전체 텍스트 검색:
Home > 초록 >산업, 생산
요약
코스 프로젝트는 과제에 따라 완료되었으며 A1 형식의 4매(부품 도면, 공작물 도면, 설비 도면(기술 장비), 기술 조정)와 52매, 도면 4개, 테이블 6개로 구성된 설명이 포함되어 있습니다. 8개의 소스가 작업에 사용되었습니다.
코스 프로젝트의 주제: “개발 기술 과정"Step Shaft"부품 생산.
작업 과정에서 ESTD에 따라 설계된 경로 운영 기술 프로세스가 설계되었습니다.
소개 5
1 부품의 가공 공정 설계 6
1.1 부품의 서비스 목적 및 기술 요구 사항그녀에 6
1.2 도면의 기술적 제어 및 제조 가능성 분석
디자인 7
1.3 생산 유형 결정 9
1.4 원본 치수 선택 및 결정의 정당화
공백 14
1.5 부품 가공을 위한 경로 기술 설계 17
1.6 가공 여유 계산 19
1.7 운영 기술 설계 23
1.7.1 절단 조건 및 시간 계산 23
1.7.1.1 설계 작업 번호 010 "CNC 선삭" 23
1.7.1.2 설계 작업 번호 020 "밀링" 30
1.7.1.3 설계 작업 번호 025 "볼트 절단" 37
1.7.2 가공 정확도 계산 44
1.7.3 장비 선택 46
2 기술 장비 설계 48
2.1 Fixture 48에 부품을 설치하기 위한 선택 및 정당화
2.2 기술적 설명디자인과 작동 원리
비품 48
2.3 메커니즘의 고정 및 계산을 위한 계산 방식 개발
클램프 48
참고 문헌 51
부록 52
소개
샤프트는 서비스 목적, 구조적 형태, 크기 및 재료 면에서 매우 다릅니다. 그럼에도 불구하고 기술자는 샤프트 제조를 위한 기술적 프로세스를 개발할 때 유사한 많은 작업을 해결해야 하므로 분류를 기반으로 생성된 표준 프로세스를 사용하는 것이 좋습니다.
일반 기계 공학에는 무단 및 단차 축, 중실 및 중공, 평활 및 스플라인, 기어 축 및 위 그룹의 다양한 조합으로 조합된 축이 있습니다. 기하학적 축의 모양에 따라 샤프트는 직선, 크랭크 샤프트, 크랭크 및 편심(캠)이 될 수 있습니다.
공작 기계 제작을 포함한 기계 공학에서 가장 널리 사용되는 것은 다양한 중간 크기의 계단식 샤프트이며 그 중 부드러운 샤프트가 우세합니다. ENIMS에 따르면 기계 공학의 계단식 샤프트의 전체 표준 크기 수 중 85% 이상이 길이가 150-1000mm인 샤프트입니다.
샤프트 저널에는 키홈, 스플라인 또는 나사산이 있을 수 있습니다. 짝을 이루는 부품을 축 방향으로 움직이지 않도록 고정하기 위해 나사산을 스프링 링용 홈으로 교체하는 것이 종종 유리합니다. 이것은 취급 및 조립을 단순화합니다. 홈 또는 필렛은 단계의 전환 지점에서 만들어집니다. 필렛 처리는 더 복잡합니다. 따라서 가능한 경우 홈을 제공하는 것이 좋습니다. 샤프트 끝이 모따기됩니다. 스플라인 샤프트는 관통 및 폐쇄 스플라인이 있을 수 있으며 후자는 전체 크기 수의 약 65%를 차지합니다. 설계상 스플라인은 직선 및 나선형일 수 있습니다. 현재, 인벌류트 스플라인은 기술 측면에서 많은 이점이 있지만 직선형 샤프트(기계 공학에서 사용되는 전체 스플라인 샤프트 크기 수의 약 85-90%)가 우세합니다.
길이 대 직경의 비율이 15 미만인 샤프트는 강성으로 분류됩니다. 비율이 15보다 크면 샤프트는 비강성으로 간주됩니다.
1. 공정 설계 가공세부
1.1 도면 및 작동 조건에 따른 부품의 서비스 목적 및 기술 요구 사항
디테일 - 계단식 샤프트. 사용 된 재료는 강철 30X13 GOST 5632-72입니다. 성형 방법은 단조입니다. 최종 처리 후 샤프트는 조립을 위해 보내집니다.
샤프트에는 매개변수 Ra 1.25(38js6, 40js6, 45js6, 32.2n6, 32n6)에 따라 거칠기로 6등급 정확도에 따라 수행되는 5개의 저널이 있습니다. 기어는 키 연결을 통해 이러한 넥 중 2개에 장착됩니다. 샤프트의 극단적인 넥에는 M24 × 1.5-6g 나사산이 있어 너트로 축 방향 이동으로부터 기어를 고정합니다.
표면 40js6; 45js6 및 32.2n6 mm는 열처리의 결과로 얻은 37…43 HRC e.의 증가된 경도를 갖습니다. 나머지 표면이 열처리(25..30 HRC Oe)를 받지 않도록 하기 위해 유도 장치(HFC)에서 수행됩니다.
샤프트는 고합금 내식성 크롬강으로 만들어졌습니다. 이는 제품의 작업 환경 때문입니다.
1.2 부품 설계의 제조 가능성 분석
상세 도면에는 필요한 모든 치수가 포함되어 있으며 가공된 표면의 거칠기와 제조 정확도에 대한 정보가 제공됩니다.
부품 도면에는 부품의 완전한 그림을 제공하는 필수 보기가 포함되어 있습니다. 설계상 부품은 대부분의 표면이 열려 있고 처리를 위해 접근할 수 있습니다.
계수에 따라 표면을 정성적으로 평가합니다.
1) 정밀케이피엠
그리고 cf - 정확도의 평균 품질
A - 해당 정확도의 정도
N i - 주어진 정확도 품질의 표면 수
A 1 \u003d 6 n 1 \u003d 7
A 2 \u003d 7 n 2 \u003d 1
A 3 \u003d 8 n 3 \u003d 2
A 4 \u003d 12 n 4 \u003d 4
A 5 \u003d 14 n 5 \u003d 18
2) 거칠기 Kw
어디
B cf - 거칠기 매개변수의 평균 수치
;
여기서 B는 거칠기 매개변수의 숫자 값입니다.
ni w - 거칠기를 구성하는 표면의 수
B 1 \u003d 1.25 n 1 \u003d 6
B 2 \u003d 6.3 n 2 \u003d 26
3) 재료 사용
m g \u003d 5.6 kg - 부분 중량
m h - 공작물의 무게 \u003d 7.84 kg
m 폐기물 - 폐기물의 덩어리
따라서 모든 지표에 따르면 GOST 14205-83에 따라 부품을 제조할 수 있습니다.
1.3 생산 유형 결정
GOST 3.1108-74에 따른 생산 유형은 작업 통합 계수 Kz.o.로 특징 지어지며, 이는 특정 시간 내에 장치에서 수행하거나 수행할 모든 다양한 기술 작업의 비율을 숫자로 나타냅니다. 일자리.
Kz.o. \u003d Oi / Rya
여기서 ОI는 서로 다른 작업의 총 수입니다.
Rya - 다양한 작업을 수행하는 단위 작업자의 명확한 수.
GOST 14004-85는 다음 유형의 생산을 제공합니다.
하나의;
연속물;
대부분.
차례로 대량 생산은 대규모, 중형, 소규모로 나뉩니다.
계산은 가공의 주요 작업과 금속 가공 장비의 유형을 고려하여 수행됩니다.
초기 데이터:
연간 생산 프로그램: N=10000개
제품의 부품 수: m=1.
기업의 운영 모드: 하루 2교대.
대략적인 생산 유형 - 중간 배치.
고정 작업 계수를 계산하기 위해 부품 처리를 위한 예비 경로를 결정합니다. 여기서는 부품을 처리하는 일반적인 기술 프로세스를 기반으로 가공의 주요 성형 작업을 선택합니다.
밀링 및 센터링. 공작물의 끝과 센터링 밀링.
CNC 선반. 외부 표면의 황삭 및 정삭 선삭.
갈기. 밀링 키홈.
볼토레즈나야. 스레딩 M24 × 1.5-6g - 2개소.
원형 연삭. 외부 표면 연삭.
계산할 때 공식이 사용됩니다.
T sh-k \u003d WHO
1) 끝을 밀링합니다.
센터 엔드
2) 샤프트 저널 돌리기(황삭 및 미세 선삭)
3) 밀링 키홈:
핑거(키홈) 커터
여기서 i는 작업 이동 수입니다.
디스크 커터
4) 실 자르기:
5) 샌딩:
우리는 작업장의 표준 부하 계수를 결정합니다.
예상 머신 수:
어디
n n은 표준 장비 부하 계수입니다(연속 생산의 경우 n n \u003d 0.75 허용).
N – 생산 프로그램 N=10000 개.
F g - 4015 시간 - 장비 가동 시간의 실제 연간 자금
m 홍보 \u003d 1
m 홍보 \u003d 1
m 홍보 \u003d 1
m 홍보 \u003d 1
장비 부하 계수:
한 곳에서 수행되는 작업의 수:
장비 수 - 5
가동 고정 계수:
10생산 동시 출시를 위해 배치의 제품 수를 결정합니다.
N= 나/254
여기서 시작 빈도는 일 단위입니다(우리는 ㅏ = 6)
N=10000*6/254=237 개
전체 배치 처리를 위한 교대 수 결정:
나 - 작업 수
ΣT 쉿 =27.25분
c= =3,39
수락 c=4
정수 교대 근무 동안 장비를 로드하는 데 필요한 배치의 제품 수를 결정합니다.
=279.48개 n pr \u003d 280 개 수락
1.4 원래 공작물의 치수 선택 및 결정의 정당화
적은 수의 단계와 작은 직경 차이가 있는 샤프트는 열간 압연 또는 냉간 압연 막대에서 절단된 조각 블랭크로 만들어지며 더 복잡한 구성과 많은 수의 단계 또는 직경이 크게 다른 단계가 있습니다. 스탬핑, 교차 압연 또는 회전 압축으로 얻은 블랭크에서. 공작물의 선택은 기술 및 경제적 계산에 의해 정당화되어야 합니다.
대량 생산 및 대규모 생산에서 샤프트는 금속의 효율적인 사용(금속 활용 계수 CMM = 0.65 ... 0.7)을 보장하고 노동 집약도를 크게 줄이는 피스 블랭크로 만들어집니다. CIM이 5% 이상 증가하면 막대 스톡이 스탬핑으로 대체됩니다. 방사형 감소로 얻은 공작물은 구성 및 크기면에서 완성된 부품에 가장 가깝지만 CIM = 0.85 ... 0.95입니다.
블랭크는 닫힌 다이의 열간 단조 프레스에서 얻습니다.
GOST 7505-89 "Stamped steel forgings"에 따라 공작물의 치수를 계산합니다.
1.4.1. 초기 데이터.
장비 - 핫 스탬핑 프레스.
공작물 재료는 강철 30X13입니다.
부품 무게 - 5.6kg.
1.4.2. 단조의 기술적 특성 결정.
1) 단조품의 예상 질량 찾기 =
, 어디
- 부품의 질량,
- GOST 7505-89에 따라 결정된 설계 계수. \u003d 1.4(부품에 직선 축이 있기 때문에).
가져오기 = 킬로그램.
2) 정확도 등급 - T2.
3) 철강 그룹 - M3.
4) 단조의 복잡성 정도는 비율에 따라 결정 , 어디
- 단조품이 새겨진 그림의 질량. 우리는 =
, 단조의 복잡성 정도는 C1입니다.
