Полнотекстовый поиск:
Главная > Реферат >Промышленность, производство
Реферат
Курсовой проект выполнен в соответствии с заданием и содержит 4 листа формата А1 (чертеж детали, чертеж заготовки, чертеж приспособления (технологическая оснастка), технологические наладки) и расчётно-пояснительную записку, состоящую из 52 листов, 4 рисунков, 6 таблиц. В работе было использовано 8 источников.
Тема курсового проекта: “Разработка технологического процесса изготовления детали “Вал ступенчатый”.
В процессе работы был спроектирован маршрутно-операционный технологический процесс, оформленный в соответствии с ЕСТД.
Введение 5
1 Проектирование процесса механической обработки детали 6
1.1 Служебное назначение детали и технические требования на неё 6
1.2 Технологический контроль чертежа и анализ технологичности
конструкции 7
1.3 Определение типа производства 9
1.4 Обоснование выбора и определение
размеров исходной
заготовки 14
1.5 Проектирование маршрутной технологии обработки детали 17
1.6 Расчет припусков на механическую обработку 19
1.7 Проектирование операционной технологии 23
1.7.1 Расчет режимов резания и норм времени 23
1.7.1.1 Проектирование операции №010 «Токарная с ЧПУ» 23
1.7.1.2 Проектирование операции №020 «Фрезерная» 30
1.7.1.3 Проектирование операции №025 «Болтонарезная» 37
1.7.2 Расчет точности механической обработки 44
1.7.3 Выбор оборудования 46
2 Конструирование средств технологического оснащения 48
2.1 Выбор и обоснования установки детали в приспособлении 48
2.2 Техническое описание конструкции и
принципа работы
приспособления 48
2.3 Разработка расчетной схемы
закрепления и расчёт механизма
зажима 48
Список использованной литературы 51
Приложение 52
Введение
Валы весьма различны по служебному назначению, конструктивной форме, размерам и материалу. Несмотря на это, технологу при разработке технологического процесса изготовления валов приходится решать многие однотипные задачи, поэтому целесообразно пользоваться типовыми процессами, которые созданы на основе проведенной классификации.
В общем машиностроении встречаются валы бесступенчатые и ступенчатые, цельные и пустотелые, гладкие и шлицевые, валы-шестерни, а также комбинированные валы в разнообразном сочетании из приведенных выше групп. По форме геометрической оси валы могут быть прямыми, коленчатыми, кривошипными и эксцентриковыми (кулачковыми).
Наибольшее распространение в машиностроении, в том числе и станкостроении, получили различные ступенчатые валы средних размеров, среди которых преобладают гладкие валы. По данным ЭНИМСа, свыше 85% от общего количества типоразмеров ступенчатых валов в машиностроении составляют валы длиной 150-1000 мм.
Шейки валов могут иметь шпоночные пазы, шлицы или резьбу. Резьбы для закрепления сопряженных деталей от осевого перемещения часто выгодно заменять канавками для пружинных колец. Это упрощает обработку и сборку. В местах перехода ступеней делают канавки или галтели. Обработка галтели более сложна; поэтому предпочтительно, где это допустимо, предусматривать канавки. Торцы вала имеют фаски. Шлицевые валы могут быть со сквозными и закрытыми шлицами, последние составляют около 65% от общего количества типоразмеров. По конструкции шлицы могут быть прямобочными и эвольвентными. В настоящее время преобладают прямобочные (приблизительно 85-90% от общего количество применяемых в машиностроении типоразмеров шлицевых валов), хотя в отношении технологии эвольвентные шлицы имеют ряд преимуществ.
Валы с отношением длины к диаметру менее 15 относят к жестким; при отношении более 15 валы считают нежесткими.
1. Проектирование процесса механической обработки детали
1.1 Служебное назначение и технические требования на деталь по чертежу и условиям эксплуатации
Деталь – ступенчатый вал. В качестве материала применяется сталь 30Х13 ГОСТ 5632-72. Метод формообразования – поковка. После окончательной обработки вал отправляется на сборку.
Вал имеет пять шеек, выполняемых по 6 квалитету точности с шероховатостью по параметру Ra 1,25 (38js6; 40js6; 45js6; 32,2n6; 32n6). На две из этих шеек устанавливаются зубчатые колёса по средствам шпоночного соединения. Крайние шейки вала имеют резьбу М24×1,5-6g для закрепления зубчатых колёс от осевого перемещения гайками.
Поверхности 40js6; 45js6 и 32,2n6 мм имеют повышенную твердость 37…43 HRC Э. , получаемую в результате термообработки. Для того, чтобы остальные поверхности не подвергались термообработке (25..30 HRC Э), она производится в индукционной установке (ТВЧ).
Вал изготовляется из высоколегированной коррозионностойкой хромистой стали. Это обусловлено рабочей средой изделия.
1.2 Анализ технологичности конструкции детали
На чертеже детали имеются все необходимые размеры, даны сведения о шероховатости обрабатываемой поверхности и точности их изготовления.
Чертёж детали содержит необходимые виды, дающие полное представление о детали. По своей конструкции деталь имеет большинство поверхностей открытых и доступных для обработки.
Качественную оценку поверхностей производим по коэффициентам:
1) точности К тч
А ср – средний квалитет точности
А – соответствующий квалитет точности
N i – число поверхностей данного квалитета точности
А 1 = 6 n 1 = 7
А 2 = 7 n 2 = 1
А 3 = 8 n 3 = 2
А 4 = 12 n 4 = 4
А 5 = 14 n 5 = 18
2) шероховатости К ш
где
Б ср – среднее числовое значение параметра шероховатости
;
где Б – числовое значение параметров шероховатости на
n i ш – число поверхностей составляющих шероховатость
Б 1 =1,25 n 1 =6
Б 2 =6,3 n 2 =26
3) использования материала
m g =5,6 кг – масса детали
m з – масса заготовки =7,84 кг
m отх –
масса отходов
Таким образом, по всем показателям в соответствии с ГОСТ 14205-83 деталь является технологичной.
1.3 Определение типа производства
Тип производства по ГОСТ 3.1108-74 характеризуется коэффициентом закрепления операций Кз.о., который показывает отношение всех различных технологических операций, выполняемых или подлежащих выполнению подразделением в течение определенного времени, к числу рабочих мест.
Кз.о.=Оi/Ря
где ОI - суммарное число различных операций;
Ря - явочное число рабочих подразделения, выполняющих различные операций.
По ГОСТ 14004-85 предусматриваются следующие типы производства:
Единичное;
Серийное;
Массовое.
В свою очередь серийное производство подразделяется на крупносерийное, среднесерийное, мелкосерийное.
Расчет ведется с учетом основных операций механической обработки и типов металлообрабатывающего оборудования.
