חיפוש טקסט מלא:
בית > תקציר > תעשייה, ייצור
תַקצִיר
פרויקט הקורס הסתיים בהתאם למטלה ומכיל 4 גיליונות בפורמט A1 (שרטוט חלק, שרטוט חלקי עבודה, שרטוט מתקן (ציוד טכנולוגי), התאמות טכנולוגיות) והערת הסבר המורכבת מ-52 גיליונות, 4 שרטוטים, 6 טבלאות. ביצירה נעשה שימוש ב-8 מקורות.
נושא פרויקט הקורס: "פיתוח תהליך טכנולוגיייצור חלק "פיר צעד".
בתהליך העבודה תוכנן תהליך טכנולוגי תפעולי מסלול, שתוכנן בהתאם ל-ESTD.
מבוא 5
1 תכנון תהליך העיבוד של חלק 6
1.1 מטרת השירות של החלק ו דרישות טכניותעל ה-6 שלה
1.2 בקרה טכנולוגית של השרטוט וניתוח יכולת הייצור
עיצובים 7
1.3 קביעת סוג הייצור 9
1.4 הצדקה לבחירה וקביעת מידות המקור
ריקים 14
1.5 תכנון טכנולוגיית מסלול לעיבוד חלקים 17
1.6 חישוב קצבאות עיבוד שבבי 19
1.7 עיצוב טכנולוגיית הפעלה 23
1.7.1 חישוב תנאי וזמני חיתוך 23
1.7.1.1 פעולת תכנון מס' 010 "פניית CNC" 23
1.7.1.2 פעולת תכנון מס' 020 "כרסום" 30
1.7.1.3 פעולת תכנון מס' 025 "חיתוך בריח" 37
1.7.2 חישוב דיוק עיבוד 44
1.7.3 בחירת ציוד 46
2 עיצוב ציוד טכנולוגי 48
2.1 בחירה והצדקה להתקנת החלק במתקן 48
2.2 תיאור טכניעיקרון עיצוב ועבודה
מתקנים 48
2.3 פיתוח תכנית חישוב לחיזוק וחישוב המנגנון
מהדק 48
הפניות 51
נספח 52
מבוא
פירים שונים מאוד מבחינת מטרת השירות, צורה קונסטרוקטיבית, גודל וחומר. למרות זאת, הטכנולוג, בעת פיתוח התהליך הטכנולוגי לייצור פירים, צריך לפתור משימות דומות רבות, ולכן רצוי להשתמש בתהליכים סטנדרטיים שנוצרים על בסיס הסיווג.
בהנדסת מכונות כללית קיימים פירי גלגלי שיניים חסרי מדרגות ומדרגים, מוצקים וחלולים, חלקים ומשובצים, וכן צירים משולבים בשילובים שונים מהקבוצות הנ"ל. לפי צורת הציר הגיאומטרי, הצירים יכולים להיות ישרים, גל ארכובה, ארכובה ואקסצנטרי (קאם).
הנפוצים ביותר בהנדסת מכונות, כולל בניית כלי מכונות, הם פירים מדורגים בגודל בינוני, ביניהם שולטים פירים חלקים. לפי ENIMS, מעל 85% מסך הגדלים הסטנדרטיים של פירים מדורגים בהנדסת מכונות הם פירים באורך של 150-1000 מ"מ.
למחסני פיר עשויים להיות פתחי מפתח, קווים או חוטים. לעתים קרובות כדאי להחליף חוטים לאבטחת חלקים מתואמים נגד תנועה צירית בחריצים לטבעות קפיצים. זה מפשט את הטיפול וההרכבה. חריצים או פילטים נעשים בנקודות המעבר של השלבים. עיבוד פילה מורכב יותר; לכן עדיף, במידת האפשר, לספק חריצים. קצוות פיר משופשפים. פירים משובצים יכולים להיות עם שולים דרך וסגורים, האחרונים מהווים כ-65% מסך הגדלים. לפי התכנון, השבלולים יכולים להיות בעלי צד ישר וסתמי. נכון לעכשיו, פירים בעלי צד ישר שולטים (כ-85-90% מהמספר הכולל של גדלי פיר משופשפים המשמשים בהנדסת מכונות), אם כי לשפלים פיתולים יש מספר יתרונות במונחים של טכנולוגיה.
פירים עם יחס של אורך לקוטר פחות מ-15 מסווגים כנוקשים; עם יחס של יותר מ-15, הפירים נחשבים לא קשיחים.
1. עיצוב תהליך עיבוד שבביפרטים
1.1 מטרת השירות ודרישות טכניות לחלק בהתאם לשרטוט ותנאי ההפעלה
פירוט - פיר מדורג. החומר המשמש הוא פלדה 30X13 GOST 5632-72. שיטת העיצוב היא חישול. לאחר העיבוד הסופי, הפיר נשלח להרכבה.
לפיר יש חמישה כוננים, המבוצעים לפי דרגת דיוק ו' בחספוס לפי הפרמטר Ra 1.25 (38js6; 40js6; 45js6; 32.2n6; 32n6). גלגלי שיניים מותקנים על שניים מהצווארים הללו באמצעות חיבור מפתח. לצווארים הקיצוניים של הפיר יש חוט M24 × 1.5-6g כדי לאבטח את גלגלי השיניים מתנועה צירית עם אומים.
משטחים 40js6; ל-45js6 ו-32.2n6 מ"מ יש קשיות מוגברת של 37…43 HRC e., המתקבלת כתוצאה מטיפול בחום. כדי להבטיח שהמשטחים הנותרים לא יהיו נתונים לטיפול בחום (25..30 HRC Oe), זה מתבצע ביחידת אינדוקציה (HFC).
הפיר עשוי מפלדת כרום בעלת סגסוגת גבוהה עמידה בפני קורוזיה. זה נובע מסביבת העבודה של המוצר.
1.2 ניתוח ייצור של עיצוב החלק
ציור הפירוט מכיל את כל הממדים הדרושים, מידע ניתן על החספוס של המשטח המעובד והדיוק של ייצורם.
ציור החלק מכיל את התצוגות הדרושות שנותנות תמונה מלאה של החלק. לפי התכנון, לחלק יש את רוב המשטחים פתוחים ונגישים לעיבוד.
אנו מבצעים הערכה איכותית של משטחים לפי המקדמים:
1) דיוק K PM
וע"פ - איכות הדיוק הממוצעת
A - מידת הדיוק המתאימה
N i - מספר המשטחים באיכות נתונה של דיוק
A 1 \u003d 6 n 1 \u003d 7
A 2 \u003d 7 n 2 \u003d 1
A 3 \u003d 8 n 3 \u003d 2
A 4 \u003d 12 n 4 \u003d 4
A 5 \u003d 14 n 5 \u003d 18
2) חספוס ק וו
איפה
B cf - הערך המספרי הממוצע של פרמטר החספוס
;
כאשר B הוא הערך המספרי של פרמטרי החספוס על
n i w - מספר המשטחים המרכיבים את החספוס
B 1 \u003d 1.25 n 1 \u003d 6
B 2 \u003d 6.3 n 2 \u003d 26
3) שימוש בחומרים
m g \u003d 5.6 ק"ג - משקל חלק
מ"ש - משקל חומר העבודה \u003d 7.84 ק"ג
m waste - מסה של פסולת
לפיכך, על פי כל האינדיקטורים, בהתאם ל- GOST 14205-83, החלק ניתן לייצור.
1.3 קביעת סוג הייצור
סוג הייצור על פי GOST 3.1108-74 מאופיין במקדם איחוד הפעולות Kz.o., המראה את היחס בין כל הפעולות הטכנולוגיות השונות שבוצעו או יבוצעו על ידי היחידה תוך זמן מסוים למספר של מקומות תעסוקה.
Kz.o. \u003d Oi / Rya
כאשר ОI הוא המספר הכולל של פעולות שונות;
ריא - המספר הברור של עובדי היחידה המבצעים פעולות שונות.
GOST 14004-85 מספק את סוגי הייצור הבאים:
יחיד;
סידורי;
תִפזוֹרֶת.
בתורו, ייצור המוני מחולק בקנה מידה גדול, בקנה מידה בינוני, בקנה מידה קטן.
החישוב מתבצע תוך התחשבות בפעולות העיקריות של עיבוד שבבי וסוגי ציוד לעיבוד מתכת.
נתונים ראשוניים:
תוכנית הפקה שנתית: N=10000 יח'.
מספר חלקים במוצר: m=1.
מצב תפעול המיזם: 2 משמרות ביום.
סוג ייצור משוער - אצווה בינונית.
כדי לחשב את מקדם פעולות התיקון, אנו קובעים את המסלול המקדים לעיבוד החלק. כאן, בהתבסס על תהליך טכנולוגי טיפוסי של עיבוד חלק, נבחר את פעולות העיצוב העיקריות של עיבוד שבבי:
כרסום ומרוכז. כרסום קצוות חומר העבודה וריכוזם.
מחרטת CNC. סיבוב מחוספס וגימור של משטחים חיצוניים.
כִּרסוּם. כרסום מפתחות.
בולטורזניה. השחלה M24 × 1.5-6g - שני מקומות.
שחיקה מעגלית. השחזה של משטחים חיצוניים.
בעת החישוב משתמשים בנוסחה
T sh-k \u003d מי
1) טוחנים את הקצוות.
מרכז מסתיים
2) סובב את דוכני הציר (סיבוב גס ועדין)
3) מפתחות טחינה:
חותך אצבע (מפתח).
כאשר i הוא מספר מהלכי העבודה
חותך דיסקים
4) חתוך חוט:
5) שיוף:
אנו קובעים את מקדם העומס הסטנדרטי של מקום העבודה.
מספר משוער של מכונות:
איפה
n n הוא מקדם העומס של הציוד הסטנדרטי (לייצור סדרתי אנו מקבלים n n \u003d 0.75).
N – תוכנית ייצור N=10000 יח'.
F g - 4015 שעות - הקרן השנתית בפועל של זמן פעולת הציוד
m pr \u003d 1
m pr \u003d 1
m pr \u003d 1
m pr \u003d 1
גורם עומס ציוד:
מספר הפעולות שבוצעו במקום אחד:
מספר ציוד - 5
מקדם קיבוע הפעולה:
10 קבע את מספר המוצרים באצווה להפעלה בו-זמנית לייצור:
נ= לא/254
כאשר a הוא תדירות ההשקה בימים (אנו מקבלים א = 6)
נ=10000*6/254=237 יח'
קביעת מספר המשמרות לעיבוד כל המנה:
אני - מספר פעולות
ΣT ש-ק =27.25 דקות
c= =3,39
קבל c=4
אנו קובעים את מספר המוצרים באצווה הנדרשים לטעינת הציוד עבור מספר שלם של משמרות:
=279.48 יח'. קבל n pr \u003d 280 יח'
1.4 הצדקה לבחירה וקביעת מידות חומר העבודה המקורי
פירים עם מספר קטן של מדרגות והפרשי קוטר קטנים עשויים מחלקי חלקים חתוכים ממוט מגולגל חם או נמשך קר, ובעלי תצורה מורכבת יותר ועם מספר רב של מדרגות או עם מדרגות הנבדלות באופן משמעותי בקוטר - מחסר המתקבל על ידי הטבעה, גלגול צולב או דחיסה סיבובית. הבחירה בחומר העבודה חייבת להיות מוצדקת על ידי חישובים טכניים וכלכליים.
בייצור המוני ובקנה מידה גדול, פירים עשויים מחסרי חלקים המבטיחים שימוש יעיל במתכת (מקדם ניצול מתכת CMM = 0.65 ... 0.7) והפחתה משמעותית בעוצמת העבודה בעיבוד שבבי. מלאי בר מוחלף בהחתמה אם ה-CIM גדל ב-5% לפחות. חומר העבודה המתקבל על ידי הקטנה רדיאלית הוא הקרוב ביותר בתצורה ובגודל לחלק המוגמר, בעוד CIM = 0.85 ... 0.95.
הריק מתקבל על מכבש חישול חם בתבנית סגורה.
אנו מחשבים את הממדים של חומר העבודה על פי GOST 7505-89 "חישול פלדה מוטבע".
1.4.1. נתונים ראשוניים.
ציוד - מכונת הטבעה חמה.
חומר העבודה הוא פלדה 30X13.
משקל חלק - 5.6 ק"ג.
1.4.2. קביעת המאפיינים הטכניים של הפרזול.
1) מצא את המסה המשוערת של הפרזול =
, איפה
- מסת החלק,
- מקדם עיצוב נקבע על פי GOST 7505-89. \u003d 1.4 (מכיוון שלחלק יש ציר ישר).
קבל = ק"ג.
2) דרגת דיוק - T2.
3) קבוצת פלדה - M3.
4) מידת המורכבות של הפרזול נקבעת בהתאם ליחס , איפה
- מסת הדמות שבה רשום הפרזול. יש לנו =
, מכאן שמידת המורכבות של הפרזול היא C1.