5) 금형 분할면의 구성은 P(평면)입니다.
6) 초기 지수 - 10.
1.4.3. 허용량 및 단조 랩 결정.
1) 치수에 대한 기본 허용치, mm:
1.5 – 직경 40 mm, 표면 마감 Ra=1.25 µm
1.2 – 직경 42 mm, 표면 마감 Ra=6.3 µm
1.6 – 직경 46 mm, 표면 마감 Ra=1.25 µm
1.2 – 직경 53 mm, 표면 마감 Ra=6.3 µm
1.4 – 직경 39.5 mm, 표면 마감 Ra=6.3 µm
1.5 – 직경 32.2 mm, 표면 마감 Ra=1.25 µm
1.4 – 직경 24 mm, 표면 마감 Ra=6.3 µm
1.1 - 두께 5mm, 거칠기 Ra=6.3 µm
1.2 - 두께 62 mm, 거칠기 Ra=6.3 µm
1.2 - 두께 54 mm, 거칠기 Ra=6.3 µm
1.7 - 길이 597 mm, 거칠기 Ra=6.3 µm.
2) 다이 분할 표면을 따라 오프셋 - 0.3mm.
평탄도 및 진직도의 편차 - 0.5mm
스탬핑 슬로프 - 5
1.4.4. 단조 치수 및 공차.
1) 단조 치수, mm:
직경 24+(1.4+0.3+0.5)×2=28.4, 허용 28.5 mm
직경 Ç40+(1.5+0.3+0.5)×2=44.6, 허용 45 mm
직경 Ç42+(1.2+0.3+0.5)×2=46, 수용46 mm
직경 Ç46+(1.6+0.3+0.5)×2=50.8, 허용 51 mm
직경 Ç53+(1.2+0.3+0.5)×2=57, 허용 57 mm
직경 Ç39.5+(1.4+0.3+0.5)×2=43.9, 수용 44 mm
직경 Ç32.2+(1.5+0.3+0.5)×2=36.8, 수용 37 mm
두께 5+(1.1+0.3+0.5)×2=8.8, 9mm 수용
두께 62+1.2+0.3+0.5=64, 64mm 수용
두께 54 + 1.2 + 0.3 + 0.5 \u003d 56, 56mm 허용
길이 597+(1.7+0.3+0.5)×2=602, 602mm 수용
2) 외부 모서리의 라운딩 반경은 2.5mm입니다.
3) 치수의 허용 편차, mm:
직경 Ç28.5 직경 Ç57
직경 Ç45 직경 Ç44
직경 Ç46 직경 Ç37
직경 Ç51 두께 9
두께 56 두께 64
길이 602 .
공작물의 도면은 A2 형식의 시트에 표시됩니다.
PenzGU 1.3-09.151001.123.002-CHZ
1.5 부품 가공을 위한 라우팅 기술 설계
1 번 테이블.
№ 오페라 |
이름과 요약 |
기술 기반 |
장비 |
밀링 및 센터링 밀 끝 2면의 중심 |
미완성 목과 엉덩이 20 |
||
CNC 선반 먼저 왼쪽 샤프트를 날카롭게 미리 오른쪽의 샤프트를 날카롭게 왼쪽 샤프트를 완전히 날카롭게 오른쪽 샤프트를 완전히 날카롭게 |
축 및 끝 1 (축 및 끝 30) |
||
자물쇠 제조공 |
자물쇠 제조공 작업대 |
||
갈기 키홈(핑거) 커터로 키홈 밀링 디스크 커터로 키홈 밀링 |
목 표면 Ç40js6 및 엉덩이 30; 목 표면 Ç32,2n6 및 끝면 1; |
||
스레드 절단 실 M24 × 1.5-6g - 2 개소 |
목 표면 32.2n6; 38js6 |
||
자물쇠 제조공 디버 |
자물쇠 제조공 작업대 |
||
세탁 |
|||
제어 |
컨트롤 플레이트 |
||
열의 |
인덕션 설치 |
||
원통형 연삭 그라인드 샤프트 저널 Ç38 mm; Ç40mm; Ç45mm; Ç46mm; Ç32.2mm; Ç32mm |
축 및 끝 1 |
||
자물쇠 제조공 버, 무딘 날카로운 모서리 제거 |
자물쇠 제조공 작업대 |
||
세탁 |
|||
제어 |
컨트롤 플레이트 |
||
보존 |
자물쇠 제조공 작업대 |
경로 기술의 최종 버전은 GOST 3.1118-82에 따라 부록에 제공된 경로 맵에 작성됩니다.
1.6 계산 및 분석 방법에 의한 허용량 결정
한 표면의 경우 허용치는 계산 및 분석 방법에 의해 결정되고 나머지는 GOST 7505-89에 따라 결정됩니다.
우리는 크기 허용치를 계산 40 js6 (±0.008) mm
처리 계획:
황삭 선삭
미세 선삭
연마
선삭 및 연삭은 중심에서 수행되므로 표면 위치의 편차는 다음과 같습니다.
밀링 및 센터링 작업의 기준으로 사용되는 표면 공차는 GOST 7505-89에 따라 결정됩니다.
공간 편차의 잔차 값:
황삭 후
완료 후
수당의 최소값 계산은 다음 공식에 따라 수행됩니다.
최소 허용량:
사전 절단:
최종 선삭의 경우:
샌딩:
얻은 데이터는 표 2에 입력되어 있습니다.
표면 처리의 기술 전환 |
허용량 요소, 미크론 |
예상 수당 |
예상 크기 DP, mm |
제한 크기, mm |
허용치, 미크론의 한계 값 |
|||||
2 지맥스 |
||||||||||
공백 |
||||||||||
예비 전환 |
||||||||||
결승 진출 |
||||||||||
연마 |
" 예상 크기"(d p) 열이 전체 크기로 시작하여 보완됩니다.
최소 크기 제한은 허용 오차가 있는 소수점 이하 자릿수와 동일한 부호로 반올림하여 결정됩니다. 가장 작은 것에 허용오차를 더하여 가장 큰 한계 크기를 찾습니다.
수당 가치를 계산합니다.
일반 수당 그리고
우리는 중간 허용량을 합산하여 결정합니다.
212+336+2960=3508 µm
258+434+4400=5092 µm
수행 된 계산의 정확성을 확인합시다.
확인이 정확하므로 계산이 완료된 것입니다.
그림 1. 크기 40 js6 mm에 대한 허용 오차 및 공차 계획.
1.7 운용 기술 설계
1.7.1 절단 조건 및 시간 표준의 계산
1.7.1.1 작업 번호 010 "CNC 선삭" 설계
작업은 CNC 나사 절삭 선반 모드에서 수행됩니다. 4가지 설정(A 및 B - 황삭, C 및 D - 정삭)을 위한 16K20F3, 각 설정은 하나의 전환을 수행합니다. 이 작업에서는 플로팅 프론트 센터와 심압대에 설치된 회전 센터가 있는 2-죠 구동 척을 사용하여 공작물을 기계에 설치하고 베이스합니다.
절삭 공구로는 ISCAR에서 제조한 ISO 표준의 외경 가공용 선삭 공구가 사용됩니다.
거친 터닝:
홀더: PCLNR 2020K-12
플레이트: CNMG 120408T-NR
모서리 반경 r=0.8mm
인서트 등급 IC 9025
V=150..250m/min
S=0.15..0.5mm/회전
미세 선삭:
홀더: SVJCR 2020K-16
플레이트: VCMT 160404E-14
모서리 반경 r=0.4mm
인서트 등급 IC 9025
TiN, AL 2 O 3 , TiCN의 3개 층으로 화학 증착에 의해 코팅된 경질 합금.
V=250..400m/min
S=0.12..0.25mm/회전
이 작업에 대한 모든 계산은 공식에 따라 수행됩니다.
외부 종방향 및 횡방향 선삭의 절삭 속도는 다음 공식으로 계산됩니다.
절단 속도에 대한 Kv는 개별 계수의 곱입니다.
에게뮤직비디오
Knv - 공작물 표면 상태의 영향(압연 제품의 경우 = 0.8, 황삭 후 = 1.0) 표 5,
쿠브 – 절단부 재질의 영향(= 1.9) table.6
케이에프 – 커터 평면에서 주각의 영향(f95Å=0.7의 경우, f93Å=0.7의 경우) 표 18
황삭 선삭(설정 A 및 B):
절삭 깊이 t = 4mm
이송 S=0.5mm/rev
와 함께 V= 350 tab.17
중= 0,2
= 0,15
= 0,35
우리는 기계 800 rpm의 여권에 따라 가장 가까운 값을 선택합니다
절삭력 결정:
피 지 =10 씨 피 티 엑스 에스 와이 V N 케이 피
일반 보정 계수 크롬 케이 피 = 케이 MP 케이 피 케이 피 케이 피 케이 rp
케이 MP =0.75 탭.9
케이 제이 피=0.89 탭.23
케이 G 피 =1,1
케이 엘 피 =1,0
케이 rp
케이 피 = 0,75*0,89*1,1*1=0,734
와 함께 피= 204 표 22
N = 0
피 지 =10*204*4 1 *0,5 0,75 *135,7 0 *0.734=3561N
절삭력 계산
~까지= .
Lpx:
엘픽셀=엘컷+와이+ 엘추가의
어디 엘자르다 -
엘추가하다 -
와이 –
설정 A의 경우:
엘컷= 430mm
엘엑스트라+와이= 14mm
엘픽셀= 444mm
~까지= 1.11분
설정 B의 경우:
엘컷= 187mm
엘엑스트라+와이= 14mm
엘픽셀= 201mm
~까지= 0.503분
미세 선삭(설정 C 및 D):
절삭 깊이 t = 0.4mm
이송 S=0.25mm/rev
공구 수명 T = 60분
와 함께 V= 420 tab.17
중= 0,2
우리는 기계 2000 rpm의 여권에 따라 가장 가까운 값을 선택합니다
실제 절단 속도
절삭력 결정:
피 지 =10 씨 피 티 엑스 에스 와이 V N 케이 피
일반 보정 계수 크롬절삭력에 대한 개별 계수의 곱 케이 피 = 케이 MP 케이 피 케이 피 케이 피 케이 rp
케이 MP =0.75 탭.9
케이 제이 피=0.89 탭.23
케이 G 피 =1,1
케이 엘 피 =1,0
케이 rp– 고속강에만 고려됩니다.
케이 피 = 0,75*0,89*1,1*1=0,734
와 함께 피= 204 표 22
N = 0
피 지 =10*204*0,4 1 *0,25 0,75 *333,01 0 *0.734=211.76N
절삭력 계산
kW
kW
주요 기계 처리 시간을 결정합시다.
~까지=.
스트로크 길이 결정 Lpx:
엘픽셀=엘컷+와이+ 엘추가의
어디 엘자르다 -가공 길이와 동일한 절단 길이.
엘추가하다 -경우에 따라 부품의 설정 및 구성 기능으로 인해 추가 스트로크 길이가 발생합니다.
와이 – 접근 길이, 플런지 및 공구 오버런
설치 B의 경우:
엘컷= 432mm
엘엑스트라+와이= 6mm
엘픽셀= 438mm
~까지= 0.876분
G를 설치하려면:
엘컷= 196mm
엘엑스트라+와이= 6mm
엘픽셀= 202mm
~까지= 0.404분
작업에 대한 조각 계산 시간 결정.
대량 생산 및 대량 생산 조건에서 시간의 기술적 규범은 계산 및 분석 방법에 의해 설정됩니다. 연속 생산에서 조각 계산 시간의 표준이 결정됩니다.
Tsh-k= + 쉿,
어디 Tpz -준비 - 작업의 마지막 시간입니다.