Исходные данные:
Годовая программа выпуска изделий:
N=10000
шт.
Количество деталей в изделии: m=1.
Режим работы предприятия: 2 смены в сутки.
Ориентировочный тип производства – среднесерийное.
Для расчета коэффициента закрепления операций определим предварительный маршрут обработки детали. Здесь, основываясь на типовом технологическом процессе обработки детали, выберем основные формообразующие операции механической обработки:
Фрезерно-центровальная. Фрезерование торцов заготовки и их зацентровка.
Токарная с ЧПУ. Черновое и чистовое точение наружных поверхностей.
Фрезерная. Фрезерование шпоночных пазов.
Болторезная. Нарезание резьбы М24×1,5-6g – два места.
Круглошлифовальная. Шлифование наружных поверхностей.
При расчете используется формула
Т ш-к = к Т о
1) Фрезеровать торцы.
Зацентровать торцы
2) Обточить шейки вала (черновое и чистовое точение)
3) Фрезеровать шпоночные пазы:
Пальцевой (шпоночной) фрезой
где i – количество рабочих ходов
Дисковой фрезой
4) Нарезать резьбу:
5)Шлифовальная:
Определяем нормативный коэффициент загрузки рабочего места.
Расчетное число станков:
где
n н – нормативный коэффициент загрузки оборудования (для серийного производства принимаем n н =0,75).
N – программа выпуска N=10000 шт.
F g - 4015 час – действительный годовой фонд времени работы оборудования
m пр =1
m пр =1
m пр =1
m пр =1
Коэффициент загрузки оборудования:
Число операций выполняемых на одном месте:
Количество оборудования – 5
Коэффициент закрепления операции:
10Определим количество изделий в партии для одновременного запуска в производство:
n = Na /254
где а – периодичность запуска в днях (принимаем а = 6)
n =10000*6/254=237 шт
Определение числа смен на обработку всей партии:
i – количество операций
ΣТ ш-к =27,25 мин
с==3,39
принимаем с=4
Определяем число изделий в партии, необходимое для загрузки оборудования в течение целого числа смен:
=279,48
шт. принимаем n пр =280
шт
1.4 Обоснование выбора и определение размеров исходной заготовки
Валы с небольшим числом ступеней и незначительными перепадами диаметров изготовляют из штучных заготовок, отрезанных от горячекатаного или холоднотянутого прутка, а имеющие более сложную конфигурацию и с большим числом ступеней или со ступенями, значительно отличающимися по диаметрам - из заготовок, получаемых штамповкой, поперечным прокатом или ротационным обжатием. Выбор заготовки должен быть обоснован технико-экономическими расчетами.
В массовом и крупносерийном производстве валы изготовляют из штучных заготовок, обеспечивающих эффективное использование металла (коэффициент использования металла КИМ = 0,65…0,7) и значительное сокращение трудоемкости механической обработки. Штучную заготовку из прутка заменяют штамповкой, если КИМ повышается не менее чем на 5%. Заготовка, полученная радиальным обжатием, наиболее близка по конфигурации и размерам к готовой детали, при этом КИМ = 0,85…0,95.
Заготовку, получаем на горячештамповочном прессе в закрытом штампе.
Расчет размеров заготовки проводим по ГОСТ 7505-89 «Поковки стальные штампованные».
1.4.1. Исходные данные.
Оборудование – горячештамповочный пресс.
Материал заготовки – сталь 30Х13.
Масса детали – 5,6 кг.
1.4.2. Определение технических характеристик поковки.
1)
Найдем расчетную массу поковки
=
,
где
- масса детали,
- расчетный коэффициент, определяемый
по ГОСТ 7505-89.
=1,4
(т.к. деталь имеет прямую ось).
Получаем
=
кг.
2) Класс точности – Т2.
3) Группа стали – М3.
4)
Степень сложности поковки определяется
в зависимости от соотношения
,
где
- масса фигуры в которую вписана поковка.
Имеем
=
,
откуда степень сложности поковки – С1.
5) Конфигурация поверхности разъема штампа – П (плоская).
6) Исходный индекс – 10.
1.4.3. Определение припусков и кузнечных напусков.
1) Основные припуски на размеры, мм:
1,5 – диаметр 40 мм, чистота поверхности Ra=1,25 мкм
1,2 – диаметр 42 мм, чистота поверхности Ra=6,3 мкм
1,6 – диаметр 46 мм, чистота поверхности Ra=1,25 мкм
1,2 – диаметр 53 мм, чистота поверхности Ra=6,3 мкм
1,4 – диаметр 39,5 мм, чистота поверхности Ra=6,3 мкм
1,5 – диаметр 32,2 мм, чистота поверхности Ra=1,25 мкм
1,4 – диаметр 24 мм, чистота поверхности Ra=6,3 мкм
1,1 – толщина 5 мм, шероховатость Ra=6,3 мкм
1,2 – толщина 62 мм, шероховатость Ra=6,3 мкм
1,2 – толщина 54 мм, шероховатость Ra=6,3 мкм
1,7 – длина 597 мм, шероховатость Ra=6,3 мкм.
2) Смещение по поверхности разъема штампов – 0,3 мм.
Отклонение от плоскостности и прямолинейности – 0,5 мм
Штамповочный уклон - 5
1.4.4. Размеры поковки и их допускаемые отклонения.
1) Размеры поковки, мм:
Диаметр 24+(1,4+0,3+0,5)×2=28,4, принимаем 28,5 мм
Диаметр Ç40+(1,5+0,3+0,5)×2=44,6, принимаем 45 мм
Диаметр Ç42+(1,2+0,3+0,5)×2=46, принимаем46 мм
Диаметр Ç46+(1,6+0,3+0,5)×2=50,8, принимаем51 мм
Диаметр Ç53+(1,2+0,3+0,5)×2=57, принимаем57 мм
Диаметр Ç39,5+(1,4+0,3+0,5)×2=43,9, принимаем44 мм
Диаметр Ç32,2+(1,5+0,3+0,5)×2=36,8, принимаем37 мм
Толщина 5+(1,1+0,3+0,5)×2=8,8, принимаем 9 мм
Толщина 62+1,2+0,3+0,5=64, принимаем 64 мм
Толщина 54+1,2+0,3+0,5=56, принимаем 56 мм
Длина 597+(1,7+0,3+0,5)×2=602, принимаем 602 мм
2) Радиус закругления наружных углов – 2,5 мм.
3) Допускаемые отклонения размеров, мм:
Диаметр Ç28,5
диаметр Ç57
Диаметр Ç45 диаметр Ç44
Диаметр Ç46 диаметр Ç37
Диаметр Ç51 толщина 9
Толщина 56 толщина 64
Длина 602.
Чертёж заготовки представлен на листе
формата А2
ПензГУ 1.3-09.151001.123.002-ЧЗ
1.5 Проектирование маршрутной технологии обработки детали
Таблица 1.
