Под управлением станком принято понимать совокупность воздействий на его механизмы, обеспечивающих выполнение этими механизмами технологического цикла обработки, а под системой управления - устройство или совокупность устройств, реализующие эти воздействия.
Ручное управление основывается на том, что решение об использовании тех или иных элементов рабочего цикла принимает человек – оператор станка. Оператор на основании принятых решений включает соответствующие механизмы станка и задает параметры их работы.
Операции ручного управления осуществляются как в неавтоматических универсальных и специализированных станках разного назначения, так и в автоматических станках. В автоматических станках ручное управление используется для реализации наладочных режимов и специальных элементов рабочего цикла.
В автоматических станках ручное управление часто сочетается с цифровой индикацией информации, поступающей от датчиков положения исполнительных органов.
Автоматическое управление заключается в том, что решения об использовании элементов рабочего цикла принимает система управления без участия оператора. Она же выдает команды на включение и выключение механизмов станка и управляет его работой.
Циклом обработки называют совокупность перемещения рабочих органов, повторяющихся при обработке каждой заготовки. Комплекс перемещений рабочих органов в цикле работы станка осуществляется в определенной последовательности, т. е. по программе.
Управляющая программа – это совокупность команд, соответствующая заданному алгоритму функционирования станка по обработке конкретной заготовки.
Алгоритмом называют способ достижения цели (решения задачи) с однозначным описанием процедуры его выполнения.
По функциональному назначению автоматическое управление можно разделить следующим образом:
управление неизменными повторяющимися циклами обработки (например, управление агрегатными станками, выполняющими фрезерные, сверлильные, расточные и резьбонарезные операции путем осуществления циклов движения многошпиндельных силовых головок);
управление изменяемыми автоматическими циклами, которые задают в виде индивидуальных для каждого цикла материальных моделей-аналогов (копиров, наборов кулачков, системы упоров и т. д.) Примером циклового управления станков (ЦПУ) являются системы управления копировальных токарных и фрезерных станков, многошпиндельных токарных автоматов и др.;
ЧПУ, при котором программу задают в виде записанного на том или ином носителе массива информации. Управляющая информация для станков с ЧПУ является дискретной, и ее обработка в процессе управления осуществляется цифровыми методами.
Цикловое программное управление (ЦПУ)
Система циклового программного управления (ЦПУ) позволят частично или полностью программировать цикл работы станка, режим обработки и смену инструмента, а также задавать (с помощью предварительного налаживания упоров) величину перемещений исполнительных органов станка. Она является аналоговой системой управления замкнутого типа (рисунок 1) и обладает достаточно высокой гибкостью, т. е. обеспечивает легкое изменение последовательности включения аппаратуры (электрической, гидравлической, пневматической и т. д.), управляющей элементами цикла.
Рисунок 1 – Устройство циклового программного управления
Программатор циклов содержит блок 1 задания программы и блок 2 поэтапного ее ввода (этапом программы называют часть программы, одновременно вводимую в систему управления). Из блока 1 информация поступает в схему автоматики, состоящую из блока 3 управления циклом работы станка и блока 4 преобразования сигналов контроля. Схема автоматики (которую, как правило, выполняют на электромагнитных реле) согласует работу программатора циклов с исполнительными органами станка и датчиком обратной связи; усиливает и размножает команды; может выполнять ряд логических функций (например, обеспечивать выполнение стандартных циклов). Из блока 3 сигнал поступает в исполнительное устройство, обеспечивающее отработку заданных программой команд и включающее в себя исполнительные элементы 5 (приводы исполнительных органов станка, электромагниты, муфты и т. д.). Последние отрабатывают этап программы. Датчик 7 контролирует окончание обработки и через блок 4 дает команду блоку 2 на включение следующего этапа программы. Датчик 7 контролирует окончание обработки и через блок 4 дает команду блоку 2 на включение следующего этапа программы. Для контроля окончания этапа программы часто используют путевые переключатели или реле времени.
В устройствах циклового управления в числовом виде программа содержит информацию только о цикле режимах обработки, а величину перемещения рабочих органов задают настройкой упоров.
Достоинствами системы ЦПУ являются простота конструкции и обслуживания, а также низкая стоимость; недостатком – трудоемкость размерной наладки упоров и кулачков.
Станки с ЦПУ целесообразно применять в условиях серийного, крупносерийного и массового производства деталей простых геометрических форм. Системами ЦПУ оснащают токарно-револьверные, токарно-фрезерные, вертикально-сверлильные станки, агрегатные станки, промышленные роботы (ПР) и др.
Система ЦПУ (рисунок 2) включает в себя программатор циклов, схему автоматики, исполнительное устройство и устройство обратной связи. Собственно устройство ЦПУ состоит из программатора циклов и схемы автоматики.
Рисунок 2 -
На основе достижений кибернетики, электроники, вычислительной техники и приборостроения были разработаны принципиально новые системы программного управления – системы ЧПУ, широко используемые в станкостроении. В этих системах величина каждого хода исполнительного органа станка задается с помощью числа. Каждой единице информации соответствует дискретное перемещение исполнительного органа на определенную величину, называемую разрешающей способностью системы ЧПУ или ценой импульса. В определенных пределах исполнительный орган можно переместить на любую величину, кратную разрешающей способности. Число импульсов, которое нужно подать на вход привода, чтобы осуществить требуемое перемещение L, определяется по формуле N = L/ q , где q – цена импульса. Число N, записанное в определенной системе кодирования на носителе информации (перфоленте, магнитной ленте и др.), является программой, определяющей величину размерной информации.
Под ЧПУ станком понимают управление (по программе, заданной в алфавитно-цифровом коде) движением исполнительных органов станка, скоростью их перемещения, последовательностью цикла обработки, режимом резания и различными вспомогательными функциями.
Система ЧПУ – это совокупность специализированных устройств, методов и средств, необходимых для реализации ЧПУ станком. Устройство ЧПУ (УЧПУ) – часть системы ЧПУ, предназначенная для выдачи управляющих воздействий исполнительным органом станка в соответствии с управляющей программой (УП).
Структурная схема системы ЧПУ представлена на рисунке 3.
Чертеж детали (ЧД), подлежащей обработке на станке с ЧПУ, одновременно поступает в систему подготовки программы (СПП) и систему технологической подготовки (СТП). СТП обеспечивает СПП данными о разрабатываемом технологическом процессе, режиме резания и т. д. На основании этих данных разрабатывается управляющая программа (УП). Наладчики устанавливают на станок приспособления, режущие инструменты согласно документации, разработанной в СТП. Установку заготовки и снятие готовой детали осуществляет оператор или автоматический загрузчик. Считывающее устройство (СУ) считывает информацию с программоносителя. Информация поступает в УЧПУ , оно выдает управляющие команды на целевые механизмы (ЦМ) станка, осуществляющие основные и вспомогательные движения обработки. Датчики обратной связи (ДОС) на основе информации (фактические положения и скорость перемещения исполнительных узлов, фактический размер обрабатываемой поверхности, тепловые и силовые параметры технологической системы и др.) контролируют величину перемещения ЦМ . Станок содержит несколько ЦМ, каждый из которых включает в себя: двигатель (ДВ), являющийся источником энергии; передачу П, служащую для преобразования энергии и ее передачи от двигателя к исполнительному органу (ИО) ; собственно ИО (стол, салазки, суппорт, шпиндель и т. д.), выполняющий координатные перемещения цикла.
Рисунок 3 – Структурная схема системы ЧПУ
Универсальные системы ЧПУ предоставляют пользователю и оператору большие возможности. Они могут быть приспособлены путем программирования к широкому классу объектов, в том числе к разным станкам; обеспечивают при этом все виды интерполяции – линейную, круговую, параболическую и др., а также подготовку и отладку управляющей программы непосредственно у станка в диалоговом режиме. Управляющая программа может храниться в памяти и считываться из нее в процессе обработки, что в ряде случаев позволяет обойтись без предварительного ввода программы путем ее считывания с программоносителя. Системы ЧПУ имеют широкие возможности по редактированию программы, дают возможность автоматической коррекции (из памяти) без использования корректоров пульта. Следует отметить наличие специальных программ диагностики для проверки работы узлов с целью выявления источников неисправности, также возможность сохранения в памяти информации о систематических погрешностях кинематических цепей и исключения или компенсации этих погрешностей при воспроизведении заданного профиля; возможность введения в систему ограничений на зону обработки во избежание брака или поломки станка; возврат в любую точку, в которой был прерван процесс обработки. Универсальные системы ЧПУ работают в линейных и полярных координатах, обеспечивая преобразование координатных осей, например при использовании на горизонтально-фрезерных станках программ, составленных для вертикально-фрезерных станков.
Основным режимом работы устройства ЧПУ - автоматический режим. В процессе автоматической обработки управляющей программы решается широкий круг задач разного уровня сложности: опрос кнопок пульта оператора; распределение и выдача данных для индикации на пульте оператора; вычисление текущего положения по координатам и выдача информации на пульт оператора; расчет циклов обработки; расчет смещения эквидистанты; введение коррекции; компенсация погрешностей; опрос датчиков электроавтоматики; опрос сигналов готовности устройств ввода - вывода; интерполяция; расчет скорости; расчет режимов разгона-торможения; опрос датчиков обратной связи; выдача управляющих воздействий на технологическое оборудование; анализ текущего времени; контроль времени отработки управляющей программы; анализ выполнения программы, содержащейся в данном кадре; подготовка исходной информации для обработки следующего кадра.
Система ЧПУ может видоизменяться в зависимости от вида программоносителя, способа кодирования информации в УП и метода ее передачи в систему ЧПУ.
Числовое программное управление (ЧПУ) – это управление, при котором программу задают в виде записанного на каком – либо носителе массива информации. Управляющая информация для систем ЧПУ является дискретной и ее обработка в процессе управления осуществляется цифровыми методами. Управление технологическими циклами практически повсеместно осуществляется с помощью программируемых логических контроллеров, реализуемых на основе принципов цифровых электронных вычислительных устройств.
Программируемые контроллеры
Программируемый контроллер (ПК ) – это устройство управления электроавтоматикой станка с помощью определенных алгоритмов, реализованных программой, хранящейся в памяти устройства. Программируемый контроллер (командоаппарат) может либо применяться автономно в системе ЦПУ, либо входить в состав общей системы управления (например, системы управления гибкого производственного модуля (ГПМ) ), а также применяться для управления оборудованием автоматических линий и др. Структурная схема приведена на рисунке 4.
Рисунок 4 - Структурная схема программируемого контроллера:
1 – процессор; 2 – таймер и счетчики; 3 – перепрограммируемая память; 4 – оперативная память (ОЗУ); 5 – общая шина связи блоков; 6 – блок связи с устройством ЧПУ или ЭВМ; 7 – блок подключения пульта для программирования; 8 – модули ввода; 9 – коммутатор ввода – вывода; 10 – модули вывода; 11 – пульт программирования с клавиатурой и дисплеем.
Большинство программируемых контролеров имеют модульную конструкцию, в состав которой входят источник питания, процессорный блок и программируемая память, а также различные модули входов / выходов. Модули ввода (входные модули) формируют сигналы, поступающие от разных периферийных устройств (конечных выключателей, электрических аппаратов, тепловых реле и т. п.). Сигналы, поступающие на вход, имеют, как правило, два уровня «О» и»1». Модули вывода (выходные модули) подают сигналы на управляемые исполнительные устройства электроавтоматики станка (контакторы, пускатели, электромагниты, сигнальные лампы, электромагнитные муфты и т. д.). При выходном сигнале «1» соответствующее устройство получает команду на включение, а при выходном сигнале «О» - на выключение.
Процессор с памятью решает логические задачи управления модулями вывода на основании информации, поступающей на модули ввода, и алгоритмов управления, введенных в память. Таймеры настраивают на обеспечение выдержек времени в соответствии с циклами работы ПК. Счетчики также решают задачи реализации цикла работы ПК.
Ввод программы в память процессора и ее отладка выполняются с помощью специального переносно пульта, временно подключаемого к ПК. Этим пультом, представляющим собой устройство записи программы, можно обслуживать поочередно несколько ПК. В процессе записи программы на дисплее пульта отображается текущее состояние управляемого объекта в релейных символах ли условных обозначениях. Ввод программы может также осуществляться через блок связи с устройством ЧПУ или ЭВМ.
Всю программу, хранящуюся в памяти, можно разбить на две части: основную, представляющую собой алгоритм управления объектом, и служебную, обеспечивающую обмен информацией между ПК и управляемым объектом. Обмен информацией между ПК и управляемым объектом состоит в опросе входов (получение информации из управляемого объекта) и переключения выходов (выдача управляющего воздействия в управляемый объект). В соответствии с этим служебная часть программы состоит их двух этапов: опроса входов и переключения выходов.
В программируемых контролерах используют различные типы памяти , в которой хранится программа электроавтоматики станка: электрическую перепрограммируемую энергонезависимую память; оперативную память со свободным доступом; стираемую ультрафиолетовым излучением и электрически перепрограммируемую.
Программируемый контроль имеет систему диагностики: входов / выходов, ошибки в работе процессора, памяти, батареи, связи и других элементов. Для упрощения поиска неисправности современные интеллектуальные модули имеют самодиагностику.
Программируемый логический контроллер (ПЛК) – это микропроцессорная система, предназначенная для реализации алгоритмов логического управления. Контроллер предназначен для замены релейно-контактных схем, собранных на дискретных компонентах – реле, счетчиках, таймерах, элементах жесткой логики.
Современный ПЛК может обрабатывать дискретные и аналоговые сигналы, управлять клапанами, шаговым двигателями, сервоприводами, преобразователями частоты, осуществлять регулирование.
Высокие эксплуатационные характеристики делают целесообразным применение ПЛК везде, где требуется логическая обработка сигналов от датчиков. Применение ПЛК обеспечивает высокую надежность работы оборудования; простое обслуживание устройств управления; ускоренные монтаж и наладка оборудования; быстрое обновление алгоритмов управления (в том числе и на работающем оборудовании).
Кроме прямых выгод от применения ПЛК, обусловленных низкой ценой и высокой надежностью, есть и косвенные: появляется возможность реализовать дополнительные функции, не усложняя и не увеличивая стоимости готовой продукции, которые помогут полнее реализовать возможности оборудования. Большой ассортимент ПЛК дает возможность находить оптимальные решения, как для несложных задач, так и для комплексной автоматизации производства.
Программоносители
Программа работы исполнительных органов станка задается с помощью программоносителя.
Программоноситель – это носитель данных, на котором записана управляющая программа.
Программоноситель может содержать как геометрическую, так и технологическую информацию. Технологическая информация обеспечивает определенный цикл работы станка, содержит данные о последовательности ввода в работу различных инструментов, об изменении режима резания и включении смазочно-охлаждающей жидкости и т.д., а геометрическая – характеризует форму, размеры элементов обрабатываемой заготовки и инструмента и их взаимное положение в пространстве.
Наиболее распространенными программоносителями являются:
перфокарта - изготавливается из картона, имеет форму прямоугольника, один конец которого срезан для ориентации при установке карты в считывающее устройство. Программа записывается пробивкой отверстий на месте соответствующих цифр.
восьмидорожечные перфоленты (рисунок 5) шириной 25,4 мм. Транспортная дорожка 1, служит для перемещения ленты (с помощью барабана) в считывающем устройстве. Рабочие отверстия 2, несущие информацию, пробивают на специальном устройстве, называемом перфоратором. Информацию на перфоленту наносят кадрами, каждый из которых является составной частью УП. В кадре можно записать только такой набор команд, при котором каждому исполнительному органу станка задается не более одной команды (например, в одном кадре нельзя задать движение ИО как вправо, так и влево);
Рисунок 5 - Восьмидорожечная перфолента
1 – кодовые дорожки; 2 – кромка базовая; 3 – номер кодовой дорожки; 4 – порядковый номер бита в кодовой комбинации
магнитная лента – двухслойная композиция, состоящая из пластмассовой основы и рабочего слоя из порошкового ферромагнитного материала. Информация на магнитную ленту записывается в виде магнитных штрихов, наносимых вдоль ленты и располагаемых в кадре УП с определенным шагом, соответствующим заданной скорости ИО. При считывании УП магнитные штрихи преобразуются в управляющие импульсы. Каждому штриху соответствует один импульс. Каждому импульсу соответствует определенное (дискретное) перемещение ИО; длина этого перемещения определяется числом импульсов, содержащихся в кадре магнитной ленты. Такая запись команд на перемещение ИО называется декодированной .
Декодирование осуществляется с помощью интерполятора , который преобразует вводимую в него (на перфоленте или от ЭВМ) кодированную геометрическую информацию о контуре обрабатываемой детали в последовательность управляющих импульсов, соответствующих элементарным перемещениям ИО. Запись декодированной программы на магнитную ленту производят на специальном устройстве, включающем в себя: интерполирующее устройство с выходом, предназначенным для записи; лентопротяжный механизм с магнитными головками для стирания, записи и воспроизведения.
Информацию в декодированном виде записывают, как правило, на магнитную ленту, а в кодированном – на перфоленту или перфокарту. Магнитные ленты применяют в токарных станках с шаговыми двигателями, которым необходим декодированный вид программы.
Интерполяция – это отработка программы движения рабочего органа (инструмента), по контуру обрабатываемой поверхности детали, последовательно отдельными участками (кадрами).
Интерполятор – блок УЧПУ, ответственный за вычисление координат промежуточных точек траектории, которую должен пройти инструмент между точками, заданными в УП. Интерполятор имеет в качестве исходных данных команду УП перемещения инструмента от начальной до конечной точки по контуру в виде отрезка прямой, дуги окружности и т. п.
Для обеспечения точности воспроизведения траектории порядка 1 мкм (точность датчиков положения и точность позиционирования суппорта составляют порядка 1 мкм) интерполятор выдает управляющие импульсы каждые 5…10 мс, что требует от него высокого быстродействия.
С целью упрощения алгоритма работы интерполятора заданные криволинейный контур формируется обычно из отрезков прямых линий или из дуг окружностей, причем часто шаги перемещений по разным осям координат выполняются неодновременно, а поочередно. Тем не менее за счет высокой частоты выдачи управляющих воздействий и инерционности механических узлов привода происходит сглаживание ломанной траектории до плавного криволинейного контура.
Интерполятор , входящий в систему ЧПУ, выполняет следующие функции:
на основе численных параметров участка обрабатываемого контура (координат начальной и конечной точек прямой, величины радиуса дуги и т. д.), заданных УП, рассчитывает (с определенной дискретностью) координаты промежуточных точек этого участка контура;
вырабатывает управляющие электрические импульсы, последовательность которых соответствует перемещению (с требуемой скоростью) исполнительного органа станка по траектории, проходящей через эти точки.
В системах ЧПУ применяют в основном линейные и линейно-круговые интерполяторы; первые обеспечивают перемещение инструмента между соседними опорными точками по прямым линиям, расположенным под любым углом, а вторые - как по прямым линиям, так и по дугам окружностей.
Линейная интерполяция – участки между дискретными координатами представляются прямой линией, расположенной в пространстве в соответствии с траекторией движения режущего инструмента.
Круговая интерполяция – предусматривает представление участка контура обработки в виде дуги соответствующего радиуса. Возможности устройств ЧПУ позволяют обеспечить интерполяцию путем описания участка контура сложным алгебраическим уравнением.
Винтовая интерполяция – винтовая линия складывается из двух видов движений: кругового в одной плоскости и линейного перпендикулярно этой плоскости. В данном случае может программироваться или подача кругового движения, или линейная подача трех используемых координат (осей) станка.
Важнейшей технической характеристикой системы ЧПУ является ее разрешающая способность или дискретность .
Дискретность – это минимально возможная величина перемещения (линейного или углового) исполнительного органа станка, соответствующая одному управляющему импульсу.
Большинство современных систем ЧПУ имеют дискретность 0,01 мм/импульс. Осваиваются в производстве системы с дискретностью 0,001 мм/импульс.
Система ЧПУ практически вытесняют другие типы систем управления.
Классификация систем ЧПУ
По технологическим возможностям и характеру движения рабочих органов системы ЧПУподразделяют на три группы:
Позиционные системы обеспечивают прямолинейное перемещение исполнительного органа станка по одной или двум координатам. Перемещение ИО из позиции в позицию осуществляется с максимальной скоростью, а его подход к заданной позиции – с минимальной («ползучей») скоростью. Такими системами ЧПУ оснащены сверлильные и координатно-расточные станки.