N – 부품의 출시 배치 크기; N= 280개
CNC 선반에서 가공할 때 조각 시간 비율은 다음과 같이 정의됩니다.
티 PC =티 영형 +T V +T 서비스 +T 레인
티오 -주요 기술 시간
톳슬 -유지 보수 및 서비스 시간.
트퍼- 휴식 시간 .
TV -보조 시간:
티 V =티 수염 +T m.v + 티 조 + 티 ~에서
Tm.w. -공구 교환은 물론 유휴 인출 및 공급을 포함하여 처리 영역에서 기계의 포탑을 이동하는 데 필요한 기계 지원 시간.
쪼 -부품을 조이고 푸는 시간,
투스 -,
티즈 -부품을 측정하는 시간,
티 m.v. =티 더블 엑스 +T sk +T 시
Txx- 총 유휴 시간
츠크 -제어 프로그램의 프레임을 변경하는 총 시간(평균적으로 한 프레임을 변경하는 데 걸리는 시간은 1.5-2초)입니다.
시 -도구를 변경하는 데 필요한 총 시간입니다.
티 PC =티 영형 +T 수염 + 티 ~에서 + 티 조 +T 더블 엑스 +T sk +T 시 +T 서비스 +T 레인
공회전의 총 길이 -1862 mm
빠른 이동 속도 - 2000mm/min
Txx=1862/2000= 0.931분
시= 0.17분
츠크=1.5분
Tm.w.\u003d 0.931 + 1.5 + 0.17 \u003d 2.601분
2.893+0.4+2.601=5.894분
Tobsl+ Tper= 작동 시간의 12%
Tobsl+ Tper=5,894*0,12=0,707
얻은 시간 규범 값은 표 3에 요약되어 있습니다.
표 3
세트 A |
세트 B |
세트 B |
G 설정 |
||
티 수염 , 분 |
|||||
티 조 , 분 |
|||||
티 ~에서 , 분 |
|||||
티 서비스 +T 레인 , 분 |
|||||
티 피즈 , 분 |
|||||
티 영형 , 분 |
테이블을 기반으로 다음을 얻습니다.
티 PC =2,893+0,74+ 2,64 + 0,176 +2.601+2.828=11.878분
Tsh-k= +11.878=11.942분.
1.7.1.2 설계 작업 번호 020 "밀링"
작업은 두 가지 설정으로 키 밀링 머신 6D91에서 수행됩니다. 이 작업을 위해서는 부품이 설치되고 외부 원통형 표면과 끝을 따라 기계를 기반으로 하는 특수 장치를 사용해야 합니다(장치의 조립 도면은 형식 A1 PenzGU 1.3- 09.151001.123.005-SB).
특수 절단기는 절단 도구로 사용됩니다.
설정용 A - 키 커터 12 mm, 커터 재질 - 고속강 R6M5
B 설정용 - 곰팡이 커터 48 mm 및 b = 8 H8 mm, 커터 재료 - 고속 강철 R6M5
이 작업에 대한 모든 계산은 공식에 따라 수행됩니다.
세트 A:
부품은 40.2(도면40js6)를 기준으로 Fixture에 설치됩니다.
이 전환에서 치수가 있는 평행 키에 대해 홈이 밀링됩니다. V=12,
티=
4.5H12. 가공은 2.2mm 깊이로 이송하여 2회 통과하는 "진자" 방법으로 수행됩니다.
밀링 깊이 t=2.2mm
밀링 폭 H=12mm
커터 직경 D=12mm
커터 날당 이송 시즈= 0.18mm/치아
커터 톱니 수 z=2
스트로크 길이 결정 Lpx:
엘픽셀=엘컷+와이+ 엘추가의
어디 엘자르다 -가공 길이와 동일한 절단 길이. 엘컷= 54mm
엘추가하다 -경우에 따라 부품의 설정 및 구성 기능으로 인해 추가 스트로크 길이가 발생합니다.
와이 – 접근 길이, 플런지 및 공구 오버런
엘엑스트라+와이=6 mm
엘픽셀 = 54+6=60mm
절단 속도 결정 V N,
분 ,
절삭 속도에 대한 총 보정 계수 Kv는 개별 계수의 곱입니다.
에게뮤직비디오- 가공된 재료의 품질에 대한 영향(강의 경우 = 0.9) 표 3,
Knv
쿠브 –
티 -공구 수명; 티= 80분 탭40;
와 함께 V= 12 표 39
중 = 0,26
큐= 0,3
유= 0
피= 0
스핀들 속도:
N= 250분
절단 속도 지정:
분 피드 정의 에스중, mm/분:
에스m=시즈* 지* N= 0.18*2*250=90mm/분
절삭력 결정:
피 지 =10
보정 계수 케이 MP절삭력용
케이 MP =0.3 탭.9
와 함께 피= 82 표 41
유 = 1
큐= 0,86
피 지 =10
시간
절삭력 계산
kW
kW
주요 기계 처리 시간을 결정합시다.
~까지=
분
설정 B:
부품은 고정구에 설치되며 Ç32.4(도면 Ç32.2n6)를 기반으로 합니다.
이 전환에서 키의 홈은 치수로 밀링됩니다. V=8 +0,022 , 티= 4 H12. 가공은 곰팡이 커터 Ç48 mm 및 b = 8 H8 mm로 수행되며 커터의 재질은 고속강 R6M5입니다.
밀링 깊이 t=4mm
밀링 폭 H=8mm
커터 직경 D=48mm
커터 날당 이송 시즈= 0.01mm/톱니
커터 톱니 수 z=12
스트로크 길이 결정 Lpx:
엘픽셀=엘컷+와이+ 엘추가의
어디 엘자르다 -가공 길이와 동일한 절단 길이. 엘컷= 54mm
엘추가하다 -경우에 따라 부품의 설정 및 구성 기능으로 인해 추가 스트로크 길이가 발생합니다.
와이 – 접근 길이, 플런지 및 공구 오버런
엘엑스트라+와이=6 mm
엘픽셀 = 54+6=60mm
절단 속도 결정 V, m/min, 스핀들 속도 N, 분,
절삭 속도에 대한 총 보정 계수 Kv는 개별 계수의 곱입니다.
에게뮤직비디오- 가공된 재료의 품질에 대한 영향(강의 경우 = 0.9) 표 3,
Knv - 공작물 표면 상태의 영향(가공 후 = 1.0) 표 5,
쿠브 – 절단부 재질의 영향(= 1.0) table.6
티 -공구 수명; 티= 60분 탭40;
와 함께 V= 72 표 39
중 = 0,15
큐= 0,2
유= 0,1
피= 0,1
스핀들 속도:
기계의 여권에 따라 회전 수를 받아들입니다. N= 1000분
절단 속도 지정:
분 피드 정의 에스중, mm/분:
에스m=시즈* 지* N= 0.01*12*1000=120mm/분
절삭력 결정:
피 지 =10
보정 계수 케이 MP절삭력용
케이 MP =0.3 탭.9
와 함께 피= 68.2 탭.41
유 = 1
큐= 0,86
승= 0
피 지 =10
시간
절삭력 계산
kW
kW
주요 기계 처리 시간을 결정합시다.
~까지=
분
Tsh-k = + Tsht,
어디 Tpz -
N – N= 280개
Tsht=To+Tv케이+Tob.from,
어디 저것 -메인 타임,
TV -보조 시간:
TV=터스+쯔+툽+티즈,
어디 투스 -설치 및 제거 시간 ,
쪼 -
멍청한 -
티즈 -부품을 측정하는 시간,
Tob.from -
케이 케이=1,85).
토브닷=티 op ·9 %
티 op =티 영형 +T V · 케이
티 op =2.833+(0.094+0.068+0.12+0.62)1.85=4.502분
Tob.from \u003d 4.502 0.09 \u003d 0.405분
얻은 시간 규범 값은 표 4에 요약되어 있습니다.
표 4
이름 |
전환 1 |
전환 2 |
|
투스 - |
|||
쪼 - |
|||
멍청한 - |
|||
티즈 - |
|||
Tob.from – |
|||
Tpz - |
|||
저것– 주요 시간, 분 |
|||
Tsh-k=
+4,502+0,405
= 5.004분.
1.7.1.3 작업 번호 025 "나사 절단" 설계
작업은 두 가지 설정에서 나사 절단 반자동 장치 5D07에 의해 수행됩니다. 이 작업을 위해서는 부품이 설치되고 외부 원통형 표면을 따라 기계를 기반으로 하는 자체 센터링 턱이 있는 바이스인 장치를 사용해야 합니다. 밀링 작업에 사용되는 장치와 유사한 특수 장치를 사용할 수 있습니다.
절단 도구로 자체 개방 나사 절단 헤드가 사용됩니다. GOST 21760에 따른 4KA-70 - 76에 따른 둥근 빗이 있습니다.
질화티타늄(TiN)의 내마모성 코팅이 된 R6M5 고속강으로 만든 GOST 21761-76
이 작업에 대한 모든 계산은 공식에 따라 수행됩니다.
1) 세트 A:
부품은 Fixture에 설치되며 Neck Ç38js6의 표면을 기준으로 합니다.
이 전환에서 나사산 M24 × 1.5-6g가 수행됩니다.
이송(나사 피치와 동일) 에스= 1.5mm/회전
나사 직경 D=24mm
절삭 깊이 t=1.3mm
Lpx:
엘픽셀=엘컷+와이+ 엘추가의
어디 엘자르다 -가공 길이와 동일한 절단 길이. 엘컷= 31mm
엘추가하다 -경우에 따라 부품의 설정 및 구성 기능으로 인해 추가 스트로크 길이가 발생합니다.
와이 – 접근 길이, 플런지 및 공구 오버런
엘엑스트라+와이=3 mm
엘픽셀 = 31+3=34mm
절단 속도 결정 V, m/min, 스핀들 속도 N, 분,
에게뮤직비디오
케이 티 V
쿠브 –
티 -공구 수명; 티= 120분 탭49;
와 함께 V= 7.4 탭.49
중 = 0,5
큐= 1,2
스핀들 속도:
기계의 여권에 따라 회전 수를 받아들입니다. N= 160분
절단 속도 지정:
토크 결정:
중 KP =10 씨 중 디 큐 에스 와이 케이 MP
보정 계수 케이 MP절삭력용
케이 MP =0.85 탭.50
와 함께 중= 0.046 표 51
큐= 1,1
중 KP =10 0.046 24 1,1 1.5 1,5 0.85=23.69시간중
절삭력 계산
kW
kW
주요 기계 처리 시간을 결정합시다.
~까지=
분
2) 설정 B:
부품은 고정구에 설치되며 목 Ç32,2n6의 표면을 기준으로 합니다.
이 전환에서 나사산 M24 × 1.5-6g가 수행됩니다.
이송(나사 피치와 동일) 에스= 1.5mm/회전
나사 직경 D=24mm
절삭 깊이 t=1.3mm
스트로크 길이 결정 Lpx:
엘픽셀=엘컷+와이+ 엘추가의
어디 엘자르다 -가공 길이와 동일한 절단 길이. 엘컷= 20.4mm
엘추가하다 -경우에 따라 부품의 설정 및 구성 기능으로 인해 추가 스트로크 길이가 발생합니다.
와이 – 접근 길이, 플런지 및 공구 오버런
엘엑스트라+와이=3 mm
엘픽셀 = 20.4+3=23.4mm
절단 속도 결정 V, m/min, 스핀들 속도 N, 분,
절삭 속도에 대한 총 보정 계수 Kv는 개별 계수의 곱입니다.