5) התצורה של משטח הפרידה של התבנית היא P (שטוח).
6) מדד ראשוני - 10.
1.4.3. קביעת קצבאות וזיוף הקפות.
1) ההפרשות הבסיסיות למידות, מ"מ:
1.5 – קוטר 40 מ"מ, גימור פני השטח Ra=1.25 מיקרומטר
1.2 – קוטר 42 מ"מ, גימור פני השטח Ra=6.3 מיקרומטר
1.6 – קוטר 46 מ"מ, גימור פני השטח Ra=1.25 מיקרומטר
1.2 – קוטר 53 מ"מ, גימור פני השטח Ra=6.3 מיקרומטר
1.4 – קוטר 39.5 מ"מ, גימור פני השטח Ra=6.3 מיקרומטר
1.5 – קוטר 32.2 מ"מ, גימור פני השטח Ra=1.25 מיקרומטר
1.4 – קוטר 24 מ"מ, גימור פני השטח Ra=6.3 מיקרומטר
1.1 - עובי 5 מ"מ, חספוס Ra=6.3 מיקרומטר
1.2 - עובי 62 מ"מ, חספוס Ra=6.3 מיקרומטר
1.2 - עובי 54 מ"מ, חספוס Ra=6.3 מיקרומטר
1.7 - אורך 597 מ"מ, חספוס Ra=6.3 מיקרומטר.
2) קיזוז לאורך פני השטח של הפרידה של המות - 0.3 מ"מ.
סטייה משטיחות וישרות - 0.5 מ"מ
שיפוע הטבעה - 5
1.4.4. מידות פרזול והסובלנות שלהן.
1) מידות פרזול, מ"מ:
קוטר 24+(1.4+0.3+0.5)×2=28.4, קבל 28.5 מ"מ
קוטר Ç40+(1.5+0.3+0.5)×2=44.6, קבל 45 מ"מ
קוטר Ç42+(1.2+0.3+0.5)×2=46, קבל46 מ"מ
קוטר Ç46+(1.6+0.3+0.5)×2=50.8, קבל51 מ"מ
קוטר Ç53+(1.2+0.3+0.5)×2=57, קבל57 מ"מ
קוטר Ç39.5+(1.4+0.3+0.5)×2=43.9, קבל44 מ"מ
קוטר Ç32.2+(1.5+0.3+0.5)×2=36.8, קבל37 מ"מ
עובי 5+(1.1+0.3+0.5)×2=8.8, קבלו 9 מ"מ
עובי 62+1.2+0.3+0.5=64, מקבלים 64 מ"מ
עובי 54 + 1.2 + 0.3 + 0.5 \u003d 56, אנו מקבלים 56 מ"מ
אורך 597+(1.7+0.3+0.5)×2=602, קבלו 602 מ"מ
2) רדיוס העיגול של הפינות החיצוניות הוא 2.5 מ"מ.
3) סטיות מידות מותרות, מ"מ:
קוטר Ç28.5 קוטר Ç57
קוטר Ç45 קוטר Ç44
קוטר Ç46 קוטר Ç37
קוטר Ç51 עובי 9
עובי 56 עובי 64
אורך 602 .
הציור של חומר העבודה מוצג על גיליון בפורמט A2
PenzGU 1.3-09.151001.123.002-CHZ
1.5 עיצוב טכנולוגיית ניתוב לעיבוד חלקים
שולחן 1.
№ אופרות |
שם ו סיכום |
בסיסים טכנולוגיים |
צִיוּד |
כרסום ומרוכז מיל מסתיימת מרכז מ-2 צדדים |
צוואר ותחת לא גמורים 20 |
||
מחרטת CNC חידד תחילה את הפיר משמאל חידד את הפיר מימין לפני כן חידד את הפיר משמאל לחלוטין חידד את הפיר מימין לחלוטין |
ציר וסיום 1 (ציר ומקצה 30) |
||
פורץ מנעולים |
שולחן עבודה של מנעולן |
||
כִּרסוּם טוחנים את המפתח עם חותך מפתח (אצבע). כרסום פתח המפתח עם חותך דיסק |
משטח צוואר Ç40js6 ותחת 30; משטח צוואר Ç32,2n6 ופנים קצה 1; |
||
מוּשׁחָל חותכים חוט M24 × 1.5-6g - שני מקומות |
משטחי צוואר 32.2n6; 38js6 |
||
פורץ מנעולים דבור |
שולחן עבודה של מנעולן |
||
כְּבָסִים |
|||
לִשְׁלוֹט |
צלחת בקרה |
||
תֶרמִי |
התקנת אינדוקציה |
||
שחיקה גלילית טחינת פירי טחינה Ç38 מ"מ; Ç40 מ"מ; Ç45 מ"מ; Ç46 מ"מ; Ç32.2 מ"מ; Ç32 מ"מ |
ציר וסיום 1 |
||
פורץ מנעולים הסר כתמים, קצוות חדים עמומים |
שולחן עבודה של מנעולן |
||
כְּבָסִים |
|||
לִשְׁלוֹט |
צלחת בקרה |
||
שימור |
שולחן עבודה של מנעולן |
הגרסה הסופית של טכנולוגיית המסלול מנוסחת על מפות מסלול, המפורטות בנספח, בהתאם ל- GOST 3.1118-82.
1.6 קביעת קצבאות בשיטת החישוב והניתוח
עבור משטח אחד, הקצבה נקבעת לפי שיטת החישוב והניתוח, לכל השאר לפי GOST 7505-89.
אנו מחשבים את קצבת הגודל 40 js6 (±0.008) מ"מ
תוכנית עיבוד:
סיבוב גס
סיבוב משובח
שְׁחִיקָה
החריטה והשחזה מתבצעות במרכזים, לפיכך, הסטיות במיקום המשטחים הן:
הסובלנות על פני השטח המשמשים כבסיס לפעולת הכרסום והריכוז נקבעת על פי GOST 7505-89:
ערך שיורי של סטיות מרחביות:
לאחר חיספוס
אחרי הסיום
חישוב הערכים המינימליים של הקצבאות מתבצע על פי הנוסחה:
קצבה מינימלית:
לחיתוך מוקדם:
לפנייה אחרונה:
לשיוף:
הנתונים שהתקבלו מוזנים בטבלה 2.
מעברים טכנולוגיים של טיפול פני השטח |
רכיבי קצבה, מיקרונים |
קצבה משוערת |
גודל משוער dp, מ"מ |
גודל מוגבל, מ"מ |
ערכי הגבלה של קצבאות, מיקרונים |
|||||
2 Zmax |
||||||||||
רֵיק |
||||||||||
מפנה ראשוני |
||||||||||
מפנה לגמר |
||||||||||
שְׁחִיקָה |
העמודה "גודל משוער" (d p) מתווספת, החל מהגודל המלא:
מגבלת הגודל הקטן ביותר נקבעת על ידי עיגול כלפי מעלה לאותו סימן כמו השבר העשרוני, אשר ניתנת לו סובלנות. אנו מוצאים את גודל המגבלה הגדול ביותר על ידי הוספת הסובלנות לגודל הקטן ביותר.
אנו מחשבים את ערך הקצבאות:
קצבאות כלליות ו
אנו קובעים על ידי סיכום קצבאות הביניים:
212+336+2960=3508 מיקרומטר
258+434+4400=5092 מיקרומטר
בואו נבדוק את נכונות החישובים שבוצעו:
הבדיקה נכונה, לכן, החישוב נעשה, נכון.
איור.1. ערכת קצבאות וסובלנות לגודל 40 js6 מ"מ.
1.7 עיצוב טכנולוגיית הפעלה
1.7.1 חישוב תנאי חיתוך ותקני זמן
1.7.1.1 פעולת תכנון מס' 010 "פניית CNC"
הפעולה מתבצעת על מוד מחרטת חיתוך בהברגה CNC. 16K20F3 לארבע הגדרות (A ו-B - חיספוס, C ו-D - גימור), שכל אחת מהן מבצעת מעבר אחד. בפעולה זו, צ'אק הנעה בעל 2 לסתות עם מרכז קדמי צף ומרכז מסתובב המותקן בעמוד האחורי משמשים להתקנה ולביסוס חלק העבודה על המכונה.
ככלי חיתוך, נעשה שימוש בכלי חריטה לעיבוד חיצוני בתקן ISO המיוצרים על ידי ISCAR:
סיבוב גס:
מחזיק: PCLNR 2020K-12
צלחת: CNMG 120408T-NR
רדיוס פינה r=0.8 מ"מ
כיתה הכנס IC 9025
V=150..250 מ' לדקה
S=0.15..0.5 מ"מ/סיבוב
סיבוב עדין:
מחזיק: SVJCR 2020K-16
צלחת: VCMT 160404E-14
רדיוס פינה r=0.4 מ"מ
כיתה הכנס IC 9025
סגסוגת קשה מצופה בתצהיר כימי עם שלוש שכבות של TiN, AL 2 O 3, TiCN.
V=250..400 מ' לדקה
S=0.12..0.25 מ"מ/סיבוב
כל החישובים עבור פעולה זו מתבצעים על פי הנוסחאות
מהירות החיתוך עבור פנייה אורכית ורוחב חיצונית מחושבת על ידי הנוסחה
Kv עבור מהירות חיתוך הוא התוצר של המקדמים האישיים
לmv
Knv - השפעת מצב פני השטח של חומר העבודה (עבור מוצרים מגולגלים = 0.8; לאחר חיספוס = 1.0) טבלה 5,
קו – השפעת החומר של החלק החיתוך (= 1.9) טבלה.6
קו – השפעת הזווית הראשית בתוכנית החותך (עבור f95Å=0.7; עבור f93Å=0.7) טבלה 18
סיבוב גס (הגדרות A ו-B):
עומק חיתוך t = 4 מ"מ
הזנה S=0.5 מ"מ/סיבוב
עם V= 350 טאב.17
M= 0,2
= 0,15
= 0,35
אנו בוחרים את הערך הקרוב ביותר לפי הדרכון של המכונה 800 סל"ד
קבע את כוח החיתוך:
פ ז =10 ג ע ט איקס ס y v נ ק ע
מקדם תיקון כללי Cr ק ע = ק mp ק ע ק ע ק ע ק rp
ק mp =0.75 tab.9
ק י ע=0.89 tab.23
ק ז ע =1,1
ק ל ע =1,0
ק rp
ק ע = 0,75*0,89*1,1*1=0,734
עם ע= 204 טבלה 22
נ = 0
פ ז =10*204*4 1 *0,5 0,75 *135,7 0 *0.734=3561 N
חשב כוח חיתוך
ל= .
Lpx:
לpx=ללחתוך+y+ לנוֹסָף
איפה לגזירה -
ללהוסיף -
y –
להגדרה א':
ללחתוך= 430 מ"מ
לתוספת+y= 14 מ"מ
לpx= 444 מ"מ
ל= 1.11 דקות
להגדרה ב':
ללחתוך= 187 מ"מ
לתוספת+y= 14 מ"מ
לpx= 201 מ"מ
ל= 0.503 דקות
פנייה עדינה (הגדרות C ו-D):
עומק חיתוך t = 0.4 מ"מ
הזנה S=0.25 מ"מ/סיבוב
חיי כלי T = 60 דקות
עם V= 420 טאב.17
M= 0,2
אנו בוחרים את הערך הקרוב ביותר לפי הדרכון של המכונה 2000 סל"ד
מהירות חיתוך בפועל
קבע את כוח החיתוך:
פ ז =10 ג ע ט איקס ס y v נ ק ע
מקדם תיקון כללי Crעל כוח החיתוך הוא מכפלת המקדמים הבודדים ק ע = ק mp ק ע ק ע ק ע ק rp
ק mp =0.75 tab.9
ק י ע=0.89 tab.23
ק ז ע =1,1
ק ל ע =1,0
ק rp- נלקח בחשבון רק עבור פלדה במהירות גבוהה.
ק ע = 0,75*0,89*1,1*1=0,734
עם ע= 204 טבלה 22
נ = 0
פ ז =10*204*0,4 1 *0,25 0,75 *333,01 0 *0.734=211.76 N
חשב כוח חיתוך
קילוואט
קילוואט
בואו נקבע את זמן העיבוד העיקרי של המכונה:
ל=.
קבע את אורך השבץ Lpx:
לpx=ללחתוך+y+ לנוֹסָף
איפה לגזירה -אורך חיתוך שווה לאורך העיבוד.
ללהוסיף -אורך מהלך נוסף, הנגרם במקרים מסוימים על ידי תכונות ההתקנה והתצורה של החלק.
y – אורך הגישה, הצלילה וחריפת הכלים
להתקנה B:
ללחתוך= 432 מ"מ
לתוספת+y= 6 מ"מ
לpx= 438 מ"מ
ל= 0.876 דקות
כדי להתקין G:
ללחתוך= 196 מ"מ
לתוספת+y= 6 מ"מ
לpx= 202 מ"מ
ל= 0.404 דקות
קביעת זמן חישוב החתיכה לפעולה.