№ опер |
Наименование и краткое содержание |
Технологические базы |
Оборудование |
Фрезерно-центровальная Фрезеровать торцы Зацентровать с 2 х сторон |
Необработанные поверхности шеек и торец 20 |
||
Токарная с ЧПУ Точить вал слева предварительно Точить вал справа предварительно Точить вал слева окончательно Точить вал справа окончательно |
Ось и торец 1 (Ось и торец 30) |
||
Слесарная |
Верстак слесарный |
||
Фрезерная Фрезеровать шпоночный паз шпоночной(пальцевой) фрезой Фрезеровать шпоночный паз дисковой фрезой |
Поверхность шейки Ç40js6 и торец 30; Поверхность шейки Ç32,2n6 и торец 1; |
||
Резьбонарезная Нарезать резьбу М24×1,5-6g – два места |
Поверхности шеек 32,2n6; 38js6 |
||
Слесарная Зачистить заусенцы |
Верстак слесарный |
||
Моечная |
|||
Контроль |
Плита контрольная |
||
Термическая |
Установка индукционная |
||
Круглошлифовальная Шлифовать шейки вала Ç38 мм; Ç40мм; Ç45 мм; Ç46мм; Ç32,2 мм; Ç32 мм |
Ось и торец 1 |
||
Слесарная Зачистить заусенцы, острые кромки притупить |
Верстак слесарный |
||
Моечная |
|||
Контроль |
Плита контрольная |
||
Консервация |
Верстак слесарный |
Окончательный вариант маршрутной технологии оформляем на маршрутных картах, которые приведены в приложении, согласно ГОСТу 3.1118-82.
1.6 Определение припусков расчетно-аналитическим методом
На одну поверхность припуск определяем расчетно-аналитическим методом, на остальные по ГОСТ 7505-89.
Рассчитываем припуск на размер 40 js6 (±0,008) мм
План обработки:
Черновое точение
Чистовое точение
Шлифование
Обтачивание и шлифование производится в центрах, следовательно отклонения расположения поверхностей равно:
Допуск на поверхность, используемые в качестве базовых на фрезерно-центровальной операции определяем по ГОСТ 7505-89:
Остаточная величина пространственных отклонений:
После черновой обработки
После чистовой обработки
Расчет минимальных значений припусков производим по формуле:
Минимальный припуск:
Под предварительное обтачивание:
Под окончательное обтачивание:
Под шлифование:
Полученные данные заносим в таблицу 2 .
Технологические переходы обработки поверхности |
Элементы припуска, мкм |
Расчет-ный припуск |
Расчет-ный размер dp , мм |
Предельный размер, мм |
Предельные значения припусков, мкм |
|||||
2 Zmax |
||||||||||
Заготовка |
||||||||||
Обтачивание предварительное |
||||||||||
Обтачивание окончательное |
||||||||||
Шлифование |
Графа «Расчетный размер » (d р) дополняем, начиная с полного размера:
Наименьший предельный размер определим округлив до того же знака что и у десятичной дроби, которой задан допуск. Наибольший предельный размер найдем прибавлением допуска к наименьшему.
Рассчитываем значение припусков:
Общие
припуски
и
определяем,
суммируя промежуточные припуски:
212+336+2960=3508 мкм
258+434+4400=5092 мкм
Произведем проверку правильности выполненных расчетов:
Проверка верна, следовательно, расчет произведен, верно.
Рис.1. Схема расположения припусков и допусков на размер 40 js6 мм.
1.7 Проектирование операционной технологии
1.7.1 Расчет режимов резания и норм времени
1.7.1.1 Проектирование операции №010 «Токарная с ЧПУ»
Операция выполняется на токарно-винторезном станке с ЧПУ мод. 16К20Ф3 за четыре установа(А и Б – черновая обработка, В и Г – чистовая обработка), на каждом из которых выполняется по одному переходу. На данной операции для установки и базирования заготовки на станке используются 2 х кулачковый поводковый патрон с плавающим передним центром и вращающийся центр, установленный в задней бабке.
В качестве режущих инструментов используются токарные резцы для наружной обработки стандарта ISO производства компании ISCAR:
Черновое точение:
Державка: PCLNR 2020К-12
Пластина: CNMG 120408T-NR
радиус при вершине r=0,8 мм
сплав пластины IC 9025
V=150..250 м/мин
S=0,15..0,5 мм/об
Чистовое точение:
Державка: SVJCR 2020К-16
Пластина: VCMT 160404E-14
радиус при вершине r=0,4 мм
сплав пластины IC 9025
твёрдый сплав, покрытый методом химического осаждения тремя слоями покрытия из TiN, AL 2 O 3 , TiCN.
V=250..400 м/мин
S=0,12..0,25 мм/об
Все расчеты по данной операции ведутся согласно формулам
Скорость резания при наружном продольном и поперечном точении рассчитываем по формуле
Кv на скорость резания представляет собой произведение из отдельных коэффициентов
К mv
Knv – влияние состояния поверхности заготовки (для проката = 0,8 ;после черновой обработки = 1,0) табл.5,
Kuv – влияние материала режущей части(= 1,9) табл.6
K f – влияние главного угла в плане резца (для f95Å=0,7; для f93Å=0,7)табл.18
Черновое точение (установы А и Б):
Глубина резания t = 4 мм
Подача S=0,5 мм/об
С V = 350 табл.17
m = 0,2
= 0,15
= 0,35
Выбираем ближайшее значение по паспорту станка 800 об/мин
Определяем силу резанья:
P z =10 C p t x s y v n K p
Общий поправочный коэффициент Кр K p = K mp K p K p K p K rp
K mp =0,75 таб.9
K j p =0,89 таб.23
K g p =1,1
K l p =1,0
K rp
K p = 0,75*0,89*1,1*1=0,734
С p = 204 табл.22
n = 0
P z =10*204*4 1 *0,5 0,75 *135,7 0 *0,734=3561 Н
Рассчитываем мощность резанья
То=.
Lрх :
L рх= L рез+ y + L доп
где L рез –
L доп –
y –
Для установа А:
L рез= 430 мм
L доп+ y = 14 мм
L рх= 444 мм
То=
1,11
мин
Для установа Б:
L рез= 187 мм
L доп+ y = 14 мм
L рх= 201 мм
То=
0,503
мин
Чистовое точение (установы В и Г):
Глубина резания t = 0,4 мм
Подача S=0,25 мм/об
Период стойкости инструмента Т = 60 мин
С V = 420 табл.17
m = 0,2
Выбираем ближайшее значение по паспорту станка 2000 об/мин
Действительная скорость резания
Определяем силу резанья:
P z =10 C p t x s y v n K p
Общий поправочный коэффициент Кр на силу резания представляет собой произведение из отдельных коэффициентов K p = K mp K p K p K p K rp
K mp =0,75 таб.9
K j p =0,89 таб.23
K g p =1,1
K l p =1,0
K rp – учитывается только для быстрорежущей стали.