Контурные системы предназначены для выполнения рабочих перемещений по определенной траектории с заданной скоростью согласно программе обработки. Системы ЧПУ, обеспечивающие прямоугольное, прямолинейное и криволинейное формообразование, относятся к контурным (непрерывным) системам, так как они позволяют обработать деталь по контуру. В системах ЧПУ с прямоугольным формообразованием ИО станка перемещается по координатным осям поочередно, поэтому траектория инструмента имеет ступенчатый вид, а каждый элемент этой траектории параллелен координатным осям. Число управляемых координат в таких системах достигает 5 , а число одновременно управляемых координат 4 . В системах ЧПУ с прямолинейным формообразованием различают движение инструмента при резании по двум координатным осям (X и Y). В данных системах используется двухкоординатный интерполятор, выдающий управляющие импульсы сразу на два привода подач. Общее число управляемых координат 2–5. Системы ЧПУ с криволинейным формообразованием позволяют управлять обработкой плоских и объемных деталей, содержащих участки со сложными криволинейными контурами. Контурные системы ЧПУ имеют шаговый двигатель. Такими системами оснащаются токарные, фрезерные, расточные станки.
Комбинированные системы (универсальные) обладают особенностями как позиционных, так и контурных систем и наиболее типичны для многоцелевых станков (сверлильно-фрезерно-расточных).
В станках с системами ЧПУ, управление осуществляется от программоносителя, на котором в числовом виде, занесена геометрическая и технологическая информация.
В отдельную группу выделяют станки с цифровой индикацией и преднабором координат. В этих станках имеется электронное устройство для задания координат нужных точек (преднабор координат) и крестовый стол, снабженный датчиками положения, который дает команды на перемещение до необходимой позиции. При этом на экране высвечивается каждое текущее положение стола (цифровая индикация) . В таких станках можно применять преднабор координат или цифровую индикацию; исходную программу работы задает станочник.
В моделях станков с ПУ для обозначения степени автоматизации добавляется буква Ф с цифрой:
Ф 1 – станки с цифровой индикацией и преднабором координат;
Ф 2 – станки с прямоугольными и позиционными системами ЧПУ;
Ф 3 – станки с контурными прямолинейными и криволинейными системами ЧПУ;
Ф 4 – станки с универсальной системой ЧПУ для позиционно - контурной обработки.
Кроме того, к обозначению модели станка с ЧПУ могут прибавляться приставки С1, С2, С3, С4 и С5, что указывает на различные модели систем ЧПУ, применяемых в станках, а также на различные технологические возможности станков. Например, станок модели 16К20Ф3С1 оснащен системой ЧПУ «Контур 2ПТ-71», станок модели 16К20Ф3С4 – системой ЧПУ ЭМ907 и т. д.
Для станков с цикловыми системами ПУ в обозначении модели введен индекс Ц , с оперативными системами – индекс Т (например, 16К20Т1). ЧПУ обеспечивает управление движение рабочих органов станка и скоростью их перемещения при формообразовании, а также последовательностью цикла обработки, режима резанья, различными вспомогательными функциями.
Для характеристики станков с ЧПУ используют следующие показатели:
Класс точности : Н – нормальной точности, П – повышенной точности, В – высокой точности, А – особо высокой точности, С – сверхвысокой точности (мастер-станки);
Технологические операции , выполняемые на станке : точение, сверление, фрезерование, шлифование и т. д.;
Основные параметры станка : для патронных станков – наибольший диаметр устанавливаемого изделия над станиной; для центровых и патронных станков – наибольший диаметр обрабатываемого изделия над суппортом; для прутково-токарных станков – наибольший диаметр обрабатываемого прутка; для фрезерно-расточных станков – габаритные размеры (длина, ширина) рабочей поверхности стола, диаметр рабочей поверхности круглого поворотного стола; для сверлильных станков – наибольший диаметр сверления, диаметр выдвигаемого шпинделя и т. д.;
Величины перемещений рабочих органов станка – суппорта по двум координатам, стола по двум координатам, шпиндельного узла по линейной и угловой координатам и т. д.;
Величина дискретности (цена деления) минимальное задание перемещения по программе (шаг);
Точность и повторяемость позиционирования по управляемым координатам ;
Привод главного движения – тип, номинальное и максимальное значения мощности, пределы скоростей вращения шпинделя (ступенчатое или бесступенчатое), число рабочих скоростей, число автоматически переключаемых скоростей;
Привод подачи станка – координата, тип, номинальный и максимальный моменты, пределы скоростей рабочих подач и число скоростей рабочих подач, скорость быстрого перемещения;
Число инструментов – в резцедержателе, револьверной головке, инструментальном магазине;
Вид смены инструмента – автоматический, ручной;
Габаритные размеры станка и его масса .
По способу подготовки и ввода управляющей программы различают:
оперативные системы ЧПУ (в этом случае управляющую программу готовят и редактируют непосредственно на станке, в процессе обработки первой детали из партии или имитации ее обработки);
адаптивные системы , для которых управляющая программа готовится, независимо от места обработки детали. Причем независимая подготовка управляющей программы может выполняться либо с помощью средств вычислительной техники, входящих в состав системы ЧПУ данного станка, либо вне ее (вручную или с помощью системы автоматизации программирования.)
По уровню технических возможностей в международной практике приняты следующие обозначения числовых систем программного управления:
NC (Computer Numerical Control) - ЧПУ;
HNC (Hand Numerical Control) – разновидность устройства ЧПУ с заданием программы обработки оператором с пульта с помощью клавиш, переключателей и т. д.;
SNC (Speiher Numerical Control) – устройство ЧПУ, имеющее память для хранения всей управляющей программы (программа хранится во внутренней памяти);
CNC – устройство ЧПУ позволяет управлять одним станком с ЧПУ; устройство соответствует структуре управляющей мини – ЭВМ или процессора; расширяет функциональные возможности программного управления, появляется возможность хранения УП и ее редактирование на рабочем месте, диалоговое общение с оператором, широкие возможности коррекции, возможность изменения программы при ее эксплуатации и др.;
DNC (Direct Numerical Control)– системы более высокого уровня, обеспечивающие: управление сразу группой станков от общей ЭВМ; хранение в памяти весьма значительного количества программ; взаимодействие со вспомогательными системами ГПС (транспортирования, складирования); выбор времени начала обработки той или иной детали; учет времени работы и простоев оборудования и т. д.
По числу потоков информации системы ЧПУ делятся на замкнутые, разомкнутые и адаптивные.
Разомкнутые системы характеризуются наличием одного потока информации, поступающего со считывающего устройства к исполнительному органу станка. В механизмах таких систем используют шаговые двигатели. Он является задающим устройством, сигналы которого усиливаются различными способами, например, с помощью гидроусилителя моментов, вал которого связан с ходовым винтом привода подач. В разомкнутой системе нет датчика обратной связи и поэтому отсутствует информация о действительном положении исполнительных органов станка.
Замкнутые системы ЧПУ характеризуются двумя потоками информации – от считывающего устройства и от датчика обратной связи по пути. В этих системах рассогласование между заданными и действительными величинами перемещений исполнительных органов устраняется благодаря наличию обратной связи.
Адаптивные системы ЧПУ характеризуются тремя потоками информации: 1) от считывающего устройства; 2) от датчика обратной связи по пути; 3) от датчиков, установленных на станке и контролирующих процесс обработки по таким параметрам, как износ режущего инструмента, изменение сил резания и трения, колебания припуска и твердости материала обрабатываемой заготовки и др. Такие программы позволяют корректировать программу обработки с учетом реальных условий резания.
Использование конкретного вида оборудования с ЧПУ зависит от сложности изготовляемой детали и серийности производства. Чем меньше серийность производство, тем большую технологическую гибкость должен иметь станок.
При изготовлении деталей со сложными пространственными профилями в единичном мелкосерийном производстве использование станков с ЧПУ является почти единственным технически оправданным решением. Это оборудование целесообразно применять и в случае, если не возможно быстро изготовить оснастку. В серийном производстве также целесообразно использовать станки с ЧПУ. В последнее время широко используют автономные станки с ЧПУ или системы из таких станков в условиях переналаживаемого крупносерийного производства.
Принципиальная особенность станка с ЧПУ – это работа по управляющей программе (УП), на которой записаны цикл работы оборудования для обработки конкретной детали и технологические режимы. При изменении обрабатываемой на станке детали необходимо просто сменить программу, что сокращает на 80…90% трудоемкость переналадки по сравнению с трудоемкостью этой операции на станках с ручным управлением.
Основные преимущества станков с ЧПУ:
производительность станка повышается в 1,5….2,5 раза по сравнению с производительностью аналогичных станков с ручным управлением;
сочетается гибкость универсального оборудования с точностью и производительностью станка – автомата;
снижается потребность в квалифицированных рабочих – станочниках, а подготовка производства переносится в сферу инженерного труда;
детали, изготовленные по одной программе. Являются взаимозаменяемыми, что сокращает время пригоночных работ в процессе сборки;
сокращаются сроки подготовки и перехода на изготовление новых деталей, благодаря предварительной подготовки программ, более простой и универсальной технологической оснастки;
снижается продолжительность цикла изготовления деталей и уменьшается запас не завершенного производства.
Контрольные вопросы:
Что такое программное управление станками? Какие виды ПУ станками вы знаете?
Что обозначают станки с ЦПУ?
Что такое система ЧПУ станком? Какие системы ЧПУ вы знаете?
В чем заключается принципиальная особенность станков с ЧПУ?
Перечислите основные преимущества применения станков с ЧПУ?
Оси координат и структуры движений станков с ЧПУ
Для всех станков ЧПУ применяют единую систему обозначений координат, рекомендованную стандартом ISO – R841: 1974. Координатами обозначают положение оси вращения шпинделя станка или заготовки, а также прямолинейные или круговые движения подачи инструмента или заготовки. При этом обозначение осей координат и направление движений в станках устанавливают так, чтобы программирование операций обработки не зависело от того, перемещается инструмент либо заготовка или нет. За основу принимается перемещение инструмента относительно системы координат неподвижной заготовки.
Стандартная система координат представляет собой правую прямоугольную систему, связанную с заготовкой, оси которой параллельны прямолинейным направляющим станка.
Все прямолинейные перемещения рассматриваются в системе координат X , Y , Z . Круговое движение по отношению к каждой из координатных осей обозначают прописными буквами латинского алфавита: А, В, С (рисунок 6).Во всех станках ось Z совпадает с осью шпинделя главного движения, т. е. шпинделя, вращающего инструмент (в станках сверильно-фрезерно-расточной группы), или шпинделя, вращающего заготовку (в станках токарной группы). При наличии нескольких шпинделей в качестве основного выбирают шпиндель перпендикулярный к рабочей поверхности стола, на котором крепится заготовка.
Рисунок 6 - Стандартная система координат в станках с ЧПУ
Движение по оси Z в положительном направлении должно соответствовать направлению отвода инструмента от заготовки . На сверлильных и расточных станках обработка происходит при перемещении инструмента в отрицательном направлении по оси Z.
Ось X должна располагаться предпочтительно горизонтально и параллельно поверхности крепления заготовки. На станках с вращающейся заготовкой (токарные) движение по оси X направлено по радиусу заготовки и параллельно поперечным направляющим. Положительное движение по оси X происходит, когда инструмент , установленный в главном резцедержателе поперечных салазок, отходит от оси вращения заготовки.
На станках с вращающимся инструментом (фрезерные, сверлильные) при горизонтальном расположении оси Z положительное перемещение по оси X направлено вправо, если смотреть от основного инструментального шпинделя в сторону изделия. При вертикальном расположении оси Z положительное перемещение по оси X вправо для одностоечных станков, а для двухстоечных – от основного инструментального шпинделя на левую стойку.
Положительное направление по оси Y следует выбирать так, чтобы ось Y вместе с осями Z и X образовала правую прямоугольную систему координат. Для этого использую правило правой руки: большой палец – ось X, указательный – ось Y, средний - ось Z (рисунок).
Если дополнительно к основным (первичным) прямолинейным движениям по осям X, Y и Z имеются вторичные движения, параллельные им, то они обозначаются соответственно U, V, W. В случае, если имеются третичные движения, их обозначают P, Q и R.
Первичные, вторичные и третичные движения рабочих органов станка определяются в зависимости от удаленности этих органов от основного шпинделя.
Вторичные вращательные движения, параллельные или не параллельные осям А, В и С, обозначаются D или E.
Способы и начало отсчета координат
При настройке станка с ЧПУ каждый исполнительный орган устанавливается в некоторое исходное положение, из которого он перемещается при обработке заготовки на строго определенные расстояния. Благодаря этому инструмент проходит через заданные опорные точки траектории. Величины и направления перемещений исполнительного органа из одного положения в другое задаются в УП и могут выполняться на станке по-разному в зависимости от конструкции станка и системы ЧПУ. В современных станках с ЧПУ применяются два способа отсчета перемещений: абсолютный и относительный (в приращениях).
Абсолютный способ отсчета координат – положение начала координат фиксировано (неподвижно) для всей программы обработки заготовки. При составлении программы записываются абсолютные значения координат последовательно расположенных точек, заданных от начала координат. При обработке программы координаты каждый раз отсчитываются от этого начала, что исключает накапливание погрешности перемещений в процессе обработки программы.
Относительный способ отсчета координат – за нулевое положение каждый раз принимается положение исполнительного органа, которое он занимает перед началом перемещения к следующей опорной точке. В этом случае в программу записываются приращения координат для последовательного перемещения инструмента от точки к точке. Этот способ отсчета используется в контурных системах ЧПУ. Точность позиционирования исполнительного органа в данной опорной точке определяется точностью обработки координат всех предыдущих опорных точек, начиная от исходной, что приводит к накапливанию погрешностей перемещения в процессе обработки программы.
Для удобства программирования и настройки станков с ЧПУ начало координат в ряде случаев может быть выбрано в любом месте в пределах ходов исполнительных органов. Такое начало координат называется «плавающим нулем» и используется в основном на сверлильных и расточных станках, оснащенных позиционными системами ЧПУ.
Разработка управляющих программ
При разработке управляющей программы необходимо:
спроектировать маршрутную технологию обработки в виде последовательности операций с выбором режущих и вспомогательных инструментов и приспособлений;
разработать операционную технологию с расчетом режимов резания и определением траекторий движения режущих инструментов;
определить координаты опорных точек для траекторий движения режущих инструментов;
составить расчетно-технологическую карту и карту наладки станка;
закодировать информацию;
нанести информацию на программоноситель и переслать в память устройства ЧПУ станка или вручную набрать на пульте устройства ЧПУ;
проконтролировать и при необходимости исправить программу.
Для программирования необходим чертеж детали, руководство по эксплуатации станка, инструкция по программированию, каталог режущих инструментов и нормативы режимов резания.
Согласно ГОСТ20999-83 запись элементов программы производится в определенном порядке в виде последовательности кадров и с использованием соответствующих символов (см. таблицу 1).
Таблица 1 Значения управляющих символов и знаков
Символ |
Значение |
Угол поворота вокруг оси X |
|
Угол поворота вокруг оси Y |
|
Угол поворота вокруг оси Z |
|
Вторая функция инструмента |
|
Вторая функция подачи |
|
Первая функция (скорость) подачи |
|
Подготовительная функция |
|
Коррекция длины инструмента |
|
Параметр угловой интерполяции или шаг резьбы параллельно оси X |
|
Параметр угловой интерполяции или шаг резьбы параллельно оси Y |
|
Параметр угловой интерполяции или шаг резьбы параллельно оси Z |
|
Вспомогательная функция |
|
Номер кадра |
|
Третичная длина перемещения, параллельного оси X |
|
Третичная длина перемещения, параллельного оси Y |
|
Перемещение на быстром ходу по оси Z или третичная длина перемещения, параллельного оси Z |
|
Функция (скорость) главного движения |
|
Первая функция инструмента |
|
Вторичная длина перемещения, параллельно оси X |
|
Вторичная длина перемещения, параллельно оси Y |
|
Вторичная длина перемещения, параллельно оси Z |
|
Первичная длина перемещения, параллельно оси X |
|
Первичная длина перемещения, параллельно оси Y |
|
Первичная длина перемещения, параллельно оси Z |
|
Символ, обозначающий конец кадра управляющей программы |
|
Знак, обозначающий начало управляющей программы |
|
Математический знак |
|
Математический знак |
|
Десятичный знак |
Кадр программы (фраза) - последовательность слов, расположенных в определенном порядке и несущих информацию об одной технологической рабочей операции (рисунок 8).
Слово программы – последовательность символов, находящихся в определенной связи как единое целое.
Рисунок 8 – Кадр программы
Каждый кадр управляющей программы должен содержать:
слово «Номер кадра»;
информационные слова или слово (допускается не использовать);
символ «Конец кадра»;
символ табуляции (допускается не применять). При использовании этих символа они проставляются перед каждым словом в кадре УП, кроме слова «Номер кадра».
слово (или слова) «Подготовительная функция»;
слова «Размерные перемещения», которые рекомендуется записывать в следующей последовательности символов: X, Y, Z, U, V, W, Р, Q, R, A, B, C;
слова «Параметр интерполяции» или «Шаг резьбы» I, J, K;
слово (или слова) «Функция подачи», которые относятся только к определенной оси и должны следовать непосредственно за словами «Размерное перемещение» по этой оси; слово «Функция подачи», относящееся к двум и более осям, должно следовать за словом «Размерное перемещение»;
слово «Функция главного движения»;
слово (или слова) «Функция инструмента»;
слово (или слова) «Вспомогательная функция».
Порядок и кратность записи слов с адресами D, E, H, U, V, W, P, Q, R, используемых в значениях отличных от принятых, указывают в форме конкретного устройства ЧПУ.
В пределах одного кадра УП не должны повторяться слова «Размерные перемещения» и «Параметр интерполяции» или «Шаг резьбы»; не должны использоваться слова «Подготовительная функция», входящие в одну группу.
После символа «Главный кадр» (:) в УП должна быть записана вся информация, необходимая для начала или возобновления обработки. Этот символ используется для определения начала программы на носителе данных.
Каждое слово в кадре УП должно состоять из символа адреса (прописная буква латинского алфавита согласно таблице), математического знака «+» или «-« (при необходимости), последовательности цифр.
Слова в УП могут быть записаны одним из двух способов: без использования десятичного знака (подразумевается положение десятичной запятой) и с его использованием (явное положение десятичной запятой). Явная десятичная запятая обозначается символом «DS». Подразумеваемое положение десятичной запятой должно быть определено в характеристиках конкретного устройства ЧПУ.
При записи слов с использованием десятичного знака слова, в которых десятичный знак отсутствует, должны рассматриваться устройством ЧПУ как целые числа. В этом случае могут быть опущены незначащие нули, стоящие до и (или) после знака: Х.03 означает размер 0,03 мм по оси Х; Х1030 – размер 1030,0 мм по оси Х.
В настоящее время при программировании чаще используется адресный способ записи информации на перфоленту. Информация каждого кадра делится на два вида: 1) буква (адрес), обозначает исполнительный орган системы ЧПУ (или станка), которому подается команда; 2) число, следующее за адресом и обозначающее величину перемещения исполнительного органа станка (со знаком «+» или «-») или кодовую запись (например, величина подачи и т. д.). Буква и следующее за ней число являются словом. Кадр программы состоит из одного, двух или нескольких слов.
Кодированная запись ряда кадров УП для обработки заготовки на токарном станке может иметь следующий вид:
№ 003 X +000000 - перемещение резца в нулевую точку по оси Х;
№ 004 Z +000000 - перемещение резца в нулевую точку по оси Z;
№ 005 G26 - команда на работу в приращения
№ 006 G10 X -006000 - G10 -линейная интерполяция (прямолинейная
траектория перемещения)
№ 007 X -014000 F10080
№ 008 Z +000500 F10600
№ 009 X +009500 F70000
№ 010 X +002000 Z -001000 F10100
………………………………………………………..
…………………………………………………………….