הנורמות הטכניות של הזמן בתנאים של ייצור המוני וייצור המוני נקבעות על ידי שיטת החישוב והניתוח. בייצור סדרתי, הנורמה של זמן חישוב החתיכה נקבעת:
תש-ק= + Tsht,
איפה Tpz -הכנה - הזמן האחרון לניתוח.
נ – גודל קבוצת ההשקה של החלקים; נ= 280 יחידות
קצב זמן החתיכה בעת עיבוד על מחרטות CNC מוגדר כ:
ט מחשב =T O +T v +T שֵׁרוּת +T נתיב
טאו -הזמן הטכנולוגי העיקרי
טובסל -זמן תחזוקה ושירות.
טפר- זמני הפסקה .
טלוויזיה -זמן עזר:
ט v =T שפם +T m.v + ט זו + T מ
טמ.וו. -זמן בסיוע מכונה הנדרש להזזת צריח המכונה באזור העיבוד, כולל משיכות סרק ואספקה, כמו גם החלפת כלים.
צו -זמן להדק ולשחרר את החלק,
טו -,
טיז -זמן למדוד את החלק,
ט m.v. =T xx +T sk +T סִי
Txx- זמן סרק כולל
טסק -הזמן הכולל לשינוי פריימים של תוכנית הבקרה (בממוצע, הזמן לשינוי פריים אחד הוא 1.5-2 שניות).
צי -הזמן הכולל הנדרש כדי לשנות את הכלי.
ט מחשב =T O +T שפם + ט מ + ט זו +T xx +T sk +T סִי +T שֵׁרוּת +T נתיב
האורך הכולל של הסרק -1862 מ"מ
מהירות נסיעה מהירה - 2000 מ"מ לדקה
Txx=1862/2000= 0.931 דקות
Tsi= 0.17 דקות
טסק= 1.5 דקות
טמ.וו.\u003d 0.931 + 1.5 + 0.17 \u003d 2.601 דקות
2.893+0.4+2.601=5.894 דקות
Tobsl+Tper= 12% מזמן הפעולה
Tobsl+Tper=5,894*0,12=0,707
הערכים שהושגו של נורמות הזמן מסוכמים בטבלה 3.
שולחן 3
סט א |
סט ב' |
סט ב' |
הגדרות G |
||
ט שפם , דקות |
|||||
ט זו , דקות |
|||||
ט מ , דקות |
|||||
ט שֵׁרוּת +T נתיב , דקות |
|||||
ט pz , דקות |
|||||
ט O , דקות |
על סמך הטבלה אנו מקבלים:
ט מחשב =2,893+0,74+ 2,64 + 0,176 +2.601+2.828=11.878 דקות.
תש-ק= +11.878=11.942 דקות.
1.7.1.2 פעולת תכנון מס' 020 "כרסום"
הפעולה מתבצעת במכונת כרסום 6D91 בשתי הגדרות. עבור פעולה זו, יש צורך להשתמש במתקן מיוחד, שבאמצעותו מותקן החלק ומבוסס על המכונה לאורך המשטח והקצה הגלילי החיצוני (ציור ההרכבה של המתקן מוצג על גיליון בפורמט A1 PenzGU 1.3 -09.151001.123.005-SB).
חותכים מיוחדים משמשים ככלי חיתוך:
להגדרה A - חותך מפתחות 12 מ"מ, חומר חותך - פלדה במהירות גבוהה R6M5
להגדרה B - חותך פטרייתי 48 מ"מ ו-b = 8 H8 מ"מ, חומר חותך - פלדה במהירות גבוהה R6M5
כל החישובים עבור פעולה זו מתבצעים על פי הנוסחאות.
סט א':
החלק מותקן על המתקן ומבוסס על 40.2 (ציור 40js6).
במעבר זה, חריץ הוא כרסום עבור מפתח מקביל עם מידות V=12,
ט=
4.5H12. העיבוד מתבצע בשיטת "מטוטלת" בשני מעברים עם הזנה לעומק של 2.2 מ"מ
עומק כרסום t=2.2 מ"מ
רוחב כרסום H=12 מ"מ
קוטר חותך D=12 מ"מ
הזנה לכל שן חותך Sz= 0.18 מ"מ/שן
מספר שיני החותך z=2
קבע את אורך השבץ Lpx:
לpx=ללחתוך+y+ לנוֹסָף
איפה לגזירה -אורך חיתוך שווה לאורך העיבוד. ללחתוך= 54 מ"מ
ללהוסיף -אורך מהלך נוסף, הנגרם במקרים מסוימים על ידי תכונות ההתקנה והתצורה של החלק.
y – אורך הגישה, הצלילה וחריפת הכלים
לתוספת+y=6 מ"מ
לpx = 54+6=60 מ"מ
קבע את מהירות החיתוך V נ,
דקה ,
מקדם התיקון הכולל Kv עבור מהירות החיתוך הוא תוצר של הגורמים הבודדים
לmv- השפעת איכות החומר המעובד (עבור פלדה = 0.9) טבלה 3,
Knv
קו –
T -חיי כלי עבודה; T= 80 דקות tab40;
עם V= 12 טבלה 39
M = 0,26
ש= 0,3
u= 0
ע= 0
מהירות הציר:
נ= 250 דקות
ציון מהירות החיתוך:
הגדר את הזנת הדקות סM,מ"מ/דקה:
סm=Sz* ז* נ= 0.18*2*250=90 מ"מ/דקה
קבע את כוח החיתוך:
פ ז =10
גורם התיקון ק mpעבור כוח חיתוך
ק mp =0.3 tab.9
עם ע= 82 טבלה 41
u = 1
ש= 0,86
פ ז =10
ח
חשב כוח חיתוך
קילוואט
קילוואט
בואו נקבע את זמן העיבוד העיקרי של המכונה:
ל=
דקה
הגדרה ב':
החלק מותקן על המתקן ומבוסס על Ç32.4 (ציור Ç32.2n6).
במעבר זה, החריץ עבור המפתח כרסם במידות V=8 +0,022 , ט= 4 H12. העיבוד מתבצע עם חותך פטרייתי Ç48 מ"מ ו-b = 8 H8 מ"מ, החומר של החותך הוא פלדה מהירה R6M5
עומק כרסום t=4 מ"מ
רוחב כרסום H=8 מ"מ
קוטר חותך D=48 מ"מ
הזנה לכל שן חותך Sz= 0.01 מ"מ/שן
מספר שיני החותך z=12
קבע את אורך השבץ Lpx:
לpx=ללחתוך+y+ לנוֹסָף
איפה לגזירה -אורך חיתוך שווה לאורך העיבוד. ללחתוך= 54 מ"מ
ללהוסיף -אורך מהלך נוסף, הנגרם במקרים מסוימים על ידי תכונות ההתקנה והתצורה של החלק.
y – אורך הגישה, הצלילה וחריפת הכלים
לתוספת+y=6 מ"מ
לpx = 54+6=60 מ"מ
קבע את מהירות החיתוך V, מ/דקה, מהירות ציר נ, דקה,
מקדם התיקון הכולל Kv עבור מהירות החיתוך הוא תוצר של הגורמים הבודדים
לmv- השפעת איכות החומר המעובד (עבור פלדה = 0.9) טבלה 3,
Knv - השפעת מצב פני השטח של חומר העבודה (לאחר עיבוד = 1.0) טבלה 5,
קו – השפעת החומר של החלק החיתוך (= 1.0) טבלה.6
T -חיי כלי עבודה; T= 60 דקות tab40;
עם V= 72 טבלה 39
M = 0,15
ש= 0,2
u= 0,1
ע= 0,1
מהירות הציר:
על פי הדרכון של המכונה, אנו מקבלים את מספר המהפכות נ= 1000 דקות
ציון מהירות החיתוך:
הגדר את הזנת הדקות סM,מ"מ/דקה:
סm=Sz* ז* נ= 0.01*12*1000=120 מ"מ/דקה
קבע את כוח החיתוך:
פ ז =10
גורם התיקון ק mpעבור כוח חיתוך
ק mp =0.3 tab.9
עם ע= 68.2 tab.41
u = 1
ש= 0,86
w= 0
פ ז =10
ח
חשב כוח חיתוך
קילוואט
קילוואט
בואו נקבע את זמן העיבוד העיקרי של המכונה:
ל=
דקה
Tsh-k = + Tsht,
איפה Tpz -
נ – נ= 280 יחידות
Tsht=To+Tvק+Tob.from,
איפה זה -הזמן העיקרי,
טלוויזיה -זמן עזר:
TV=Tus+Tzo+Tup+Tiz,
איפה טו -זמן התקנה והסרה ,
צו -
טיפש -
טיז -זמן למדוד את החלק,
טוב.מ-
ק ק=1,85).
Tob.ot=ט אופ ·9%
ט אופ =T O +T v · ק
ט אופ =2.833+(0.094+0.068+0.12+0.62)1.85=4.502 דקות
Tob.from \u003d 4.502 0.09 \u003d 0.405 דקות
הערכים שהושגו של נורמות הזמן מסוכמים בטבלה 4.
טבלה 4
שֵׁם |
מעבר 1 |
מעבר 2 |
|
טו - |
|||
צו - |
|||
טיפש - |
|||
טיז - |
|||
Tob.from - |
|||
Tpz - |
|||
זֶה- זמן עיקרי, דקות |
|||
תש-ק=
+4,502+0,405
= 5.004 דקות.
1.7.1.3 פעולת תכנון מס' 025 "חיתוך חוט"
הפעולה מתבצעת על ידי מכשיר חצי אוטומטי לחיתוך חוט 5D07 בשתי הגדרות. עבור פעולה זו, יש צורך להשתמש במכשיר - סגן עם לסתות מרוכזות עצמיות, שבאמצעותו מותקן החלק ומבוסס על המכונה לאורך המשטח הגלילי החיצוני. אפשר להשתמש במכשיר מיוחד הדומה למכשיר המשמש בפעולת הכרסום.
ככלי חיתוך, נעשה שימוש בראש חיתוך בורג נפתח - 4KA-70 לפי GOST 21760 - 76 עם מסרק עגול לפי
GOST 21761-76 עשוי מפלדה מהירה R6M5 עם ציפוי עמיד בפני שחיקה של טיטניום ניטריד (TiN)
כל החישובים עבור פעולה זו מתבצעים על פי הנוסחאות.
1) סט א':
החלק מותקן על המתקן ומבוסס על פני השטח של הצוואר Ç38js6.
במעבר זה מתבצעת השחלה של M24 × 1.5-6g.
הזנה (שווה לגובה החוט) ס= 1.5 מ"מ/סיבוב
קוטר חוט D=24 מ"מ
עומק חיתוך t=1.3 מ"מ
Lpx:
לpx=ללחתוך+y+ לנוֹסָף
איפה לגזירה -אורך חיתוך שווה לאורך העיבוד. ללחתוך= 31 מ"מ
ללהוסיף -אורך מהלך נוסף, הנגרם במקרים מסוימים על ידי תכונות ההתקנה והתצורה של החלק.
י – אורך הגישה, הצלילה וחריפת הכלים
לתוספת+y=3 מ"מ
לpx = 31+3=34 מ"מ
קבע את מהירות החיתוך V, מ/דקה, מהירות ציר נ, דקה,
לmv
ק ט v
קו –
T -חיי כלי עבודה; T= 120 דקות tab49;
עם V= 7.4 tab.49
M = 0,5
ש= 1,2
מהירות הציר:
על פי הדרכון של המכונה, אנו מקבלים את מספר המהפכות נ= 160 דקות
ציון מהירות החיתוך:
קבע מומנט:
M KP =10 ג M ד ש ס y ק mp
גורם התיקון ק mpעבור כוח חיתוך
ק mp =0.85 tab.50
עם M= 0.046 טבלה 51
ש= 1,1
M KP =10 0.046 24 1,1 1.5 1,5 0.85=23.69חM
חשב כוח חיתוך
קילוואט
קילוואט
בואו נקבע את זמן העיבוד העיקרי של המכונה:
ל=
דקה
2) הגדרה ב':
החלק מותקן על המתקן ומבוסס על פני השטח של הצוואר Ç32,2n6.