에게뮤직비디오- 가공된 재료의 품질의 영향(강의 경우 = 0.8) 표 50,
케이 티 V - 절단되는 나사의 정확도 고려(정확도 = 0.8) 표 50,
쿠브 – 절단부 재질의 영향(= 1.0) tab.50
티 -공구 수명; 티= 120분 탭49;
와 함께 V= 7.4 탭.49
중 = 0,5
큐= 1,2
스핀들 속도:
기계의 여권에 따라 회전 수를 받아들입니다. N= 160분
절단 속도 지정:
토크 결정:
중 KP =10 씨 중 디 큐 에스 와이 케이 MP
보정 계수 케이 MP절삭력용
케이 MP =0.85 탭.50
와 함께 중= 0.046 표 51
큐= 1,1
중 KP =10 0.046 24 1,1 1.5 1,5 0.85=23.69시간중
절삭력 계산
주요 기계 처리 시간을 결정합시다.
~까지=
분
3) 작업에 대한 조각 계산 시간의 결정.
대량 생산 및 대량 생산 조건에서 시간의 기술적 규범은 계산 및 분석 방법에 의해 설정됩니다. 연속 생산에서 조각 계산 시간의 표준이 결정됩니다.
Tsh-k = + Tsht,
어디 Tpz -준비 - 작업의 마지막 시간입니다.
N – 부품의 출시 배치 크기; N= 280개
Tsht=To+Tv케이+Tob.from,
어디 저것 -메인 타임,
TV -보조 시간:
TV=터스+쯔+툽+티즈,
어디 투스 -설치 및 제거 시간 ,
쪼 -부품을 조이고 푸는 시간,
멍청한 -약속 시간 기계 제어,
티즈 -부품을 측정하는 시간,
Tob.from -작업장 유지 및 휴식 및 개인적인 필요를 위한 휴식 시간,
케이- 연속 생산을 고려한 계수 ( 케이=1,85).
토브닷=티 op 7%
티 op =티 영형 +T V · 케이
티 op =0.24+(0.094+0.068+0.12+0.55)1.85=1.78분
Tob.ot \u003d 1.78 0.07 \u003d 0.125분
얻은 시간 규범 값은 표 5에 요약되어 있습니다.
표 5
이름 |
전환 1 |
전환 2 |
|
투스 -설치 시간과 부품 제거, 분 |
|||
쪼 -부품을 조이고 푸는 시간, 분 |
|||
멍청한 -기계 제어 시간, 분 |
|||
티즈 -부품 측정 시간, 최소 |
|||
Tob.from –작업장 유지 관리 시간 및 휴식 및 개인적인 필요를 위한 휴식 시간, 분 |
|||
Tpz -준비 - 마지막 시간, 분 |
|||
저것– 주요 시간, 분 |
|||
기기를 받고 반환하는 데 걸리는 시간, 최소 |
테이블을 기반으로 다음을 얻습니다.
Tsh-k= +0,24+0,125 = 0.46분.
1.7.2 가공 정확도 계산
가공정도의 계산은 정밀가공의 총오차를 결정하고 이를 9등급 정확도 40.266 h9(-0.062)에 따른 치수공차와 비교하는 것으로 이루어진다.
총 처리 오류는 다음 공식으로 계산됩니다.
어디서 - 처리 과정에서 발생하는 오류;
- 기술 시스템을 크기로 설정하는 오류.
1. 공구의 치수 마모로 인한 가공 오차를 파악합니다.
공작물 배치를 처리 할 때 공구의 허용 치수 마모 표 29를 사용하여 다음을 결정합니다.
20μm
2. 힘의 불일치로 인한 탄성 푸시다운 정의
기계 캠에 고정하여 표면 처리를 하였으므로 여기에는 다음 공식이 적용됩니다.
규정 준수 와 동등하다
μm/kN
레이디얼 포스 공식으로 정의
어디 mm;
mm
절단 속도 값: m/min.
표 22에 따르면 다음을 찾습니다. 와 함께 피 = 204; N = 0; 엑스= 1,0; 와이= 0,75
절삭력에 대한 보정 계수 값
케이 피 =0,734
절단 속도를 계산하고 반경 방향 힘을 결정하십시오
탄력있는 팔굽혀펴기를 정의하자
3. 사이즈에 대한 기술적 시스템 설정의 오류를 판단하자
㎛.
4. 온도 변형은 공식에 의해 결정됩니다.
,
미크론
5. 공식으로 결정
,
mm,
mm;
㎛.
총 처리 오류
총 오차를 크기 허용 오차 40.266 h9, 즉 62 µm와 비교합니다.
62μm > 55.5μm
결론: 가공의 정확도가 관찰됩니다.
1.7.3 장비 선택
기업에서는 가능한 한 모든 작업이 한 작업장의 장비에서 수행되는 방식으로 기술 경로를 그리려고 합니다. 경로 프로세스의 일부를 다른 상점으로 이동할 때 많은 문서를 작성해야 하기 때문입니다.
설계된 기술은 이 규칙을 만족합니다. 수확 작업을 제외한 모든 작업은 작업장의 한 섹션에서 수행됩니다.
장비의 특정 모델 선택은 전체, 정확도 및 전력 기준에 따라 수행됩니다.
작업별 장비 분포는 표 6에 요약되어 있습니다.
표 6
머신 이름 |
자르는 기계 |
장치 및 보조 도구 |
측정 도구 |
|
밀링 및 센터링 반자동 |
드릴 4 R6M5 GOST 14034-74 드릴 센터. 2317-0107 (f4.00) GOST 14952-75 엔드밀 Ø 100 T5K10 GOST 24359-80 커터(f100) 2214-0001 T5K10 45° GOST 24359-80 |
|||
나사 절삭 선반 CNC 16K20F3 |
인서트가 있는 스루 커터 PCLNR 2020K-12: CNMG120408T-NR 스트레이트 커터 SVJCR 2020К-16 |
척 2 x 캠 |
마이크로미터 MK 25-1 GOST 6507-78 캘리퍼스 ШЦ-I-125-0.1-1 GOST 166 거칠기 샘플 GOST 9378-75 |
|
키홈 밀링 머신 6D92 |
특수 키 커터 Ç12mm P6M5 커터(f12) 2234-0367 N9 GOST 9140-78 특수 곰팡이 절단기 Ç48 mm 및 b=8 H8 R6M5 |
특수 장치 |
캘리퍼스 ШЦ-I-125-0.1-1 GOST 166 |
|
나사 절단 반자동 장치 5D07 |
빗 2671-0773 GOST 21761-76 |
머리 2681-0023 GOST 21761-76. 자체 센터링 죠가 있는 바이스 |
나사산 링 М24×1.5. 홍보 및 NOT. |
|
원형 연삭기 3M151 |
그라인딩 휠 PP300×30×24A40PS1-S2 6K5 50 m/s 1kl.A GOST 2424-83 |
중앙 전면, 후면 GOST 13214-79 칼라 GOST 16488-79 |
스테이플스 애비뉴 그리고 아닙니다. 거칠기 샘플 GOST 9378-75 |
드릴 2300-6173 (f5.00) GOST 10902-77
캘리퍼스 ШЦ-I - 250-630 - 0.05-1 GOST 166-89
캘리퍼스 ШЦ-I - 125 - 0.05-1 GOST 166
캘리퍼스 ШЦ-I - 125 - 0.10-1 GOST 166
삼각대 ШМ-I-8 GOST 10197-70
표시기 ICH02 cl. 1 GOST 577-68
각도계 유형 1-2 GOST 5378-88
마이크로미터 MK50-1 GOST 6507
마이크로미터 MK25-1 GOST 6507-90
브래킷 061 OST 95 1960-78 컷. 지름
브래킷 СР 50 GOST 11098-75
링 8211-0094 6g(M24 X1.5-PR) GOST 17763-72
링 8211-1094 6g (M24 X 1.5-NOT) GOST 17764-72
코르크 8133-0630 (f5) H14 GOST 14807-69
2. 기술 장비, 측정 및 절단 도구의 설계
2.1 고정 장치에 부품을 설치하기 위한 선택 및 정당화
부품 도면에서 키홈 밀링 작업을 위해 특수 고정 장치를 사용하여 부품을 기계에 고정해야 합니다. 그 안에 공작물은 프리즘과 두 개의 지지대를 기반으로합니다. 픽스쳐는 대규모 생산에 사용되기 때문에 퀵 클램핑 장치가 장착되어야 합니다. 이러한 요구 사항은 클램핑 메커니즘의 공압 드라이브에 의해 충족됩니다.
2.2 장치의 설계 및 작동 원리에 대한 기술적 설명
장치는 본체, 설치 프리즘, 레버 클램핑 장치로 구성됩니다. 단동식 피스톤 공압 실린더는 압축 공기가 공압 실린더의 상부에 공급될 때 드라이브로 채택되며, 로드가 있는 피스톤은 레버 전달을 통해 부품을 하강하고 가압합니다. 즉 부품이 고정됩니다. 상부 캐비티로의 압축 공기 공급이 중단되면 클램핑 메커니즘에 장착된 스프링이 클램프를 올리고 이에 따라 로드와 피스톤 로드가 상승하여 부품이 해제됩니다.
2.3 클램핑 메커니즘의 고정 및 계산을 위한 설계 계획 개발
공작물은 고정물의 장착 요소를 기반으로 하며 힘 Q로 클램프에 의해 눌려지고 절삭력 P o는 수직 방향으로 작용합니다. 절삭력 P o 는 고정물의 지지 표면과 부품의 하부 베이스 평면 사이, 그리고 부품의 상부 평면과 클램핑 표면 사이의 마찰력 T에 의해 상쇄됩니다.
쌀. 4
Y 축을 기준으로 공작물에 작용하는 모든 힘의 평형 방정식을 작성해 보겠습니다.
ΣF yi =Q – 2Rsina/2=0
필요한 클램핑력은 다음 식에서 결정됩니다.
kP o \u003d Qf 1 + 2Rf 2
, 어디
k-클램프 안전 계수.
k 0 =1.5 - 보장된 안전 계수.
k 1 \u003d 1.0 - 수당 변경을 고려한 계수
k 2 \u003d 1.4 - 공구가 둔해질 때 절삭력 증가를 고려한 계수.
k 3 \u003d 1.2 - 단속 절삭으로 절삭력 증가를 고려한 계수
k 4 \u003d 1.0 - 클램핑력의 불변성을 고려한 계수
k 5 \u003d 1.0 - 수동 클램핑 메커니즘만을 특성화하는 계수
k 6 \u003d 1.0 - 공작물을 회전시키는 경향이 있는 모멘트의 존재를 고려한 계수.
에이= - 프리즘 각도
f 1 \u003d f 2 \u003d 0.15
클램핑 메커니즘 계산:
드라이브 크기를 결정합니다.
아르 자형 그리고 =0,785 디 2 피시간
p \u003d 0.4 N / m 2 \u003d 4 kgf / cm 2 - 압축 공기의 특정 압력;
=0,7.
결과 지름을 가장 가까운 값으로 반올림합니다.
막대 직경: d=0.25D=0.25*100=25mm.
중고 문헌 목록.
A.F. 고르바체비치.엔지니어링 기술을 위한 코스 디자인. 민스크: 고등학교, 1983년.
A. G. 코실로바그리고 R. K. 메시체랴코프.기술자 기계 제작자의 핸드북. 두 권으로. 볼륨 2. M .: "엔지니어링", 1985.
"금속 절단 모드". 에 의해 편집된 핸드북 유.브이. 바라노프스키. M. "엔지니어링", 1972.
A. G. 코실로바그리고 R. K. 메시체랴코프.기술자 기계 제작자의 핸드북. 두 권으로. 볼륨 1. M .: "엔지니어링", 1985
일명 고로쉬킨.금속 절삭 공작 기계용 장치. 핸드북 7판, 수정 및 보완. M.: 마시노스트로에니 1979
"금속 가공": 핸드북 편집 A.A. 파노바. - M.: 마시노스트로에니, 1988.