№………М102
Цифры после букв определяют число разрядов числовой части данного слова. В скобках адресов X,Z,I,K указаны возможные разряды чисел, выражающих геометрическую информацию при различных режимах работы УЧПУ. Эта информация записывается в виде числа импульсов (число миллиметров перемещения ИО, деленное на величину дискретности их обработки).
Слово (или слова) «Подготовительная функция» должно быть выражено кодовым символом в соответствии с таблицей 2 .
Таблица 2 - Подготовительные функции
Обозначение функции |
Значение функции |
Позиционирование. Перемещение на быстром ходу в заданную точку. Ранее заданная рабочая подача не отменяется |
|
Линейная интерполяция. Перемещение с запрограммированной подачей по прямой к точке |
|
Круговая интерполяция соответственно по ходу и против хода часовой стрелки |
|
Задержка в обработке на определенное время, которое задается с пульта управления или в кадре |
|
Временный останов. Длительность останова не ограничена. В работу станок включается нажатием кнопки |
|
Параболическая интерполяция. Движение по параболе с запрограммированной подачей |
|
Разгон. Плавное увеличение скорости подачи до запрограммированного его значения в начале движения |
|
Торможение в конце кадра. Плавное уменьшение скорости подачи до фиксированного значения |
|
Плоскости интерполяции соответственно XY,XZ,YZ |
|
Нарезание резьбы соответственно с постоянным, увеличивающимся и уменьшающимся шагом |
|
Отмена коррекции инструмента, заданного одной из функций G41- G52 |
|
Коррекция диаметра или радиуса инструмента при контурном управлении. Режущий инструмент расположен соответственно слева и справа от детали |
|
Коррекция диаметра или радиуса инструмента соответственно положительная и отрицательная |
|
Коррекция диаметра или радиуса инструмента при прямолинейном формообразовании:G45+/+,G46+/-,G47-/-,G48-/+,G49 0/+,G50 0/-,G51 +/0, |
|
Отмена линейного сдвига, заданного одной из функций G54-G59 |
|
Линейный сдвиг по координатам X,Y,Z и в плоскостях XY,XZ,YZ соответственно |
|
Нарезание резьбы метчиком |
|
Отмена постоянного цикла, заданного одной из функций G81-G89 |
|
Постоянные циклы |
|
Абсолютный размер. Отсчет перемещений в абсолютной системе координат с началом в нулевой точке системы ЧПУ |
|
Размер в приращениях. Отсчет перемещений относительно предыдущей запрограммированной точки |
|
Установка абсолютных накопителей положения |
|
Скорость подачи в функции, обратной времени |
|
Единица подачи соответственно в минуту и на оборот |
|
Единица скорости резания (м/мин) |
|
Единица главного движения (об/мин) |
Примечание: G07,G10-G16,G20,G32,G36-G39,G60-G62,G64-G79,G98,G99 – резервные коды.
Все размерные перемещения должны задаваться в абсолютных значениях или приращениях. Способ управления должен выбираться одной из подготовительных функций : G90 (абсолютный размер) или G91 (размер в приращениях ).
За адресом каждого слова «Размерное перемещение» следует две цифры, первая из которых показывает количество разрядов перед подразумеваемой десятичной запятой, отделяющей целую часть числа от дробной, вторая – количество разрядов после запятой. Если можно опустить нули, стоящие перед первой значащей цифрой и после последней в словах «Размерные перемещения», за адресом «Размерное перемещение» должны следовать три цифры. Если опускаются нули, стоящие перед первой значащей цифрой, то нулем должна быть первая цифра. Если опускаются нули, стоящие после значащей цифры, нулем должна быть последняя цифра.
Все линейные перемещения должны быть выражены в миллиметрах и их десятичных долях. Все угловые размеры даются в радианах или градусах. Допускается выражение угловых размеров в десятичных долях оборота.
Если устройство ЧПУ допускает задание размеров в абсолютных значениях (положительных или отрицательных) в зависимости от начала системы координат, то математический знак («+» или «-») является составной частью слова «Размерное перемещение» и должен предшествовать первой цифре каждого размера.
Если абсолютные размеры всегда положительны, то между адресом и следующим за ним числом не ставят никакого знака, а если они либо положительны, либо отрицательны, то знак ставится.
Если устройство ЧПУ допускает задание размеров в приращениях, то математический знак должен предшествовать первой цифре каждого размера, указывая направление перемещения.
Движение инструмента по сложной траектории обеспечивается специальным устройством – интерполятором. Интерполяция линейных и дуговых отрезков производится отдельно по участкам заданной траектории. Каждый из участков может быть записан в одном или нескольких кадрах управляющей программы.
Функциональный характер интерполируемого участка траектории (прямая, окружность, парабола или кривая более высокого порядка) определяется соответствующей подготовительной функцией (G01 – G03, G06). Для задания параметров интерполяции применяют адреса I, J, K, используя их для определения геометрических характеристик кривых (например, центра дуги окружности, радиусов, углов и т. п.). Если вместе с параметрами интерполяции необходимо записать математический знак («+» или «-»), он должен следовать за адресным символом и перед цифровыми символами. Если знак отсутствует, то подразумевается знак «+».
Начальная точка каждого участка интерполяции совпадает с конечной точкой предыдущего участка, поэтому в новом кадре она не повторяется. Каждой последующей точке, лежащей на этом участке интерполяции и имеющей определенные координаты, соответствует отдельный кадр информации с адресами перемещений X, Y или Z .
Современные устройства ЧПУ в своем программном обеспечении имеют «встроенные» функции для выполнения простейшей интерполяции. Так, в токарных станках с ЧПУ фаска под углом 45° задается адресом С со знаком и конечным размером по той координате, по которой идет обработка детали перед фаской. Знак под адресом С должен совпадать со знаком обработки по координате X (рисунок,а). Направление по координате Z задается только в отрицательную сторону.
Для задания дуги указываются координаты конечной точки дуги и радиус под адресом R с положительным знаком при обработке по ходу часовой стрелки и отрицательным при обработке против хода часовой стрелки (рисунок 9).
Рисунок 9 - Программирование фасок (а) и дуги (б) на токарном станке с ЧПУ
Подача и скорость главного движения кодируются числами, количество разрядов которых указано в формате конкретного устройства ЧПУ. Выбор типа подачи G93 (подача в функции, обратной времени), G94 (подача в минуту), G95 (подача на оборот).
Выбор типа главного движения должен осуществляться одной из подготовительных функций: G96 (постоянная скорость резания) или G97 (обороты в минуту).
В качестве основного метода кодирования подачи используется метод прямого обозначения, при котором должны применяться следующие единицы: миллиметр в минуту – подача не зависит от скорости главного движения; миллиметр на оборот – подача зависит от скорости главного движения; радиан в секунду (градус в минуту) – подача относится только к круговому перемещению. При прямом кодировании скорости главного движения число обозначает угловую скорость шпинделя (радианах в секунду или оборотах в минуту) либо скорость резания (в метрах в минуту). Например, если в программе частота вращения шпинделя задана как S – 1000, это означает, что шпиндель вращается по ходу часовой стрелки с частотой вращения 1000 об/мин. (Если минус отсутствует, значит, вращение шпинделя происходит против часовой стрелки).
Слово «Функция инструмента» используется для выбора инструмента . Допускается применять его для коррекции (или компенсации) инструмента. В этом случае слово «Функция инструмента» будет состоять из двух групп цифр. Первая группа используется для выбора инструмента, вторая – для коррекции. Если для записи коррекции (компенсации) инструмента используется другой адрес, рекомендуется использовать символ D или H.
Количество цифр, следующих за адресами T, D и H , указывается в формате конкретного устройства ЧПУ.
Слово (или слова) «Вспомогательная функция» выражается кодовым числом в соответствии с таблицей 3.
Таблица 3 - Вспомогательные функции
Обозначение функции |
Значение функции |
Программируемый останов. Останов шпинделя, подачи и выключение охлаждения |
|
Останов с подтверждением. То же, что М 00, но выполняется при предварительном нажатии соответствующей кнопки на пульте оператора |
|
Конец программы. Останов шпинделя и выключение подачи СОЖ |
|
Вращение шпинделя соответственно по ходу и против хода часовой стрелки |
|
Останов шпинделя наиболее эффективным способом |
|
Смена инструмента. Команда на смену инструмента подается вручную или автоматически |
|
Включение охлаждения соответственно №2 и №1 |
|
Выключение охлаждения. Отменяет команды М07, М08, М50, М51 |
|
Зажим и разжим. Относится к зажимным приспособлениям столов станка, заготовки и т. д. |
|
Вращение шпинделя по ходу и против часовой стрелки при одновременном включении охлаждения |
|
Быстрое перемещение в «+» и «-» |
|
Конец программы для устройства ЧПУ со встроенной памятью |
|
Останов шпинделя в определенном угловом положении |
|
Конец программы, которой является многократно считываемая глава программы |
|
Конец информации |
|
Обход блокировки. Команда на временную отмену блокировки |
|
Диапазон подач соответственно №1 и №2 |
|
Диапазон вращения шпинделя соответственно №1 и №2 |
|
Отмена М 49 |
|
Отмена ручной коррекции |
|
Выключение охлаждения соответственно №3 и №4 |
|
Линейное смещение инструмента в положении №1 и №2 соответственно |
|
Отмена М 59 |
|
Постоянная скорость шпинделя |
|
Смена заготовки |
|
Линейное смещение заготовки в фиксированное положение 31 и №2 соответственно |
|
Зажим и отжим заготовки |
|
Зажим и отжим стола |
Значение шага резьбы должно быть выражено в миллиметрах на один оборот шпинделя. Количество цифр в словах, задающих шаг резьбы, определено в формате конкретного устройства ЧПУ. При нарезании резьбы с переменным шагом слова под адресами I и K должны задавать размеры начального шага резьбы.
Слово «Функция подачи» при постоянном шаге резьбы программироваться не должно.
Каждая управляющая программа должна начинаться символом «Начало программы», после которого должен стоять символ «Конец кадра», а затем кадр с соответствующим номером. Если необходимо обозначить управляющую программу, это обозначение (номер) должно находиться непосредственно за символом «Начало программы» перед символом «Конец кадра».
Управляющая программа должна заканчиваться символом «Конец программы» или «Конец информации». Информация, помещенная после символа «Конец информации», не воспринимается устройством ЧПУ. Перед символом «Начало программы» и после символа «Конец программы» и «Конец информации» на перфоленте рекомендуется оставлять участки с символом ПУС («Пусто»).
Отладка и корректирование программы
При подготовке управляющей программы важным моментом является разработка траектории движения режущих инструментов относительно детали и на этой основе – описание движений соответствующих органов станка. Для этого используется несколько систем координат.
Главная расчетная система – система координат станка , в которой определяются предельные перемещения и положения его рабочих органов. Эти положения характеризуются базовыми точками , которые выбираются в зависимости от конструкции станка. Например , для шпиндельного узла базовой точкой является точка пересечения торца шпинделя с осью его вращения, для крестового стола – точка пересечения его диагоналей, для поворотного стола – центр поворота на зеркале стола и т. д. Положение осей и их направления в стандартной системе координат рассмотрены выше.
Начало стандартной системы координат обычно совмещается с базовой точкой узла, несущего заготовку. При этом узел фиксируется в таком положении, при котором все перемещения рабочих органов станка происходят в положительном направлении (рисунок 10). От этой базовой точки, называемой нулем станка , определяется положение рабочих органов, если информация об их положении потеряна (например, вследствие аварийного выключения электроэнергии). В нуль станка рабочие органы перемещаются при нажатии соответствующих кнопок на пульте управления или с помощью команд управляющей программы. Точный останов рабочих органов в нулевом положении по каждой из координат обеспечивается датчиками нулевого положения. Например, при токарной обработке, нуль станка во избежание аварии устанавливается со смещением.
Система координат детали с базовой точкой, рассматривается при закреплении заготовки на станке, для определения положения этой системы и системы координат станка относительно друг друга (рисунок 9). Иногда такая связь осуществляется при использовании базовой точки крепежного приспособления.
Система координат инструмента предназначена для задания положения его рабочей части относительно узла крепления. Инструмент описывается в рабочем положении в сборе с державкой. При этом оси системы координат инструмента параллельны соответствующим осям стандартной системы координат станка и направлены в ту же сторону. За начало системы координат инструмента принимают базовую точку инструментального блока , выбираемую с учетом особенностей его установки на станке.
Положение вершины инструмента задается радиусом r и координатами X и Z ее настроечной точки. Эта точка обычно используется при определении траектории, элементы которой параллельны координатным осям. При криволинейной траектории за расчетную точку принимают центр закругления при вершине инструмента. Связь между системами координат станка, детали и инструмента легко проследить по рисунку 9.
Рисунок 9 - Системы координат детали при обработке на фрезерном (а) и токарном (б) станках ЧПУ
При разработке управляющей программы и обработке детали используют систему координат программы . Её оси параллельны осям координат станка и так же направлены.
Начало координат (исходная точка станка) выбирают исходя из удобства отсчета размеров. Чтобы избежать значительных холостых ходов, исходное положение, от которого начинается обработка и в котором производится смена инструментов и заготовок, задается так, чтобы инструменты находились по возможности ближе к обрабатываемой детали.
Для «привязки» в пространстве системы измерения перемещений станка используется нулевая (базовая) точка отсчета. При каждом включении станка эта точка «привязывает» измерительную систему к нулевой точке станка.
При смене режущих инструментов в ходе обработки деталей может возникнуть несоответствие результатов обработки требованиям к ней (потеря точности, возрастание шероховатости, появление вибраций и т. д.). В этом случае необходимо оперативно откорректировать программу. Погрешности обработки, требующие коррекции, могут возникнуть при сверлении отверстий, точении конических и фасонных поверхностей вследствие наличия у резцов радиуса вершины.
Возможны две разновидности коррекции – на длину и на радиус инструмента.
В первом случае коррекция длины сверла или вылета державки резца осуществляется с помощью команды Н с набором цифр, соответствующих величине коррекции. Например, кадр N 060 T 02 H 15
Означает введение коррекции на длину 15 мм для инструмента № 2.
Второй случай обеспечивает коррекцию радиуса инструмента и связан с тем, что при точении конических и фасонных поверхностей при фрезеровании контуров траектория движения центра радиусной поверхности инструмента должна представлять собой эквидистанту относительно формы поверхности (рисунок 11).
Приведем фрагмент программы для компенсации радиуса резца:
N 035 G 81 X +25 Z +4 I +7 ………………………………………………………. Описание контура обработки ………………………………………………………. |
Рисунок 11 - Компенсация радиуса резца |
Фрагмент программы, предусматривающий фрезерование по эквидистанте (рисунок 12)
N 005 G 90 G 00 X 0 Y 0 S 1000 T01 M 03
N 006 G 41 G 01 X 220 Y 100 F 100
N 007 X 220 Y 430 F 50
N 008 G 02 G 17 X 370 Y 580 I 370 J 430
N 009 G 01 X 705 Y 580
N 010 X 480 Y 190
N 011 X 220 Y 190
N 012 G 00 X 0 Y 0 05M
Функция G 41 (коррекция диаметра фрезы, если фреза находится слева от детали) в кадре N 006 обеспечивает движение центра фрезы по эквидистанте относительно обрабатываемой поверхности.
В ряде случаев требуется скорректировать подачу, чтобы уменьшить шероховатость обрабатываемой поверхности, исключить вибрации и т. д. Для этого на пульте управления необходимо установить новое значение подачи и ввести его в память устройства ЧПУ.
Рисунок 12 - Движение фрезы по эквидистанте при фрезеровании наружного контура
Конструктивные особенности станков с ЧПУ.
Станки с ЧПУ имеют расширенные технологические возможности при сохранении высокой надежности работы. Конструкция станков с ЧПУ должна, как правило, обеспечить совмещение различных видов обработки (точение - фрезерование, фрезерование – шлифование), удобство загрузки заготовок, выгрузки деталей (что особенно важно при использовании промышленных роботов), автоматическое или дистанционное управление сменной инструмента и т. д.
Повышение точности обработки достигается высокой точностью изготовления и жесткостью станка, превышающей жесткость обычного станка того же назначения. Для чего производят сокращения длины его кинематических цепей: променяют автономные приводы, по возможности сокращают число механических передач. Приводы станков с ЧПУ должны также обеспечивать высокое быстродействие.
Повышению точности способствует и устранение зазоров в передаточных механизмов приводов подач, снижение потерь на трение направляющих и др. механизмов. Повышение виброустойчивости, снижение тепловых деформаций, применение в станках датчиков обратной связи. Для уменьшения тепловых деформаций необходимо обеспечить равномерный температурный режим в механизмах станка, чему, например, способствует предварительный разогрев станка и его гидравлической системы. Температурную погрешность станка можно также уменьшить, водя коррекцию в привод подач от сигналов датчиков температура.
Базовые детали (станины, колонны, основания) выполняют более жесткими за счет введения дополнительных ребер жесткости. Повышенную жесткость имеют и подвижные несущие элементы (суппорты, столы, салазки). Столы, например, конструируют коробчатой формы с продольными и поперечными формами. Базовые детали изготовляют литыми или сварными. Наметилась тенденция выполнять такие детали из полимерного бетона или синтетического гранита, что в еще большей степени повышает жесткость и виброустойчивости станка.
Направляющие станков с ЧПУ имеет высокую износостойкость и малую силу трения, что позволяет снизить мощность следящего привода, увеличить точность перемещений, уменьшить рассогласование следящей системе.
Направляющие скольжения станины и суппорта для уменьшения коэффициента трения создают в виде пары скольжения « сталь (или высококачественный чугун) – пластиковое покрытие (фторопласт и др.)»
Направляющие качения имеют высокую долговечность, характеризуются небольшим трением, причем коэффициент трения практически не зависит от скорости движения. В качестве тел качения используют ролики. Предварительный натяг повышает жесткость направляющих в 2 ..3 раза, для создания натяга используют регулирующие устройства.
Приводы и преобразователи для станков с ЧПУ. В связи с развитием микропроцессорной техники применяются преобразователи для приводов подачи и главного движения с полным микропроцессорным управлением – цифровые преобразователи или цифровые приводы. Цифровые приводы представляют собой электродвигатели, работающие на постоянном или переменном токе. Конструктивно преобразователи частоты, сервоприводы и устройства главного пуска и реверса являются отдельными электронными блоками управления.
Привод подачи для станков с ЧПУ. В качестве привода используют двигатели, представляющие собой управляемые от цифровых преобразователей синхронные или асинхронные машины. Бес коллекторные синхронные (вентильные) двигатели для станков с ЧПУ изготовляют с постоянным магнитом на основе редкоземельных элементов и оснащают датчиками обратной связи и тормозами. Асинхронные двигатели применяют реже, чем синхронные. Привод движения подач характеризуется минимально возможными зазорами, малым временем разгона и торможения, и большими силами трения, уменьшенным нагревом элементов привода, большим диапазоном регулирования. Обеспечение этих характеристик возможно благодаря применению шариковых и гидростатических винтовых передач, направляющих качение и гидростатических направляющих, без зазорных редукторов с короткими кинематическими цепями и т. д.
Приводами главного движения для станков с ЧПУ обычно являются двигатели переменного тока – для больших мощностей и постоянного тока – для малых мощностей. В качестве приводов служат трехфазные четырехполюсные асинхронные двигатели, воспринимающие большие перегрузки и работающие при наличии в воздухе металлической пыли, стружки, масла и т.д. поэтому в их конструкции предусмотрен внешний вентилятор. В двигатель встраивают различные датчики, например датчик положения шпинделя, что необходимо для ориентации или обеспечения независимой координаты.
Преобразователи частоты для управления асинхронными двигателями имеет диапазон регулирования до 250. Преобразователи представляют собой электронные устройства, построенные на базе микропроцессорной технике. Программирование и параметрирование их работы осуществляются от встроенных программаторов с цифровым или графическим дисплеем. Оптимизация управления достигается автоматически после введения параметров электродвигателя. В математическом обеспечении заложена возможность настройки привода и пуск его в эксплуатацию.
Шпиндели станков с ЧПУ выполняют более точными, жесткими, с повышенной износостойкостью шеек, посадочных и базирующих поверхностей. Конструкция шпинделя значительно усложняется из–за встроенных в него устройств автоматического разжима и зажима инструмента, датчиков используемых при адаптивном управлении и автоматической диагностики.
