의 각 줄에서 천공된 구멍의 수는 짝수여야 합니다. 나머지 7개 트랙은 이진수 시스템의 해당 숫자를 나타냅니다.
기계 작업 몸체의 각 이동 방향에는 특정 좌표 값과 해당 주소 기호(예: X, Y, Z, W 등)가 할당됩니다. 금속 절단기의 좌표축 축에는 단일 방향이 있습니다. 기계 요소의 양의 이동 방향은 가공 도구(홀더)와 공작물이 서로 멀어지는 방향으로 간주됩니다.
오늘날 기계 가공에 종사하는 거의 모든 기업에는 수치 제어(CNC) 기능이 있는 공작 기계가 있습니다. CNC 기계는 기존 수동 기계와 동일한 기능을 모두 수행하지만 이러한 기계의 집행 기관의 움직임은 전자적으로 제어됩니다. CNC 기계의 주요 장점은 무엇이며 점점 더 많은 공장이 상대적으로 저렴한 범용 기계를 구입하는 것보다 자동 제어 기능이 있는 현대식 장비에 투자하는 것을 선호합니까?
CNC 기계 사용의 첫 번째 명백한 이점은 더 높은 수준의 생산 자동화입니다. 부품 제조 과정에서 기계 작업자의 개입 사례를 최소화합니다. CNC 기계는 매일, 매주 거의 자율적으로 작동하여 일관되게 고품질 제품을 생산할 수 있습니다. 동시에 기계 작업자의 주요 관심사는 부품 설치 및 제거, 도구 설정 등 주로 준비 및 최종 작업입니다. 결과적으로 한 작업자가 여러 기계를 동시에 사용할 수 있습니다.
두 번째 장점은 제조 유연성입니다. 즉, 다른 부품을 처리하려면 프로그램만 변경하면 됩니다. 그리고 이미 테스트되고 검증된 프로그램은 언제 어디서나 사용할 수 있습니다.
세 번째 장점은 처리의 높은 정확도와 반복성입니다. 동일한 프로그램을 사용하여 요구되는 품질로 거의 동일한 수천 개의 부품을 생산할 수 있습니다. 마지막으로 수치 제어를 통해 기존 장비에서 제조할 수 없는 부품을 처리할 수 있습니다. 금형 및 금형과 같이 복잡한 공간 형상을 가진 부품입니다.
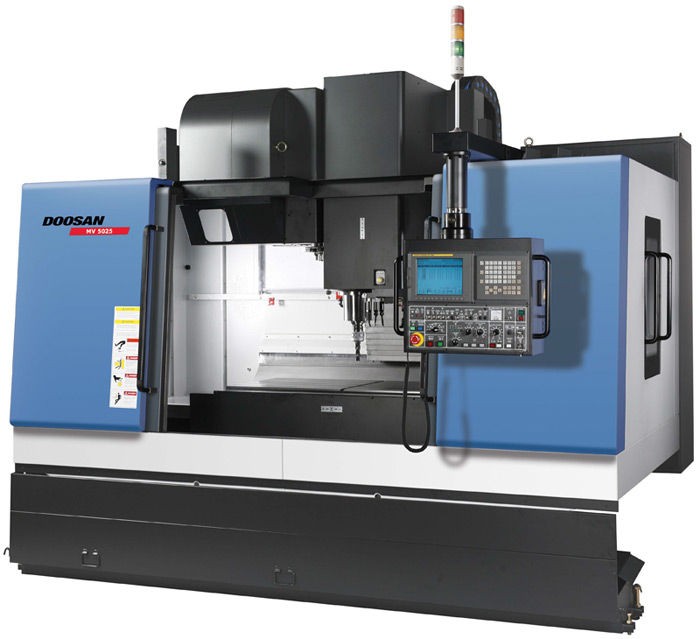
프로그램 자체에 따라 작업하는 방법을 사용하면 특정 부품 배치의 처리 시간을 보다 정확하게 예측할 수 있으므로 장비를 보다 완전히 로드할 수 있습니다.