K p = 0,75*0,89*1,1*1=0,734
С p = 204 табл.22
n = 0
P z =10*204*0,4 1 *0,25 0,75 *333,01 0 *0,734=211,76 Н
Рассчитываем мощность резанья
кВт
кВт
Определим основное машинное время обработки:
То= .
Определим длину рабочего хода Lрх :
L рх= L рез+ y + L доп
где L рез – длина резания, равная длине обработки.
L доп – дополнительная длинна хода, вызванная в ряде случаев особенностями наладки и конфигурации детали.
y – длина подвода, врезания и перебега инструментов
Для установа В:
L рез= 432 мм
L доп+ y = 6 мм
L рх= 438 мм
То=
0,876
мин
Для установа Г:
L рез= 196 мм
L доп+ y = 6 мм
L рх= 202 мм
То=
0,404
мин
Определение штучно-калькуляционного времени на операцию.
Технические нормы времени в условиях массового и серийного производства устанавливаются расчетно-аналитическим методом. В серийном производстве определяется норма штучно-калькуляционного времени:
Тш-к=+Тшт
,
где Тпз – подготовительно – заключительное время на операцию.
n – величина партии запуска деталей; n = 280 шт
Норма штучного времени при обработке на токарных станках с ЧПУ определяется как:
Т шт =Т о +Т в +Т обсл +Т пер
T о – основное технологическое время
Тобсл – время технического и эксплуатационного обслуживания.
Тпер – время перерывов.
Тв – вспомогательное время:
Т в =Т ус +Т м.в + Т зо + Т из
Тм.в. – машинно-вспомогательное время необходимое для перемещения револьверной головки станка в зоне обработки, включая холостые отводы и подводы, а также смену инструмента.
Тзо – время на закрепление и открепление детали,
Тус – ,
Тиз – время на измерение детали,
Т м.в. =Т хх +Т ск +Т си
Тхх – суммарное время холостых ходов
Тск – суммарное время смены кадров управляющей программы (в среднем время смены одного кадра 1,5-2 сек).
Тси – Суммарное время необходимое для смены инструмента.
Т шт =Т о +Т ус + Т из + Т зо +Т хх +Т ск +Т си +Т обсл +Т пер
Общая длина холостого хода –1862 мм
Скорость быстрых перемещений – 2000 мм/мин
Тхх =1862/2000= 0,931 мин
Тси= 0,17 мин
Тск =1,5 мин
Тм.в. =0,931+1,5+0,17=2,601 мин
2,893+0,4+2,601=5,894
мин
Тобсл+ Тпер =12% от оперативного времени
Тобсл+ Тпер =5,894*0,12=0,707
Полученные значения норм времени сведем в таблицу 3.
Таблица 3.
Установ А |
Установ Б |
Установ В |
Установ Г |
||
Т ус , мин |
|||||
Т зо , мин |
|||||
Т из , мин |
|||||
Т обсл +Т пер , мин |
|||||
Т пз , мин |
|||||
Т о , мин |
На основании таблицы получаем:
Т шт =2,893+0,74+ 2,64 + 0,176 +2,601+2,828=11,878 мин.
Тш-к=+11,878=11,942
мин
.
1.7.1.2 Проектирование операции №020 «Фрезерная»
Операция выполняется на шпоночно-фрезерном станоке 6Д91 за два установа. Для данной операции необходимо применение специального приспособления, посредством которого деталь устанавливается и базируется на станке по наружной цилиндрической поверхности и торцу (сборочный чертёж приспособления представлен на листе формата А1 ПензГУ 1.3-09.151001.123.005-СБ).
В качестве режущих инструментов
используются специальные фрезы:
для
установа А – шпоночная фреза 12мм,
материал фрезы – быстрорежущая сталь
Р6М5
для установа Б – грибковая фреза
48 мм и b=8
Н8 мм, материал фрезы – быстрорежущая
сталь Р6М5
Все расчеты по данной операции ведутся согласно формулам .
Установ А:
Деталь устанавливается на приспособление и базируется по 40,2 (чертежный 40js6).
На
данном переходе производится фрезерование
паза под призматическую шпонку размерами
В
=12,
t
=
4,5Н12. Обработка
ведётся «маятниковым» методом за два
прохода с подачей на глубину 2,2 мм
Глубина фрезерования t=2,2 мм
Ширина фрезерования В=12 мм
Диаметр фрезы D=12 мм
Подача на один зуб фрезы Sz = 0,18 мм/зуб
Число зубьев фрезы z=2
Определим длину рабочего хода Lрх :
L рх= L рез+ y + L доп
где L рез – длина резания, равная длине обработки. L рез= 54 мм
L доп – дополнительная длинна хода, вызванная в ряде случаев особенностями наладки и конфигурации детали.
y – длина подвода, врезания и перебега инструментов
L доп+ y =6 мм
L рх = 54+6=60мм
Определим скорость резания V
n
,
мин,
Общий поправочный коэффициент Кv
на скорость резания представляет собой
произведение из отдельных коэффициентов
К mv – влияние качества обрабатываемого материала (для стали = 0,9) табл.3,
Knv
Kuv –
Т – стойкость инструмента; Т= 80мин таб40;
С V = 12 табл.39
m = 0,26
q = 0,3
u = 0
p = 0
Число оборотов шпинделя:
n = 250 мин
Уточняем скорость резания:
Определим минутную подачу S м, мм/мин:
S м= Sz * z * n = 0,18*2*250=90 мм/мин
Определяем силу резанья:
P z =10
поправочный коэффициент K mp на силу резания
K mp =0,3 таб.9
С p = 82 табл.41
u = 1
q = 0,86
P
z
=10
Н
Рассчитываем мощность резанья
кВт
кВт
Определим основное машинное время обработки:
То=
мин
Установ Б:
Деталь устанавливается на приспособление и базируется по Ç32,4 (чертежный Ç32,2n6).