Опоры шпинделей должны обеспечить точность шпинделя в течение длительного времени в переменных условиях работы, повышенную жесткость, небольшие температурные деформации. Точность вращения шпинделя обеспечивается, прежде всего, высокой точностью изготовления подшипников.
Наиболее часто в опорах шпинделей применяю подшипники качения. Для уменьшения влияния зазоров и повышения жесткости опор обычно устанавливают подшипники с предварительным натягом или увеличивают число тел качения. Подшипники скольжения в опорах шпинделей применяют реже и только при наличии устройств с периодическим (ручным) или автоматическим регулированием зазора в осевом или радиальном направлении. В прецизионных станках применяют аэростатические подшипники, в которых между шейкой вала и поверхностью подшипника находится сжатый воздух, благодаря этому снижается износ и нагрев подшипника, повышается точность вращения и т. п.
Привод позиционирования (т.е. перемещение рабочего орган станка требуемую позицию согласно программе) должен иметь высокую жесткость и обеспечивать плавность перемещения при малых скоростях, большую скорость вспомогательных перемещений рабочих органов (до 10 м /мин и более).
Вспомогательный механизм станков с ЧПУ включает в себя устройства смены инструмента, уборки стружки, систему смазывания, зажимные приспособления, загрузочные устройства и т.д. это группа механизмов в станках с ЧПУ значительно отличается от аналогичных механизмов, используемых в обычных универсальных станках. Например, в результате повышения производительности станков с ЧПУ произошло резкое увеличение сходящей стружки в единицу времени, а отсюда возникла необходимость создания специальных устройств отвода стружки из зоны обработки. Для сокращения потерь времени при загрузке применяют приспособления, позволяющие одновременно устанавливать заготовку и снимать деталь во время обработки др. заготовки.
Устройства автоматической сменой инструмента (магазины, автооператоры, револьверные головки) должны обеспечивать минимальные затраты времени на смену инструмента, высокую надежность в работе, стабильность положения инструмента, т.е. постоянство размера вылета и положение оси при повторных сменах инструмента, иметь необходимую вместимость магазина или револьверной головки.
Револьверная головка – это наиболее простое устройство смены инструмента: установку и зажим инструмента осуществляют вручную. В рабочей позиции один из шпинделей приводится во вращение от главного привода станка. Револьверные головки устанавливают на токарные, сверлильные, фрезерные, многоцелевые станки с ЧПУ; в головке закрепляют от 4 до 12 инструментов.
Контрольные вопросы:
Назовите основные конструктивные особенности станков с ЧПУ.
Перечислите конструктивные особенности базовых деталей, приводов главного движения и движения подач, а также вспомогательных механизмов станков с ЧПУ.
Токарные станки с ЧПУ.
Токарные станки с ЧПУ предназначены для наружной и внутренней обработки сложных заготовок типа тел вращения. Они составляют самую значительную группу по номенклатуре в парке станков с ЧПУ. На токарных станках с ЧПУ выполняют традиционный комплекс технологических операций: точение, отрезку, сверление, нарезание резьбы и др.
В основе классификации токарных станков с ЧПУ лежат следующие признаки:
расположение оси шпинделя (горизонтальные и вертикальные станки);
число используемых в работе инструментов (одно – и много – инструментальные станки);
способы их закрепления (на суппорте, в револьверной головке, в магазине инструментов);
вид выполняемых работ (центровые, патронные, патронно-центровые, карусельные, прутковые станки;
степень автоматизации (полуавтоматы и автоматы).
Центровые станки с ЧПУ служат для обработки заготовок типа валов с прямолинейным и криволинейным контурами. На этих станках можно нарезать резьбу резцом по программе.
Патронные с танки с ЧПУ предназначены для обработки, сверления, развертывания, зенкерования, цекования, нарезание резьбы метчиками в осевых отверстиях деталей типа фланцев, зубчатых колес, крышек, шкивов и др.; возможно нарезание резцом внутренней и наружной резьбы по программе.
Патронные центровые станки с ЧПУ служат для наружной и внутренней обработки разнообразных сложных заготовок деталей типа тал вращения и обладают технологическими возможностями токарных центровых и патронных станков.
Карусельные станки с ЧПУ применяются для обработки заготовок сложных корпусов.
Токарные станки с ЧПУ (рисунок 12) оснащают револьверными головками или магазином инструментов. Револьверные головки бывают 4-, 6- и двенадцатипозиционные, причем на каждой позиции можно устанавливать по два инструмента для наружной и внутренней обработки заготовки. Ось вращения головки может располагаться параллельно оси шпинделя, перпендикулярно к ней или наклонно.
При установке на станке двух револьверных головок в одной из них (1) закрепляют инструменты для наружной обработки, в другой (2) – для внутренней обработки (см. рисунок 13). Такие головки могут располагаться соосно одна относительно другой или иметь разное расположение осей. Индексирование револьверных головок производится, как правило, путем применения закаленных и шлифованных плоскозубчатых торцовых муфт, которые обеспечивают высокую точность и жесткость индексирования головки. В пазы револьверных головок устанавливают сменные взаимозаменяемые инструментальные блоки, которые настраивают на размер вне станка, на специальных приборах, что значительно повышает производительность и точность обработки. Резцовые блоки в револьверной головке базируют или на призме, или с помощью цилиндрических хвостовиков 6 (рисунок 14). Резец закрепляют винтами через прижимную планку 3. Для установки резца по высоте центров служит подкладка 2. Два регулировочных винта 5, расположенных под углом 45° один к другому, позволяют при наладке вывести вершину резца на заданные координаты. Подача СОЖ в зону резания осуществляется через канал в корпусе 1, заканчивающийся соплом 4, позволяющим регулировать направление подачи СОЖ.
Магазины инструментов (вместимость 8…20 инструментов) применяют редко, так как практически для токарной обработки одной заготовки требуется не более 10 инструментов. Использование большого числа инструментов целесообразно в случаях точения труднообрабатываемых материалов, когда инструменты имеют малый период стойкости.
Расширение технологических возможностей токарных станков возможно благодаря стиранию грани между токарными и фрезерными станками, добавлению внецентрового сверления, фрезерования контура (т.е. программируется поворот шпинделя); в некоторых случаях возможно резьбонарезание несоосных элементов заготовок.
Контрольные вопросы:
Как классифицируют токарные станки с ЧПУ по виду выполняемых работ?
Какими устройствами для крепления инструмента оснащают токарные станки с ЧПУ?
Как базируют резцовые блоки в револьверной головке станка?
Фрезерные станки с ЧПУ
Фрезерные станки с ЧПУ предназначены для обработки плоских и пространственных поверхностей заготовок сложной формы. Конструкции фрезерных станков с ЧПУ аналогичны конструкциям традиционных фрезерных станков, отличие от последних заключается в автоматизации перемещений по УП при формообразовании.
В основе классификации фрезерных станков с ЧПУ лежат следующие признаки:
Расположение шпинделя (горизонтальное и вертикальное);
Число координатных перемещений стола или фрезерной бабки;
Число используемых инструментов (одноинструментные и многоинструментные);
Способ установки инструментов в шпиндель станка (вручную или автоматически).
По компоновке фрезерные станки с ЧПУ делятся на четыре группы:
вертикально – фрезерные станки с крестовым столом;
консольно-фрезерные станки;
продольно – фрезерные станки;
широкоуниверсальные инструментальные станки.
В вертикально – фрезерных станках с крестовым столом (рисунок 15, а) стол перемещается в продольном (ось X) и поперечном (ось Y) горизонтальном направлениях, а фрезерная бабка – в вертикальном направление (ось Z).
В консольно-фрезерных станках (рисунок 15, б) стол перемещается по трем координатным осям (X, Y и Z), а бабка не подвижна.
В продольно фрезерных станках с подвижной поперечиной (рисунок 15, в) стол перемещается по оси X,шпиндельная бабка - по оси Y, а поперечная по оси Z. В продольно – фрезерных станках, с неподвижной поперечиной (рисунок 15, г) стол перемещается по оси X, а шпиндельная бабка – по осям Y и Z.
В широкоуниверсальных инструментальных фрезерных станках (рисунок 15,д) стол перемещается по осям X и Y, а шпиндельная бабка – по оси Z.
Рисунок 15 – Система координат в различных модификациях фрезерных станков:
а) – фрезерный станок с крестовым столом; б) консольно-фрезерный станок; в) продольно-фрезерный станок с подвижной поперечиной; г) продольно-фрезерный станок с не подвижной поперечиной; д) широкоуниверсальный фрезерный станок.
Фрезерные станки в основном оснащают прямоугольными и контурными устройствами ЧПУ.
При прямоугольном управлении (условное обозначение в модели станка – Ф 2) стол станка совершает движение в направление, параллельном одной из координатных осей, что делает не возможной обработку сложных поверхностей. Станки с прямоугольным управлением применяют для фрезерования плоскостей, скосов, уступов, пазов, разновысоких бобышек и других аналогичных поверхностей.
При контурном управлении (условное обозначение в модели станка – Ф 3 и Ф 4) траектория перемещения стола более сложная. Станки с контурным управлением используются для фрезерования различных кулачков, штампов, пресс форм и др. аналогичных поверхностей. Число управляемых координат, как правило, равно трем, а в некоторых случаях четырем и пяти. При контурном управлении движении формообразования производится не менее чем по двум координатным осям одновременно.
В отдельных случаях на фрезерных станках при обработке заготовок простой формы в условиях средне – и крупносерийного производства также применяют системы ЧПУ.
Во фрезерных станках с ЧПУ в качестве привода главного движения используют асинхронные электродвигатели (в этих случаях имеется коробка скоростей) или электродвигатели постоянного тока.
На небольших фрезерных станках с прямоугольным ЧПУ применяют один приводной электродвигатель постоянного тока и коробку передач с автоматически переключаемыми электромагнитными муфтами, а на тяжелых станках с контурным управлением каждое управляемее координатное перемещение осуществляется от автоматного электропривода постоянного тока.
Приводы движения подач фрезерных станков с ЧПУ имеют короткие кинематические цепи, передающие движения от двигателя непосредственно исполнительному органу.
Рассмотрим устройство консольного вертикально-фрезерного станка мод. 6Р13Ф3. Данный станок является консольным, т.е. его стол имеет рабочее перемещение в горизонтальной плоскости (по координатам X и Y) и (вместе с консолью) установочное перемещение в вертикальном направлении (по координате W); рабочее перемещение по координате Z имеет ползун со шпинделем. Станина 8 является базой, на которой монтируются узлы и механизмы станка. Спереди станина имеет вертикальные направляющие, закрытые кожухом 9, по которым перемещается консоль 1. На горизонтальных направляющих смонтированы салазки 2, по продольным направляющим которых передвигается стол 3. На привалочной плоскости станины закреплена фрезерная бабка 6, по вертикальным направляющим которой перемещается ползун 7 со шпинделем 5. В соответствии с требованиями техники безопасности ползун имеет защитный щиток 4. Сзади станка расположен шкаф 10 с электрооборудованием и УЧПУ.
Рисунок 16 – Вертикально-фрезерный станок мод. 6Р13Ф3:
1-консоль; 2-салазки; 3-стол; 4-защитный щиток; 5-шпиндель: 6-фрезерная бабка; 7-ползун; 8-станина; 9-кожух;
10-шкаф с электрооборудованием.
Контрольные вопросы:
Какие компоновки фрезерных станков с ЧПУ вы знаете?
Какими системами ЧПУ оснащают фрезерные станки?
Сверлильные станки с ЧПУ
Вертикально – сверлильные станки с ЧПУ в отличие от аналогичных станков с ручным управлением оснащены крестовыми столами, автоматически перемещающими заготовку по осям X и Y, в результат чего отпадает необходимость в кондукторах или в ее предварительной разметке.
Радиально – сверлильные станки с ЧПУ имеют подвижную по оси X колонну, подвижную по оси Y рукав со шпиндельной бабкой, в которой смонтирован сверлильный шпиндель, перемещающийся по оси Z. Помимо этого рукава при накладке может перемещаться в вертикальном направлении.
Автоматизированные перемещение рабочих органов сверлильных станков по осям X и Y обеспечивают выполнение обработки отверстий и фрезерования.
Сверлильные станки оснащают позиционными УЧПУ, позволяющими автоматически установить рабочие органы в позицию, заданную программой. Режущий инструмент на сверлильных станках с УЧПУ закрепляют непосредственно в коническом отверстии шпинделя или с помощью промежуточных втулок и оправок.
Общий вид вертикально сверлильного станка модели 2Р135Ф2 – 1, оснащенного ЧПУ, показан на рисунке 17. На основании станка 1 смонтирована колона 10, по прямоугольным вертикальным направляющим которой перемещается суппорт 4, несущий револьверную головку 3. На колонне 10 смонтированы коробки скоростей 5 и редуктор подач 6. Салазки 2 крестового стола перемещаются по горизонтальным направляющим основания 1, а верхняя часть 11 стола – по направляющим салазок. С правой стороны станка расположены шкаф 8 с электрооборудованием и УЧПУ 9. Станок имеет подвесной пульт 7 управления.
Рисунок 17 – Вертикально-сверлильный станок модели 2Р135Ф2:
1-основание; 2-салазки; 3-револьверная головка; 4- суппорт; 5-коробка скоростей; 6-редуктор подач; 7-подвесной пульт; 8- шкаф с электрооборудованием; 9-УЧПУ; 10-колонна;11-верхняя часть стола.
Контрольные вопросы:
Какое принципиальное различие существует между вертикально – сверлильными станками с ЧПУ и без ЧПУ?
Какими системами ЧПУ оснащают вертикально – сверлильные станки?
Шлифовальные станки с ЧПУ
Система ЧПУ оснащают плоскошлифовальные, кругло – и бесцентрово-шлифовальные и другие станки. При создании шлифовальных станков с ЧПУ возникают технические трудности, которые объясняются следующими причинами. Процесс шлифования характеризуется, с одной стороны, необходимостью получения высокой точности и качества поверхности при минимальном рассеянии размеров, с другой стороны, - особенностью, заключающейся в быстрой потере размерной точности шлифовального круга вследствие его интенсивного изнашивания в процессе работы. В этом случае в станке необходимы механизмы автоматической компенсации изнашивания шлифовального круга. ЧПУ должно компенсировать деформации системы СИД, температурные погрешности, различия припусков на заготовках, погрешности станка при перемещении по координатам и т. д. Измерительные системы должны иметь разрешающую способность, обеспечивающую жесткие допуски на точность позиционирования. Например, в кругло-шлифовальных станках такие приборы обеспечивают непрерывное измерение диаметра заготовки в процессе обработки с относительной погрешностью не более 2 ×10 -5 мм. Контроль продольных перемещений стола осуществляется с погрешностью не более 0, 1 мм.
Для шлифовальных станков используется системы типа CNC с управлением по трем – четырем координатам, но в станках, работающим несколькими кругами, возможно управление по пяти – шести и даже по восьми координатам. Взаимосвязь между оператором и системой ЧПУ (CNC) шлифовального станка в большинстве случаев осуществляется в диалоговом режиме с помощью дисплея. В системе управления применяются встроенные диагностические системы, повышающие надежность станков.
Наиболее распространены кругло-шлифовальные станки с ЧПУ, дающие максимальный эффект при обработке с одной установки многоступенчатых деталей типа шпинделей, валов электродвигателей, редукторов, турбин и т.д. Производительность повышается в основном в результате снижения вспомогательного времени на установку заготовок и съем готовой детали, на переустановку для обработки следующей шейки вала, на измерение и т. д. При обработке многоступенчатых валов на кругло-шлифовальном станке с ЧПУ достигается экономия времени в 1,5 – 2 раза по сравнению с ручным управлением.
Бесцентровые кругло-шлифовальные станки эффективно применяются при обработке деталей малого и большого диаметров без ограничения длины, либо тонкостенных деталей, а также деталей, имеющих сложные наружные профили (поршень, кулак и т.д.). В условиях массового производства эти станки характеризуются высокой производительностью и точностью обработки. В мелкосерийном и индивидуальном производстве применение таких станков ограничено трудоемкостью переналадки. Расширение областей применения бесцентровых кругло-шлифовальных станков сдерживают два фактора: большие затраты времени на правку кругов и сложность наладки станков, что требует значительных затрат времени и высокой квалификации персонала. Это объясняется тем, что в конструкции станков используются шлифовальные и ведущие круги; устройства правки, обеспечивающие придание соответствующей формы поверхностям шлифовального и ведущего кругов; возможность установки положения опорного ножа; механизмы компенсационных подач шлифовального круга на обрабатываемую деталь и на правку, а также ведущего круга на деталь и на правку; установка положения загрузочного и разгрузочного устройства.
Применение СЧПУ позволило управлять многокоординатным функционированием бесцентровых кругло-шлифовальных станков. В системе управления станков используют программные модули, которые рассчитывают траектории инструмента (круга, алмаза), его коррекцию взаимодействия с человеком. Для обработки деталей с различными геометрическими формами (конус, шар и др.) создается программное обеспечение6 диспетчер режимов, интерполятор и модуль управления приводами.
При обработке и правке число сочетаемых управляемых координат может доходить до 19, в том числе по две – три координаты отдельно для правки шлифовального и ведущего кругов.
В условиях серийного производства применение СЧПУ обеспечивает гибкое построение цикла шлифования и правки, что позволяет быстро переналаживать станки на обработку других изделий.
Наличие многокоординатной системы ЧПУ обеспечивает большую универсальность станка, малые величины подачи кругов, что позволяет эффективно управлять процессом шлифования и правки.
СЧПУ бесцентровых кругло-шлифовальных станков строится по агрегатному принципу (например, на станках японских фирм). На станке возможна установка любого из четырех вариантов управления станком от СЧПУ:
одна управляемая координата – поперечная подача шлифовального круга;
две управляемые координаты – поперечная подача шлифовального круга и правящего алмаза в целях их синхронизации;
три управляемые координаты - поперечная подача шлифовального круга, а также поперечная и продольная подача алмаза при его правке;
пять управляемых координат - поперечная подача шлифовального круга, а также поперечная и продольная подачи алмазов при правке шлифовального и ведущего кругов.
Использование СЧПУ для управления бесцентровыми кругло-шлифовальными станками позволяет существенно упростить конструкции ряда механических узлов: устройств правки (в результате отказа от копирных линеек, механизмов подачи алмазов и т.д.), приводов продольного перемещения устройств правки, механизмов тонкой подачи шлифовального и ведущего кругов, контрольных и контрольно – подналадочных устройств и др.
Контрольные вопросы:
Каковы технические трудности создания шлифовальных станков с ЧПУ?
Какими системами ЧПУ оснащают шлифовальные станки?
Многоцелевые станки с ЧПУ
Благодаря оснащению многоцелевых станков (МС) устройствами ЧПУ и автоматической смены инструмента существенно сокращается вспомогательное время при обработке и повышается мобильность переналадки. Сокращение вспомогательного времени достигается благодаря автоматическим установке инструмента (заготовки) по координатам, выполнению всех элементов цикла, смене инструмента, кантованию и смене заготовки, изменение режимов резания, выполнению контрольных операций, а также большим скоростям вспомогательных перемещений.
По назначению МС делятся на две группы: для обработки заготовок корпусных и плоских деталей, и для обработки заготовок деталей типа тел вращения. В первом случае для обработки используют МС сверлильно-фрезерно-расточной группы, а во втором – токарной и шлифовальной групп. Рассмотрим МС первой группы, как наиболее часто используемые.
МС имеют следующие характерные особенности: наличие инструментального магазина, обеспечивающего оснащенность большим числом режущих инструментов для высокой концентрации операций (черновых, получистовых и чистовых), в том числе точения, растачивания, фрезерования, сверления, зенкерования, развертывания, нарезание резьб, контроля качества обработки и др.; высокая точность выполнения чистовых операция (6…7-й квалитеты).
Для системы управления МС характерны сигнализация, цифровая индикация положения узлов станка, различные формы адаптивного управления. МС – это в основном одношпиндельные станки с револьверными и шпиндельными головками.
Многоцелевые станки (обрабатывающие центры) для обработки заготовок корпусных деталей. МС для обработки заготовок корпусных деталей подразделяют на горизонтальные и вертикальные станки (рисунок 18).