BL 베스팔로프, LA 글레이저, 아이엠 콜레소프엔지니어링 기술 M., "엔지니어링", 1973
자동화 엔지니어링 기술의 설계: Proc. 기계공학용. 전문가. 대학/ 그들을. Baranchukova, A.A. Gusev, Yu.B. Kramarenko 및 기타; 에드. 유엠 솔로멘체프. - 2nd ed., Rev. - 남: 더 높습니다. 학교, 1999
"샤프트"클래스의 부품은 주로 한 축을 중심으로 한 외부 회전 표면에 의해 형성된다는 사실이 특징입니다. 샤프트의 길이는 직경보다 훨씬 큽니다.
일부 디자인에서는 내부 중앙 구멍이 있을 수 있습니다.
목적, 디자인, 무게, 가공 정확도, 재료 및 기타 지표면에서 이 클래스의 부품은 매우 다양합니다.
압연 장비에서는 무게가 수 킬로그램에서 20-30톤까지이고 직경이 최대 -800-1200mm인 샤프트가 사용됩니다.
"샤프트"클래스는 다음과 같은 주요 그룹으로 나뉩니다. 샤프트와 차축은 부드럽습니다. 계단식; 구멍; 모양의 곡선 및 원추형 표면이 있습니다.
각 그룹에서 샤프트는 가공할 표면의 크기만 다른 유형으로 나뉩니다.
"샤프트"클래스의 부품을 처리 할 때 다음이 필요합니다.
1. 축을 똑바로 유지하십시오. 샤프트와 액슬의 모든 섹션의 정렬 및 직진도는 설정된 허용 오차 내에 있어야 합니다.
2. 축을 중심으로 회전 표면을 유지하십시오. 가공된 넥의 타원도와 테이퍼는 직경 허용 오차 내에 있어야 합니다.
3. 위치 지정 저널에 대한 샤프트 베어링 저널의 반경 방향 런아웃 값이 0.02-0.03mm 이내로 유지되도록 합니다.
4. 기어, 풀리 및 플라이휠의 베어링 저널 표면은 6등급 청정도로, 구름 베어링은 7등급 청정도로, 롤 배럴은 7-8등급 청정도로 처리하십시오.
5. 끝과 선반을 축에 정확히 수직으로 자릅니다.
6. 키홈, 스플라인 및 클럽에 올바른 프로파일을 지정하고 샤프트 표면의 특정 위치에 배치합니다.
7. 설계자가 지정한 작업면의 경도를 유지하십시오.
샤프트의 공작물 선택은 샤프트의 목적, 샤프트를 만드는 재료의 브랜드 및 설계 특징에 따라 결정됩니다.
대부분의 범용 샤프트의 경우 탄소강 등급 St. 5, 예술. 6, 강철 40 및 50. 특히 중요한 샤프트는 크롬, 크롬-몰리브덴, 크롬-실리콘 등의 고합금강으로 만들어집니다. 압연 롤 제조의 경우 경우에 따라 크롬과 니켈이 첨가된 합금 주철 마그네슘이 개질제인 변성 주철도 사용됩니다. 롤의 목적에 따라 작업 표면의 경도는 30에서 75 쇼어 단위까지 다양합니다.
샤프트 블랭크는 다음 순서로 전처리됩니다. 편집, 마킹, 절단, 트리밍 및 센터링, 제어.
샤프트 가공의 주요 작업은 선삭이며 그 동안 재료의 대부분이 제거됩니다. 그 결과 샤프트에 필요한 모양과 주요 표면 치수가 제공됩니다.
황삭 선삭은 4-5등급 정확도 등급과 3-4등급 청정도 등급을 제공합니다. 가공은 절삭 깊이 5-25mm 이상, 이송 0.5-3mm/rev, 절삭 속도 30-40m/min으로 수행됩니다. 압연 제품을 황삭할 때 고속 강판에 커터를 사용하면 좋은 결과를 얻을 수 있습니다. 무거운 단조품을 가공할 때 T5K10 및 T15K6 경질 합금 인서트가 있는 커터를 사용하면 최상의 결과를 얻을 수 있습니다. 황삭은 주로 동력 절단의 원리에 따라 수행됩니다. 주요 시간과 기계의 전체 사용을 줄이기 위해 다음 조치가 사용됩니다.
두 개의 커터가 캘리퍼에 설치되어 있으며, 각각은 도달 범위가 다르며 깊이의 특정 부분을 제거합니다.
"캘리퍼의 정방향 및 역방향 스트로크로 절단할 수 있는 여러 절단 모서리가 있는 절단기를 사용하십시오.
솔리드 칩 너비를 줄여 절삭력을 줄이는 스텝 커터가 사용됩니다.< ,
길고 무거운 샤프트를 가공할 때 기계의 전후방 캘리퍼를 사용하여 2개 및 3개의 캘리퍼를 사용합니다.
샤프트 황삭은 일반적으로 두 가지 설정으로 수행됩니다. 선삭의 경우 커터를 통해 직선 또는 구부러진 오른쪽 및 왼쪽이 사용되며 끝과 선반 절단 - 언더컷 및 필렛 처리 - 특수 곡선 및 오목 필렛 커터가 사용됩니다. 큰 반경(30mm 이상)의 필렛은 종종 템플릿에 따라 세로 및 가로 이송을 결합하거나 캘리퍼스의 크로스 슬라이드에 장착된 특수 회전 장치를 사용하여 절단됩니다.
단차축을 가공할 때는 직경이 크고 더 큰 단차를 먼저 가공하는 것이 좋습니다. 가장 널리 퍼진 것은 계단식 샤프트 처리를 위한 두 가지 방식입니다(그림 45).
계단의 직경에 약간의 차이가 있으면 그림 1의 구성표. 45, a, 직경과 큰 직경의 샤프트에 상당한 차이가 있습니다. 45, 나. 때로는 두 체계를 모두 사용하여 결합 처리가 사용됩니다. 최상의 성능과 그 이상을 제공하는 방법을 선택해야 합니다. 완전한 사용기계.
원추형 및 모양의 표면을 돌릴 때 세로 및 가로 피드의 조합을 사용하거나 템플릿에 따른 처리 또는 복사기가 사용됩니다.
공연자의 높은 자격을 요구하는 첫 번째 방법은 단일 및 소규모 생산에 사용됩니다.
짧고 가파른 원뿔은 캘리퍼스의 상단 슬라이드를 돌리고 원뿔 각도의 절반과 같은 각도로 커터를 공급하여 가공됩니다. 길고 얕은 원뿔은 심압대를 혼합하여 회전하여 원뿔의 모선이 스핀들 축과 커터의 길이 방향 움직임과 평행이 되도록 합니다. 이 방법은 매우 간단하고 모든 선반에 적용할 수 있지만 작업이 고르지 않고 센터가 마모되고 센터 홀이 파손됩니다.
길이가 작은 모양의 표면을 처리할 때 일반적으로 가로 이송으로 처리되는 특수 모양의 커터가 사용됩니다. 절삭날을 따른 커터의 프로파일은 부품의 반대 프로파일에 해당합니다. 모양 절단기 중에서 나사산, 필렛 및 홈 절단기가 야금 공학에서 더 자주 사용됩니다.
중공 가공물의 중공축 가공시 마킹, 양단 밀링, 센터링 후 황삭 가공 외부 표면샤프트를 센터와 척에 장착하여 구멍은 고정된 선반 또는 수평 보링 및 보링 머신에서 드릴링 및 보링됩니다. 최근에는 코어가 별도의 샤프트 형태로 제거될 때 중공 드릴을 사용한 드릴링이 보편화되었습니다. 직경이 100mm 이상인 구멍에도 유사한 방법이 사용됩니다.
에 따라 명세서황삭 후 샤프트는 마무리 또는 후속 기계적 마무리와 함께 중간 열처리로 이송될 수 있습니다. 이 모든 경우에 황삭 후에 여유를 남겨야 합니다. 압연 블랭크의 황삭 선삭 후 미세 선삭에 대한 여유는 면당 0.5-2mm 남습니다. 단조 샤프트의 경우 허용 오차는 2.5-5mm로, 한편으로는 크게 설명됩니다. 전체 치수샤프트 및 다른 한편으로 더 많은 노력과 열 변형으로 더 어려운 조건에서 황삭이 수행되어 결과적으로 표면층이 더 깊이 손상되었습니다. 황삭 후 열처리가 수행되면 가능한 변형 및 부품 표층 손상을 보상하기 위해 공차가 약 1.5-2 배 증가합니다. 열처리.
열처리를 위해 준비된 공작물은 샤프트 단차 사이의 모든 직경 차이를 반복해야 합니다. 그러나 인접한 단계의 직경 차이가 10mm를 초과하지 않으면 직경이 1만큼 회전합니다. 날카로운 전환이나 모서리가 없어야 합니다. 노멀라이제이션 또는 에이징의 형태로 열처리하는 동안 구조가 개선되고 내부 응력이 제거됩니다. 열처리 후 상당한 여유가 있으면 작업은 반마무리와 정삭의 두 가지 전환으로 나뉩니다. 후자는 1-2mm의 절단 깊이에서 생산됩니다.
마무리 패스에서 커터는 반경이 2-3mm인 둥근 상단 또는 Zcp = 0°인 더 넓은 절삭날을 가지며, 이는 1의 증가된 이송으로 작업할 수 있는 Kolesov 유형 커터에 일반적입니다. -2.5 mm/rev 및 세심한 작업 청결도 6등급 제공.
작업장에 무거운 연삭기가없고 큰 샤프트에서 2 등급에 따라 별도의 단계를 견뎌야하는 경우 절단 깊이가 0.1-0.3mm 이하인 넓은 스프링 커터로 회전됩니다. 7급 청정도가 요구될 때 기계 지지대의 특수 홀더에 설치된 롤러가 작동합니다. 롤러 처리는 높은 청정도를 제공할 뿐만 아니라 표면에 약간의 가공 경화를 생성하여 밀도와 내마모성을 증가시킵니다.
롤러로 롤링하는 데에는 특별한 여유가 없습니다. 실제로 허용 오차는 측면당 0.01-0.02mm의 허용 오차 범위 내에 있습니다.
정삭 및 정삭 시 샤프트 및 공구 설치의 정확성, 전체 시스템의 강성, 절삭 공구의 형상 및 위치 결정 표면의 품질에 주의를 기울여야 합니다. 중심 구멍( 센터에서 가공할 때 - 팍스) 및 가공된 벨트 및 넥(lunettes에서 가공할 때). 절삭력과 부품에 대한 열 영향을 최소화해야 합니다. 어떤 경우에는 키 홈, 슬롯 또는 클럽이 표면에 위치할 수 있다는 사실로 인해 샤프트 가공이 복잡합니다.
keyed paeov 가공을 위해 샤프트에 마킹을 한 후 밀링 머신으로 이송합니다.
소형 및 중형 샤프트의 경우 키홈은 엔드 또는 특수 키홈 커터가 있는 수직 밀링 및 키홈 밀링 머신에서 가공됩니다. 첫 번째 경우 닫힌 홈을 만들 때 커터를 삽입하기 위해 드릴이 필요합니다. 무거운 샤프트는 엔드밀과 엔드밀이 있는 수평 보링 및 세로 밀링 머신의 표시에 따라 밀링됩니다. 후자는 접선 키홈 가공에 널리 사용됩니다.
홈이 있는 홈은 분할 방식 또는 롤링 방식으로 가공됩니다. 분할 방식은 미리 마킹을 하고, 중소축의 경우 분할 헤드도 사용한다. 압연 방법에 따른 절단은 웜 슬롯 커터를 사용하는 특수 슬롯 밀링 머신에서 수행됩니다.