במעבר זה מתבצעת השחלה של M24 × 1.5-6g
הזנה (שווה לגובה החוט) ס= 1.5 מ"מ/סיבוב
קוטר חוט D=24 מ"מ
עומק חיתוך t=1.3 מ"מ
קבע את אורך השבץ Lpx:
לpx=ללחתוך+y+ לנוֹסָף
איפה לגזירה -אורך חיתוך שווה לאורך העיבוד. ללחתוך= 20.4 מ"מ
ללהוסיף -אורך מהלך נוסף, הנגרם במקרים מסוימים על ידי תכונות ההתקנה והתצורה של החלק.
y – אורך הגישה, הצלילה וחריפת הכלים
לתוספת+y=3 מ"מ
לpx = 20.4+3=23.4 מ"מ
קבע את מהירות החיתוך V, מ/דקה, מהירות ציר נ, דקה,
מקדם התיקון הכולל Kv עבור מהירות החיתוך הוא תוצר של הגורמים הבודדים
לmv- השפעת איכות החומר המעובד (עבור פלדה = 0.8) טבלה 50,
ק ט v - תוך התחשבות בדיוק החוט הנחתך (מדויק = 0.8) טבלה 50,
קו – השפעת החומר של החלק החיתוך (= 1.0) tab.50
T -חיי כלי עבודה; T= 120 דקות tab49;
עם V= 7.4 tab.49
M = 0,5
ש= 1,2
מהירות הציר:
על פי הדרכון של המכונה, אנו מקבלים את מספר המהפכות נ= 160 דקות
ציון מהירות החיתוך:
קבע מומנט:
M KP =10 ג M ד ש ס y ק mp
גורם התיקון ק mpעבור כוח חיתוך
ק mp =0.85 tab.50
עם M= 0.046 טבלה 51
ש= 1,1
M KP =10 0.046 24 1,1 1.5 1,5 0.85=23.69חM
חשב כוח חיתוך
בואו נקבע את זמן העיבוד העיקרי של המכונה:
ל=
דקה
3) קביעת זמן חישוב החתיכה לפעולה.
הנורמות הטכניות של הזמן בתנאים של ייצור המוני וייצור המוני נקבעות על ידי שיטת החישוב והניתוח. בייצור סדרתי, הנורמה של זמן חישוב החתיכה נקבעת:
Tsh-k = + Tsht,
איפה Tpz -הכנה - הזמן האחרון לניתוח.
נ – גודל קבוצת ההשקה של החלקים; נ= 280 יחידות
Tsht=To+Tvק+Tob.from,
איפה זה -הזמן העיקרי,
טלוויזיה -זמן עזר:
TV=Tus+Tzo+Tup+Tiz,
איפה טו -זמן התקנה והסרה ,
צו -זמן להדק ולשחרר את החלק,
טיפש -זמן לתורים בקרת מכונה,
טיז -זמן למדוד את החלק,
טוב.מ-זמן לתחזוקת מקום העבודה והפסקות למנוחה ולצרכים אישיים,
ק- מקדם תוך התחשבות בייצור הסדרתי ( ק=1,85).
Tob.ot=ט אופ 7%
ט אופ =T O +T v · ק
ט אופ =0.24+(0.094+0.068+0.12+0.55)1.85=1.78 דקות
טוב \u003d 1.78 0.07 \u003d 0.125 דקות
הערכים שהושגו של נורמות הזמן מסוכמים בטבלה 5.
טבלה 5
שֵׁם |
מעבר 1 |
מעבר 2 |
|
טו -זמן התקנה ו הסרה של חלק, דקות |
|||
צו -זמן הידוק ושחרור החלק, דקות |
|||
טיפש -זמן לבקרת מכונה, דקות |
|||
טיז -זמן למדוד את החלק, דקות |
|||
Tob.from -זמן לתחזוקת מקום העבודה והפסקות למנוחה ולצרכים אישיים, דקות |
|||
Tpz -הכנה - זמן אחרון, דקות |
|||
זֶה- זמן עיקרי, דקות |
|||
זמן קבלת והחזרת המכשיר, דקות |
על סמך הטבלה אנו מקבלים:
תש-ק= +0,24+0,125 = 0.46 דקות.
1.7.2 חישוב דיוק העיבוד
חישוב דיוק העיבוד מורכב מקביעת השגיאה הכוללת של סיבוב עדין והשוואתה לסובלנות הממדית לפי דרגת דיוק 9 40.266 h9 (-0.062).
שגיאת העיבוד הכוללת מחושבת על ידי הנוסחה
כאשר - טעויות המתעוררות בתהליך העיבוד;
- השגיאה של הגדרת המערכת הטכנית לגודל.
1. קבע את שגיאת העיבוד הנגרמת מהבלאי הממדים של הכלי
באמצעות טבלה 29 של בלאי ממדי מותר של הכלי בעת עיבוד אצווה של חלקי עבודה, אנו קובעים:
20 מיקרומטר
2. הגדירו את הדחיפות האלסטיות שנגרמות מחוסר העקביות של הכוח
מכיוון שטיפול פני השטח התבצע עם קיבוע במצלמות מכונה, הנוסחה הבאה חלה כאן
הענות שווה ל
מיקרומטר/kN
כוח רדיאלי להגדיר לפי הנוסחה
איפה מ"מ;
מ"מ
ערך מהירות חיתוך: מ'/דקה.
על פי טבלה 22 אנו מוצאים: עם ע = 204; נ = 0; איקס= 1,0; י= 0,75
הערך של מקדם התיקון לכוח החיתוך
ק ע =0,734
חשב את מהירות החיתוך וקבע את הכוח הרדיאלי
בואו נגדיר שכיבות סמיכה אלסטיות
3. הבה נקבע את השגיאה של הגדרת המערכת הטכנית לגודל
מיקרומטר.
4. דפורמציות טמפרטורה נקבעות לפי הנוסחה
,
מיקרון
5. קבע לפי הנוסחה
,
מ"מ,
מ"מ;
מיקרומטר.
שגיאת עיבוד כוללת
אנו משווים את השגיאה הכוללת עם סובלנות הגודל 40.266 h9, שהיא 62 מיקרומטר.
62 מיקרומטר > 55.5 מיקרומטר
מסקנה: דיוק העיבוד נצפה.
1.7.3 בחירת ציוד
במפעלים מנסים לצבוע את המסלול הטכנולוגי באופן שאם אפשר, הכל מתבצע בציוד של בית מלאכה אחד. זה נובע מהצורך לערוך הרבה מסמכים בעת העברת חלק מתהליך המסלול לחנות אחרת.
הטכנולוגיה המעוצבת עונה על כלל זה. כל פעולותיו מבוצעות בתוך חלק אחד בבית המלאכה, למעט פעולת הקטיף.
הבחירה בדגם ספציפי של ציוד מתבצעת על פי קריטריונים כלליים, דיוק והספק.
התפלגות הציוד לפי פעולות מסוכמת בטבלה 6.
טבלה 6
שם המכונה |
כלי חיתוך |
מכשיר וכלי עזר |
כלי מדידה |
|
כרסום ומרכוז חצי אוטומטי |
מקדחה 4 R6M5 GOST 14034-74 מרכז מקדחה. 2317-0107 (f4.00) GOST 14952-75 טחנת קצה Ø 100 T5K10 GOST 24359-80 חותך (f100) 2214-0001 T5K10 45° GOST 24359-80 |
|||
מחרטה לחיתוך בורג CNC 16K20F3 |
חותך דרך PCLNR 2020K-12 עם הוספה: CNMG120408T-NR חותך ישר SVJCR 2020К-16 |
צ'אק 2 x פקה |
מיקרומטר MK 25-1 GOST 6507-78 קליפר ШЦ-I-125-0.1-1 GOST 166 דגימות חספוס GOST 9378-75 |
|
מכונת כרסום מפתח מפתח 6D92 |
חותך מפתחות מיוחד Ç12mm P6M5 חותך (f12) 2234-0367 N9 GOST 9140-78 חותך פטריות מיוחד Ç48 מ"מ ו-b=8 H8 R6M5 |
מכשיר מיוחד |
קליפר ШЦ-I-125-0.1-1 GOST 166 |
|
מכשיר חצי אוטומטי לחיתוך חוטים 5D07 |
מסרק 2671-0773 GOST 21761-76 |
ראש 2681-0023 GOST 21761-76. צמיגים עם לסתות מרוכזות בעצמם |
טבעת הברגה М24×1.5. Pr ו- NOT. |
|
מכונת שחיקה מעגלית 3M151 |
גלגל השחזה PP300×30×24A40PS1-S2 6K5 50 m/s 1kl.A GOST 2424-83 |
מרכז קדמי, אחורי GOST 13214-79 צווארון GOST 16488-79 |
שדרת סטייפלס ולא. דגימות חספוס GOST 9378-75 |
מקדחה 2300-6173 (f5.00) GOST 10902-77
קליפר ШЦ-I - 250-630 - 0.05-1 GOST 166-89
קליפר ШЦ-I - 125 - 0.05-1 GOST 166
קליפר ШЦ-I - 125 - 0.10-1 GOST 166
חצובה ШМ-I-8 GOST 10197-70
מחוון ICH02 cl. 1 GOST 577-68
סוג גוניומטר 1-2 GOST 5378-88
מיקרומטר MK50-1 GOST 6507
מיקרומטר MK25-1 GOST 6507-90
סוגר 061 OST 95 1960-78 על חתך. קוֹטֶר
סוגר СР 50 GOST 11098-75
טבעת 8211-0094 6 גרם (M24 X1.5-PR) GOST 17763-72
טבעת 8211-1094 6 גרם (M24 X 1.5-NOT) GOST 17764-72
Cork 8133-0630 (f5) H14 GOST 14807-69
2. תכנון ציוד טכנולוגי, כלי מדידה וחיתוך
2.1 בחירה והצדקה להתקנת חלק במתקן
משרטוט החלק עולה כי לצורך פעולת כרסום המפתח יש להשתמש במתקן מיוחד כדי להדק את החלק על המכונה. בתוכו, חומר העבודה מבוסס על פריזמה ושני תומכים. מכיוון שהמתקן משמש בייצור בקנה מידה גדול, עליו להיות מצויד במכשיר הידוק מהיר. דרישות אלה מתקיימות על ידי ההנעה הפנאומטית של מנגנון ההידוק.
2.2 תיאור טכני של התכנון ועקרון הפעולה של המכשיר
המכשיר מורכב מגוף, פריזמת התקנה, מתקן הידוק מנוף. צילינדר פנאומטי בוכנה חד פעולת מאומצת כהנעה כאשר אוויר דחוס מסופק לחלק העליון של הגליל הפנאומטי, הבוכנה עם המוט יורדת ולוחצת על החלק באמצעות תמסורת מנוף, כלומר החלק קבוע. כאשר נפסקת אספקת האוויר הדחוס לחלל העליון, הקפיצים המורכבים על מנגנון ההידוק מעלים את המהדק, ואיתו עולים המוטות ומוט הבוכנה והחלק משתחרר.
2.3 פיתוח תכנית עיצוב לחיזוק וחישוב מנגנון ההידוק
חומר העבודה מבוסס על רכיבי ההרכבה של המתקן ונלחץ אליהם על ידי מהדק עם כוח Q, וכוח החיתוך Po פועל בכיוון מאונך. כוח החיתוך Po מנוגד על ידי כוח החיכוך T בין משטח התמיכה של המתקן למישור הבסיס התחתון של החלק, כמו גם בין המישור העליון של החלק למשטח ההידוק.
אורז. 4
הבה נרכיב את משוואת שיווי המשקל של כל הכוחות הפועלים על חומר העבודה ביחס לציר Y:
ΣF yi =Q – 2Rsina/2=0
כוח ההידוק הנדרש נקבע מהביטוי:
kP o \u003d Qf 1 + 2Rf 2
, איפה
מקדם בטיחות k-clamp.
k 0 =1.5 - מקדם בטיחות מובטח.
k 1 \u003d 1.0 - מקדם תוך התחשבות בשינוי בקצבה
k 2 \u003d 1.4 - מקדם שלוקח בחשבון את הגידול בכוח החיתוך כאשר הכלי הופך עמום.
k 3 \u003d 1.2 - מקדם תוך התחשבות בעלייה בכוח החיתוך עם חיתוך מופרע
k 4 \u003d 1.0 - מקדם תוך התחשבות בקביעות כוחות ההידוק
k 5 \u003d 1.0 - מקדם המאפיין רק מנגנוני הידוק ידניים
k 6 \u003d 1.0 - מקדם תוך התחשבות בנוכחות של רגע נוטה לסובב את חומר העבודה.
a= - זווית פריזמה
f 1 \u003d f 2 \u003d 0.15
חישוב מנגנון הידוק:
קבע את גודל הכונן:
ר ו =0,785 ד 2 עח
p \u003d 0.4 N / m 2 \u003d 4 kgf / cm 2 - לחץ ספציפי של אוויר דחוס;
=0,7.
עיגלו את הקוטר המתקבל לערך הקרוב ביותר.
קוטר מוט: d=0.25D=0.25*100=25 מ"מ.
רשימת ספרות משומשת.
א.פ. גורבצביץ'.עיצוב קורס לטכנולוגיה הנדסית. מינסק: בית ספר גבוה, 1983.
א.ג. קוסילובהו ר' ק' משצ'רייקוב.מדריך של טכנולוג בונה מכונות. בשני כרכים. כרך 2. מ.: "הנדסה", 1985.
"מצבי חיתוך מתכת". מדריך בעריכת Yu.V. ברנובסקי. מ' "הנדסה", 1972.