Горизонтальный МС мод. ИР-500МФ4, предназначен для обработки корпусных деталей. Данный станок имеет шпиндельную бабку 4, перемещающуюся по вертикальным направляющим стойки 7. Магазин инструментов 6 неподвижно закреплен на стойке 7; инструмент устанавливается в шпиндель 3 автооператором 5 в верхнем положении шпиндельной бабки. Обрабатываемую деталь устанавливают на стол 1, перемещающийся по координате Х. У правого торца станины размещена поворотная платформа 8, на которой установлены два стола-спутника с обрабатываемыми деталями.
Рисунок 18 – Многоцелевой станок (обрабатывающий центр) мод. ИР-500МФ4:
1-стол поворотный; 2-приспособление; 3-шпиндель; 4-шпиндельная бабка; 5-автооператор; 6-инструментальный магазин; 7-подвижная стойка; 8-поворотная платформа; 9-стол-спутник; 10-направляющие; 11-УЧПУ; 12-шкаф с электрооборудованием.
Обработка заготовок на МС по сравнению с их обработкой на фрезерных, сверлильных и других станках с ЧПУ имеет ряд особенностей. Установка и крепление заготовки должны обеспечивать ее обработку со всех сторон за один установ (свободный доступ инструментов к обрабатываемым поверхностям), так как только в этом случае возможна многосторонняя обработка без переустановки.
Обработка на МС не требует, как правило, специальной оснастки, так как крепление заготовки осуществляется с помощью упоров и прихватов. МС снабжены магазином инструментов, помещены на шпиндельной головке, рядом со станком или на другом месте. Для фрезерования плоскостей используют фрезы небольшого диаметра и обработку производят строчками. Консольный инструмент, применяемый для обработки неглубоких отверстий, имеют повышенную жесткость и, следовательно, обеспечивает заданную точность обработки. Отверстия, лежащие на одной оси, но расположенные в параллельных станках заготовки, растачивают с двух сторон, поворачивая для этого стол с заготовкой. Если заготовки корпусных деталей имеют группы одинаковых поверхностей и отверстий, то для упрощения составления технологического процесса и программы их изготовления, а также повышения производительности обработки (в результате сокращения вспомогательного времени) в памяти УЧПУ станка вводят постоянные циклы наиболее часто повторяющихся движений (при сверлении, фрезеровании). В этом случае программируется только цикл обработки первого отверстия (поверхности), а для остальных – задаются лишь координаты (X и Y) их расположения.
В качестве примера на рисунке 19 показаны некоторые постоянные циклы, включенные в программное обеспечение и используемые при обработке на станках модели ИР320ПМФ4.
Рисунок 19 – Постоянные циклы обработки на многоцелевом станке модели ИР320ПМФ4:
1-фрезерование наружного контура (с круговой интерполяцией), 2-глубокое сверление с выходом сверла для отвода стружки; 3-растачивание ступенчатых отверстий; 4-обратная цековка с использованием ориентации шпинделя; 5-растачивание отверстия Ø 125 мм с использованием специальной оправки; 6-фрезерование по контуру внутренних торцов; 7-цековка путем фрезерования по контуру (с круговой интерполяцией); 8-сверление отверстия Ø 30 мм; 9-нарезание резьбы (до М16); 10-фрезерование внутренних канавок дисковой фрезой (с круговой интерполяцией); 11-цековка отверстий; 12-фрезерование торцов фрезой; 13-обработка поверхностей типа тел вращения.
Устройство для автоматической смены приспособления - спутника (ПС) на станке модели ИР500МФ4 показано на рисунке 20. ПС 11 устанавливают на платформу 7 (вместимость два ПС), на которой смонтированы гидроцилиндры 10 и 13. Штоки гидроцилиндров имеют Т – образные захваты 14 и 6. При установке на платформу (перемещение по стрелке Б) ПС вырезом 12 входит в зацепление с захватом 14 штока. На платформе ПС базируется на роликах 9 и центрируется (по боковым сторонам) роликами 8 (исходное положение ПС в позиции ожидания). Перемещение штока гидроцилиндра 10 обуславливает качение (по роликам) спутника.
Рисунок 20 – Устройство для автоматической смены приспособления-спутника:
1-плита базовая; 2-болты регулировочные; 3- колесо зубчатое; 4-рейка; 5, 13,16-гидроцилиндры; 6, 14-захват штока; 7-платформа; 8,9-ролики; 10, -шток гидроцилиндра; 11-приспособление спутник; 12-фигурный вырез;15- стойка.
При движении штока гидроцилиндра 13 захвата 6 перемещается (по направляющей штанге) и катит ПС по роликам 9 и 8 (в направлении стрелки А) на поворотный стол станка, где спутник автоматически опускается на фиксаторы. В результате захвата 6 выходит из зацепления с ПС и стол станка (с закрепленным на нем спутником) на быстром ходу перемещается в зону обработки.
Заготовку закрепляют на спутнике во время обработки предыдущей заготовки (когда ПС находится в позиции ожидания) или заранее, вне станка.
После того как заготовка будет обработана, стол станка автоматически (на быстром ходу) передвигается в право к устройству для смены спутника и останавливается в таком положении, при котором фигурный паз ПС оказывается под захватом 6. Гидроцилиндр поворотного стола расфиксирует спутник, после чего ПС входит в зацепление с захватом 6, а масло поступает в штоковую полость гидроцилиндра 13, шток смещается в крайнее правое положение и перемещается спутник с заготовки на платформу 7, где уже находится ПС с новой заготовкой. Чтобы поменять спутник местами, платформа поворачивается на 180° (на станке 15) зубчатым колесом 3, сопряженным с рейкой 4, приводимой в движение гидроцилиндрами 5 и 16.
Платформу 7 точно выверяют относительно поворотного стола станка с помощью регулировочных винтов 2 и 7, ввернутых в выступы базовой плиты 1, неподвижно закрепленной на фундаменте.
Контрольные вопросы:
Чем отличаются многоцелевые станки с ЧПУ от токарных, фрезерных, сверлильных и др. станков с ЧПУ?
Расскажите об основных узлах многоцелевого станка для обработки заготовок корпусных деталей.
Обработка на станках с ЧПУ
Основу современных систем числового программного управления металлообрабатывающего оборудования составляют передовые технологические решения в области аппаратного и программного обеспечения, новых информационных технологий и технологических компонентов.
Системы ЧПУ с открытой архитектурой класса открыли новую страницу в истории устройств числового программного управления станками. Применение стандартных или индустриальных персональных компьютеров как базовой платформы для СЧПУ - это широкие возможности в унификации и вместе с тем доступ к огромным ресурсам памяти, вычислительной мощности, стандартизованным коммуникационным средствам (интерфейсам), всевозможному системному, инструментальному и пользовательскому программному обеспечению и многому другому, предоставляемому развивающейся с невероятной скоростью индустрией информационных технологий.
Рассмотрим некоторые из предлагаемых на российском рынке наиболее популярных зарубежных систем и отдадим дань отдельным отечественным разработкам. Мы не претендуем на полноту обзора, наша цель - рассказать о принципиальных решениях.
Зарубежные системы
Siemens
Последние тридцать лет фирма Siemens является одним из законодателей мод на рынке станков с ЧПУ. Что же представляет сегодня фирма Siemens? В области ЧПУ фирма расширила свою гамму и теперь предлагает системы ЧПУ не только для сложных станков, работающих на большие серии.
Для простых станков фирма предлагает семейство ЧПУ (2 оси + шпиндель для токарных и 3 оси + шпиндель для фрезерных станков). В качестве приводов могут быть использованы, как современные шаговые трехполюсные двигатели (с ЧПУ Sinumerik 802S), так и сервопривода переменного тока с аналоговым интерфейсом (с ЧПУ Sinumerik 802С).
Шаговые приводы позволяют существенно снизить общую стоимость станка, и поэтому особенно популярны в самых простых, маленьких станках, использующихся небольшими фирмами, которые являются поставщиками комплектующих для более крупных фирм либо выпускают небольшие серии деталей для собственных нужд, поддерживая при этом постоянный уровень качества и избавляясь от проблемы поиска высококвалифицированных специалистов.
Использование сервоприводов с аналоговым интерфейсом (+/-10 В) позволяет повысить точность обработки поверхности на тех же станках или же, что является очень актуальным сегодня на рынке СНГ, использовать ЧПУ Sinumerik 802С для задач модернизации станков, причем появляется возможность оставить старые приводы, что существенно удешевляет модернизацию. При этом производительность станка повышается благодаря тому, что новая система ЧПУ более надежна в эксплуатации, а новые функции ЧПУ позволяют сократить время обработки детали.
Модификация Sinumerik 802С позволяет использовать ее в качестве простой цифровой индикации для цифровых станков. Причем ее стоимость сравнима или даже ниже, чем классические системы индикации, существующие на рынке.
К этим ЧПУ вплотную примыкает система Sinumerik 802D, которая добавляет еще одну ось (например, для управления столом) и работает с универсальным сервоприводом Simodrive 611U.
Для более сложных станков фирма Siemens предлагает уже завоевавшие доверие СЧПУ Sinumerik 810D с процессорами CCU1 и CCU2 и Sinumerik 840D с процессорами NCU 571 и NCU 572. Эти системы позволяют осуществлять управление по 6-12 осям и имеют в своем составе функции, позволяющие управлять не только токарной или фрезерной обработкой, но и такими технологиями, как шлифование, лазерная резка, вырубка и управление роботами. Эти системы работают совместно с цифровым приводом Simodrive 611D, что позволяет достичь точности и динамики, недостижимых для традиционного аналогового привода.
Для сложных технологий формообразования, подготовки моделей и высокоскоростной обработки твердосплавных деталей предлагается линия Sinumerik Power line, представленная в настоящий момент СЧПУ Sinumerik 810D с CCU3 и Sinumerik 840D с NCU 573. Отдельной линией проходит система ЧПУ Sinumerik 840Di. Это так называемая система ЧПУ типа PCNC, базирующаяся на стандартном промышленном ПК. При этом интерфейс пользователя и ядро ЧПУ реализованы программно, а контроллер ПЛК и интерфейсы подключения периферии и приводов - на единой слот-плате. В качестве привода используется тот же универсальный привод Simodrive 611U, что и для Sinumerik 802D.
Появление новых функций в ЧПУ позволяет сегодня существенно уменьшить время переналадки станка, которое в универсальном станке может занимать до 90% от общего времени работы. Другие функции позволяют избежать поломки дорогостоящего инструмента и повреждения дорогостоящей детали. Износ инструмента также можно снизить за счет программных функций ЧПУ. Повышение качества обработки поверхности с использованием систем ЧПУ фирмы Siemens позволяет отказаться от финишной обработки деталей и тем самым не только сократить время производства (т. е. повысить производительность), но и уменьшить парк дорогостоящих станков.
GE Fanuc Automation
Устройства ЧПУ компании GE Fanuc Automation пользуются спросом благодаря их высокой эксплуатационной надежности и производительности. Компания выпускает ЧПУ открытого и традиционного типов, которые увеличивают производительность станков за счет обеспечения возможности доступа к информационным и программным средствам в самом станке. Системы ЧПУ компании GE Fanuc рассчитаны на такой широкий спектр операций, как: шлифование, сверление, резка, фрезерование, перфорирование, токарная обработка, обработка древесины и прочее.
ЧПУ традиционного типа.
Блок управления ЧПУ компании GE Fanuc во всех моделях новой серии ЧПУ имеет толщину всего лишь 60 мм. Встроенная в блок миниатюрная печатная плата ЧПУ позволяет полностью использовать возможности самых современных БИС и технологий поверхностного монтажа. Плата монтируется за жидкокристаллическим дисплеем. Компания также разработала высокоскоростную сервошину последовательного действия и компактный распределяемый модуль ввода-вывода, что позволяет подключать один блок управления ЧПУ и сразу несколько сервоусилителей к одному волоконно-оптическому кабелю. Различные модули ввода-вывода могут монтироваться на рабочей панели и на пульте управления станком, что позволяет значительно уменьшить объем электроавтоматики станка и его размеры. Производственная система может быть улучшена с помощью Factolink, который может использовать ЧПУ в качестве оконечного устройства оперативной системы.
ЧПУ открытого типа.
Весь спектр ЧПУ открытого типа компании GE FANUC представлен сериями 160i, 180i, 210i and 160is, 180is, 210is, разработанными на базе 16i, 18i и 21 i серий. ЧПУ серии «is» являются самыми компактными и тонкими из ЧПУ открытого типа. Печатная плата, совместимая с функцией карманного ПК MS Windows СЕ, монтируется за цветным жидкокристаллическим дисплеем. Панель разработана с использованием самых современных БИС и технологий поверхностного монтажа. Серии 160i, 180i, 210i совмещают надежность автономного ЧПУ с мощностью интеллектуального терминала компании GE Fanuc. ЧПУ открытого типа обеспечивают высокоэффективную реализацию функций управления ЧПУ компании GE Fanuc одновременно с функциями персонального компьютера и возможностью их дальнейшего расширения. Благодаря высокой надежности они могут с уверенностью применяться на производствах любого уровня. Устройство ЧПУ и станок могут управляться с помощью графического пользовательского интерфейса персонального компьютера. Кроме того, сетевые возможности могут быть использованы для обмена информацией, а программные средства базы данных - для управления сервисными программами. Используя наиболее продвинутые функции персональной ЭВМ, можно преобразовать самый простой станок в машину с интеллектуальными возможностями. Прикладное программное обеспечение поддерживается средой Microsoft Windows 95/98, Windows NT4.0 и Windows 2000 для ЧПУ открытого типа серии «i», Microsoft Windows СЕ для ЧПУ открытого типа серии «is». Механики могут разработать прикладное программное обеспечение для станка, как и для обычной ЭВМ. Программное обеспечение компании GE Fanuc (библиотека CNC) используется для ввода-вывода внутренней информации ЧПУ. Такое программное обеспечение может поддерживать стандартный набор языков программирования Microsoft (Visual Basic или Visual С++ТМ), а также обмен через OLE/DDE. Имеется возможность простой установки любого прикладного программного обеспечения.
Помимо уже названных компаний на российском рынке присутствует продукция таких зарубежных фирм, как Heidenhain, Bosch Rexroth, IPA, Indramat, Andron GmbH, M&R Numeric (все Германия), итальянских Fidia, OSPI, Olivetti, японских Mitsubishi, Toshiba, Hitachi, американской Allen-Bredly и других.
О пользе кооперации
Из систем ЧПУ, выпускаемых в бывших советских республиках, можно отметить продукцию ЗАО МШАК (Армения) и украинской компании «Вест Лабе».
Система ЧПУ MSHAK-DELTA TAU с открытой архитектурой класса PC-based построена на базе стандартных или индустриальных персональных компьютеров. На компьютер устанавливается мощный программируемый многоосевой контроллер РМАС фирмы Delta Таu Data System, Inc. (США), управляющий в реальном масштабе времени всеми подсистемами станка. Это всего лишь одна плата, устанавливаемая на ISA (или PCI) шину, несущая в себе функции управления движением осей (до 32) и управления электроавтоматикой (PLC до 2048 вх./вых.). Система способна обеспечить одновременное управление 8 станками, количество синхронных (интерполируемых) осей - 32.
Система ЧПУ WL4T компании «Вест Лабе» является базовой моделью 2-координатной контурной системы управления второго поколения семейства WL4 и предназначена для использования в карусельных станках и токарных станках с базовыми функциями автоматического управления. Число одновременно управляемых координат 2 + 1 (планшайба). Способы интерполяции - линейная и круговая.
Отечественные решения
Компания «Балт-Систем» (Санкт- Петербург) предлагает две системы ЧПУ последнего поколения NC-110 и NC-200.
Система NC-110 отличается сочетанием многофункциональности и надежности. Система построена по модульному принципу и позволяет удовлетворить растущие требования потребителей путем установки дополнительных модулей. Система NC-200 представляет собой малогабаритное, моноблочное устройство, в котором объединены в одно целое блок управления, пульт оператора и станочный пульт.Эти системы предоставляют пользователям широкий спектр технологических возможностей, среди которых: возможность параметрического программирования, программирования в элементах векторной геометрии, программирования двух виртуальных осей, масштабирования размеров, смещения нуля детали и поворот плоскости обработки, векторной компенсации радиуса при вершине резца при токарной обработке, управления моторизованным инструментом; возможность активизации фрезерно-расточных циклов при токарной обработке и многое другое.
Устройства ЧПУ «Микрос» серий 11, 12Т, 12ТВ, выпускаемые ЗАО «Микрос» (дочернее предприятие АО ЦНИТИ), базируются на современной компьютерной технологии промышленного типа и имеют удобную блочную компоновку. Их основу составляют промышленный компьютер и операционная система жесткого реального времени, гарантирующая быструю реакцию управления. Жесткий диск большой емкости обеспечивает практически неограниченную память управляющим технологическим программам.
Пользователю предоставляется полный контроль над выполняемыми функциями и операциями и за состояние станка и системы ЧПУ.
Встроенный редактор дает возможность вводить и корректировать управляющие программы. Программирование осуществляется при помощи G-функций и трехбуквенных кодов.
Имеющийся режим графической поддержки позволяет визуализировать реальное движение инструмента и проверять запрограммированные элементы траектории инструмента еще до начала обработки.
Кроме того, системы ЧПУ серии «Микрос» обладают развитыми функциями компенсации погрешностей механики станка: непрямолинейности и неперпендикулярности направляющих, непараллельности направляющих оси «Z» - оси вращения шпинделя, зазора в механической подаче; а также функцией компенсации непостоянства радиуса режущей кромки резца.
Автономная самонастройка системы позволяет определить оптимальные параметры управления положением для каждой оси.
Универсальная система FMS-3000 компании «Модмаш-Софт» (Нижний Новгород)- высокопроизводительная система числового программного управления, предназначенная для установки на различные типы технологического оборудования: фрезерные станки, копировальные станки, обрабатывающие центры, токарные станки и другое оборудование с ЧПУ.
Адаптация к конкретному типу станка осуществляется с помощью программы электроавтоматики и разветвленной системы параметров FMS-3000.
Основа FMS-3000 - персональный компьютер промышленного исполнения, изготовленный по новейшим технологиям. Открытая архитектура FMS- 3000 в комплексе с мощным программным обеспечением позволяет легко интегрировать в ее состав компьютерные компоненты ведущих производителей вычислительной техники.
Программное обеспечение системы реализовано на базе ядра жесткого реального времени с использованием библиотеки RT-Kernel, гарантирующей высокое качество выполнения таймерных задач управления сервоприводами и циклами электроавтоматики. Открытая структура системы позволяет включать в состав системы программные модули пользователя.
Ижевским НПП ИЖПРЭСТ с 1992 г. разработаны и серийно выпускаются ЧПУ Маяк-400 (1992 г.) и Маяк-500 (1999 г.). Последней разработкой компании является система ЧПУ Маяк-600. Система числового программного управления Маяк-600 предназначена для комплектования новых станков и модернизации старых.
Концепция размещения системы - отдельно блок ЧПУ и отдельно пульт оператора, соединенные последовательным интерфейсом. Блок ЧПУ встраивается в электрошкаф станка, а пульт оператора устанавливается в пульт станка или в электрошкаф. Маяк-600 позволяет управлять восемью координатными осями и шпинделем. Приводы подач и шпиндель управляются аналоговым сигналом (+/-10 В). К измерительным контурам можно подключать фотоэлектрические и индуктивные датчики обратной связи. Существует исполнение УЧПУ для управления шаговыми двигателями.
Некоторые функции системы: возможность отработки программы с любого кадра с автоматическим определением начальных условий (исходной точки и G-функций), диагностика блоков при включении и во время работы, многоуровневая система доступа к данным станка, редактирование управляющих программ, параметров, корректоров с пульта оператора, возможность отработки управляющих программ объемом 30 Мбайт и более, винтовая интерполяция, линейная интерполяция по всем осям одновременно.
Типы измерительных преобразователей перемещений - индуктивные и фотоэлектрические (круговые и линейные). В состав СЧПУ входит интегрированный программируемый контроллер.