롤링 롤 끝의 클럽 가공은 마킹을 위한 보링 머신 또는 특수 단면 및 양면 클럽 밀링 머신에서 수행됩니다. 절삭 공구는 맨드릴 또는 기계 스핀들에 장착된 커터 또는 특수 클럽 밀링 헤드입니다.
회전을 전달하기 위한 롤링 롤에 끝에 절단부가 있는 평평한 블레이드가 있는 경우 이러한 블레이드를 처리할 때 다음 작업이 필요합니다.
I. 마킹 - 중심선을 그립니다.
Ⅱ. 대패질 - 칼날 대패질 -
파이. 표시 - 인두를 표시합니다.
IV. 드릴링 - 목구멍을 뚫습니다.
V. 자물쇠 제조공 - 인두의 뚫린 부분을 녹아웃. .
VI, 보링 - 보링 머신에서 내부 윤곽을 따라 셰드를 밀링합니다.
마지막 작업은 휴대용 크로스 대패에서도 수행할 수 있습니다. 하나 또는 다른 기계의 선택은 장비의 가용성, 목의 크기 및 경제성에 따라 결정됩니다. 일례로, 다음은 도 1에 도시된 단차축을 가공하기 위한 공정 흐름이다. 46. 샤프트 재질 - 인장 강도 av = 65 kg / mm2인 크롬강 20XA - 빌렛 - 자유 단조로 얻은 단조. 수당은 기준에 따라 선택됩니다.
처리 중 작업 순서는 다음과 같습니다. I. 마킹 - 블레이드를 표시합니다.
Ⅱ. 보링 - 끝을 밀링하고 중심선을 줄이고 중심과 중심을 표시합니다.
6 주문 222
III. 터닝 - 크기로 회전하고 끝과 선반을 자릅니다.
IV. 마킹 - 키홈을 표시합니다.
V. 밀링 - 키홈 밀링.
무화과. 46. 계단형 샤프트와 그 블랭크.
VI. 연삭 - 목을 갈기.
VII. 터닝 - 필렛을 처리하고 끝 부분과 선반을 크기에 맞게 자릅니다.
Ⅷ. 자물쇠 제조공 - 버를 제거하십시오.
이 TP에는 다음 작업이 포함됩니다.
직면, 센터링
샤프트 저널의 선삭(선삭)
사전 연마
키홈 밀링
스플라인 밀링
스레드 처리
열처리
센터 홀 고정
샤프트 저널의 미세 연삭
스플라인 연삭
나사산 교정 및 디버링
홍조
제어
1.2.1. 샤프트 페이싱 및 센터링
단일 및 소규모 생산에서 끝단은 터닝 및 밀링 머신에서 처리됩니다. 센터링은 드릴링, 터닝, 회전 및 수평에서 수행됩니다. 보링 머신.센터링은 두 개의 도구(트위스트 드릴 및 카운터싱크) 또는 하나의 결합된 센터 드릴로 수행할 수 있습니다. 드릴의 테이퍼 각도는 일반적으로 60°이지만 무거운 샤프트 블랭크의 경우 75° 또는 90°로 증가됩니다.
어떤 경우에는 절삭 공구에 120° 각도의 추가 모따기가 있어 우발적으로 샤프트 끝이 손상된 경우 중앙 구멍을 흠집으로부터 보호합니다.
연속 및 대량 생산에서는 2개의 끝이 동시에 밀링되는 반자동 밀링 및 센터링 기계가 사용됩니다(그림 1.3의 위치 2). 그런 다음 2개의 구멍이 센터링됩니다(위치 3).
쌀. 1.3. - 밀링 센터링 반자동 장치의 샤프트 가공 방식.
1.2.2. 샤프트 터닝
샤프트 선삭에는 일반적으로 황삭 및 정삭 작업이 포함됩니다. 황삭 선삭에서는 더 큰 절삭 깊이와 높은 이송 속도로 작업하여 대부분의 여유가 제거됩니다.단일 및 소규모 생산에서 선삭은 선삭에서 수행됩니다. 범용 기계. 계단식 샤프트를 가공할 때 예를 들어 그림과 같이 다양한 절단 패턴이 사용됩니다. 1.4.
그림의 다이어그램에서. 1.4., 커터 이동의 전체 길이 , 즉. 그림의 다이어그램보다 작습니다. 1.4., 그러나 작업 및 보조 이동의 수는 더 많습니다.
쌀. 1.4. – 샤프트 터닝 방식
절단 방식을 선택할 때 생산성을 극대화하고 작업 비용을 최소화하기 위해 노력합니다. 동시에 샤프트의 치수, 치수를 설정하고 제어하는 방법, 공차 및 기타 요소가 고려됩니다.
가끔은 단차의 지름차이가 커서 축을 최대한 약하게 하지 않고 지름이 가장 작은 단차를 마지막으로 돌리는 경향이 있습니다.
긴 비강성 샤프트를 회전할 때 고정식 또는 이동식 스테디 레스트가 사용됩니다. 고정 레스트는 머신 베드에 장착됩니다. 움직일 수 있는 안정된 받침대는 캘리퍼에서 움직이고 캠은 커터를 따릅니다(그림 1.5., a).
가공 표면과 표면 2의 정렬을 보장해야 하는 경우(그림 1.5., b) lunette 캠은 표면의 커터 앞에 배치됩니다.
쌀. 1.5. – 스테디 레스트를 사용하여 샤프트를 회전시키는 방식
현재 CNC 기계는 소규모 생산에 사용됩니다. 이를 통해 처리 주기를 자동화하고, 향상된 절단 조건을 사용하고, 생산성을 높이고, 다중 기계 유지 관리를 적용하고, 고도로 숙련된 노동력의 부족을 줄이고, 낭비를 줄이고, 생산 준비 시간을 줄일 수 있습니다.
터닝 샤프트의 대규모 및 대량 생산에는 다중 절단 및 수중 복사 기계와 반자동 기계가 사용됩니다. 일반적으로 종단 및 보링 홈 및 형상 선삭에 사용되는 세로 및 가로 2개의 캘리퍼스가 있습니다.
캘리퍼스는 동시에 작동할 수 있습니다. 다중 절단기에서 필요한 경우 플런지 선삭 및 후속 세로 이송이 사용됩니다(그림 1.6., b).
쌀. 1.6. - 다절삭 반자동에서 샤프트를 돌리는 방식
다공선반은 범용선반에 비해 스트로크 단축, 커터 동시작업, 커터교체, 툴포스트 회전, 캘리퍼 공회전에 소요되는 시간을 줄여 생산성을 높인다.
수경 복사기의 세로 지지대에는 하나의 샤프트 넥 크기로 조정되는 1개의 커터가 설치되어 있습니다. 나머지 치수를 얻는 것은 복사기와 추적 시스템에 의해 제공됩니다. 동시에 측정 횟수가 줄어들고 수동 피드로 작업할 때보다 더 높은 절단 모드가 적용됩니다.
샤프트는 하나 또는 여러 작업 스트로크로 회전하는 반면 복사기는 복사기로 드럼을 회전하여 자동으로 변경됩니다.
샤프트가 수중 복사 및 단일 스핀들 다중 절단 반자동 기계에서 처리될 수 있는 경우 타당성 조사를 기반으로 장비 선택이 이루어집니다.
이것은 다음 고려 사항을 고려합니다.
가공 길이를 분할하여 다중 절단 선삭을 하면 작업 스트로크의 길이가 복사 가공보다 짧습니다.
수중 복사기의 설정 및 재조정 시간은 다중 절단기보다 훨씬 짧습니다.
다중 절단 기계의 절단기 수와 절단 조건은 종종 공작물 규정 준수와 불충분한 기계 출력으로 인해 제한됩니다. 수중 복사기에서는 주 절단 동작의 높은 이송 속도로 작업할 수 있습니다.
위와 관련하여 수경 복사기의 생산성은 많은 경우에 더 높습니다.
다중 절단 가공의 정확도는 상대 위치의 오차와 커터의 고르지 않은 마모에 의해 영향을 받습니다. 여러 커터로 한 표면을 처리하면 단면의 경계에 선반이 형성됩니다. 수중 복사기에서는 이러한 오류가 없으므로 치수 정확도는 높이고 거칠기는 줄일 수 있습니다.
1.2.3. 외부 원통형 표면 마무리
미세 선삭, 연삭, 연마, 래핑, 초정삭, 롤러 선삭 등은 외부 원통형 표면을 마무리하는 데 사용됩니다.1.2.2.1. 미세 회전
미세 선삭은 비철 금속 및 합금으로 만든 공작물을 마무리하는 데 더 자주 사용되며 강철 및 주철로 만든 공작물에는 덜 자주 사용됩니다. 이것은 연삭 휠의 "부하"로 인한 비철 합금 연삭의 어려움으로 설명됩니다.가공은 다이아몬드, 복합 재료, 금속-세라믹 커터 및 경질 합금이 장착된 커터를 사용하여 고속의 주요 절삭 동작, 낮은 이송 속도 및 절삭 깊이에서 수행됩니다.
미세 선삭을 사용하면 6 ... 7 등급의 가공 정확도와 표면 거칠기를 얻을 수 있습니다. ㎛.
가공 성능은 연삭보다 높습니다. 미세 선삭을 위한 대규모 및 대량 생산에는 고정밀 및 내진동성을 갖춘 특수 고속 기계가 사용됩니다.
1.2.2.2. 연마
외부 원통형 표면을 마무리하는 주요 방법입니다. 연삭의 장점은 열처리 후 공작물 오류를 수정할 수 있다는 것입니다. 기존 미세 연삭의 경우 표면 거칠기가 1.2 ... 0.3 미크론인 6-7 정확도 등급에 따라 처리가 수행됩니다.미세 연삭은 5등급 정확도와 0.16 ... 0.8 미크론의 거칠기를 제공합니다. 높은 회전 속도, 공작물의 낮은 회전 속도 및 작은 절삭 깊이에서 작은 입자의 원으로 수행됩니다.
연삭은 원형 및 센터리스에서 수행됩니다. 연삭기원의 길이 방향 이송 또는 회전 방법에 따라 (그림 1.7.)
A - 세로 피드 포함; B, C - 회전 방법(방법)에 따라
쌀. 1.7. – 원형 연삭기의 연삭 방식:
회전 방법에 따른 연삭은 더 생산적이며 원통형 및 성형 표면 처리에서 대규모 및 대량 생산에 사용됩니다.
여러 넥의 동시 연삭에 사용 특수 기계, 연삭 중 보조 시간을 줄이기 위해 여러 원으로 작업하는 활성 제어 장치는 연삭 중 공작물을 측정하는 데 사용되며 지정된 크기에 도달하면 기계를 자동으로 멈추는 장치입니다.
센터리스 연삭 (그림 1.8.)을 사용하면 공작물이 두 개의 연삭 휠 사이에 배치되며 그 중 하나 (더 큰 직경)는 연삭이고 다른 하나는 선두입니다.
쌀. 1.8. – 센터리스 연삭 방식
그라인딩 휠 1은 20-35m/s의 속도로 회전하고 휠 2는 20-30m/min의 속도로 회전합니다. 공작물(3)은 어떤 것으로도 고정되지 않고, 리딩 원을 향한 경사가 있는 지지대(4)에 의해 지지됩니다.
구동 원이있는 공작물의 파지력은 연삭보다 큽니다. 이는 다음과 같은 이유 때문입니다.
휠 속도 감소로 절삭력 증가
연결부에 리딩 서클이 생성되어 원과 공작물 사이의 마찰 계수가 증가합니다.