א.ג. קוסילובהו ר' ק' משצ'רייקוב.מדריך של טכנולוג בונה מכונות. בשני כרכים. כרך 1. מ.: "הנדסה", 1985
א.ק. גורושקין.מכשיר לכלי חיתוך מתכת. מדריך מהדורה 7, מתוקן והושלם. מ.: משינוסטרוניה 1979
"עיבוד מתכת": מדריך נערך על ידי א.א. פאנובה. - מ.: משינוסטרוניה, 1988.
ב.ל. בספלוב, ל.א. גלזר, I.M. קולסובטכנולוגיה הנדסית מ., "הנדסה", 1973
עיצוב טכנולוגיה הנדסית אוטומטית: פרוק. להנדסת מכונות. מוּמחֶה. אוניברסיטאות/ אוֹתָם. ברנצ'וקובה, א.א. גוסב, יו.בי. קרמרנקו ואחרים; ed. יו.מ. סולומנצב. - מהדורה שנייה, ר'. - מ .: גבוה יותר. בית ספר, 1999
חלקים של המעמד "פירים" מאופיינים בעובדה שהם נוצרים בעיקר על ידי משטחים חיצוניים של סיבוב סביב ציר אחד. אורך הפיר גדול בהרבה מהקוטר.
בעיצובים מסוימים, עשוי להיות חור מרכזי פנימי.
במונחים של מטרה, עיצוב, משקל, דיוק עיבוד, חומר ואינדיקטורים אחרים, חלקים ממעמד זה מגוונים מאוד.
בציוד גלגול משתמשים בפירים במשקל ממספר קילוגרמים עד 20-30 טון ואף יותר בקטרים של עד -800-1200 מ"מ.
המחלקה "פירים" מחולקת לקבוצות העיקריות הבאות: צירים וסרנים חלקים; צעד; חָלוּל; עם משטחים עקומים וקוניים בצורת.
בכל קבוצה, הפירים מחולקים לסוגים, הנבדלים רק בגודל המשטחים לעיבוד.
בעת עיבוד חלקים ממחלקת "פירים", יש צורך:
1. שמור על הציר ישר. היישור והישור של כל החלקים של הצירים והסרנים חייבים להיות בתוך הטלרנסים שנקבעו.
2. שמור על משטחי המהפכה קונצנטריים סביב הציר. האליפטיות וההתחדדות של הצווארים המעובדים חייבים להיות בגבולות הקוטר.
3. כך שערך היציאה הרדיאלית של רכזי מיסב הציר למחסני האיתור נשמר בטווח של 0.02-0.03 מ"מ.
4. טפלו במשטחים של עמודי המיסבים לגלגלי שיניים, גלגלות וגלגלי תנופה בניקיון דרגה 6, למיסבים מתגלגלים בניקיון בדרגה 7, וחביות גלגול בניקיון בדרגה 7-8.
5. חותכים את הקצוות והמדפים בניצב בדיוק לציר.
6. תנו למפתחות, השפלינים והאלות את הפרופיל הנכון והניחו אותם במקום מסוים על פני הפיר.
7. שמרו על קשיות משטחי העבודה שצוינו על ידי המעצב.
הבחירה של חומר עבודה לפיר נקבעת על פי מטרת הפיר, מותג החומר שממנו צריך לעשות את הפיר ותכונות העיצוב שלו.
עבור רוב הצירים לשימוש כללי, פלדת פחמן בדרגות St. 5, אמנות. 6, פלדה 40 ו-50. פירים קריטיים במיוחד עשויים מפלדות סגסוגת גבוהה: כרום, כרום-מוליבדן, כרום-סיליקון וכו'. לייצור גלילים מתגלגלים, בחלק מהמקרים ברזל יצוק סגסוג בתוספת כרום וניקל וגם ברזל יצוק שונה משמשים - שבהם מגנזיום הוא משנה. קשיות משטחי העבודה, בהתאם לייעוד הגלילים, נעה בין 30 ל-75 יחידות שור.
חלקי פיר מטופלים מראש בסדר הבא; עריכה, סימון, חיתוך, חיתוך ומרכז, בקרה.
הפעולות העיקריות בעיבוד פירים הן פנייה, במהלכה מוסר עיקר החומר - הקצבה, כתוצאה מכך ניתנת לפיר את הצורה והמידות הנדרשות של המשטחים העיקריים.
פנייה גסה מספקת שיעורי דיוק 4-5 ושיעורי ניקיון 3-4. העיבוד מתבצע עם עומק חיתוך של 5-25 מ"מ או יותר, עם הזנות של 0.5-3 מ"מ/סל"ד ובמהירות חיתוך של 30-40 מ"מ/דקה. בעת חיספוס של מוצרים מגולגלים, מתקבלות תוצאות טובות במקרה של שימוש בחותכים עם לוחות פלדה במהירות גבוהה. בעת עיבוד פרזול כבד, התוצאות הטובות ביותר מתקבלות עם חותכים עם תוספות סגסוגת קשה T5K10 ו-T15K6. החיספוס מתבצע בעיקר על פי עקרון חיתוך החשמל. כדי להפחית את הזמן העיקרי ואת השימוש המלא במכונה, נעשה שימוש באמצעים הבאים:
שני חותכים מותקנים בקליפר, לכל אחד מהם יש טווח שונה, מסיר חלק מסוים מהקצבה לעומק;
החל חותכים עם כמה קצוות חיתוך, אשר "יכולים לחתוך עם התנועה קדימה ואחורה של הקליפר;
נעשה שימוש בחותכי צעד, המפחיתים את רוחב השבב המוצק ובכך מפחיתים את כוח החיתוך;< ,
בעת עיבוד פירים ארוכים וכבדים, משתמשים בשניים ושלושה קליפרים, תוך שימוש בקליפרים הקדמיים והאחוריים של המכונה.
חיספוס גל מתבצע בדרך כלל בשתי הגדרות. לפנייה, משתמשים בחותכי דרך ישרים או כפופים ימינה ושמאלה, לחיתוך קצוות ומדפים - חתוכים ולעיבוד פילטים - חותכי פילה מעוקלים וקעורים מיוחדים. פילטים בעלי רדיוס גדול (30 מ"מ ומעלה) נחתכים לעתים קרובות על ידי שילוב הזנות אורך ורוחבי לפי תבניות, או באמצעות מכשיר סיבובי מיוחד המותקן על השקופית הצולבת של המחוגה.
כאשר מעבדים פירים מדורגים, רצוי לעבד תחילה את השלבים המסיביים יותר בקוטר גדול. הנפוצות ביותר הן שתי תוכניות לעיבוד פירים מדורגים (איור 45).
עם הבדל קטן בקטרים של השלבים, התוכנית של איור. 45, א, עם הבדל משמעותי בקטרים ובפירים בקוטר גדול - הדיאגרמה של איור. 45, ב. לפעמים נעשה שימוש בעיבוד משולב תוך שימוש בשתי הסכמות. כדאי לבחור בשיטה שמספקת את הביצועים הטובים ביותר ועוד שימוש מלאמְכוֹנָה.
בעת הפיכת משטחים חרוטיים ומעוצבים, הם משתמשים בשילוב של הזנות אורך ורוחב, עיבוד על פי תבניות, או מכונות צילום.
השיטה הראשונה, הדורשת הסמכה גבוהה של המבצע, משמשת בייצור יחיד וקטן.
קונוסים קצרים ותלולים מעובדים על ידי סיבוב החלק העליון של הקליפר והזנת החותך בזווית השווה למחצית הזווית של החרוט. קונוסים ארוכים ורדודים מסובבים על ידי ערבוב עמוד הזנב כך שהגנרטיקס של החרוט מקביל לציר הציר ולתנועת האורך של החותך. שיטה זו פשוטה למדי וניתנת ליישום על כל מחרטה, אך ישנה תפעול ובלאי לא אחיד של המרכזים, כמו גם התמוטטות של החורים המרכזיים.
בעת עיבוד משטחים מעוצבים באורך קטן, נעשה שימוש בחותכים בצורת מיוחד, אשר מעובדים בדרך כלל עם הזנה רוחבית. הפרופיל של החותך לאורך קצה החיתוך מתאים לפרופיל ההפוך של החלק. מבין החותכים המעוצבים, חותכי הברגה, פילה וחריצים משמשים לעתים קרובות יותר בהנדסה מתכות.
בעת עיבוד פיר חלול מחומר עבודה מוצק, לאחר סימון, כרסום הקצוות ומרכוז, מתבצעת סיבוב גס משטח חיצוניעל ידי הרכבת הפיר במרכזים וצ'אק. החור נקדח ומשעמם על מחרטה עם מנוחה יציבה או על מכונת משעמם אופקית משעממת. לאחרונה, קידוח עם מקדחים חלולים הפך נפוץ, כאשר הליבה מוסרת בצורה של פיר נפרד. שיטה דומה משמשת לחורים בקוטר של יותר מ-100 מ"מ.
תלוי ב מפרטיםניתן להעביר את הפיר לאחר חיספוס לגימור או לטיפול בחום ביניים עם גימור מכני לאחר מכן. בכל המקרים הללו יש להשאיר קצבה לאחר חיספוס. הקצבאות לפנייה עדינה לאחר סיבוב גס של חלקים מגולגלים נותרות 0.5-2 מ"מ לכל צד. עבור פירים מזויפים, ההפרשות נלקחות להיות 2.5-5 מ"מ, אשר מוסבר, מצד אחד, בגדול מימדים כולליםפירים, ומאידך בכך שהחספוס בוצע בתנאים קשים יותר, תוך מאמצים גדולים יותר ועיוותים תרמיים, כתוצאה מכך שכבת פני השטח נפגעה לעומק רב יותר. אם לאחר חיספוס מבוצע עיבוד תרמי, הקצבאות מוגדלות פי 1.5-2 בערך על מנת לפצות על עיוות אפשרי ונזק לשכבת פני השטח של החלק במהלך טיפול בחום.
חומר העבודה שהוכן לטיפול בחום חייב לחזור על כל ההבדלים בקטרים בין שלבי הפיר. אבל אם ההבדל בקטרים של שלבים סמוכים אינו עולה על 10 מ"מ, אז הם מסובבים בקוטר אחד. לא צריכים להיות מעברים חדים או פינות. במהלך טיפול בחום בצורה של נורמליזציה או הזדקנות, המבנה משתפר ומתבטלים מתחים פנימיים. עם הקצבה משמעותית לאחר טיפול בחום, הפעולה מחולקת לשני מעברים: חצי גימור וגימור. האחרון מיוצר בעומק חיתוך של 1-2 מ"מ.
במעבר הגמר, לחותכים יש חלק עליון מעוגל ברדיוס של 2-3 מ"מ או קצה חיתוך רחב יותר עם Zcp = 0°, שאופייני לחותכים מסוג Kolesov, המאפשרים לעבוד עם הזנה מוגברת של 1 -2.5 מ"מ/סל"ד ומספקים ניקיון עבודה קפדני כיתה ו'.
אם אין מכונות שחיקה כבדות בסדנה, ועל פיר גדול יש צורך לעמוד בצעדים נפרדים לפי המחלקה השנייה, אז הם מסובבים עם חותכי קפיץ רחבים עם עומק חיתוך של לא יותר מ 0.1-0.3 מ"מ. כאשר נדרש ניקיון מחלקה ז', מפעילים את הרולר המותקן במחזיק מיוחד במשענת המכונה. טיפול ברולר מספק לא רק ניקיון גבוה, אלא, על ידי יצירת התקשות עבודה על פני השטח, מגביר את הצפיפות שלו ואת עמידות הבלאי שלו.
אין קצבה מיוחדת לגלגול עם רולר. בפועל, הקצבה היא בסובלנות של 0.01-0.02 מ"מ לכל צד.
בגימור ובגימור יש לשים לב לדיוק התקנת הפיר והכלי, לקשיחות המערכת כולה, לגיאומטריה של כלי החיתוך ולאיכות משטחי האיתור: חורים מרכזיים ( בעת עיבוד שבבי במרכז - pax) וחגורות וצוואר מעובדים (בעת עיבוד ב-lunettes). יש לצמצם למינימום את כוחות החיתוך והשפעות תרמיות על החלק. במקרים מסוימים, העיבוד של פירים מסובך על ידי העובדה שניתן למקם מפתחות, חריצים או אלות על פני השטח שלהם.
לעיבוד Paeov מפתח, הפיר מסומן, ולאחר מכן מועבר למכונת כרסום.
עבור פירים קטנים ובינוניים, המפתחות מעובדים במכונות כרסום אנכיות וכרסום מפתחות עם חותכי קצה או מיוחדים. במקרה הראשון, בעת ביצוע חריצים סגורים, יש צורך לקדוח כדי להכניס את החותך. כרסום פירים כבדים על פי סימונים במכונות כרסום אופקיות וכרסום אורכיות עם כרסום קצה וקצה - האחרונים נמצאים בשימוש נרחב בעיבוד של מסלולי מפתח משיקים.