На данном переходе производится фрезерование паза под шпонку размерами В =8 +0,022 , t = 4 Н12. Обработка ведётся грибковой фрезой Ç48 мм и b=8 Н8 мм, материал фрезы – быстрорежущая сталь Р6М5
Глубина фрезерования t=4 мм
Ширина фрезерования В=8 мм
Диаметр фрезы D=48 мм
Подача на один зуб фрезы Sz = 0,01 мм/зуб
Число зубьев фрезы z=12
Определим длину рабочего хода Lрх :
L рх= L рез+ y + L доп
где L рез – длина резания, равная длине обработки. L рез= 54 мм
L доп – дополнительная длинна хода, вызванная в ряде случаев особенностями наладки и конфигурации детали.
y – длина подвода, врезания и перебега инструментов
L доп+ y =6 мм
L рх = 54+6=60мм
Определим скорость резания V , м/мин, число оборотов шпинделя n , мин,
Общий поправочный коэффициент Кv на скорость резания представляет собой произведение из отдельных коэффициентов
К mv – влияние качества обрабатываемого материала (для стали = 0,9) табл.3,
Knv – влияние состояния поверхности заготовки (после обработки = 1,0) табл.5,
Kuv – влияние материала режущей части (= 1,0) табл.6
Т – стойкость инструмента; Т= 60мин таб40;
С V = 72 табл.39
m = 0,15
q = 0,2
u = 0,1
p = 0,1
Число оборотов шпинделя:
По паспорту станка принимаем число оборотов n = 1000 мин
Уточняем скорость резания:
Определим минутную подачу S м, мм/мин:
S м= Sz * z * n = 0,01*12*1000=120 мм/мин
Определяем силу резанья:
P z =10
поправочный коэффициент K mp на силу резания
K mp =0,3 таб.9
С p = 68,2 табл.41
u = 1
q = 0,86
w = 0
P
z
=10
Н
Рассчитываем мощность резанья
кВт
кВт
Определим основное машинное время обработки:
То=
мин
Тш-к=+Тшт ,
где Тпз –
n – n = 280 шт
Тшт=То+Тв· k +Тоб.от ,
где То – основное время,
Тв – вспомогательное время:
Тв=Тус+Тзо+Туп+Тиз ,
где Тус – время на установку и снятие детали,
Тзо –
Туп –
Тиз – время на измерение детали,
Тоб.от –
k k =1,85).
Тоб.от= Т оп ·9 %
Т оп =Т о +Т в · k
Т оп =2,833+(0,094+0,068+0,12+0,62)1,85=4,502 мин
Тоб.от=4,502 ·0,09=0,405 мин
Полученные значения норм времени сведем в таблицу 4.
Таблица 4.
Наименование |
Переход 1 |
Переход 2 |
|
Тус – |
|||
Тзо – |
|||
Туп – |
|||
Тиз – |
|||
Тоб.от – |
|||
Тпз – |
|||
То – основное время, мин |
|||
Тш-к=
+4,502+0,405
= 5,004 мин
.
1.7.1.3 Проектирование операции №025 «Резьбонарезная»
Операция выполняется резьбонарезном полуавтомате 5Д07 за два установа. Для данной операции необходимо применение приспособления – тиски с самоцентрирующими губками, посредством которого деталь устанавливается и базируется на станке по наружной цилиндрической поверхности. Возможно применение специального приспособления аналогичного приспособлению, используемому на фрезерной операции.
В качестве режущего инструмента
используется головка винторезная
самооткрывающаяся – 4КА-70 по ГОСТ 21760 –
76 с круглой гребёнкой по
ГОСТ 21761 -76
изготовленной из быстрорежущей стали
Р6М5 с износостойким покрытием нитрида
титана (TiN)
Все расчеты
по данной операции ведутся согласно
формулам .
1) Установ А:
Деталь устанавливается на приспособление и базируется по поверхности шейкиÇ38js6.
На данном переходе производится нарезание резьбы М24×1,5-6g .
Подача (равна шагу резьбы) S = 1,5 мм/об
Диаметр резьбы D=24 мм
Глубина резанья t=1,3 мм
Lрх :
L рх= L рез+ y + L доп
где L рез – длина резания, равная длине обработки. L рез= 31 мм
L доп – дополнительная длинна хода, вызванная в ряде случаев особенностями наладки и конфигурации детали.
Y – длина подвода, врезания и перебега инструментов
L доп+ y =3 мм
L рх = 31+3=34мм
Определим скорость резания V , м/мин, число оборотов шпинделя n , мин,
К mv
K Т v
Kuv –
Т – стойкость инструмента; Т= 120мин таб49;
С V = 7,4 табл.49
m = 0,5
q = 1,2
Число оборотов шпинделя:
По паспорту станка принимаем число оборотов n = 160 мин
Уточняем скорость резания:
Определяем крутящий момент:
M KP =10 C M D q S y K mp
поправочный коэффициент K mp на силу резания
K mp =0,85 таб.50
С M = 0,046 табл.51
q = 1,1
M KP =10 ·0,046 ·24 1,1 ·1,5 1,5 ·0,85=23,69 Н ·м
Рассчитываем мощность резанья
кВт
кВт
Определим основное машинное время обработки:
То=
мин
2) Установ Б:
Деталь устанавливается на приспособление и базируется по поверхности шейки Ç32,2n6.
На данном переходе производится нарезание резьбы М24×1,5-6g
Подача (равна шагу резьбы) S = 1,5 мм/об
Диаметр резьбы D=24 мм
Глубина резанья t=1,3 мм
Определим длину рабочего хода Lрх :
L рх= L рез+ y + L доп
где L рез – длина резания, равная длине обработки. L рез= 20,4 мм
L доп – дополнительная длинна хода, вызванная в ряде случаев особенностями наладки и конфигурации детали.
y – длина подвода, врезания и перебега инструментов
L доп+ y =3 мм
L рх = 20,4+3=23,4мм
Определим скорость резания V , м/мин, число оборотов шпинделя n , мин,
Общий поправочный коэффициент Кv на скорость резания представляет собой произведение из отдельных коэффициентов
К mv – влияние качества обрабатываемого материала (для стали = 0,8) табл.50,
K Т v – учитывающий точность нарезаемой резьбы (точный = 0,8) табл.50,
Kuv – влияние материала режущей части (= 1,0) табл.50
Т – стойкость инструмента; Т= 120мин таб49;
С V = 7,4 табл.49
m = 0,5
q = 1,2
Число оборотов шпинделя:
По паспорту станка принимаем число оборотов n = 160 мин
Уточняем скорость резания:
Определяем крутящий момент:
M KP =10 C M D q S y K mp
поправочный коэффициент K mp на силу резания
K mp =0,85 таб.50
С M = 0,046 табл.51
q = 1,1
M KP =10 ·0,046 ·24 1,1 ·1,5 1,5 ·0,85=23,69 Н ·м
Рассчитываем мощность резанья
Определим основное машинное время обработки:
То=
мин
3) Определение штучно-калькуляционного времени на операцию.