공작물 피드의 길이 방향 이동으로 센터리스 연삭에서 구동 휠의 축은 연삭 휠의 축과 평행하지 않습니다. 그 덕분에 아무 일 없이 특별한 메커니즘이송, 공작물이 속도로 이동합니다. 어디
- 리딩 서클의 회전 속도.
증가하는 각도로 원의 축을 교차하면 처리 성능이 향상되지만 표면 품질이 저하되므로 일반적으로
.
가공의 정확성을 향상시키기 위해 연삭을 통해 여러 작업 스트로크로 수행되는 경우가 있습니다. 대규모 및 대량 생산에서 자동 라인에 연결된 여러 기계에서 순차적으로 처리를 수행할 수 있습니다.
플 런징 방법에 따른 센터리스 연삭에서 원의 축은 대부분 평행합니다. 먼저 리딩 원이 연삭에서 후퇴하고 공작물이 지지대에 놓인 다음 리딩 원이 공작물로 가져와 지정된 크기가 얻어 질 때까지 교차 이송이 수행됩니다.
센터 연삭과 비교하여 센터리스 연삭은 다음과 같은 장점이 있습니다.
터렛 기계 및 자동 기계에서 처리되는 부품에 특히 중요한 공작물을 센터링할 필요가 없습니다.
가공된 표면을 기술 기반으로 사용하기 때문에 가공 허용 오차가 허용 오차에 미치는 영향이 제거되기 때문에 가공 허용 오차가 크게 감소합니다.
길고 가는 샤프트를 연삭할 때 스테디 레스트를 사용할 필요가 없습니다.
센터리스 연삭기는 비교적 자동화하기 쉽고 자동 라인에 통합됩니다.
센터에서 연삭할 때보다 높은 생산성을 제공합니다.
기계 제어가 쉽기 때문에 평균적인 그라인더 기술로 높은 정확도를 얻을 수 있습니다.
휠 마모로 인한 가공 오차는 센터 연삭보다 2배 적습니다. 휠 마모는 반경의 크기가 아니라 공작물의 직경 크기에 직접 반영됩니다.
1. 그러한 기계를 설정하고 조정하는 데 소요되는 시간은 상당히 크며 대량의 공작물 배치로 보상됩니다. 따라서 센터리스 연삭은 자동차 및 베어링 산업에서 가장 자주 사용됩니다.
2. 키홈, 홈, 구멍, 가공된 표면의 파손은 정상 작동을 방해하고 심지어 불가능하게 만듭니다.
3. 센터리스 연삭으로 가공면의 진원도 확보가 어렵다.
4. 이전에 처리된 다른 표면과 샌딩된 표면의 정렬을 달성하기가 어렵습니다.
1.2.3.3. 폴리싱 및 슈퍼피니싱
펠트, 펠트 또는 테이프로 만든 부드러운 휠을 사용한 연마는 공구의 고속으로 수행되며 표면에는 미세한 연마 분말과 윤활유의 혼합물이 도포됩니다. 연마는 낮은 표면 거칠기를 제공합니다(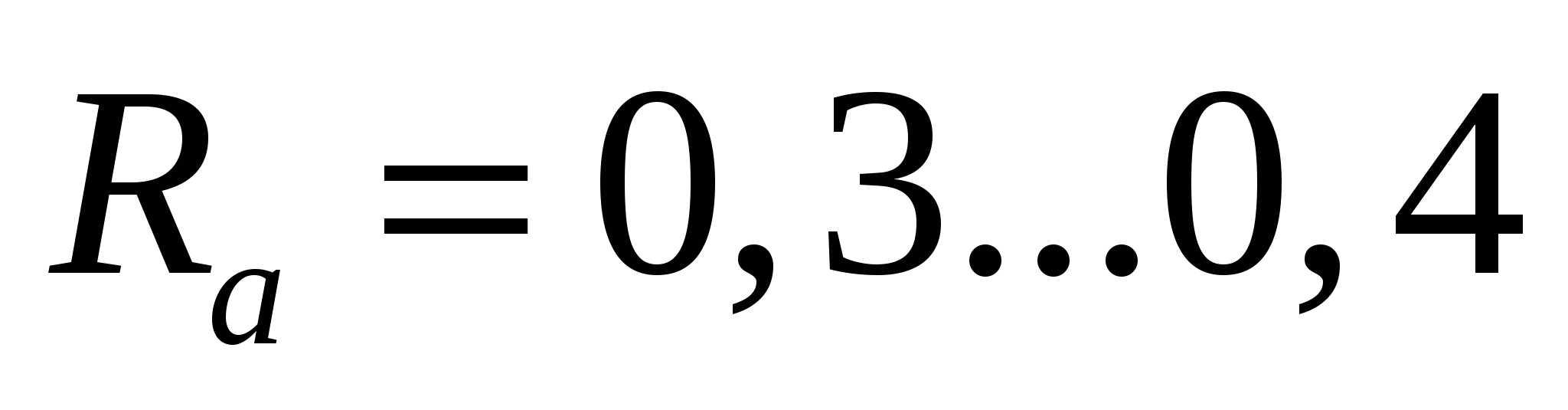
Superfinishing(진동 막대로 마무리)은 연마 입자가 같은 경로를 따라 두 번 통과하지 않는다는 사실에 있는 반복되지 않는 흔적의 원리를 구현합니다. 이를 위해 회전하는 공작물 외에도 저속 (1-2.5m / min) 및 막대의 길이 방향 이동 (그림 1.9.)에서 작은 진폭으로 분당 200-1000 진동을 알려줍니다.
진동 운동, 바의 작은 입자 크기 및 낮은 압력으로 인해 공작물의 작은 거칠기가 보장됩니다( μm).
쌀. 1.9. - 연마 막대로 샤프트를 처리하는 계획.
이 공정은 절삭유를 사용하여 진행되며, 초기 순간에 처리된 표면과 바의 접촉 면적이 작고 바의 압력이 상당하여 집중적인 금속 제거를 유발합니다. . 미래에는 막대가 들어가고 압력이 감소하며 절단 과정이 강도를 잃습니다.
초정삭은 공작물의 거시적 형상을 개선하지 않으므로 사전 처리는 부품의 정확한 기하학적 형상을 보장해야 합니다. 초정밀 수당은 일반적으로 남아 있지 않습니다.
1.2.4. 스레드 처리
1.2.4.1. 커터와 빗으로 스레딩
~에 스레딩선반에서 공작물에 회전이 주어지고 커터는 나사 피치와 동일한 회전당 이송으로 공작물의 축을 따라 이동합니다. 피치 정확도는 기계의 운동 학적 체인 정확도에 의해 결정되고 나사 프로파일의 정확도는 커터를 날카롭게하고 설정하는 정확도에 의해 결정됩니다. 따라서 처리 과정에서 터너는 일반적으로 ????????????????????????를 제어합니다.여러 작업 스트로크로 나사를 절단 할 때 예를 들어 그림 4에 표시된 구성표에 따라 커터의 가로 이송 이동을 수행 할 수 있습니다. 1.10. (a, b). 계획 (a)를 사용할 때 제공됩니다. 최고의 품질처리 된 표면 및 계획 (b)에 따라 작업 할 때 절단 층의 모양이 단순화되고 절단 및 칩 제거 프로세스가 용이합니다. 따라서 때때로 (b) 방식에 따라 황삭이 수행되고, (a) 방식에 따라 마지막 레이어가 잘립니다.
쌀. 1.10. – 스레딩을 위한 절단 패턴.
여러 작업 스트로크에서 하나의 커터로 나사를 가공하면 절삭 날이 빨리 무뎌지고 모양이 왜곡되므로 큰 피치의 나사 가공(황삭 및 정삭)에는 2개의 커터를 사용하거나 나사용 빗을 사용하는 것이 좋습니다. 스트로크 수를 줄임으로써 빗은 생산성을 향상시킵니다. 표준 빗의 단점은 포인트 블랭크 작업에 사용할 수 없다는 것입니다. 더 큰 직경의 넥에 인접한 나사 절삭용.
선반의 스레딩은 일반적으로 다음과 같은 경우에 수행됩니다.
이전에 동일한 기계를 켠 공작물의 나사산을 절단할 때 이것은 보조 시간을 줄이고 표면의 상대적 위치의 정확도를 높입니다.
정밀 긴 나사를 만들 때.
직경이 크거나 비표준 피치 및 프로파일의 나사를 절단 할 때 작은 출력으로 인해 특수 고성능 공구의 구매가 정당하지 않은 경우.
직사각형 나사를 절단할 때.
주절삭 이동의 속도를 높여 나사산의 생산성을 높이는 것은 선반에 인접한 나사를 가공하는 커터를 빠르게 후퇴시키는 것이 어렵기 때문에 어려운 경우가 많다.
대규모 및 대량 생산에서 스레드는 다중 패스 처리 주기를 자동화하는 특수 반자동 기계에서 절단되는 경우가 많습니다. 소규모 생산에서는 CNC 기계를 사용하는 것이 좋습니다.
1.2.4.2. 암나사를 사용한 나사 밀링
암 머리를 사용한 나사 가공은 나사 절단 및 나사 밀링 기계에서 수행됩니다. 초경 커터 1(그림 1.11.)은 커터 헤드에 고정되어 150-450m/min의 속도로 회전합니다. 헤드는 나사산의 각도에 따라 공작물의 축과 비스듬히 설정되며 천천히 회전하는 공작물의 1회전마다 축을 따라 단차만큼 이동합니다. 큰 스레드를 처리할 때 가장 큰 효과를 얻을 수 있습니다.쌀. 1.11. – 암 머리가 있는 실 절단 패턴.
1.2.4.3. 다이 및 자체 확장 헤드를 사용한 스레딩
터렛 선반 및 모듈러 기계에 나사 가공을 할 때 다이를 도구로 사용할 수 있습니다. 다이 홀더를 사용하면 도구가 소량을 자유롭게 움직이거나 길이 방향으로 자체 정렬할 수 있습니다. 이것은 공작물 축을 따라 다이 홀더의 이동 속도와 공작물에 다이를 나사로 고정하는 속도가 일치하지 않을 때 나사산 파손을 제거합니다.다이의 주요 단점은 나사 가공이 완료된 후 다이를 함께 나사로 조여야 하므로 생산성과 가공 품질이 저하된다는 것입니다.
자동 개방 커팅 헤드로 가공할 때 메이크업이 필요하지 않고 생산성이 크게 향상됩니다.
1.2.4.4. 디스크 및 빗(그룹) 커터를 사용한 나사 밀링
디스크 커터로 밀링 (그림 1.12.) 충분히 큰 출력 볼륨으로 큰 나사를 처리하는 데 사용됩니다. 이 경우 처리는 1-3 작업 단계로 수행됩니다. 공작물이 천천히 회전하고 주 이동 속도로 회전하는 커터는 나사 피치와 동일한 회전당 이송으로 축을 따라 이동합니다.쌀. 1.12. – 나사 밀링 방식.
밀링의 장점은 선삭에 비해 높은 생산성, 다중 기계 유지 보수의 가능성 및 저숙련 작업자의 사용입니다.
빗(그룹) 커터를 사용한 밀링은 미세 피치의 짧은 암나사를 얻는 데 사용됩니다.
디스크 커터로 나사산을 처리하는 것과 달리 콤 커터와 공작물의 축은 평행합니다(그림 1.13.). 커터의 길이는 일반적으로 공작물의 나사 부분의 길이보다 2-3 단계 더 깁니다.
쌀. 1.13. – 콤 커터를 사용한 나사 밀링 방식.