Система WinPCNC. Система WinPCNC (компания NCSYSTEMS.RU, Москва) является однокомпьютерной системой ЧПУ, построенной на мощной платформе персонального компьютера с операционной системой Windows NT и расширением реального времени RTX 4.1 фирмы VentureCom. Она относится к классу PCNC. Система использует единственный процессор для обслуживания всех ее функций, включая функции электроавтоматики. Аппаратная часть представлена стандартной аппаратурой персонального компьютера и дополнительными интерфейсными модулями для связи со следящими приводами подачи и главного движения, приводами электроавтоматики, панелью оператора. Система ЧПУ состоит из двух независимых блоков - системного и панели оператора. Системный блок размещен в корпусе промышленного компьютера. Блок панели оператора встраивается в свой корпус и конструктивно оформляется так, как это удобно потребителю. Системный блок представляет собой базовый набор плат на шине PCI. Существует также возможность установки дополнительных плат: например, для увеличения числа управляемых координат, для увеличения общего числа параллельных входов-выходов электроавтоматики, для установки сетевых интерфейсных плат типа Fieldbus с целью управления приводами и электроавтоматикой.
Интерфейс оператора открыт для включения любых приложений конечного пользователя, разработанных в среде Windows. При этом конечным пользователям предоставлен широкий открытый набор интерфейсных функций API. Интерфейс оператора (его внешний вид, набор режимов, страниц и меню) может быть в кратчайший срок существенно перепроектирован с помощью специальной инструментальной системы State_Machine_Builder. Система ЧПУ может быть настроена на любую версию языка управляющих программ в коде ISO-7bit (DIN 66025). Настроенная версия поддерживается редактором-дебаггером управляющих программ и гибким интерпретатором управляющих программ (ISO-процессором). Интерпретатор может быть настроен на любое (разумное) число буферируемых кадров. Редактор-дебаггер располагает системой графического моделирования управляющей программы на входе системы и на выходе интерпретатора, т. е. с учетом эквидистант. Интерполятор системы имеет гибкую собственную архитектуру и фиксированный входной интерфейс IPD (Interpolator Data); он открыт для включения любых специальных алгоритмов интерполяции. В процессе управления может быть использована любая комбинация имеющихся алгоритмов. Гибкая система электроавтоматики построена на основе концепции SoftPLC, т. е. на основе программной реализации контроллера в составе прикладной компоненты системы ЧПУ. Взаимодействие всех модулей системы ЧПУ осуществляется через многофункциональную программную шину, которая служит глобальным сервером системы. Подобная организация допускает масштабирование системы.
Системы ЧПУ 4CKFF (АОЗТ «4С») - серийно выпускаемые представители серии 4СК, разработанной и поставленной на производство в Санкт-Петербурге совместно с фирмой Olivetti. Устройства МС/ТС управляют станками, обрабатывающими центрами, гибкими модулями, а GP - специальными типами станков, роботами и автоматическими линиями. Управление пятью (МСГГС) и неограниченным (GP) числом технологических процессов в реальном времени позволяет параллельно выполнять в СЧПУ несколько управляющих программ, например от одного устройства управлять обработкой деталей на нескольких станках одновременно. 4CKFF в 10 раз быстрее, чем ранее выпускавшиеся 4СК, что позволяет наиболее полно использовать широкие возможности программного обеспечения.
Всего 8 функционально различных аппаратных модулей снижает технологическую трудоемкость производства, упрощает сервисное обслуживание и обеспечивает программно-аппаратную совместимость современных и ранее выпускавшихся 4СК. В 2000 г. выполнен практически полный переход на использование в 4CKFF элементной базы зарубежного производства, определяющей качество и надежность. Производство СЧПУ 4CKFF, включая смежные производства: печатных плат, металлоконструкций, клавиатуры - сосредоточено в Санкт-Петербурге.
Новая система ЧПУ с повышенной степенью электронной интеграции «Мини 4CKFF» на основе малогабаритного блока управления (294x356x262 мм) на 5 платомест, модульное и программно совместимое с предыдущими моделями 4СК, обеспечивает управление 6 координатными осями (+2 шпинделя) и имеет 112/64 дискретных входов/выходов.
Система ЧПУ Арта НВП «Арта-Тест» (г. Фрязино Московской обл.) предназначена для управления электроэрозионными станками с количеством управляемых координат до 5 и является дальнейшим развитием производимых в последние годы СЧПУ «Арта» ДАКШ3.035.002.
Производятся как отдельные СЧПУ, так и со встроенным генератором БЭРМ-2М. Система выполнена на базе современной ЭВМ Intel архитектуры с процессором Pentium. Комплектуется собственными серийно выпускаемыми блоками: приводами шаговых двигателей, АЦП, электронным диском со встроенными ПЗУ рабочего ПО и статической памятью для хранения параметров и координат обработки при выключении питания, блоком питания.
Интерфейс оператора с СЧПУ обеспечивают графический цветной 15- дюймовый монитор, выдвижная клавиатура пульта оператора, панель управления (в случае варианта исполнения СЧПУ со встроенным генератором БЭРМ-2М дополняется элементами регулирования и индикации параметров технологических импульсов).
СЧПУ производятся по принципу «разъем в разъем» как для нового оборудования, так и для модернизации ранее изготовленного электроэрозионного и лазерного оборудования.
ООО «Русь Автоматика» (Санкт-Петербург) предлагает универсальные, многофункциональные системы ЧПУ семейства UNIC, базирующиеся на современном промышленном PC компьютере под управлением операционной системы Windows-98 и выше, что делает их максимально адаптируемыми для конкретных нужд потребителя. Система ЧПУ UNIC-23 - хорошее решение для обрабатывающих центров, многофункционального фрезерного и токарного оборудования. Система ЧПУ UNIC-22F,T предназначена для управления простыми фрезерными и токарными станками, применяется в металло- и деревообработке, а также в раскройном оборудовании. Система ЧПУ UNIC-21 - модульная система, позволяющая управлять сложным технологическим оборудованием, технологическими процессами, контролируемыми многочисленными датчиками. Наиболее эффективно используется в легкой и пищевой промышленности.
Система ЧПУ КРТ4-00 НПО КРИСТА (г. Рыбинск) построена на базе компьютера в промышленном исполнении. В состав системы входят: графический дисплей, алфавитно-цифровая и функциональная клавиатура, процессорный блок, платы связи с технологическим оборудованием, источник питания. СЧПУ может быть использована как для модернизации существующего оборудования, так и для применения во вновь разрабатываемых системах. Количество управляемых координат - до 6, управление приводами подач определяется типом привода, тип датчиков положения - инкрементные фотоэлектрические.
Система поддерживает следующие виды интерполяции: линейная - по всем шести координатам одновременно, круговая - по двум любым линейным координатам одновременно, линейно-круговая - по трем любым координатам одновременно, автоматическая коррекция контура на величину радиуса и длину инструмента.
Ввод управляющих программ возможен набором с алфавитно-цифровой клавиатуры СЧПУ (встроен полнофункциональный текстовый редактор), загрузкой ранее введенных программ из внутренней энергонезависимой памяти СЧПУ либо загрузкой с внешнего носителя данных (дискета формата 3,5 дюйма; переносные энергонезависимые модули памяти; компьютерная сеть, витая пара 10 Мбит/с).
Некоторые технические характеристики отдельных систем ЧПУ приведены в таблице.
И все-таки Siemens
Как можно было убедиться, российский рынок систем ЧПУ весьма представителен и насыщен предложениями. Причем практически каждый производитель предлагает от одной-двух до десятка и более моделей и модификаций.
Предложений достаточно много, а что же покупается, каким же системам ЧПУ отдается предпочтение? Разные источники информации сходятся примерно на таких числах: доля продаваемых в России зарубежных систем ЧПУ от 60 до 70%, соответственно, доля отечественной продукции 30-40%. Сходятся источники информации и в том, что безусловным лидером продаж является Siemens (до 90% продаж среди зарубежных систем ЧПУ).
Автор этого материала тоже не избежал соблазна и в свою очередь попытался оценить, какими системами ЧПУ оснащено предлагаемое на российском рынке новое металлообрабатывающее оборудование. Было взято пятьдесят производителей, из которых 34 зарубежных (американских, германских, швейцарских, японских) и 16 российских, таких как питерский «Свердлов», станкозаводы из Стерлитамака и Иванова, московский «Красный пролетарий» и другие. Так вот, из этих пятидесяти: 28 фирм предлагают оборудование, оснащенное системами ЧПУ фирмы Siemens, 15 - GE Fanuc, 8 - Heidenhain, 9 - других иностранных фирм (в том числе и собственных разработок) и 4 - отечественных фирм (сумма не равна 50, т. к. ряд производителей оснащают станки разными системами).
Кроме того, из десяти компаний (как российских, так и иностранных), предлагающих провести модернизацию станочного оборудования, практически все в качестве альтернативы установленным на этом оборудовании системам ЧПУ предлагают продукцию фирмы Siemens.
Таким образом, можно констатировать (наверное, с сожалением, но это так), на российском рынке в настоящее время преобладает продукция фирмы Siemens. Эта компания всегда была лидером в производстве систем ЧПУ, что основано на колоссальном опыте и практически неограниченных инженерных и технологических возможностях. «Слабое место» только одно - по российским понятиям дорого.
В последнее время стало заметным присутствие на российском рынке американских и китайских производителей систем ЧПУ. Но в отличие от Siemens они не имеют широкой сети представительств, способных осуществлять обслуживание, ремонт и консультационные услуги.
С сожалением отмечая отсутствие заинтересованности государства в развитии этой вне всяких сомнений стратегической отрасли, следует отметить, что появление новых предприятий, специализирующихся на выпуске такой продукции, появление новых современных ее образцов, позволяют, тем не менее, смотреть в будущее с осторожным оптимизмом.
Системы ЧПУ первого поколения имели элементную базу на дискретных полупроводниковых элементах (транзисторах). Ввод программы в этих системах осуществлялся на магнитной ленте в унитарном коде или в фазовом виде. Моделями устройств ЧПУ первого поколения являются ПРС1-58, ПРС-ЗК, К-4МИ. В то же время в устройствах ЧПУ первого поколения К2П-67, КЗП-68, УМС-2 ввод программы осуществлялся уже на пятидорожечной перфоленте (код БЦК-5).
Системы ЧПУ второго поколения
Системы ЧПУ второго поколения имели элементную базу малой (серия 155) и средней (серия 176) степени интеграции, с помощью которых осуществлялась схемная реализация алгоритмов управления. К моделям устройств ЧПУ второго поколения можно отнести Н22, НЗЗ, Н55, П-33, «Размер 2». В устройствах ЧПУ второго поколения Н22, НЗЗ ввод программы осуществлялся на восьмидорожечной перфоленте (код ISO 7).
Системы ЧПУ третьего поколения
Системы ЧПУ третьего поколения создавались на базе микроЭВМ («Электроника-60», «Электроника НЦ-03» и др.), БИС (серия 589 и др.). Эти системы ЧПУ имели расширенные технологические возможности, осуществлялась программная реализация алгоритмов управления. К моделям устройств ЧПУ третьего поколения можно отнести 15МП, «Размер 4М», 2С42, 2С85, 2У32, 2МЧЗ, «Электронику НЦ-31». В устройствах ЧПУ третьего поколения ввод программы осуществлялся как на перфоленте, так и с помощью клавиатуры. Системы ЧПУ начинают оснащаться дисплейно-диалоговыми системами задания УП с графическим отображением детали на экране. Появляются оперативные системы ЧПУ, на которых программирование простых деталей может осуществляться непосредственно на станке с использованием типовых циклов.
Системы ЧПУ четвертого поколения
Для систем ЧПУ четвертого поколения характерно блочное мультипроцессорное исполнение. В качестве элементной базы используются специальные БИС и микроЭВМ. Программирование технологических функций и диалоговых режимов осуществляется на языках высокого уровня. К моделям устройств ЧПУ четвертого поколения можно отнести «Электронику МС2101», ЗС100, ЗС200. В устройствах ЧПУ четвертого поколения ввод программы осуществлялся электронной кассетой или кассетой на цифровых магнитных доменах.
Системы ЧПУ пятого поколения
Системы ЧПУ пятого поколения создаются на базе промышленных персональных компьютеров. В этих системах ЧПУ реализуются все современные достижения, свойственные персональным компьютерам, включая языки программирования; программно-математическое обеспечение; системы ввода, хранения и обмена информации; возможность структурного изменения; возможность выполнения функций самонастройки и адаптации и др.
Станки с ЧПУ подразделяются на следующие технологические группы:
- станки токарной группы;
- станки сверлильно-фрезерно-расточной группы;
- станки шлифовальной группы;
- станки зубообрабатывающей группы;
- станки электрофизической группы;
- многоцелевые станки, ОЦ:
По отношению к инструменту
- с ручной сменой инструмента;
- с автоматической сменой инструмента в револьверной головке;
- с автоматической сменой инструмента в магазине.
Станки могут оснащаться разными системами ЧПУ. В зависимости от конфигурации системы управления обозначения металлорежущих станков могут быть следующие:
- Ф1 - станки с цифровой индикацией, в том числе с предварительным набором координат;
- Ф2 - станки с позиционными прямоугольными системами управления координат;
- Ф3 - станки с контурными прямолинейными и криволинейными системами управления координат;
- Ф4 - станки с универсальными системами управления координат для позиционно-контурной обработки.
Для характеристики станков с ЧПУ используют следующие показатели:
- Класс точности станка
- Н - станок нормальной точности
- П - повышенной
- В - высокой
- А - особо высокой
- С - сверхвысокой точности (мастер-станок)
- для патронных станков - наибольший диаметр устанавливаемого изделия над станиной, наибольший диаметр обрабатываемого изделия над станиной;
- для центровых и патронных станков - наибольший диаметр обрабатываемого изделия над суппортом;
- для прутково-токарных станков - наибольший диаметр обрабатываемого прутка;
- для расточно-фрезерных станков - габаритные размеры (длина, ширина) рабочей поверхности стола, диаметр рабочей поверхности круглого поворотного стола;
- для сверлильных станков - наибольший условный диаметр сверления, диаметр выдвигаемого шпинделя и т.д.;
На базе станков с ЧПУ созданы следующие станочные модули и станочные комплексы, предназначенные для автоматизированной обработки деталей (в скобках приведены общепринятые международные обозначения систем):
ГПМ (FMM) - гибкий производственный модуль - единица технологического оборудования с системой автоматической загрузки/выгрузки деталей, локальным накопителем, транспортером деталей и инструмента;
ГАЛ - гибкая автоматическая линия - система, включающая в себя несколько ГПМ, с общими управлением от ЭВМ, транспортной системой и складом заготовок. ЭВМ выполняет функции хранения и передачи к устройству ЧПУ станков управляющих программ, а также осуществляет текущее диспетчирование и оперативное планирование;
ГПС (FMS) - гибкая производственная система - комплекс технологического оборудования и системы управления от ЭВМ, обладающий свойством автоматизированной переналадки;
ГАД (FMF) - гибкий автоматизированный цех - система, включающая в себя несколько ГАЛ и ГПМ с общими транспортной системой, складом, многоуровневой (иерархической) системой управления от ЭВМ;
A3 - автоматический завод - система, состоящая из ГАД, в том числе цеха автоматической сборки и упаковки готовой продукции. Центральная ЭВМ осуществляет управление всеми подразделениями завода и долгосрочное планирование.
Конструкции устройств ЧПУ, систем управления высокого уровня постоянно развиваются и совершенствуются. Появляется новая элементная база, расширяются технологические возможности, повышаются степень автоматизации, производительность и точность обработки. Поэтому в пособии приводятся сведения о перспективах развития систем управления и новых требованиях к профессии оператора станков с ЧПУ.
Системы ЧПУ. Термины и понятия
Металлообрабатывающим оборудованием с программным управлением называют любые виды станков для обработки металлов резанием, например токарные, фрезерные, сверлильные, шлифовальные, расточные, многоцелевые, электроэрозионные и т.п., а также другие виды оборудования для обработки металлов (листогибочные машины, дыропробивные прессы и др.), осуществляющие по заданной программе автоматическую обработку заготовок.
Управляющая программа (УП) - совокупность команд на языке программирования, соответствующая алгоритму функционирования станка по обработке конкретной заготовки.
Числовое программное управление станков - управление обработкой заготовки на станке по УП, в которой данные об обработке заданы в цифровом коде.
Программоноситель - носитель геометрических и технологических данных, на котором записана УП. В качестве носителя данных применяются бумажная или пластиковая перфолента, магнитная лента, магнитные диски, запоминающие устройства разных видов и типов.
Геометрическая информация - информация, описывающая форму, размеры элементов детали и инструмента, их взаимное расположение на столе станка.
Технологическая информация - информация, описывающая технологические характеристики детали и условия ее обработки.
Кадр УП - составляющая часть программы, вводимая и отрабатываемая как единое целое и содержащая не менее одной команды.
Покадровая работа - функционирование устройства ЧПУ, при котором отработка каждого кадра УП происходит после воздействия оператора.
Работа устройства ЧПУ с ручным вводом данных - функционирование устройства ЧПУ, при котором набор данных, ограниченный форматом кадра, выполняется вручную оператором на пульте станка.
Работа устройства ЧПУ с ручным управлением - функционирование устройства ЧПУ, при котором оператор управляет станком с пульта без использования числовых данных.
Зеркальная обработка - функционирование устройства ЧПУ, при котором рабочие органы перемещаются по траектории, представляющей собой зеркальное отображение траектории, записанной в УП.
Ввод УП - ввод данных в память устройства ЧПУ с программоносителя от ЭВМ верхнего ранга или с пульта оператора.
Групповое ЧПУ станками - числовое управление группой станков от ЭВМ, имеющей общую память для хранения программ, распределяемых по запросам от станков.
Нулевая тонка станка - точка на узле станка, принятая за начало отсчета системы координат станка.
Координата - величина, определяющая положение точки в пространстве по отношению к заданной базе или началу отсчета.
Исходная точка станка - точка на узле станка, определенная относительно нулевой точки станка и используемая для начала работы по УП.
Фиксированная точка станка - точка, определенная относительно нулевой точки станка и используемая для определения положения рабочего органа.
Точка начала обработки - точка, определяющая начало обработки конкретной заготовки.
Плавающий нуль - возможность перемещения посредством устройства ЧПУ начала отсчета перемещения рабочего органа в любое положение относительно нулевой точки.
Дискретность задания перемещения - минимальное перемещение рабочего органа (линейное или на угол поворота), которое может быть задано в УП.
Дискретность отработки перемещения - минимальное перемещение или минимальный угол поворота рабочего органа, контролируемые в процессе управления.
Максимальное программируемое перемещение - наибольшее перемещение рабочего органа, которое может быть задано в одном кадре УП.
Контурная скорость - результирующая скорость подачи рабочего органа, направление которой совпадает с направлением касательной в каждой точке заданного контура обработки.
Коррекция положения инструмента - изменение с пульта управления запрограммированных координат рабочего органа станка.
Коррекция скорости подачи - изменение с пульта оператора запрограммированного значения скорости подачи.
Коррекция скорости главного движения - изменение с пульта оператора запрограммированной частоты вращения главного привода.
Отказ устройства ЧПУ - событие, заключающееся в нарушении работоспособности устройства ЧПУ.
Сбой устройства ЧПУ - событие, заключающееся в кратковременном самоустраняющемся нарушении работоспособности устройства ЧПУ.
Индикатируемый сбой устройства ЧПУ - сбой, фиксирующийся на пульте в момент его возникновения, приводящий к останову станка, т.е. к прекращению обработки детали, информация о котором высвечивается на пульте оператора.
Неиндикатируемый сбой устройства ЧПУ - сбой, не обнаруживаемый на пульте в момент его возникновения.
Станочная система ЧПУ - комплекс узлов и агрегатов, взаимодействующих между собой.
Типовой элемент замены устройства ЧПУ (ТЭЗ УЧПУ) - типовая минимальная составляющая часть устройства ЧПУ, которая при потере работоспособности может быть заменена аналогичной. Каждое устройство ЧПУ выдает управляющее воздействие на исполнительные органы в соответствии с УП и информацией о положении управляемого объекта.
Классификация систем ЧПУ
Отечественная классификация систем ЧПУ
Классификацию систем ЧПУ, применяемых в отечественном машиностроении, проводят по виду рабочих движений. Различают позиционные и контурные устройства ЧПУ.