Технические нормы времени в условиях массового и серийного производства устанавливаются расчетно-аналитическим методом. В серийном производстве определяется норма штучно-калькуляционного времени:
Тш-к=+Тшт ,
где Тпз – подготовительно – заключительное время на операцию.
n – величина партии запуска деталей; n = 280 шт
Тшт=То+Тв· k +Тоб.от ,
где То – основное время,
Тв – вспомогательное время:
Тв=Тус+Тзо+Туп+Тиз ,
где Тус – время на установку и снятие детали,
Тзо – время на закрепление и открепление детали,
Туп – время на приемы управления станком,
Тиз – время на измерение детали,
Тоб.от – время на обслуживание рабочего места и перерывов на отдых и личные надобности,
k – коэффициент, учитывающий серийность производства (k =1,85).
Тоб.от= Т оп ·7 %
Т оп =Т о +Т в · k
Т оп =0,24+(0,094+0,068+0,12+0,55)1,85=1,78 мин
Тоб.от=1,78 ·0,07=0,125 мин
Полученные значения норм времени сведем в таблицу 5.
Таблица 5.
Наименование |
Переход 1 |
Переход 2 |
|
Тус – время на установку и снятие детали, мин |
|||
Тзо – время на закрепление и открепление детали, мин |
|||
Туп – время на приемы управления станком, мин |
|||
Тиз – время на измерение детали, мин |
|||
Тоб.от – время на обслуживание рабочего места и перерывов на отдых и личные надобности, мин |
|||
Тпз – подготовительно – заключительное время, мин |
|||
То – основное время, мин |
|||
Время на получение и сдачу инструмента, мин |
На основании таблицы получаем:
Тш-к= +0,24+0,125 = 0,46 мин .
1.7.2 Расчет точности механической обработки
Расчет точности обработки заключается в определении суммарной погрешности чистового точения и сравнение ее с допуском на размер по 9 квалитету точности 40,266 h9 (-0,062).
Суммарная погрешность обработки рассчитывается по формуле
где - погрешности возникающие в процессе обработки;
- погрешность настройки технической
системы на размер.
1. Определим погрешность обработки
вызванную размерным износом инструмента
Используя таблицу 29 допустимого размерного износа инструмента при обработке партии заготовок определим:
20
мкм
2. Определим упругие отжатия вызванные
непостоянством силы
Т. к. обработка поверхностей происходила с закреплением в станочных кулачках, то здесь применима следующая формула
Податливость
равна
мкм/кН
Радиальное усилие
определим по формуле
где
мм;
мм
Значение скорости резания: м/мин.
По табл.22 находим: С p = 204; n = 0; X = 1,0; Y = 0,75
Значение поправочного коэффициента на силу резания
K p =0,734
Рассчитываем скорость резания и определяем радиальное усилие
Определим упругие отжатия
3. Определим погрешность настройки технической системы на размер
мкм.
4. Температурные деформации определим по формуле
,
мкм
5. Определим по формуле
,
мм,
мм;
мкм.
Суммарная погрешность обработки
Сравниваем суммарную погрешность с допуском на размер 40,266 h9, который составляет 62 мкм.
62 мкм > 55,5 мкм
Вывод: точность механической обработки соблюдается.
1.7.3 Выбор оборудования
На предприятиях стараются расписать технологический маршрут таким образом чтобы он, по возможности весь, выполнялся на оборудование одного цеха. Это связано с необходимостью оформления множества документов при перемещении части маршрутного процесса в другой цех.
Проектируемая технология удовлетворяет этому правилу. Все ее операции выполняются в пределах одного участка цеха, кроме заготовительной операции.
Выбор конкретной модели оборудования осуществляется по габаритным, точностным и мощностным критериям.
Распределение оборудования по операциям сведем в таблицу 6.
Таблица 6.
Наименование станка |
Режущий инструмент |
Приспособление и вспомогательный инструмент |
Мерительный инструмент |
|
Фрезерно-центровальный полуавтомат |
Сверло 4 Р6М5 ГОСТ
14034-74 Сверло центр. 2317-0107 (ф4,00) ГОСТ 14952-75 Фреза торцевая Ø 100 Т5К10 ГОСТ 24359-80 Фреза (ф100) 2214-0001 Т5К10 45° ГОСТ 24359-80 |
|||
Токарно-винторезный станок с ЧПУ 16К20Ф3 |
Резец проходной PCLNR 2020К-12 с пластиной: CNMG120408T-NR Резец проходной SVJCR
2020К-16 |
Патрон 2 х кулачковый |
Микрометр МК 25-1 ГОСТ 6507-78 Штангенциркуль ШЦ-I-125-0,1-1 ГОСТ 166 Образцы шероховатости ГОСТ 9378-75 |
|
Шпоночно-фрезерный станок 6Д92 |
Специальная шпоночная фреза Ç12мм Р6М5 Фреза (ф12) 2234-0367 N9 ГОСТ 9140-78 Специальная грибковая фреза Ç48 мм и b=8 Н8 Р6М5 |
Приспособление специальное |
Штангенциркуль ШЦ-I-125-0,1-1 ГОСТ 166 |
|
Резьбонарезной полуавтомат 5Д07 |
Гребенка 2671-0773 ГОСТ 21761-76 |
Головка 2681-0023 ГОСТ 21761-76. Тиски с самоцентрирую-щими губками |
Кольцо резьбовое М24×1,5. Пр и НЕ. |
|
Круглошлифовальный станок 3М151 |
Шлифовальный круг ПП300×30×24А40ПС1-С2 6К5 50 м/с 1кл.А ГОСТ 2424-83 |
Центр передний, задний ГОСТ 13214-79 Хомутик ГОСТ 16488-79 |
Скобы Пр. и НЕ. Образцы шероховатости ГОСТ 9378-75 |
Сверло 2300-6173 (ф5,00) ГОСТ 10902-77
Штангенциркуль ШЦ-I - 250-630 - 0,05-1 ГОСТ 166-89
Штангенциркуль ШЦ-I - 125 - 0,05-1 ГОСТ 166
Штангенциркуль ШЦ-I - 125 - 0,10-1 ГОСТ 166
Штатив ШМ-I-8 ГОСТ 10197-70
Индикатор ИЧ02 кл. 1 ГОСТ 577-68
Угломер тип 1-2 ГОСТ 5378-88
Микрометр МК50-1 ГОСТ 6507
Микрометр МК25-1 ГОСТ 6507-90
Скоба 061 ОСТ 95 1960-78 на рез. диаметр
Скоба СР 50 ГОСТ 11098-75
Кольцо 8211-0094 6g (M24 X1,5-ПР) ГОСТ 17763-72
Кольцо 8211-1094 6g (M24 X 1,5-НЕ) ГОСТ 17764-72
Пробка 8133-0630 (ф5) Н14 ГОСТ 14807-69
2. Конструирование средств технологического оснащения, мерительного и режущего инструмента
2.1 Выбор и обоснования установки детали в приспособлении
Из чертежа детали следует, что для операции фрезерования шпоночного паза следует применить для зажима детали на станке специальное приспособление. В нем заготовка базируется на призме и двух опорах. Так как приспособление применяется в крупносерийном производстве, то оно должно быть оснащено быстродействующим зажимным устройством. Этим требованиям удовлетворяет пневмопривод зажимного механизма.