חריצים מחורצים מעובדים בשיטת החלוקה או בשיטת הגלגול. בשיטת החלוקה מתבצע סימון ראשוני ולפירים קטנים ובינוניים משתמשים גם בראש מחלק. חיתוך לפי שיטת הגלגול מתבצע במכונות כרסום חריצים מיוחדות באמצעות חותכי מחורצים תולעים.
עיבוד האלות בקצוות גלגולים מתבצע במכונות משעממות לסימון או במכונות כרסום קלות חד-צדדיות ודו-צדדיות מיוחדות. כלי החיתוך הוא חותכים המותקנים על המדרל או בציר המכונה, או ראשי כרסום מיוחדים.
אם לגלילי הגלגול להעברת סיבוב יש להבים שטוחים עם חתך בקצוות, אזי יש צורך בפעולות הבאות בעת עיבוד להבים אלה:
I. סימון - צייר קווי מרכז.
II. הקצעה - הקצעה של הלהב -
פאי. סימון - סמן את הלוע.
IV. קידוח - לקדוח את הגרון.
V. מסגר - דופקים את החלק הקדוח של הלוע. .
VI, משעמם - במכונה משעממת, טוחנים את הסככה לאורך קו המתאר הפנימי.
ניתן לבצע את הפעולה האחרונה גם בפלנר קרוס נייד. הבחירה במכונה כזו או אחרת נקבעת על פי זמינות הציוד, גודל הגרון והכלכלה. כדוגמה, להלן זרימת תהליך לעיבוד הציר המדורג המוצג באיור. 46. חומר פיר - פלדת כרום 20XA עם חוזק מתיחה av = 65 ק"ג/ממ"ר - בילט - פרזול המתקבל בחישול חופשי. הקצבאות נבחרות לפי התקנים.
רצף הפעולות במהלך העיבוד הוא כדלקמן: I. סימון - סמן את הלהב.
II. משעמם - טוחנים את הקצוות, מצמצמים את קווי המרכז, מסמנים את המרכז והמרכז.
6 הזמנה 222
III. סיבוב - הופכים לפי מידה, חותכים קצוות ושוליים
IV. סימון - סמן את פתח המפתח.
V. כרסום - כרסום מפתח המפתח.
תאנה. 46. פיר מדורג והריק שלו.
VI. טחינה - טחינה צווארים.
VII. הפיכה - מעבדים פילטים וחותכים קצוות ושוליים לפי גודל.
ח. מנעולן - להסיר כתמים.
TP זה כולל את הפעולות הבאות:
פונה, מרוכזת
סיבוב (סיבוב) של יציבות פיר
טחינה מוקדמת
כרסום מפתחות
כרסום ספליין
עיבוד חוטים
טיפול בחום
תיקון חורים מרכזיים
שחיקה עדינה של חוטבי פיר
טחינת ספליין
כיול ושחרור חוטים
שְׁטִיפָה
לִשְׁלוֹט
1.2.1. מוט פונה וממרכז
בייצור בקנה מידה בודד וקטן, הקצוות מעובדים במכונות חריטה וכרסום. הריכוז מתבצע בקידוח, סיבוב, סיבוב ואופקי מכונות משעממות.מרכוז יכול להתבצע או עם שני כלים (מקדח טוויסט וכיור) או עם מקדחה מרכזית אחת משולבת. זווית הקידוח של המקדחה היא בדרך כלל 60 0, עם זאת, עבור ריקים פיר כבדים זה גדל ל 75 0 או 90 0.
במקרים מסוימים, לכלי חיתוך יש שיפוע נוסף בזווית של 120 0, המגן על החור המרכזי מפני חריצים במקרה של נזק מקרי לקצוות הפיר.
בייצור סדרתי והמוני, נעשה שימוש במכונות כרסום ומרוכז חצי אוטומטיות, שעליהן טוחנים 2 קצוות בו-זמנית (עמדה 2 באיור 1.3.), ואז מרוכזים 2 חורים (עמדה 3).
אורז. 1.3. - תוכנית עיבוד פיר על מכשיר חצי אוטומטי מרוכז כרסום.
1.2.2. סיבוב פיר
סיבוב פיר כולל בדרך כלל פעולות חיספוס וגימור. בסיבוב גס, רוב הקצבה מוסרת על ידי עבודה עם עומק חיתוך גדול יותר וקצב הזנה גבוה.בייצור בקנה מידה בודד וקטן, הפנייה מתבצעת על פניה מכונות אוניברסליות. בעת עיבוד פירים מדורגים, נעשה שימוש בדפוסי חיתוך שונים, לדוגמה, המוצגים באיור. 1.4.
בתרשים באיור. 1.4., באורך הכולל של תנועת החותך , כלומר פחות מאשר בתרשים באיור. 1.4., א. עם זאת, מספר מהלכי העבודה והעזר גדול יותר.
אורז. 1.4. - תוכניות סיבוב פירים
בעת בחירת ערכת חיתוך, הם שואפים להשיג פרודוקטיביות מקסימלית ועלות מינימלית של הפעולה. במקביל, נלקחים בחשבון מידות הפיר, אופן ההגדרה והבקרה של המידות, סובלנות וגורמים נוספים.
לפעמים, בהבדל גדול בקטרים של השלבים, הם נוטים לא להחליש את הפיר כמה שיותר זמן ולהפוך את השלבים של הקוטר הקטן ביותר אחרון.
בעת סיבוב פירים ארוכים שאינם קשיחים, משתמשים במשענות קבועות או ניתנות להזזה. המנוחה הקבועה מותקנת על מיטת המכונה. המנוחה היציבה הניידת נעה על הקליפר והזיזים שלה עוקבים אחר החותך (איור 1.5., א).
אם יש צורך להבטיח את יישור המשטח המעובד עם משטח 2 (איור 1.5., ב), אזי ה-lunette ממוקמים מול החותך על פני השטח.
אורז. 1.5. - תכנית של סיבוב הפיר תוך שימוש במנוחה יציבה
נכון לעכשיו, מכונות CNC משמשות בייצור בקנה מידה קטן. הם מאפשרים לך להפוך את מחזור העיבוד לאוטומטי, להשתמש בתנאי חיתוך מוגברים, להגדיל את הפרודוקטיביות, ליישם תחזוקה מרובת מכונות, להפחית את המחסור בכוח אדם מיומן, להפחית את הפסולת ולצמצם את זמן ההכנה לייצור.
בייצור בקנה מידה גדול והמוני עבור הפיכת פירים, נעשה שימוש במכונות ריבוי חיתוך והידרוקופיה ומכונות חצי אוטומטיות. בדרך כלל יש להם 2 קליפרים - אורכיים ורוחביים, המשמשים לחיתוך קצוות, לקידוח חריצים ולסיבוב צורני.
הקליפרים יכולים לעבוד בו זמנית. במכונות ריבוי חיתוך, במידת הצורך, נעשה שימוש בסיבוב עם צלילה והזנה אורכית לאחר מכן (איור 1.6., ב).
אורז. 1.6. - התוכנית של הפיכת הפיר על חצי אוטומטי רב חיתוך
בהשוואה למחרטות לשימוש כללי, מחרטות רב-כלים מגדילות את הפרודוקטיביות על ידי קיצור אורך המהלך, פעולה בו-זמנית של החותכים, ועל ידי ביטול הזמן המושקע בהחלפת חותכים, סיבוב עמוד הכלי ותנועת סרק של הקליפר.
על התמיכה האורכית של מכונת ההידרוקופיה, מותקן חותך 1, המותאם לגודל של צוואר פיר אחד בלבד. השגת המידות הנותרות מסופקת על ידי מכונת צילום ומערכת מעקב. במקביל, מספר המדידות מצטמצם, מוחל מצב חיתוך גבוה יותר מאשר בעבודה עם הזנות ידניות.
הפירים מסובבים במהלכת עבודה אחת או כמה, בעוד מכונות הצילום מוחלפות אוטומטית על ידי סיבוב התוף עם מכונת הצילום.
במקרים בהם ניתן לעבד את הפיר במכונה חצי אוטומטית חצי-אוטומטית חיתוך רב-ציר חד-ציר, בחירת הציוד נעשית על בסיס בדיקת היתכנות.
זה לוקח בחשבון את השיקולים הבאים:
בחריטה מרובה חתכים עם חלוקה של אורך העיבוד, אורך מהלך העבודה קטן יותר מאשר בעיבוד העתקה.
זמן ההגדרה וההתכווננות מחדש עבור מכונות הידרוקופיות הוא הרבה פחות מאשר עבור מכונות ריבוי חותכים.
מספר החותכים ותנאי החיתוך במכונות מרובות חיתוך מוגבלים לעתים קרובות על ידי תאימות של חלקי עבודה וכוח מכונה לא מספיק. במכונת הידרוקופיה, ניתן לעבוד עם קצב הזנה גבוה של תנועת החיתוך הראשית.
בקשר עם האמור לעיל, התפוקה של מכונות ההידרוקופיות היא במקרים רבים גבוהה יותר.
הדיוק של עיבוד ריבוי חיתוך מושפע משגיאות במיקום היחסי ובלאי לא אחיד של החותכים. בעת עיבוד משטח אחד עם מספר חותכים, נוצרים מדפים בגבולות המקטעים. במכונות הידרוקופיות, שגיאות אלו נעדרות, כך שניתן להשיג דיוק ממדי גבוה יותר ופחות חספוס.
1.2.3. גימור של משטחים גליליים חיצוניים
חריטה עדינה, השחזה, ליטוש, ליטוש, סופר-גימור, סיבוב גלגלים וכו' משמשים לגימור המשטחים הגליליים החיצוניים.1.2.2.1. סיבוב עדין
סיבוב עדין משמש לעתים קרובות יותר לגימור חלקי עבודה העשויים ממתכות וסגסוגות לא ברזליות, לעתים רחוקות יותר עבור חלקי עבודה עשויים פלדה וברזל יצוק. זה מוסבר על ידי הקשיים של טחינת סגסוגות לא ברזליות עקב "העמסה" של גלגל השחזה.עיבוד שבבי מתבצע עם חותכי יהלום, קומפוזיט, מתכת-קרמיקה וחותכים המצוידים בסגסוגות קשות, במהירויות גבוהות של תנועת החיתוך הראשית, מהירויות הזנה נמוכות ועומקי חיתוך.
סיבוב עדין מאפשר לך לקבל דרגת 6 ... 7 של דיוק עיבוד וחספוס פני השטח מיקרומטר.
ביצועי העיבוד גבוהים מהשחזה. בייצור בקנה מידה גדול והמוני עבור פנייה עדינה, נעשה שימוש במכונות מיוחדות במהירות גבוהה בעלות דיוק גבוה ועמידות בפני רעידות.
1.2.2.2. שְׁחִיקָה
זוהי השיטה העיקרית לגימור המשטחים הגליליים החיצוניים. היתרון של השחזה הוא היכולת לתקן שגיאות בחומר לאחר טיפול בחום. עם שחיקה עדינה קונבנציונלית, העיבוד מתבצע לפי דרגות דיוק של 6-7, עם חספוס פני השטח של 1.2 ... 0.3 מיקרון.שחיקה עדינה מעניקה דרגת דיוק 5 וחספוס של 0.16 ... 0.8 מיקרון. זה מתבצע על ידי מעגל עם גרגירים במהירות גבוהה של סיבובו, מהירות סיבוב נמוכה של חומר העבודה ועומק חיתוך קטן.
השחזה מתבצעת על עגול וחסר מרכזי מכונות שחיקהעם הזנה אורכית של המעגל או לפי שיטת הסיבוב (איור 1.7.)
A - עם הזנה אורכית; ב, ג - לפי שיטת (שיטת) הסיבוב
אורז. 1.7. - תוכנית השחזה במכונת שחיקה עגולה:
השחזה לפי שיטת הסיבוב היא פרודוקטיבית יותר, היא משמשת בייצור בקנה מידה גדול והמוני בעיבוד של משטחים גליליים ומעוצבים.
עבור שחיקה בו זמנית של כמה צווארים משמשים מכונות מיוחדות, עבודה עם מספר עיגולים על מנת להפחית את זמן העזר במהלך ההשחזה, התקני בקרה אקטיביים משמשים למדידת חלקי עבודה במהלך ההשחזה, וכן מכשירים לעצירה אוטומטית של המכונה כאשר מגיעים לגודל נתון.
בהשחזה ללא מרכז (איור 1.8.) מניחים את חומר העבודה בין שני גלגלי השחזה, שאחד מהם (קוטר גדול יותר) הוא שחיקה, והשני מוביל.
אורז. 1.8. - ערכת שחיקה ללא מרכז
גלגל שחיקה 1 מסתובב במהירות של 20-35 מ' לשנייה, גלגל מניע 2 - במהירות של 20-30 מ' לדקה. חומר העבודה 3 אינו קבוע בשום דבר, אלא נתמך על ידי תומך 4 עם שיפוע המכוון לכיוון המעגל המוביל.