가공 시작 시 로터리 커터가 반경 방향으로 이동합니다. 그리고 나사산 프로파일의 깊이까지 공작물 속으로 뛰어듭니다. 이 경우 공작물이 1회전할 때 커터가 축을 따라 나사 피치만큼 이동합니다(이송 동작
). 밀링은 공작물의 1.2회전에서 발생합니다. 또한 가공 시작시 커터 절단 및 끝 - 절단 흔적 청소에 0.2 회전이 필요합니다.
1.2.4.5. 스레드 롤링
나사 압연은 대규모 및 대량 생산에 사용됩니다. 높은 생산성에 더하여, 이 방법은 금속의 양호한 경화된 표면 구조를 얻는 것을 가능하게 한다. 재료의 섬유는 소성 변형되고 절단되지 않습니다.실은 플랫 다이 또는 롤링 롤러로 감습니다.
플랫 다이에(그림 1.14.) 동일한 프로파일과 리드 각도를 가진 직선 나사(나사 전개)가 있습니다. 압연 스레드와 마찬가지로. 실은 슬라이더의 한 번의 이중 스트로크로 말립니다. 분당 더블 스트로크 수는 280에 이릅니다.
쌀. 1.14. – 다이를 사용한 스레드 롤링 방식.
1개의 롤러를 사용한 나사 압연은 한쪽 반경 방향의 힘으로 인해 선반, 터렛 및 자동 기계에 사용됩니다. 이 경우 공작물의 굽힘이 가능합니다.
따라서 반경 방향 이송 운동이있는 두 개의 롤러를 사용한 실 롤링이 더 널리 보급되었습니다 (그림 1.15.).
나사산 압연은 또한 일정한 중심 거리에서 세로 방향으로 이송되는 2개 또는 4개의 롤러로 수행할 수 있습니다. 생산성 측면에서 롤러를 사용한 압연은 일반적으로 다이 압연보다 열등합니다.
쌀. 1.15. - 롤러로 실을 롤링하는 방식.
매우 드문 예외를 제외하고 모든 유형의 샤프트 가공은 센터 머신을 사용하여 구축되며 이 경우 기술은 다음 작업으로 구성됩니다. 공작물 절단, 끝단 절단 및 센터링, 선삭 작업은 센터 선반에서 가장 자주 수행 표준형 다절삭기에서는 공작물을 선삭할 때 홈가공을 한 후 모든 연삭가공 후 키홈 밀링을 샤프트 연삭가공 전에 가장 많이 수행합니다.
샤프트의 모든 가공이 완료된 후가장자리의 조임으로 인한 연삭 후 너비의 왜곡으로 인해 키 홈의 벤치 청소를 수행해야합니다. 따라서 일부 공장에서는 특히 샤프트를 연삭한 후 반원 키를 홈 가공하는 경우 키 홈을 밀링 가공하는 것을 선호합니다. 이 경우 모서리의 약간의 상승으로 인해 챔퍼링과 같은 수동 청소 작업도 수행해야 하지만 이 작업은 첫 번째 경우보다 덜 힘들고 작업 중 샤프트가 손상될 위험이 있습니다. 청소가 줄어듭니다.
모든 샤프트 터닝이 완료되었습니다., 일반적으로 다중 절단 선반의 두 가지 설치에서 각 설치마다 샤프트의 일부를 돌립니다. 또한 샤프트의 설계 및 장비의 상태에 따라 샤프트도 선삭을 마무리하는 경우가 있으며 언더컷 필렛, 홈 등의 끝 부분을 트리밍하는 등 정삭의 성격을 띠는 몇 번의 짧은 선삭 작업이 있습니다.
홈 가공종종 특수 홀더에 장착된 하나 또는 두 개의 널링 롤러를 사용하여 기존 선반에서 만들어집니다. 롤러는 전체 프로파일 주름이 한 번에 형성될 정도로 샤프트에 대해 눌려지는 동안 세로 이송으로 굴러갑니다.
연삭 작업전통적인 센터 라운드 연삭 기계에서 생산됩니다. 대부분의 표면은 원과 관련하여 제품의 길이 방향 이동으로 연마되며, 일부 경우에만 가공할 표면의 너비에 따라 가로 이송을 사용하여 넓은 원을 연삭하는 더 효율적인 방법입니다.
키홈 밀링간단한 수평 밀링 머신에서 생산됩니다. 키홈 제조에서 작은 수공구가 큰 성공을 거두었습니다. 밀링 머신레버 제어로. 단순함과 원시성에도 불구하고 이러한 밀링 머신은 이러한 단기 작업에 매우 편리하고 생산성이 높은 것으로 판명되었습니다.
길고 얇은 샤프트의 제조에서 연삭 전에 직선화 작업이 도입되며 수동 또는 기계 구동 프레스 또는 소형 유압 또는 공압 프레스에서 수행됩니다. 생산 공정의 모든 치수 제어는 견고한 한계 게이지 및 템플릿을 사용하여 수행됩니다. 런아웃 확인 및 드레싱 작업을 제외하고 표시 장치는 거의 사용되지 않습니다.
설명된 기술의 단점은 주로 다음과 같이 축소됩니다.:
1) 사용된 장비와 제조 방법은 생산성이 낮고 현대적인 대량 생산 방법에 뒤떨어져 있습니다.
2) 대부분의 경우 검정 미보정 막대 형태의 강철이 출발 재료로 사용되므로 샤프트의 중간 부분도 가공해야 합니다. 가장 큰 직경. 처리의 복잡성을 증가시키는 이 상황만으로도 최소한 15-20%의 재료 손실이 발생합니다.
3) 공작물 절단, 끝단 회전 및 센터 드릴링 작업은 대량 생산 작업을 위해 설계된 기존 장비에서 수행되므로 생산성이 낮고 수동 보조 시간의 비율이 상대적으로 많습니다. 예를 들어, 센터 드릴링은 수직에서 가장 자주 수행됩니다. 드릴링 머신두 가지 전환, 즉 샤프트의 각 측면이 독립적으로 샤프트를 회전시킵니다.
4) 선삭 작업은 생산성이 충분하지 않은 범용 장비에서도 수행됩니다. 사용되는 다중 절단기의 특별한 단점은 한 샤프트 크기에서 다른 샤프트 크기로의 빠른 설정 변경에 대한 적응성이 낮기 때문에 전환 중에 큰 시간 손실이 발생합니다. 주름을 만드는 데 사용되는 방법에 특별한주의를 기울여야합니다. ~에 기존 방식사전 회전 된 샤프트의 선반에서 롤링 할 때 직경의 치수를 충분히 정확하게 유지하고 허용되지 않는 치수 변동 및 주름의 요구되는 직진도 편차를 피하는 것은 불가능합니다. 후자는 다음을 위해 필요합니다. 적당한 핏로터 코어(전기자). 마지막으로, 세로 방향 이송으로 좁은 원을 연삭하는 방법은 비효율적입니다. 일반적으로 예를 들어 넥을 연삭할 때와 같이 매우 가능하고 합리적인 경우에도 기계에는 작동 중, 즉 이동 중에 연삭되는 치수를 측정하기 위한 장치가 장착되어 있지 않습니다. 그러나 치수를 확인하기 위해 기계가 멈춥니다.
가공 중, 특히 최종 연삭 전과 완성된 형태의 샤프트 세척 및 세척은 현재 기술에서 제공되지 않는다는 점에 유의해야 합니다. 이것이 가장 일반적인 샤프트 센터링 프로세스의 모습입니다.
그러나 센터리스 샤프트 가공에는 완전히 다른 프로세스가 있습니다., 센터 방식에 비해 많은 장점이 있으며 처리 복잡성을 크게 줄일 수 있습니다. 이 공정은 자동차 및 트랙터 전기 장비 생산에서 샤프트 제조에 큰 성공을 거두고 있습니다.
센터리스 방법을 사용하는 경우 소스 재료는 반드시 보정되고 주의 깊게 곧게 펴진 막대여야 합니다. 첫 번째 작업 - 샤프트의 완전한 회전은 바 머신에서 수행됩니다. 회전하는 동안 긴 샤프트가 구부러지는 것을 방지하기 위해 후자는 롤러 고정 받침대로 지지됩니다. 후속 샤프트 가공 작업에서는 센터리스 연삭기에서 예비 연삭이 수행되고 두 개 또는 세 개의 연속 기계에서 제품을 통해 첫 번째 작업이 수행됩니다.
미래에는 주름이 감겨집니다.. 자동차 및 트랙터 전기 장비 생산에서의 이 작업은 다른 전기 엔지니어링 공장에서 수행되는 방식과 다르게 수행되었습니다. 직경의 정확한 치수를 보장하고 다양한 샤프트의 동일한 프레스 강도를 유지하려면 롤링 전에 후자를 직경을 따라 연마해야 하며 치수는 세 번째 정확도 등급에 따라 유지되어야 합니다. 압연 작업은 강력한 수평형 나사 압연기에서 수행됩니다. 이 압연 방법의 매우 높은 생산성 외에도 주름의 완전한 직진도가 보장되며 이는 일부 기계 설계에서 절대적으로 필요합니다.
실제로 로터 코어가 주름진 샤프트에 눌려지면 프레싱 과정에서 개별 시트는 불가피하게 주름의 모양과 방향을 따르는 경향이 있습니다. 따라서 주름이 최소한 아주 약간의 곡률을 갖고 가파른 나선형으로 진행되면 코어의 모든 홈이 주름의 곡률을 반복해야 합니다.
특히 전기자의 기계 권선의 경우 홈 형태의 왜곡이 완전히 용인되지 않는 것으로 알려져 있습니다. 앵커가 전기 기계비스듬한 홈이 있어야 주름이 해당 기울기를 가질 수 있습니다. 사실, 예외 없이 전기자와 로터의 모든 디자인에 대해 주름은 가능한 한 직선이어야 하며, 홈의 필요한 경사는 프레싱 장치에서 적절한 경사 가이드 나이프를 사용하여 프레싱 과정에서 얻어집니다.
종종 공장에서 절대적으로 직선형 주름이 있는 샤프트를 제조할 수 있는 능력이 없기 때문에 샤프트에 코어를 고정하는 훨씬 더 비싼 다른 방법, 특히 이러한 목적을 위해 키를 사용해야 합니다.
파형 샤프트용플랫 다이와 프로그레시브 스트로크가 있는 기계를 사용할 필요는 없지만 다른 유형의 스레드 롤링 장비를 성공적으로 사용할 수 있습니다. 널링 후 샤프트는 센터리스 그라인더에서 연삭 작업을 수행합니다. 부분적으로는 세로 방향이지만 주로 가로 방향으로 이송됩니다.
동시에 주름진 표면의 외경도 3단계 정확도 등급 내에서 크기를 유지하기 위해 반드시 연마되어야 하며 개별 톱니의 상단이 다소 둔해짐으로써 동일한 양의 장력과 프레스 연결의 고품질을 보장합니다. .
센터리스 머시닝은 센터 머시닝보다 적은 작업을 필요로 합니다., 특히 모든 조달 작업이 제거됩니다. 즉, 공작물을 자르고 끝을 돌리고 중심을 잡습니다. 이 경우에 사용되는 장비도 생산성이 더 높습니다. 샤프트 터닝용 바 터닝 머신은 멀티 커팅 선반보다 작업자의 유지 관리가 덜 필요합니다. 두 가지 방법으로 얻은 샤프트의 품질은 거의 동일합니다. 길이를 따라 여러 개의 선반이 있는 샤프트의 센터리스 가공을 통해 비트 값을 필요한 공차 내에서 유지할 수 있습니다.
다음 항목에 관심이 있을 수도 있습니다.
혼합 성격 장애: 원인, 증상, 유형 및 치료
GTA 4 컨트롤 설정
GTA 온라인 밀수에 대한 FAQ
LPDFR - 경찰에 오신 것을 환영합니다
Grand Theft Auto San Andreas의 거대한 지도와 그 비밀