2.2 Техническое описание конструкции и принцип работы приспособления
Приспособление состоит из корпуса, установочной призмы, рычажного зажимного устройства. В качестве привода принят поршневой пневмоцилиндр одностороннего действия при подаче сжатого воздуха в верхнюю часть пневмоцилиндра, поршень со штоком опускается и по средствам рычажной передачи прижимает прижимом деталь, т.е деталь закрепляется. При прекращении подачи сжатого воздуха в верхнюю полость, пружины, установленные на зажимном механизме, поднимают прижим, а с ним тяги и шток с поршнем поднимаются вверх и деталь высвобождается.
2.3 Разработка расчетной схемы закрепления и расчёт механизма зажима
Заготовка базируется на установочных элементах приспособления и прижимается к ним зажимом с силой Q, а сила резания Р o действует в перпендикулярном направлении. Силе резания Р o противодействует сила трения Т между опорной поверхностью приспособления и нижней базовой плоскостью детали, а также между верхней плоскостью детали и поверхностью зажима.
Рис.
4
Составим уравнение равновесия всех сил, действующих на заготовку относительно оси Y:
ΣF yi =Q – 2Rsina/2=0
Требуемая сила зажима определяем из выражения:
kР о = Qf 1 +2Rf 2
,
где
k- коэффициент запаса зажима.
k 0 =1,5 – гарантированный коэффициент запаса.
k 1 =1,0 - коэффициент, учитывающий изменение припуска
k 2 =1,4 – коэффициент, учитывающий увеличение силы резания при затуплении инструмента.
k 3 =1,2 - коэффициент, учитывающий увеличение силы резания при прерывистом резании
k 4 =1,0 - коэффициент, учитывающий постоянство сил зажима
k 5 =1,0 – коэффициент характеризующий только зажимные механизмы с ручным приводом
k 6 =1,0 - коэффициент, учитывающий наличие момента стремящегося повернуть заготовку.
a=
- угол призмы
f 1 =f 2 =0,15
Расчёт зажимного механизма:
Определяем размер привода:
Р и =0,785 D 2 p h
p=0,4 Н/м 2 =4 кгс/см 2 – удельное давление сжатого воздуха;
=0,7.
Округляем полученный диаметр до ближайшего значения.
Диаметр штока: d=0,25D=0,25*100=25 мм.
Список использованной литературы.
А. Ф. Горбацевич. Курсовое проектирование по технологии машиностроения. Мн.: «Высшая школа», 1983.
А. Г. Косилова и Р. К. Мещеряков. Справочник технолога машиностроителя. В двух томах. Том 2. М.: «Машиностроение», 1985.
«Режимы резания металлов». Справочник под редакцией Ю.В. Барановского . М. «Машиностроение», 1972.
А. Г. Косилова и Р. К. Мещеряков. Справочник технолога машиностроителя. В двух томах. Том 1. М.: «Машиностроение», 1985
А.К. Горошкин. Приспособление для металлорежущих станков. Справочник 7-е издание, переработано и дополнено. М.: Машиностроение 1979
«Обработка металлов резанием»: Справочник под редакцией А.А. Панова . - М.: Машиностроение, 1988.
Б.Л. Беспалов, Л.А. Глейзер, И.М. Колесов Технология машиностроения М., “Машиностроение”, 1973
Проектирование технологии автоматизированного машиностроения: Учеб. для машиностроит. спец. вузов/ И.М. Баранчукова, А.А. Гусев, Ю.Б. Крамаренко и др.; под ред. Ю.М. Соломенцева . – 2-е изд., испр. – М.: Высш. шк., 1999
Детали класса «валы» характеризуются тем, что в основном образованы наружными поверхностями вращения около одной оси. Длина вала значительно больше диаметра.
В отдельных конструкциях возможно наличие внутреннего центрального отверстия.
По назначению, конструкции, весу, точности обработки, материалу и другим показателям детали этого класса очень разнообразны.
В прокатном оборудовании применяют валы весом от нескольких килограммов до 20-30 т и даже больше при диаметрах до -800-1200 мм.
Класс «валы» делится на следующие основные группы: валы и оси гладкие; ступенчатые; пустотелые; с фасонной криволинейной и конусной поверхностями.
В каждой группе валы подразделяют на типы, которые различаются только по размерам обрабатываемых поверхностей.
При обработке деталей класса «валы» необходимо:
1. Выдержать прямолинейность оси. Соосность и прямолинейность всех участков валов и осей должны быть в пределах установленных допусков.
2. Выдержать концентричность поверхностей вращения относительно оси. Эллиптичность и конусность обработанных шеек должны быть в пределах допуска на диаметр.
3. Чтобы величина радиального биения посадочных шеек валов к базирующим шейкам была выдержана в пределах 0,02-0,03 мм.
4. Обработать поверхности посадочных шеек для зубчатых колес, шкивов и маховиков с чистотой 6-го класса, для подшипников качения - с чистотой 7-го класса, а бочки прокатных валков - с чистотой 7-8-го классов.
5. Подрезать торцы и уступы точно перпендикулярно оси.
6. Придать шпоночным, шлицевым и трефовым пазам правилы ный профиль и расположить их на определенном месте по поверхности вала.
7. Выдержать указанную конструктором твердость рабочих поверхностей.
Выбор заготовки для вала определяется назначением вала, маркой материала, из которого должен быть изготовлен вал, и его конструктивными особенностями.
Для большинства валов общего назначения применяется углеродистая сталь марок Ст. 5, Ст. 6, сталь 40 и 50. Особо ответственные валы изготовляют из высоколегированных сталей: хромистых, хромомолибденовых, хромокремнистых и др. Для изготовления прокатных валков в ряде случаев применяют также легированные чугуны с добавлением хрома и никеля и модифицированные чугу - ны, в которых модификатором является магний. Твердость рабочих поверхностей в зависимости от назначения валков находится в пределах от 30 до 75 единиц по Шору.
Заготовки для валов подвергаются предварительной обработке, выполняемой в следующем порядке; правка, разметка, отрезка, торцовка и центровка, контроль.
Основными операциями при обработке валов являются токар-, ные, при выполнении которых снимается основная масса материала - припуска, в результате чего валу придается необходимая форма и размеры основных поверхностей.