CNC 기계는 상당히 고가이며 기존 기계보다 더 많은 설치 및 유지 관리가 필요합니다. 그럼에도 불구하고, 그들의 고성능은 적절한 사용과 적절한 생산량으로 모든 비용을 쉽게 충당할 수 있습니다.
CNC가 무엇인지 이해합시다. 수치 제어는 컴퓨터(기계 내부에 있음)와 처리 프로그램(제어 프로그램)을 사용하여 기계를 자동으로 제어하는 것입니다. CNC가 발명되기 전에는 기계가 수동 또는 기계적으로 제어되었습니다.
CNC 기계의 축 방향 이동은 제어 프로그램(NC)을 읽고 해당 모터에 명령을 내리는 컴퓨터에 의해 제어됩니다. 엔진은 기계의 집행 기관(데스크탑 또는 스핀들이 있는 기둥)을 움직입니다. 결과적으로 부품이 가공됩니다. 레일에 장착된 센서는 액추에이터의 실제 위치에 대한 정보를 컴퓨터로 다시 보냅니다. 이것을 피드백이라고 합니다. 컴퓨터는 공작 기계가 필요한 위치에 있다는 것을 알게 되는 즉시 다음 이동을 수행합니다. 이 과정은 제어 프로그램의 읽기가 끝날 때까지 계속됩니다.
설계 및 외관상 CNC 기계는 기존의 범용 기계와 유사합니다. 이 두 유형의 공작 기계 사이의 유일한 외부 차이점은 CNC 기계에 CNC 랙이라고도 하는 수치 제어 장치(CNC)가 있다는 것입니다.
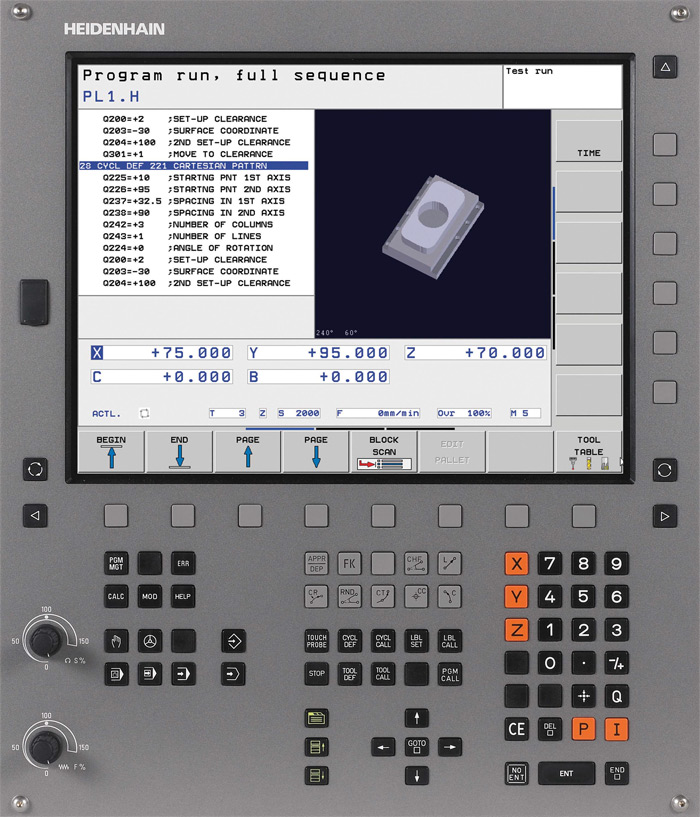
천등의 역사
직무 설명: 개념, 목적, 구조, 편집 및 공식화 절차 관리자를 위한 직무 설명의 목적 및 내용
면접 질문 어떤 직업을 가질 예정인가요?
상사가 맨날 비난하면 어떻게 하지 상사가 아무것도 하지 않는다면
이해 방법: 새끼 고양이가 푹신할 것입니까?