Позиционные устройства ЧПУ - устройства, в которых рабочие органы могут перемещаться в заданные точки, а траектория перемещения от точки до точки задается только прямолинейным движением. Позиционные устройства ЧПУ составляют группу устройств, имеющих один общий признак - позиционирование, т.е. обеспечение точности останова перемещаемых рабочих органов в точке с заданными координатами. Скорость перемещения в позиционных устройствах не программируется и обусловлена только динамикой приводов станка. Позиционными устройствами ЧПУ оснащают сверлильные, координатно-расточные, токарные, фрезерные, шлифовальные и другие станки, работающие по прямоугольному циклу.
Контурные прямоугольные (коллинеарные) устройства ЧПУ - устройства, которые обеспечивают движение по одной координате. Так как в большинстве станков применяют прямоугольную систему координат, такие устройства получили название прямоугольных. В этих устройствах, так же, как и в позиционных, программируются конечные координаты перемещения, однако в УП задается скорость движения рабочего органа в соответствии с заданным режимом резания, и перемещение выполняется поочередно по каждой из координатных осей. Прямоугольные устройства ЧПУ применяют в станках фрезерной, токарной и шлифовальной групп.
Контурные (непрерывные) устройства ЧПУ - устройства, обеспечивающие перемещение рабочих органов из данной точки пространства по траектории, форма и конечные координаты которой заданы в УП. Контурными устройствами ЧПУ оснащают станки фрезерной и токарной групп, осуществляющих формообразование деталей сложной формы.
Устройства адаптивного (самоприспосабливающегося) управления ЧПУ - устройства, в которых обеспечивается автоматическое приспособление процесса обработки к изменяющимся условиям обработки по определенным критериям (скорость резания, подача, сила резания). Самоприспосабливающиеся устройства ЧПУ имеют систему контроля и регулирования, позволяющую осуществлять защиту от перегрузок двигателей главного движения и приводов подач, что обеспечивает высокое качество обработки и защищает станочную систему от поломок. Адаптивными устройствами ЧПУ оснащают фрезерные, расточные и многоцелевые станки.
Оперативная система управления (ОСУ) - устройство ЧПУ на базе микроЭВМ с подготовкой УП у станка в режиме диалога оператора с устройством ЧПУ. Оператор с помощью клавиатуры пульта устройства ЧПУ вводит данные с чертежа детали в программу управления. Оперативными устройствами ЧПУ оснащают токарные и фрезерные станки.
Другим признаком, по которому устройства ЧПУ могут быть классифицированы, является число потоков информации, циркулирующих в системе станок-устройство ЧПУ.
Система с разомкнутым контуром - устройство ЧПУ, в котором имеется только один поток информации. В таких системах отсутствуют измерительные устройства (датчики обратной связи), контролирующие перемещение рабочих органов. Точность воспроизведения движения рабочих органов с такой системой невысока и определяется точностью отработки команд двигателем привода подач и точностью кинематической цепи, передающей движение рабочему органу.
Система с замкнутым контуром - устройство ЧПУ, в котором существуют два потока информации: один вводится в устройство управления через вводное устройство от программоносителя, а другой - в устройство ЧПУ от датчиков обратной связи, определяющих действительное положение рабочих органов. При наличии рассогласования между этими потоками устройство управления воздействует на приводы подач, последние перемещают рабочие органы в нужном направлении, изменяя рассогласование до величины, близкой к нулю.
Международная классификация систем ЧПУ
В соответствии с международной классификацией все ЧПУ по уровню технических возможностей делятся на следующие классы: Различают устройства ЧПУ с постоянной (класс NC) и переменной (класс CNC) структурой.
Устройство ЧПУ класса NC (Numerical Control) основано на принципе вычислительного устройства, где все операции, составляющие алгоритм работы, выполняются параллельно с помощью отдельных цепей или устройств, реализующих ту или иную функцию (агрегатно-блочное построение). Эти устройства называют также устройствами ЧПУ с жесткой структурой. Базовые модели таких устройств (Н22 и НЗЗ) содержат микроэлектронику и при их использовании вмешательство оператора в процесс обработки весьма ограничено.
Системы ЧПУ класса NC осуществляют покадровое чтение перфоленты на протяжении цикла обработки каждой заготовки
Системы класса NC наиболее распространены. Они работают в следующем режиме. После включения станка система ЧПУ читает первый и второй кадры программы. Как только закончилось их чтение, станок начинает выполнять команды первого кадра. В это время информация второго кадра программы находится в запоминающем устройстве системы ЧПУ. После выполнения первого кадра станок начинает отрабатывать второй кадр, который выводится из запоминающего устройства. В процессе отработки станком второго кадра система читает третий кадр программы, который вводится в освободившееся от информации второго кадра запоминающее устройство
Основным недостатком рассмотренного режима работы является то, что для обработки каждой следующей заготовки из партии системе ЧПУ приходится вновь читать все кадры перфоленты. В то же время в процессе чтения перфоленты нередко возникают сбои из-за недостаточно надежной работы считывающих устройств УЧПУ. В результате отдельные детали из партии могут оказаться бракованными. Повышенная вероятность сбоев в системах класса NC объясняется также очень большим числом кадров перфоленты, поскольку для работы таких систем в программе должно быть записано каждое элементарное действие станка. Кроме того, при таком режиме работы перфолента быстро изнашивается и загрязняется, что еще более увеличивает вероятность сбоев при чтении. Наконец, если в кадре записаны действия, которые станок выполняет очень быстро, то ЧПУ за это время может не успеть прочитать следующий кадр, что также ведет к сбоям.
Устройство ЧПУ класса CNC (Computer Numerical Control (с переменной структурой) соответствует структуре управляющей ЭВМ, включающей в себя вычислительное устройство (процессор), блоки памяти и блоки ввода-вывода информации. При этом объем функций, характер проводимых операций и их последовательность определяются программами функционирования, которые введены в блок памяти.
Системы класса CNC имеют большие возможности из-за наличия в них мини-ЭВМ на основе микропроцессоров. В запоминающее устройство системы программа может быть введена не только полностью с подготовленной перфоленты, но и отдельными кадрами вручную с пульта УЧПУ. В кадрах программы могут записываться как команды на отдельные движения рабочих органов, так и команды, задающие целые группы движений, называемые постоянными циклами, которые хранятся в запоминающем устройстве СЧПУ. Это приводит к резкому уменьшению числа кадров программы и к соответствующему повышению надежности работы станка. Системы класса CNC позволяют достаточно просто в режиме диалога при отладке программ осуществлять редактирование с ручным вводом информации и с выводом ее на дисплей, а также получать откорректированную и отработанную программу на перфоленте.
Ряд систем класса CNC (или близких к нему) делают возможной работу по одной программе в различных масштабах, в режиме «матрица - пуансон», в режиме зеркального отображения и т. д. Системы допускают введение в процессе работы самых различных видов коррекций.
Обладая сравнительно низкой стоимостью, малыми габаритными размерами и высокой надежностью, системы ЧПУ на микропроцессорах позволяют заложить в систему управления новые свойства, которые раньше не могли быть реализованы. Так, например, устройство ЧПУ «Электроника НЦ-31» имеет математическое обеспечение, позволяющее учитывать и автоматически корректировать постоянные погрешности станка и тем самым влиять на совокупность причин, определяющих точность обработки. Простейшим видом этих функций системы является компенсация люфта или зоны нечувствительности приводов в направлении перемещения по координатам. Надежность и работоспособность станков с устройствами ЧПУ на микропроцессорах повышает использование систем контроля и диагностики. Функции этих систем можно разделить на контроль состояния внешних по отношению к УЧПУ устройств, проверку внутренних блоков и контроль собственно УЧПУ. Так, например, то же устройство «Электроника НЦ-31» для токарных станков имеет специальные тест-программы для проверки работоспособности всех структурных частей системы. Эти тест-программы отрабатываются при каждом включении устройства, и в случае исправности всех частей возникает сигнал готовности системы к работе. В процессе работы станка и УЧПУ тест-программы частями отрабатываются в так называемом фоновом режиме, не мешая отработке основной управляющей программы. В случае появления неисправности на табло световой индикации возникает ее код, с помощью которого по таблице устанавливают место и причину неисправности. Кроме того, система определяет ошибки, связанные с неправильной эксплуатацией устройства, с превышением параметров теплового режима, дает величину напряжения для питания и другие параметры.
Устройства класса CNC расширяют функциональные возможности программного управления: появляются функции, которые раньше не могли быть реализованы: хранение УП и ее редактирование на рабочем месте, расширение возможности индикации на дисплее, диалоговое общение с оператором, широкие возможности коррекции, в том числе и погрешностей станка, система диагностики неисправностей, возможность изменения программным способом функций системы управления при ее эксплуатации, реализация функций электроавтоматики и др.
Кроме того существуют системы ЧПУ других классов:
SNC (Stored Numerical Control) - системы ЧПУ с однократным чтением всей перфоленты перед обработкой партии одинаковых заготовок;
ЧПУ класса SNC лишены недостатков систем класса NC, они последовательно, кадр за кадром, считывают всю программу и размещают информацию в своем запоминающем устройстве большой емкости (16 килобайт и более). Перфолента читается только один раз, перед обработкой всей партии одинаковых деталей, и поэтому мало изнашивается. Управление обработкой всех заготовок осуществляется по сигналам из запоминающего устройства, что резко уменьшает вероятность сбоев, а следовательно, и брак деталей. Системы SNC позволяют осуществлять однократный ввод управляющих программ при длине перфоленты от 40 до 310 м.
DNC (Direct Numerical Control) - системы прямого числового управления группами станков от одной ЭВМ;
Создание и применение систем класса DNC связана с общей тенденцией развития современных комплексно-автоматизированных производств. В таких производствах управление работой участков, состоящих из станков с ЧПУ, транспортно-складирующих, загрузочных средств, осуществляется от центральной вычислительной машины. Однако наличие центральной ЭВМ не означает, что необходимость в устройствах ЧПУ у станков при этом полностью отпадает. В одном из наиболее распространенное вариантов построения систем DNC каждый вид оборудования на участке сохраняет свои системы ЧПУ классов NC, SNC, CNC. Нормальным для такого участка является режим работы, при котором управляющие команды на УЧПУ всех видов оборудования подаются по проводам непосредственно от ЭВМ, минуя считывающие устройства. Это приводит к повышению надежности работы каждой единицы оборудования и всего участка в целом. Одновременно автоматизируется процесс подготовки УП с помощью ЭВМ. Вместе с тем в условиях временного выхода из строя вычислительной машины такой участок сохраняет работоспособность, поскольку каждый вид оборудования может paботать от перфоленты, подготовленной заранее на случай аварийной ситуации.
HNC (Handled Numerical Control) - оперативные системы ЧПУ с ручным набором программ на пульте управления.
Подготовка и отладка управляющих программ - процесс длительный и трудоемкий. При изготовлении простых по конфигурации деталей целесообразно было бы исключить этот процесс. Такая возможность на современных станках в принципе имеется. Она реализуется при использовании режима ручного ввода данных. Однако у большинства станков в этом режиме возможен ввод с пульта только одного кадра программы с последующей его отработкой на станке. Это слишком непроизводительно. Поэтому в последнее время разработаны так называемые оперативные системы числового программного управления класса HNC с ручным вводом программ с пульта УЧПУ. Программа из достаточно большого числа кадров легко набирается и исправляется с помощью клавиш или переключателей на пульте УЧПУ. После отладки программа фиксируется до окончания обработки партии одинаковых заготовок. Системы класса HNC обеспечивают как позиционное, так и контурное управление станками.
Список литературы
- ГОСТ Р 50369-92. Электроприводы. Термины и определения. - М.: Изд-во стандартов, 1993. - 16 с.
- Завгороднев П. И. Работа оператора на станках с программным управлением: учеб. пособие для техн. училищ / П. И. Завгороднев. - М. : Высш. шк., 1981. - 136 с.
- Программное управление станками и промышленными роботами: учебник / [В.Л.Косовский, Ю.Г.Козырев, А.Н.Ковшов и др.]. - М. : Высш. шк., 1989. - 272 с.
- Сергиевский Л. В. Пособие наладчика станков с ЧПУ / Л. В. Сергиевский, В.В.Русланов. - М.: Машиностроение, 1991. - 176 с.
- Соломенцев Ю. Н. Управление гибкими производственными система ми / Ю. Н. Соломенцев, В.Л.Сосонкин. - М.: Машиностроение, 1988. - 552 с.
- Сосонкин В. Л. Микропроцессорные системы числового программного управления станками / В.Л. Сосонкин. - М. : Машиностроение, 1985. - 288 с.
- Черпаков Б. И. Металлорежущие станки: Учебник для нач. проф. образования / Б. И. Черпаков, Т. А. Альперович. - М.: Издательский центр «Академия», 2004. - 368 с.
- Числовое программное управление станками / [В.Л. Сосонкин, О. П. Михайлев, Ю. А Павлов и др.]; под ред. В. Л. Сосонкина. - М.: Машиностроение, 1981. - 398 с.
- Чудаков АЛ. Проектирование систем управления станками и ста ночными комплексами: гл. 1.8 // Машиностроение: энциклопедия. Т. FV-7. Металлорежущие станки и деревообрабатывающее оборудование. - М.: Машиностроение, 19
Босинзон М.А. Современные системы ЧПУ и их эксплуатация: учебник для нач. проф. образования / М. А. Босинзон; под ред. Б. И.Черпакова. - 2-е изд., стер. - М.: Издательский центр «Академия», 2008. - 192 с. ISBN 978-5-7695-5184-0
Основные принципы числового программного управления
Развитие электроники и вычислительной техники, внедрение в производство ЭВМ привело к разработке и широкому применению в станкостроении систем числового программного управления (ЧПУ) металлорежущими станками, а также другим технологическим оборудованием.
Числовым программным управлением металлорежущими станками называют управление по программе, заданной в алфавитно–цифровом коде и представляющей последовательность команд, записанную на определенном языке и обеспечивающую заданное функционирование рабочих органов станка.
Принципиальное отличие систем ЧПУ от ранее рассмотренных САУ заключается в способе расчета и задания программы управления и ее передачи для управления рабочими органами станка. Информация чертежа детали представлена в аналогово-цифровом виде, то есть в виде чисел, различных словесных указаний, условных знаков и других символов, имеющих ограниченное число значений, каждое из которых имеет вполне определенную и однозначную информацию.
В обычных САУ программа управления воплощается в физические аналоги – кулачки, копиры, упоры, кондукторные плиты и другие средства, которые являются программоносителями. Данный способ задания программы управления имеет два основных недостатка.
Первый вызван тем, что информация чертежа детали из цифровой (дискретной) и однозначной превращается в аналоговую (в виде кривых кулачка, копира). Это приводит к погрешностям, вносимым при изготовлении кулачков, копиров, расстановки путевых упоров на линейках, а также при износе этих программоносителей в процессе эксплуатации. Вторым недостатком является необходимость изготовления данных программоносителей с последующей трудоемкой наладкой на станке. Это приводит к большим затратам средств и времени и делает в большинстве случаев неэффективным применение обычных САУ для автоматизации серийного и особенно мелкосерийного производства.
При подготовке программ управления для станков с ЧПУ вплоть до ее передачи рабочим органам станка, мы имеем дело с информацией в дискретной форме, полученной непосредственно из чертежа детали.
Траектория движения режущего инструмента относительно обработанной заготовки в станках с ЧПУ представляется в виде ряда его последовательных положений, каждое из которых определяется числом. В станках с ЧПУ возможно получить сложные движения рабочих органов не с помощью кинематических связей, а благодаря управлению независимыми координатными перемещениями этих рабочих органов по программе, заданной в числовом виде. Качественно новым в станках с ЧПУ является возможность увеличения числа одновременно управляемых координат, что позволило создать принципиально новые компоновки станков с получением широких технологических возможностей при автоматическом управлении.
Программа управления может быть рассчитана с любой заданной точностью и на любой требуемый закон движения рабочих органов станка. Получает все более широкое применение управление станками непосредственно от ЭВМ.
Классификация систем ЧПУ
Системы ЧПУ можно классифицировать по различным признакам.
I. Исходя из технологических задач управления обработкой все системы ЧПУ делят на три группы: позиционные, контурные и комбинированные.
Позиционные системы ЧПУ обеспечивают управление перемещениями рабочих органов станка в соответствии с командами, определяющими позиции, заданные программой управления. При этом перемещения вдоль различных осей координат могут выполняться одновременно (при заданной постоянной скорости) или последовательно. Данными системами оснащают в основном сверлильные и расточные станки для обработки деталей типа плит, фланцев, крышек и др., в которых производится сверление, зенкерование, растачивание отверстий, нарезание резьбы и др.
Контурные системы ЧПУ обеспечивают управление перемещениями рабочих органов станка по траектории и с контурной скоростью, заданными программой управления. Контурной скоростью является результирующая скорость подачи рабочего органа станка, направление которой совпадает с направлением касательной в каждой точке заданного контура обработки. Контурные системы ЧПУ в отличие от позиционных обеспечивают непрерывное управление перемещениями инструмента или заготовки поочередно или сразу по нескольким координатам, в результате чего может обеспечиваться обработка очень сложных деталей (с управлением одновременно по более чем двум координатам). Контурными системами ЧПУ оснащены в основном токарные и фрезерные станки.
Комбинированные системы ЧПУ , сочетающие функции позиционных и контурных систем ЧПУ, являются наиболее сложными, но и более универсальными. В связи с усложнением станков с ЧПУ (особенно многооперационных) расширением их технологических возможностей и повышением степени автоматизации применение комбинированных систем ЧПУ значительно расширяется.
II. По наличию обратной связи все системы ЧПУ делятся на две группы: разомкнутые и замкнутые.
Замкнутые системы ЧПУ в свою очередь могут быть:
1) с обратной связью по положению рабочих органов станка; 2) с обратной связью по положению рабочих органов и с компенсацией погрешностей станка; 3) самоприспособляющиеся (адаптивные).
Разомкнутые системы ЧПУ строятся на основе силовых или шаговых двигателей (ШД). В последнем случае ШД применяется обычно в комплекте с гидроусилителем.
III. Классификация в зависимости от уровня электронной техники .
Несмотря на относительно малый срок применения систем ЧПУ, они в своем развитии уже прошли несколько этапов, определяемых уровнем развития электронной техники.
Применяемые в настоящее время в промышленности системы ЧПУ класса NC построены по принципу цифровой модели. В этой системе программа (на перфоленте) вводится в интерполятор 3, далее переработанная
программа вводится в систему управления 2 станком 1. Данные системы ЧПУ называют системами с жесткой программой. Весьма ограничены на этих системах возможности вмешательства оператора в процесс обработки программы.
В системах класса SNC устройство для считывания программы управления применяют только один раз – для ввода программы управления в
запоминающий блок 4 (памяти). В результате повышается надежность работы станка по причинам отказа фотосчитывающего устройства.
Особенностью систем управления класса CNC является их структура, соответствующая структуре управляющей ЭВМ. С появлением систем класса CNC расширились функциональные возможности программного управления,
в том числе хранение программы управления и ее редактирование непосредственно на рабочем месте, расширенные возможности индикации на дисплее, диалоговое общение с оператором и т.д. Ввод программы управления может быть осуществлен на перфоленте или вручную. Второй тип систем получил название систем класса HNC . Программа управления здесь вводится оператором с помощью клавиатуры и хранится в памяти системы.
Наряду с автономными системами ЧПУ в промышленности применяют системы прямого числового программного управления группой различных станков от единой ЭВМ, получившие название систем класса DNC .
В этой системе средняя или большая ЭВМ (3) подготавливает программы для нескольких станков с ЧПУ и передает их системам CNC (2) отдельных станков (1). В следствии весьма высокого быстродействия ЭВМ, система осуществляет подготовку программ для всех станков , , группы. ЭВМ выполняет также и дополнительные функции по управлению полуавтоматом, например, управляет автоматизированным транспортом и складом. Непосредственное управление станками осуществляют мини ЭВМ с небольшим объемом оперативной памяти, входящие в состав отдельных систем CNC.