כוח האחיזה של חומר העבודה עם מעגל ההנעה גדול יותר מאשר עם הטחינה. זה נובע מהסיבות הבאות:
הגברת כוח החיתוך עם ירידה במהירות הגלגל
ייצור עיגולים מובילים על החיבור, מה שמגדיל את מקדם החיכוך בין המעגל לחומר העבודה.
בהשחזה ללא מרכז עם תנועה אורכית של הזנת חלקי העבודה, ציר הגלגל המניע אינו מקביל לציר גלגל ההשחזה. בזכות זה, בלי מנגנון מיוחדהזנה, חומר העבודה מועבר במהירות איפה
- מהירות הסיבוב של המעגל המוביל.
עם זווית גדלה חציית צירי המעגלים, ביצועי העיבוד עולים, אך איכות פני השטח מתדרדרת, כך שבדרך כלל
.
כדי לשפר את דיוק העיבוד, באמצעות שחיקה מתבצעת לעתים במספר משיכות עבודה. בייצור בקנה מידה גדול והמוני, ניתן לבצע עיבוד ברצף במספר מכונות המחוברות לאוטליין.
בשחיקה ללא מרכז לפי שיטת הצלילה, צירי העיגולים מקבילים לרוב. ראשית, המעגל המוביל נסוג מהשחזה, ואת חומר העבודה מניחים על התמיכה, ואז המעגל המוביל מובא אל חומר העבודה וההזנה הצולבת מתבצעת עד לקבלת הגודל שצוין.
בהשוואה לטחינה מרכזית, לטחינה ללא מרכז יש את היתרונות הבאים:
אין צורך למרכז את חומר העבודה, וזה חשוב במיוחד עבור חלקים המעובדים במכונות צריח ומכונות אוטומטיות;
קצבאות העיבוד מופחתות באופן משמעותי, מכיוון שבגלל השימוש במשטח המעובד כבסיס טכנולוגי, השפעת שגיאת הריכוז על הקצבה מתבטלת;
אין צורך להשתמש במנחים יציבים בעת שחיקה של פירים ארוכים ודקים;
קל יחסית לבצע אוטומציה של מכונות שחיקה ללא מרכז ולשלב אותן באוטוליין;
מספק פרודוקטיביות גבוהה יותר מאשר בעת טחינה במרכזים;
בשל קלות השליטה במכונה, דיוק גבוה מושג עם מיומנות ממוצעת של המטחנה;
שגיאת העיבוד הנגרמת על ידי בלאי גלגלים קטנה פי 2 מאשר בהשחזה במרכזים, בגלל בלאי הגלגלים משתקף ישירות בגודל הקוטר של חומר העבודה, ולא בגודל הרדיוס.
1. הזמן המושקע בהתקנה והתאמת מכונות כאלה הוא די גדול ומשתלם עם קבוצות גדולות של חלקי עבודה. לכן, השחזה ללא מרכז משמש לרוב בתעשיות הרכב והמיסבים.
2. מסלולי מפתח, חריצים, חורים, שברים במשטח המעובד פוגעים בפעולה תקינה ואף הופכים אותה לבלתי אפשרית.
3. עם השחזה ללא מרכז, קשה להבטיח את העגלגלות של המשטח המעובד.
4. קשה להשיג יישור של המשטח המלוטש עם משטחים אחרים שעובדו בעבר.
1.2.3.3. ליטוש וגימור על
ליטוש עם גלגלים רכים עשויים לבד, לבד או סרט מבוצע במהירויות גבוהות של הכלי, שעל פניו מוחל תערובת של אבקת שוחקים עדינה וחומר סיכה. ליטוש מספק חספוס נמוך של פני השטח (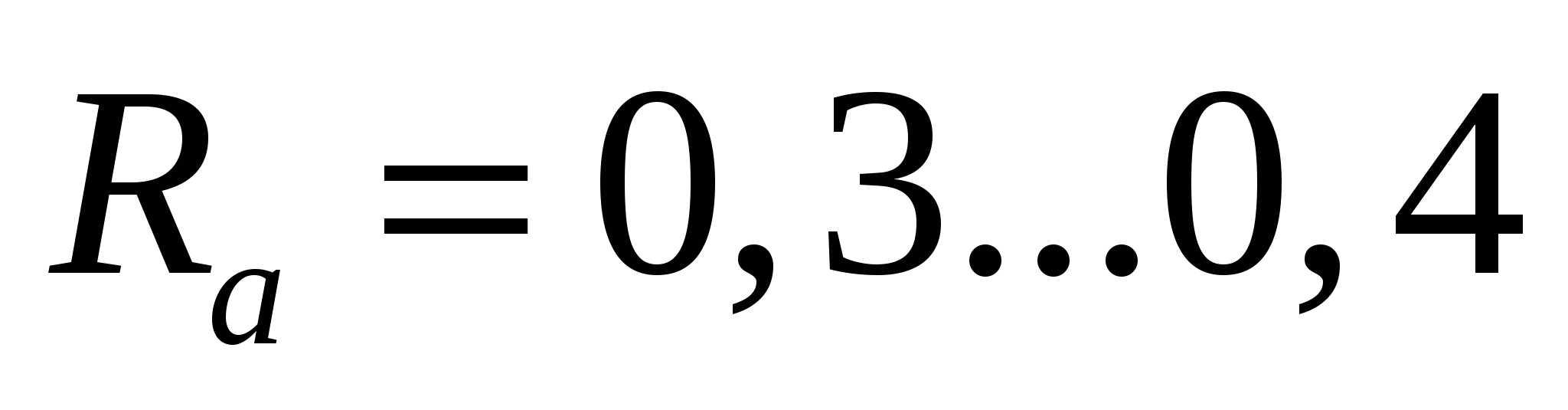
Superfinishing (גימור עם מוטות מתנודדים) מיישם את העיקרון של עקבות בלתי חוזרת, הטמון בעובדה שאף גרגר שוחק לא עובר פעמיים באותו נתיב. לשם כך, בנוסף לחומר מסתובב, במהירות נמוכה (1-2.5 מ' / דקה) ובתנועה אורכית של הסורגים (איור 1.9.), הם נאמרים מ 200 עד 1000 תנודות לדקה עם משרעת קטנה.
עקב תנועות תנודות, גודל גרגר קטן של המוטות ולחץ נמוך, מובטח חספוס קטן של חומר העבודה ( מיקרומטר).
אורז. 1.9. - תוכנית עיבוד הפיר עם מוטות שוחקים.
התהליך מתבצע בשימוש בנוזל חיתוך ומתקדם באופן הבא: ברגע הראשוני, שטח המגע של הסורגים עם המשטח המטופל קטן ולחץ המוט משמעותי, מה שגורם להסרת מתכות אינטנסיבית . בעתיד מפעילים את הסורגים, הלחץ יורד ותהליך החיתוך מאבד מעוצמתו.
גימור-על אינו משפר את המקרו-גיאומטריה של חומר העבודה, ולכן טיפול מקדים חייב להבטיח את הצורה הגיאומטרית הנכונה של החלק. קצבת Superfinish בדרך כלל לא נשארת.
1.2.4. עיבוד חוטים
1.2.4.1. השחלה בחותכים ומסרקים
בְּ הַשׁחָלָהעל מחרטות, חומר העבודה מקבל סיבוב, והחותך מועבר לאורך ציר חומר העבודה עם הזנה לכל סיבוב השווה לגובה החוט. דיוק הגובה נקבע על ידי הדיוק של השרשרת הקינמטית של המכונה, ודיוק פרופיל החוט נקבע על ידי הדיוק של השחזה והגדרת החותך. לכן, בתהליך העיבוד, הפונה שולט בדרך כלל ????????????????????????.בעת חיתוך חוטים במספר משיכות עבודה, ניתן לבצע את תנועת ההזנה הרוחבית של החותך, למשל, על פי הסכמות המוצגות באיור. 1.10. (א, ב). בעת שימוש בסכימה (א), היא מסופקת האיכות הטובה ביותרמשטח מעובד, וכאשר עובדים על פי סכימה (ב), צורת השכבה החתוכה מפשטת, תהליך החיתוך והסרת השבבים מקל. לכן, לפעמים מבצעים חיספוס לפי סכימה (ב), והשכבה האחרונה מנותקת לפי סכימה (א).
אורז. 1.10. – דפוסי חיתוך להשחלה.
בהשחלה עם חותך אחד במספר תנועות עבודה, קצה החיתוך שלו הופך במהרה לקהה וצורתו מתעוותת, לכן מומלץ להשתמש ב-2 חותכים להשחלה בגובה רב - חיספוס וגימור, או להשתמש במסרקי השחלה. על ידי הפחתת מספר המהלומות, מסרקים מספקים פרודוקטיביות מוגברת. החיסרון של מסרקים סטנדרטיים הוא שלא ניתן להשתמש בהם לעבודה נקודתית, כלומר. לחיתוך חוטים הסמוכים לצווארים בקוטר גדול יותר.
השחלה על מחרטות מתבצעת בדרך כלל במקרים הבאים:
כאשר חותכים חוטים על חלקי עבודה שהופעלו בעבר על אותה מכונה, כי זה מקטין את זמן העזר ומגביר את הדיוק של המיקום היחסי של המשטחים.
בעת ביצוע דיוק ברגים ארוכים.
בעת חיתוך חוטים בקוטר גדול או מגרש ופרופיל לא סטנדרטיים, אם רכישת כלי מיוחד בעל ביצועים גבוהים אינה מוצדקת בשל הפלט הקטן.
בעת חיתוך חוטים מלבניים.
הגדלת הפרודוקטיביות של השחלה על ידי הגדלת מהירות תנועת החיתוך הראשית במקרים רבים היא קשה בשל הקושי להחזיר במהירות את החותך, המעבד את החוט הסמוך למדף.
בייצור בקנה מידה גדול והמוני, חוטים נחתכים לעתים קרובות במכונות חצי אוטומטיות מיוחדות המהפכות את מחזור העיבוד הרב-מעבר לאוטומטי. בייצור בקנה מידה קטן, רצוי להשתמש במכונות CNC.
1.2.4.2. כרסום חוטים עם ראש נשי
הברגה עם ראש נקבה מתבצעת במכונות חיתוך ברגים וכרסום הברגה. חותכי קרביד 1 (איור 1.11.) מקובעים בראש החותך ומסתובבים במהירות של 150-450 מ' לדקה. הראש מכוון בזווית לציר חומר העבודה בהתאם לזווית ההברגה, ולכל סיבוב של חומר העבודה המסתובב לאיטו הוא נע לאורך צירו לפי כמות הצעד. האפקט הגדול ביותר מושג בעת עיבוד חוטים גדולים.אורז. 1.11. – דפוס חיתוך חוט עם ראש נשי.
1.2.4.3. השחלה במות וראשים מתרחבים מעצמם
בעת השחלה על מחרטות צריח ומכונות מודולריות, ניתן להשתמש במות ככלי. מחזיקי הקוביות מאפשרים לכלי לנוע בחופשיות כמות קטנה, או, כמו שאומרים, ליישר עצמי בכיוון האורך. זה מבטל שבירת הברגה כאשר מהירות התנועה של מחזיק התבנית לאורך ציר היצירה ומהירות הברגת התבנית על חומר העבודה אינן תואמות.החיסרון העיקרי של המות הוא הצורך בהברגה לאחר השלמת ההברגה, מה שמפחית את הפרודוקטיביות ואת איכות העיבוד.
בעיבוד שבבי עם ראשי חיתוך נפתחים מעצמם, אין צורך באיפור והפרודוקטיביות גדלה מאוד.
1.2.4.4. כרסום חוטים עם חותכי דיסק ומסרקים (קבוצתיים).
כרסום עם חותכי דיסק (איור 1.12.) משמש לעיבוד חוטים גדולים עם נפחי פלט גדולים מספיק. במקרה זה, העיבוד מתבצע ב-1-3 שלבי עבודה. חומר העבודה מסתובב באיטיות, והחותך המסתובב במהירות התנועה הראשית נע לאורך צירו עם הזנה לכל סיבוב השווה לגובה החוט.אורז. 1.12. - ערכת כרסום חוטים.
בהשוואה לחריטה, היתרון של כרסום הוא תפוקה גבוהה יותר, אפשרות לתחזוקה מרובת מכונות ושימוש בעובד בעל מיומנות נמוכה.
כרסום עם חותכי מסרקים (קבוצתיים) משמש להשגת הברגה חיצונית ופנימית קצרה עם גובה דק.
בניגוד לעיבוד חוטים עם חותך דיסק, הצירים של חותך המסרק וחומר העבודה מקבילים (איור 1.13.). אורכו של החותך הוא בדרך כלל 2-3 צעדים יותר מאורך החלק המשורשר של חומר העבודה.
אורז. 1.13. - תוכנית כרסום חוטים עם חותך מסרק.