Типовая структурная схема системы ЧПУ
На рисунке показана общая укрупненная структурная схема системы ЧПУ. Она включает следующие основные элементы: устройство ЧПУ; приводы подач рабочих органов станка и датчики обратной связи (ДОС), установленные по каждой управляемой координате. Устройство ЧПУ предназначено для выдачи управляющих воздействий рабочим органом станка в соответствии с программой управления, вводимой на перфоленте. Программа управления считывается последовательно в пределах одного кадра с запоминанием в блоке памяти, откуда она подается в блоки технологических команд, интерполяции и скоростей подач. Блок интерполяции – специализированное вычислительное устройство (интерполятор) – формулирует частичную траекторию движения инструмента между двумя или более заданными в программе управления точками. Выходная информация с этого блока поступает в блок управления приводами подач, обычно представлена в виде последовательности импульсов по каждой координате, частота которых определяет скорость подачи, а число – величину перемещения.
Блок ввода и считывания информации предназначен для ввода и считывания с перфоленты программы управления. Считывание производится последовательно строка за строкой в пределах одного кадра при периодическом протягивании перфоленты перед фотосчитывателем, содержащим фотосчитывающую головку 11 с фотопреобразователями, и осветитель,
состоящий из лампы накаливания 3 и линзы 4. Восемь фотопреобразователей обеспечивают считывание информации, а два используются для формирования синхроимпульса по отверстиям транспортной дорожки. В других устройствах применяют еще один фотопреобразователь, устанавливаемый по краю перфоленты для контроля ее обрыва.
Протягивание перфоленты 9 производится приводным роликом 7, к которому она поджимается роликом 10, при включении электромагнита протяжки (ЭМП) и притягивания якоря 6. Приводной ролик 7 вращается электродвигателем 8. При протягивании перфоленты для ее натяжения и плотного прилегания к фотосчитывающей головке 11 она подтормаживается тормозом 1 и прижимается к головке 11 прижимом 5, который при заправке перфоленты отводится рычагом 2. После считывания информации одного кадра перфолента останавливается включением тормоза ЭМТ и отключения электромагнита ЭМП. Синхронизация их работы осуществляется управляющим триггером (ТГ).
Имеются модификации устройства ввода.
Блок памяти. Так как информация с перфоленты считывается последовательно, а используется вся сразу в пределах одного кадра, при считывании она запоминается в блоке памяти. Здесь же производится ее контроль и формирование сигнала при обнаружении ошибки в перфоленте. Так как обработка информации идет последовательно по кадрам, а время считывания информации одного кадра равно примерно 0,1 – 0,2 с, получается разрыв в передачи информации, что недопустимо. Поэтому применяют два блока памяти. Пока обрабатывается информация одного кадра из первого блока памяти, производится считывание с перфоленты второго кадра и ее запоминание во втором блоке. Время же введения информации из блока памяти в блок интерполяции ничтожно мало. Во многих системах ЧПУ блок памяти может принимать информацию, минуя блок ввода и считывание непосредственно от ЭВМ.
Блок интерполяции. Это специализированное вычислительное устройство, которое формирует частичную траекторию движения инструмента между двумя или более заданными в программе управления точками. Это важнейший блок в контурных системах ЧПУ. Основой блока является интерполятор, который по заданным программой управления числовым параметрам участка контура восстанавливает функцию f(x,y). В интервалах значений координат Х и У интерполятор вычисляет значения координат промежуточных точек этой функции.
На выходах интерполятора формируется строго синхронизированные во времени управляющие импульсы для перемещения рабочего органа станка по соответствующим осям координат.
Применяют линейные и линейно – круговые интерполяторы. В соответствии с этим первые производят линейную интерполяцию, а вторые линейную и круговую.
Линейный интерполятор обеспечивает, например, перемещение рабочего органа с фрезой диаметром между двумя опорными точками по прямой линии с отклонением от заданного контура на величину .
В этом случае исходной информацией для интерполятора являются величины приращений по координатам и и время обработки перемещения по прямой , т.е. , где S – установленная скорость подачи инструмента.
Работа линейно – кругового интерполятора может осуществляться по методу оценочной функции F. Метод заключается в том, что при выработке очередного управляющего импульса логическая схема производит оценку, по какой координате следует выдавать этот импульс, чтобы суммарное перемещение рабочего органа станка максимально приближало его к заданному контуру.
Интерполируемая прямая (см. рис. а) делит плоскость, в которой она расположена, на две области: над прямой, где оценочная функция F>0, и под прямой, где F<0. Все точки, лежащие теоретически заданной линии, имеют F=0.
Траектория интерполяции представляет собой определенную последовательность элементарных перемещений вдоль координатных осей от начальной точки с координатами и до конечной точки с координатами , .
Если промежуточная точка траектории находится в области F>0, то следующий шаг делается по оси Х. Если же промежуточная точка находится в области F<0, шаг делается по оси Y. Аналогично происходит работа интерполятора при круговой интерполяции (см. рис. б).
Блок управления приводами подачи. С блока интерполяции информация поступает на блок управления приводами подач, который преобразует ее в форму, пригодную для управления приводами подач. Последнее производится так, чтобы при поступлении каждого импульса рабочий орган станка перемещался на определенную величину, характеризующую дискретность системы ЧПУ. При поступлении каждого импульса управляемый объект перемещается на определенную величину, называемую ценой импульса, которая обычно равна 0,01 – 0,02 мм. В зависимости от типа привода (замкнутые или разомкнутые, фазовые или амплитудные), применяемых на станках, блоки управления существенно различаются. В замкнутых приводах фазового типа, использующих датчики обратной связи в виде вращающихся трансформаторов, работающих в режиме фазовращателей, блоки управления представляют собой преобразователи импульсов в фазу переменного тока и фазовые дискриминаторы, которые сравнивают фазу сигнала на выходе фазового преобразователя с фазой датчика обратной связи и выдают разностный сигнал ошибки на усилитель мощности привода.
Блок скоростей подач – обеспечивает заданную скорость подачи вдоль контура, а также процессы разгона и торможения в начале и в конце участков обработки по заданному закону, чаще всего линейному, иногда экспоненциальному. Помимо рабочих подач (0,5 – 3000 мм/мин) этот блок обеспечивает, как правило, и холостой ход с повышенной скоростью (5000 – 20000 мм/мин).
Пульт управления и индикации. Связь оператора с системой ЧПУ производится через пульт управления и индикации. С помощью этого пульта производится пуск и останов системы ЧПУ, переключение режима работы с автоматического на ручной и т.д., а также коррекция скорости подачи и размеров инструментов и изменения начального положения инструмента по всем или некоторым координатам. На этом пульте находятся световая сигнализация и цифровая индикация.
Блок коррекции программы применяется для изменения запрограммированных параметров обработки: скорости подачи и размеров инструмента (длины и диаметра).
Блок постоянных циклов служит для упрощения процесса программирования при обработке повторяющихся элементов детали (например, сверление и растачивание отверстий, нарезание резьбы и др.) применяют блок постоянных циклов. Например, на перфоленте не программируются такие движения, как быстрый вывод из готового отверстия – это заложено в соответствующем цикле (G81).
Блок технологических команд обеспечивает управление циклом работы станка (его цикловой автоматики), включающего поиск и анализ режущего инструмента, переключение частоты вращения шпинделя, зажим и разжим перемещающихся рабочих органов станка, различные блокировки.
Блок питания обеспечивает питание необходимыми постоянными напряжениями и токами всех блоков ЧПУ от обычной трехфазной сети. Особенностью этого блока является наличие стабилизаторов напряжения и фильтров, защищающие электронные схемы ЧПУ от помех, всегда имеющих место в промышленных силовых сетях.
Датчики обратной связи (ДОС)
ДОС предназначены для преобразования линейных перемещений рабочего органа станка в электрические сигналы, содержащие информацию о направлении и величине перемещений.
Все многообразие ДОС можно условно разделить на угловые (круговые) и линейные. Круговые ДОС обычно преобразуют угол поворота ходового винта или перемещения рабочего органа станка через реечную передачу. Преимуществом круговых ДОС является их независимость от длины перемещения рабочего органа станка, удобство установки на станке и удобство эксплуатации. К недостаткам следует отнести принцип косвенного измерения величины перемещения рабочего органа, а следовательно погрешность измерения.
Линейные ДОС непосредственно измеряют перемещения рабочего органа, что является их основным преимуществом по сравнению с круговыми ДОС. Недостатком линейных ДОС является зависимость их габаритных размеров от величины перемещения рабочего органа, кроме того они сложны при установке и эксплуатации станка.
По принципу действия ДОС могут быть импульсными, фазовыми, кодовыми, фазоимпульсными и т.д. Наиболее часто применяют датчики типа индуктосина, которые могут быть круговыми и линейными, а также резольверы.
Линейный индуктосин состоит из линейки 1 и ползуна 2. Длина линейки несколько превышает величину измеряемого перемещения, линейка имеет одну печатную обмотку с шагом 2 мм, с которой снимается индуцируемое напряжение . Она может быть цельной (при небольшой длине хода) или сборной из нескольких пластин (длиной по 250 мм). Ползун установлен на рабочем органе и перемещается относительно линейки. Он имеет две печатные обмотки, сдвинутые на ¼ шага. На каждую обмотку подается переменный ток частотой 10 кГц, причем на первой обмотке напряжение , а на второй
, где - заданный угол смещения.
При перемещении ползуна 2 на выходе обмотки линейки 1 индуцируется напряжение
где - фактический угол смещения, отображающий фактическое перемещение рабочего органа, т.е.
Если рабочий орган находится в заданном положении, , напряжение на выходе обмотки линейки равно нулю. При отсутствии этого равенства на привод подачи поступает сигнал на дальнейшее перемещение.
Широкое применение в станках с ЧПУ находят ДОС типа вращающегося трансформатора (ВТ).
Они представляют собой двухфазные электрические машины переменного тока, у которых при вращении ротора взаимная индукция между обмотками статора 2 и ротора 1 изменяется синусоидально с высокой точностью. На обмотку (а) статора подается напряжение , а на обмотку (б) - , где - угол смещения, отражающий заданную величину перемещения. С обмотки ротора 1 снимается напряжение . Число обмоток в ВТ может быть различным, однако чаще всего применяют ВТ с двумя взаимно перпендикулярными обмотками на статоре и на роторе. Такие синусно – косинусные ВТ называют резольверами.
В позиционных системах ЧПУ применяются кодовые датчики обратной связи с измерением абсолютной величины перемещения рабочего органа. В качестве такого датчика использован, например, кодовый диск кругового фотоэлектрического датчика на десять двоичных разрядов.
Каждое концентрическое кольцо стеклянного диска состоит из затемненных и прозрачных участков, которые не пропускают или пропускают свет на фотоприемники. Кольца соответствуют определенным разрядам: внешнее – первому, внутреннее – десятому. Диск устанавливается так, чтобы его полный оборот соответствовал перемещению рабочего органа на максимальную величину. При этом каждому положению рабочего органа соответствует единственная комбинация (кодовая).
На рисунке показана схема импульсного линейного датчика с неподвижной дифракционной решеткой 1, относительно которой перемещается подвижная вспомогательная шкала 2. Она повернута относительно основной решетки на угол , поэтому при ее перемещении на величину образуются перемещаемые в вертикальном направлении муаровые полосы (3), которые периодически перекрывают пучок света (4), пропускаемый через решетку на два фотоэлемента. При перемещении вспомогательной шкалы 2 на 1 шаг штрихов с фотоэлементов поступает один импульс.
Общие принципы кодирования программы
В станках с ЧПУ все элементы программы: направление, величина и скорости заданных рабочих и вспомогательных перемещений и т.п. задаются в цифровой форме – в виде чисел, расположенных в определенном порядке и записанных определенным образом с помощью какого либо кода. Код представляет собой условную запись числа или действия, позволяющую достаточно простым способом получить изображение этого числа в форме удобной для использования в системах ПУ. В общем случае всякий код, применяемый в системах программного управления, складывается из двух основных элементов: кода перемещения и кода вспомогательных команд. Существует много разнообразных способов кодирования.
Унитарный код. Сущность этого кода заключается в том, что в нем всякое число выражается одним знаком 1. Для изображения любого числа надо столько раз последовательно повторить этот знак, сколько в данном числе содержится единиц. При использовании в качестве программоносителя – перфоленты, знак 1 выражается пробивкой отверстия, а при магнитной ленте – магнитного штриха. Главный недостаток – низкая плотность записи.
Десятичная система счисления использует для записи чисел десять знаков 0 – 9. Для записи чисел в десятичной системе счисления каждому знаку должна быть отведена своя дорожка, а каждому разряду – строка. Запись чисел в десятичном коде громоздка.
Двоичная система счисления использует для записи только два знака 0 и 1. Для записи числа в двоичном коде единица соответствует наличию сигнала, а при нуле сигнал отсутствует. Это удобно, потому что механизмы наиболее надежно различают два устойчивых состояния. Например, на перфоленте: есть пробивка, нет пробивки. ;
Для обеспечения применения кодов, используемых в станках с ЧПУ, проведена унификация языков программирования в широких масштабах. С этой целью международной организацией стандартов ISO принят единый международный код для программирования обработки на станках с ЧПУ. В нашей стране действует аналогичный код (ГОСТ 13052 – 74). Код устанавливает множество определенных символов, которые подразделяются на цифровые, буквенные в прописных буквах латинского алфавита и графические. Каждый символ имеет неповторимое выражение, получаемое путем перфорации отверстий на бумажной восьмидорожечной ленте. Шириной 25,4 мм. Первая слева дорожка (восьмая) предназначена для контрольного признака четности и нечетности. Необходимо, чтобы в каждой строке перфоленты число пробитых отверстий было бы четным числом. Остальные семь дорожек представляют собой соответствующий разряд в двоичных системе счисления.
Каждому направлению перемещений рабочих органов станков присваивают значение определенной координаты и соответствующий адресный символ, например: X, Y, Z, W и т.д. Существует единое направление осей координатных осей металлорежущих станков. Положительным направлением перемещения элемента станка принято считать то, при котором обрабатывающий инструмент (его держатель) и заготовка отступают друг от друга.
На сегодняшний день практически каждое предприятие, занимающееся механической обработкой, имеет в своем распоряжении станки с числовым программным управлением (ЧПУ). Станки с ЧПУ выполняют все те же функции, что и обычные станки с ручным управлением, однако перемещения исполнительных органов этих станков управляются электроникой. В чем же основное преимущество станков с ЧПУ и почему все большее число заводов предпочитает вкладывать деньги именно в современное оборудование с автоматическим управлением, а не покупать относительно дешевые универсальные станки?
Первым, очевидным плюсом от использования станков с ЧПУ является более высокий уровень автоматизации производства. Случаи вмешательства оператора станка в процесс изготовления детали сведены к минимуму. Станки с ЧПУ могут работать практически автономно, день за днем, неделю за неделей, выпуская продукцию с неизменно высоким качеством. При этом главной заботой станочника-оператора являются в основном подготовительно-заключительные операции: установка и снятие детали, наладка инструмента и т. д. В результате один работник может обслуживать одновременно несколько станков.
Вторым преимуществом является производственная гибкость. Это значит, что для обработки разных деталей нужно всего лишь заменить программу. А уже проверенная и отработанная программа может быть использована в любой момент и любое число раз.
Третьим плюсом являются высокая точность и повторяемость обработки. По одной и той же программе вы сможете изготовить с требуемым качеством тысячи практически идентичных деталей. Ну и, наконец, числовое программное управление позволяет обрабатывать такие детали, которые невозможно изготовить на обычном оборудовании. Это детали со сложной пространственной формой, например штампы и пресс-формы.
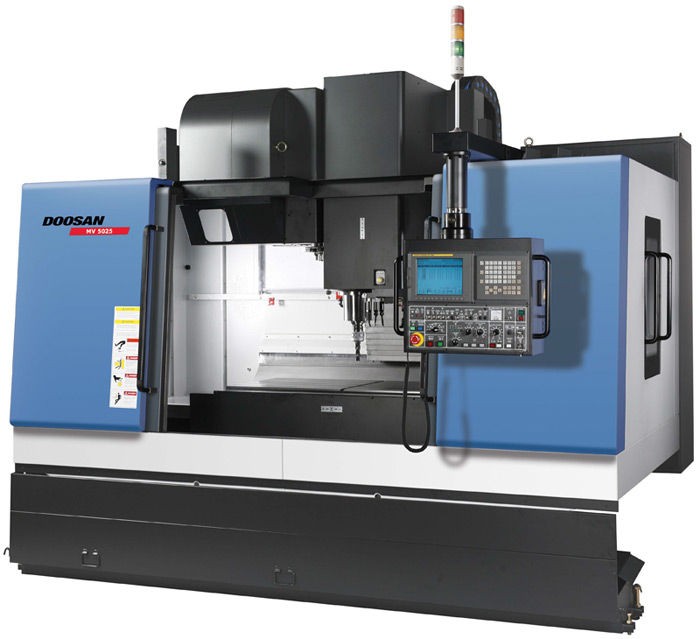
Стоит отметить, что сама методика работы по программе позволяет более точно предсказывать время обработки некоторой партии деталей и соответственно более полно загружать оборудование.
Станки с ЧПУ стоят достаточно дорого и требуют больших затрат на установку и обслуживание, чем обычные станки. Тем не менее их высокая производительность легко может перекрыть все затраты при грамотном использовании и соответствующих объемах производства.
Давайте разберемся, что же такое ЧПУ. Числовое программное управление – это автоматическое управление станком при помощи компьютера (который находится внутри станка) и программы обработки (управляющей программы). До изобретения ЧПУ управление станком осуществлялось вручную или механически.
Осевыми перемещениями станка с ЧПУ руководит компьютер, который читает управляющую программу (УП) и выдает команды соответствующим двигателям. Двигатели заставляют перемещаться исполнительные органы станка – рабочий стол или колонну со шпинделем. В результате производится механическая обработка детали. Датчики, установленные на направляющих, посылают информацию о фактической позиции исполнительного органа обратно в компьютер. Это называется обратной связью. Как только компьютер узнает о том, что исполнительный орган станка находится в требуемой позиции, он выполняет следующее перемещение. Такой процесс продолжается, пока чтение управляющей программы не подойдет к концу.
По своей конструкции и внешнему виду станки с ЧПУ похожи на обычные универсальные станки. Единственное внешнее отличие этих двух типов станков заключается в наличии у станка с ЧПУ устройства числового программного управления (УЧПУ), которое часто называют стойкой ЧПУ.
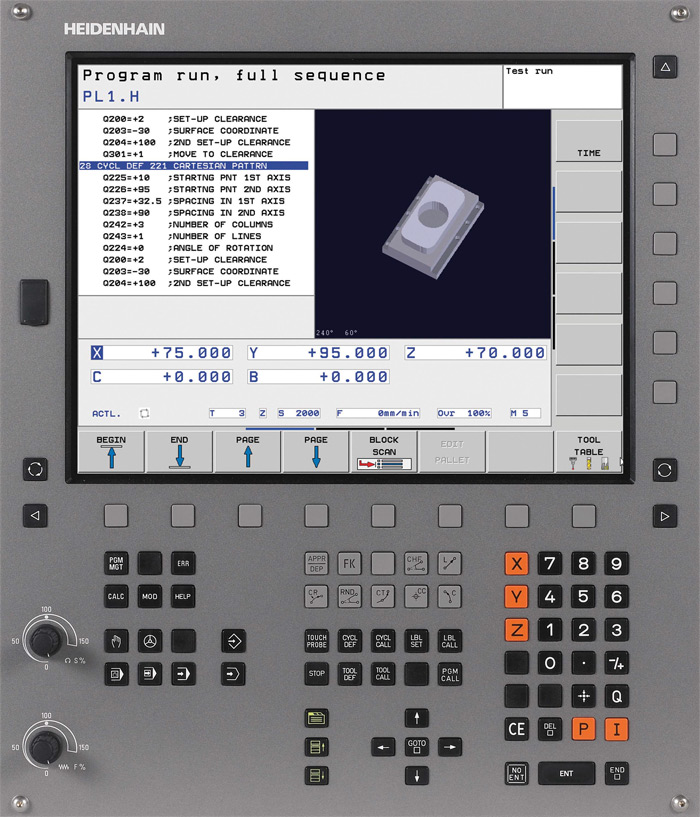
Иудейская пустыня Из истории Иудейской пустыни
Поздравления Льву (зодиак) С днем рождения львица
Вскрытие пришельца из Розуэла Бабло побеждает НЛО
Вскрытие инопланетянина: образец мистификации Вскрытие нло
Значение имени лель в сказке снегурочка