בתחילת העיבוד, החותך הסיבובי נע בכיוון הרדיאלי וצולל לתוך חומר העבודה לעומק פרופיל החוט. במקרה זה, עבור סיבוב אחד של חומר העבודה, החותך נע לאורך הציר בגובה חוט (תנועת הזנה
). הכרסום מתבצע ב-1.2 סיבובים של חומר העבודה. יתרה מכך, בתחילת העיבוד יש צורך ב-0.2 סיבובים לחיתוך החותך, ובסוף - לניקוי עקבות החיתוך.
1.2.4.5. גלגול חוט
גלגול חוטים משמש בייצור בקנה מידה גדול וייצור המוני. בנוסף לפרודוקטיביות גבוהה, השיטה מאפשרת להשיג מבנה משטח מוקשה של המתכת, שכן סיבי החומר מעוותים מבחינה פלסטית ואינם נחתכים.החוט מגולגל עם מתלים שטוחים או גלילים מתגלגלים.
על קוביות שטוחות (איור 1.14.) יש חוט ישר (פיתוח חוט) עם אותו פרופיל וזווית עופרת כמו עם חוטים מגולגלים. החוט מגולגל במכה כפולה אחת של המחוון. מספר הפגיעות הכפולות בדקה מגיע ל-280.
אורז. 1.14. - ערכת גלגול חוט עם קוביות.
גלגול חוטים עם גלגלת אחת משמש מחרטות, צריחים ומכונות אוטומטיות עקב כוח רדיאלי חד צדדי. במקרה זה, כיפוף של חומר העבודה אפשרי.
לכן, גלגול חוטים עם שני גלילים עם תנועת הזנה רדיאלית הפך לנפוצה יותר (איור 1.15.).
גלגול חוטים יכול להתבצע גם עם שניים או ארבעה גלילים עם הזנה אורכית במרחק מרכז קבוע. מבחינת פרודוקטיביות, גלגול עם גלילים הוא בדרך כלל נחות מגלגול עם מתלים.
אורז. 1.15. - ערכת גלגול חוט עם רולים.
למעט חריגים נדירים ביותר, העיבוד של כל סוגי הפירים נבנה באמצעות מכונות מרכזיות, ובמקרה זה הטכנולוגיה מורכבת מהפעולות הבאות: חיתוך חלקי עבודה, חיתוך קצוות וריכוז, לאחר מכן פעולות הפיכה מתבצעות על מחרטות מרכזיות, לרוב. במכונות ריבוי חיתוך מסוג סטנדרטי, לאחר בעת הפיכת חומר עבודה מבוצעת פעולת חריץ, ולאחר מכן כל פעולות ההשחזה, כרסום מפתח מבוצע לרוב לפני פעולות שחיקת פיר.
לאחר השלמת כל העיבוד של הפיריםיש צורך לבצע ניקוי ספסל של חריצי המפתח, עקב עיוותם ברוחב לאחר השחזה עקב הידוק הקצוות. לכן, יש מפעלים שמעדיפים לטחון מפתחות, במיוחד אם הם חורצים מפתחות חצי עגולים לאחר שחיקה של הפיר. במקרה זה, עקב הרמה מסויימת של הקצוות, יש צורך לבצע גם פעולת ניקוי ידנית, כלומר שיוף, אולם פעולה זו היא פחות עמלנית מאשר במקרה הראשון, בנוסף, הסיכון לפגיעה בפיר במהלך הניקוי מצטמצם.
כל סיבוב הציר נעשה, ככלל, בשני התקנות על מחרטות רב חיתוך, הפיכת חלק מהפיר עבור כל התקנה. כמו כן, בהתאם לעיצוב הפיר ומצב הציוד, לעיתים הפיר מסתיים גם בסיבוב ומספר פעולות סיבוב קצרות שהן בגדר גימור, לרבות חיתוך קצוות הפילטים החתוכים, חריצים וכו'.
פעולת חריציםנעשה לעתים קרובות על מחרטה קונבנציונלית, באמצעות גליל אחד או שניים, מותקן במחזיק מיוחד. הגלילים מתגלגלים בהזנה אורכית תוך כדי לחיצה כנגד הפיר עד כדי כך שנוצר גלי פרופיל מלא במעבר אחד.
פעולות טחינהמיוצרים במכונות טחינה עגולות מרכזיות קונבנציונליות. רוב המשטחים נטחנים בתנועה אורכית של המוצר ביחס לעיגול, ורק במקרים מסוימים קיימת שיטה יעילה יותר של השחזה במעגלים רחבים, בהתאם לרוחב המשטח המיועד לעיבוד, תוך שימוש בהזנות רוחביות.
כרסום מפתחותמיוצר במכונות כרסום אופקיות פשוטות. בייצור מפתחות משתמשים בכלים ידניים קטנים בהצלחה רבה. מכונות כרסוםעם שליטה במנוף. למרות הפשטות והפרימיטיביות שלהן, מכונות כרסום כאלה מתגלות כנוחות מאוד ופרודוקטיביות מאוד עבור פעולות קצרות טווח כאלה.
בייצור של פירים ארוכים ודקים, מבצעים פעולת חבישה לפני השחזה, או במכבשים מונעים ידנית או מכנית, או במכבשים הידראוליים או פנאומטיים קטנים. בקרה על כל הממדים בתהליך הייצור מתבצעת בעזרת מדי גבול קשיחים ותבניות. למעט בדיקות יציאה ופעולות חבישה, כמעט אף פעם לא נעשה שימוש בהתקני חיווי.
החסרונות של הטכנולוגיה המתוארת מצטמצמים בעיקר להלן:
1) הציוד ושיטות הייצור בהם נעשה שימוש הינם בעלי פרודוקטיביות נמוכה ופיגרו מאחורי השיטות המודרניות של ייצור המוני;
2) ברוב המקרים, פלדה בצורת מוטות שחורים לא מכוילים משמשת כחומר המוצא, מה שמוביל לצורך בעיבוד גם את החלק האמצעי של הפיר, אשר הקוטר הגדול ביותר. נסיבות אלו לבדן, המגדילות את מורכבות העיבוד, מובילות להפסדים מהותיים, לפחות 15-20%;
3) הפעולות של חיתוך חומר העבודה, הפיכת הקצוות וקידוח המרכזים מתבצעות על ציוד קונבנציונלי המיועד לעבוד בייצור המוני ולכן יש להם פרודוקטיביות נמוכה, עם חלק גדול יחסית של זמן עזר ידני. כך, למשל, קידוח מרכזי מבוצע לרוב על אנכי מכונות קידוחבשני מעברים, כלומר כל צד של הפיר באופן עצמאי, סיבוב הפיר;
4) פעולות פנייה מבוצעות גם על ציוד אוניברסלי לא פרודוקטיבי מספיק. חיסרון מיוחד של מכונות החיתוך הרבות בשימוש הוא יכולת הסתגלותן הנמוכה לשינוי מהיר של הגדרה מגודל פיר אחד למשנהו, מה שמוביל לאובדן זמן גדול במהלך ההחלפות. יש להקדיש תשומת לב מיוחדת לשיטה המשמשת לייצור גלי. בְּ דרך קיימתכאשר מתגלגלים על מחרטות של פירים מסובבים מראש, אי אפשר לשמור על מידות הקטרים בצורה מדויקת מספיק ולהימנע מתנודות בלתי מקובלות במידות וסטיות מהישר הנדרש של הגלי. האחרון נדרש עבור התאמה נכונהליבת רוטור (אבזור). לבסוף, השיטה הנהוגה של טחינה במעגלים צרים עם הזנה אורכית אינה יעילה. יצוין כי ככלל, גם כאשר הדבר אפשרי ורציונלי, כמו למשל, בשחיקת צווארים, מכונות אינן מצוידות במכשירים למדידת הממדים הנטחנים במהלך הפעולה, כלומר, בתנועה של מכונה, אבל לבדיקת המידות המכונה נעצרת.
יש לציין כי הניקוי והשטיפה של הפיר במהלך העיבוד, בפרט לפני הטחינה הסופית, ובצורה מוגמרת אינם מסופקים בטכנולוגיה הנוכחית. כך נראה תהליך ריכוז הפיר הנפוץ ביותר.
עם זאת, יש תהליך שונה לחלוטין עבור עיבוד פיר ללא מרכז., שיש לה מספר יתרונות בהשוואה לשיטת המרכז ומביאה להפחתה משמעותית במורכבות העיבוד. תהליך זה משמש בהצלחה רבה בייצור פירים בייצור ציוד חשמלי לרכב ולטרקטור.
בשיטה ללא מרכז, חומר המקור חייב להיות בהכרח פס מכויל ומיושר בקפידה. הפעולה הראשונה - הסיבוב המלא של הפיר מתבצע במכונת בר. על מנת להימנע מכיפוף הצירים הארוכים במהלך הסיבוב, האחרונים נתמכים במשענות יציבות של רולר. בפעולות עיבוד פירים עוקבות, השחזה הראשונית מתבצעת במכונות שחיקה ללא מרכז, והפעולות הראשונות מבוצעות עם הזנה דרך של מוצרים, על שתיים או שלוש מכונות רצופות.
בעתיד, גלי מתגלגל. פעולה זו בייצור ציוד חשמלי לרכב ולטרקטור בוצעה באופן שונה מאיך שהיא נעשית במפעלי הנדסת חשמל אחרים. כדי להבטיח את המידות הנכונות של הקטרים ולשמור על אותו חוזק לחיצה של פירים שונים, יש לטחון את האחרונים לפני הגלגול לאורך קוטרם, כאשר המידות נשמרו לפי דרגת הדיוק השלישית. פעולת הגלגול מתבצעת במכונת גלגול חוטים עוצמתית מסוג אופקי. בנוסף לפרודוקטיביות הגבוהה מאוד של שיטת גלגול זו, מובטחת גם ישרות מלאה של הגלי, וזה הכרחי לחלוטין בעיצובי מכונות מסוימים.
ואכן, אם ליבת הרוטור נלחצת על פיר גלי, אז היריעות הבודדות שלה בתהליך הלחיצה נוטות בהכרח לעקוב אחר הצורה והכיוון של הגלי. לכן, אם לגליות יש לפחות עקמומיות קלה מאוד והולכים בספירלה תלולה, אז כל החריצים של הליבה חייבים לחזור על העקמומיות של הגלי.
זה ידוע כי עיוותים בצורה של חריצים אינם מקובלים לחלוטין, במיוחד עם סלילה מכונה של אבזור. אתה לא צריך לחשוב שאם העוגן מכונה חשמליתחייב להיות חריצים אלכסוניים, אז הגלי עשוי להיות שיפוע מתאים. למעשה, עבור כל העיצובים של אבזור ורוטורים ללא יוצא מן הכלל, הגלי צריך להיות ישר ככל האפשר, והשיפוע הדרוש של החריצים מתקבל במהלך תהליך הלחיצה באמצעות סכיני הדרכה נטויים מתאימות במכשיר הלחיצה.
לעתים קרובות היעדר היכולת לייצר פירים עם גליות ישרות לחלוטין במפעל מאלץ אדם להשתמש בשיטות אחרות, הרבה יותר יקרות לקיבוע הליבה על הפיר, ובמיוחד להשתמש במפתחות למטרה זו.
עבור פירים גלייםאין צורך להשתמש במכונות עם קוביות שטוחות ומהלך מתקדם, אך ניתן להשתמש בהצלחה בסוגים אחרים של ציוד לגלגול חוטים. לאחר העקדה, הפירים עוברים פעולות שחיקה במטחנות חסרות מרכז, בחלקן עם הזנה אורכית, אך בעיקר עם הזנה רוחבית.
יחד עם זאת, הקוטר החיצוני של המשטח הגלי נטחן גם הוא בהכרח על מנת לשמור על הגודל בתוך דרגת הדיוק השלישית ולעמום מעט את החלק העליון של שיניים בודדות, ובכך להבטיח את אותה כמות מתח ואיכות גבוהה של חיבור הלחיצה .
עיבוד שבבי ללא מרכז דורש פחות פעולות מאשר עיבוד מרכזי, ובמיוחד, כל פעולות הרכש מבוטלות - חיתוך חומר העבודה, הפיכת קצותיו ומרכזו. לציוד המשמש במקרה זה יש גם פרודוקטיביות גבוהה יותר. מכונת סיבוב מוטים לסיבוב גלים דורשת פחות תחזוקה מהעובד מאשר מחרטה רב חיתוך. איכות הפירים המתקבלים בשתי השיטות זהה בערך. עם עיבוד ללא מרכז של פירים בעלי מספר מדפים לאורכם, ניתן לשמור על ערכי הפעימות שלהם בתוך הטלרנסים הנדרשים.
אולי יעניין אותך גם ב:
הפרעת אישיות מעורבת: גורמים, תסמינים, סוגים וטיפולים
הגדרות בקרה של GTA 4
שאלות נפוצות על הברחה ב-GTA Online
LSPDFR - ברוכים הבאים למשטרה
המפה הענקית של Grand Theft Auto San Andreas והסודות שלה