Черновая токарная обработка обеспечивает 4-5-й классы точности и 3-4-й классы чистоты. Обработка производится с глубиной резания 5-25 мм и более, с подачами 0,5-3 мм/об и при скоростях резания 30-40 м/мин. При черновой обработке проката хорошие результаты получаются в случае применения резцов с пластинами быстрорежущей стали. При обработке поковок на тяжелых лучшие результаты получаются при резцах с пластинами твердого сплава Т5К10 и Т15К6. Черновую обработку производят в основном по принципу силового резания. Для снижения основного времени и полного использования станка применяют следующие мероприятия:
В суппорте устанавливают два резца, каждый из них имеет различный вылет, снимает определенную часть припуска по глубине;
Применяют резцы с несколькими режущими кромками, которые " могут резать при прямом и обратном ходе суппорта;
Используют ступенчатые резцы, которые уменьшают сплошную - ширину стружки и этим самым уменьшают усилие резания; < ,
При обработке длинных и тяжелых валов применяют два и"три суппорта, используя передние и задние суппорты станка.
Черновую обработку вала производят обычно за две установки. Для обточки применяют прямые или отогнутые правые и левые проходные резцы, для подрезки торцов и уступов - подрезные и для обработки галтелей - специальные выгнутые и вогнутые гал- тельные резцы. Галтели большого радиуса (30 мм и выше) часто подрезают или комбинированием продольной и поперечной подач по шаблонам, или с помощью специального поворотного приспособления, устанавливаемого на поперечных салазках суппорта.
При обработке ступенчатых валов целесообразно в первую очередь обрабатывать более массивные, с большим диаметром ступени. Наибольшее распространение получили две схемы обработки ступенчатых валов (фиг. 45).
При небольшой разнице в диаметрах ступеней обычно применяют схему фиг. 45, а, при значительной разнице в диаметрах и валах большого диаметра - схему фиг. 45, б. Иногда применяют комбинированную обработку с использованием обеих схем. Следует выбирать тот метод, который обеспечивает наибольшую производительность и более полное использование станка.
При обточке конусных и фасонных поверхностей пользуются комбинированием продольной и поперечной подач, производя обработку по шаблонам, или применяют копировальные устройства.
Первый способ, требующий высокой квалификации исполнителя, применяют в единичном и мелкосерийном производстве.
Короткие и крутые конуса обрабатывают путем поворота верхних салазок суппорта и подачи резца под углом, равным половине угла конуса. Длинные и пологие конуса обтачивают, смешая заднюю бабку с таким расчетом, чтобы образующая конуса была параллельна оси шпинделя и продольному перемещению резца. Способ этот достаточно прост и его можно применить на любом токарном станке, но при этом наблюдается неравномерная работа и износ центров, а также разбивка центровых отверстий.
При обработке фасонных поверхностей небольшой длины применяют специальные фасонные резцы, которыми обрабатывают обычно с поперечной подачей. Профиль резца по режущей кромке соответствует обратному профилю детали. Из фасонных резцов более часто с металлургическом машиностроении применяют резьбовые, галтельные, канавочные.
При обработке пустотелого вала из цельной заготовки после разметки, фрезерования торцов и центрования производят черновую обточку наружной поверхности, устанавливая вал в центрах и патроне. Отверстие сверлят и растачивают либо на токарном станке с люнетом, либо на горизонтальном сврлильно-расточном станке. В последнее время широкое распространение получило сверление пустотелыми сверлами, когда сердцевину удаляют в виде дельного вала. Подобный способ применяют при отверстиях диаметром более 100 мм.
В зависимости от технических условий вал после черновой обработки может быть передан на чистовую или на промежуточную термическую обработку с последующей механической окончательной обработкой. Во всех этих случаях после черновой обработки должен быть оставлен припуск. Припуски под чистовое обтачивание после чернового у заготовок из проката оставляют 0,5-2 мм на сторону. Для кованых валов величину припусков принимают 2,5- 5 мм, что объясняется, с одной стороны, большими габаритными размерами валов, а с другой, - тем, что черновая обработка проводилась в более тяжелых условиях, с большими усилиями и тепловыми деформациями, вследствие чего поверхностный слой поврежден на большую глубину. Если после черновой обработки производят термическую, то припуски увеличивают примерно в 1,5-2 раза, чтобы компенсировать возможную деформацию и повреждение поверхностного слоя детали при термической обработке.
Заготовка, подготовленная к термической обработке, должна повторять все перепады диаметров между ступенями вала. Но если разница в диаметрах соседних ступеней не превышает 10 мм, то их обтачивают на один диаметр. Острых переходов и углов не должно быть. При термической обработке в виде нормализации или старения улучшают структуру и устраняют внутренние напряжения. При значительном припуске после термообработки операцию делят на два перехода: получистовой и чистовой. Последний производят при глубине резания 1-2 мм.
При чистовом проходе резцы имеют закругленную вершину с радиусом 2-3 мм или более широкую режущую кромку с Zcp = = 0°, что характерно для резцов типа Колесова, которые позволяют работать с увеличенной подачей 1-2,5 мм/об и обеспечивают при тщательной работе чистоту 6-го класса.
Если в цехе отсутствуют тяжелые шлифовальные станки, а на крупном валу необходимо выдержать отдельные ступени по 2-му классу, то их обтачивают широкими пружинными резцами с глубиной резания не более 0,1-0,3 мм. При требовании чистоты 7-го класса производят обкатку роликом, который устанавливают в специальной державке в суппорте станка. Обработка роликом обеспечивает не только высокую чистоту, но, создавая некоторый наклеп на поверхности, повышает ее плотность и износоустойчивость.
Специального припуска на обкатку роликом не оставляют. Практически припуск находится в пределах допуска 0,01-0,02 мм на -сторону.
При чистовой и отделочной обработке необходимо обратить внимание на точность установки вала и инструмента, на жесткость всей системы, на геометрию режущего инструмента и на качество базирующих поверхностей: центровые отверстия (при обработке в цент - pax) и на проточенные пояски и шейки (при обработке в люнетах). Усилия резания и температурные воздействия «а деталь должны быть минимальные. В отдельных случаях обработка валов усложняется тем, что на их поверхности могут быть расположены шпоночные пазы, шлицы или трефы.
Для обработки шпоночных паэов вал размечают, а затем передают на фрезерный станок.
У небольших и средних валов шпоночные пазы обрабатывают на вертикально-фрезерных и шпояочно-фрезерных станках концевыми или специальными шпоночными фрезами. R первом случае при изготовлении закрытых пазов необходимо производить засвер - ливание для ввода фрезы. Тяжелые валы фпезеруют по разметке иа горизонтально-расточных и продольно-фрезерных станках концевыми и торцовыми фрезами - Последние нашли широкое применение при обработке тангенциальных шпоночных пазов.
Шлицевые пазы обрабатывают методом деления или методом обкатывания. При методе деления предварительно производят разметку, а при малых и средних валах применяют и делительную головку. Йарезание по методу обкатывания производят на специальных шли - це-фрезерных станках с применением червячных шлицевых фрез.
Обработку треф на концах прокатных валков производят на расточных станках по разметке или на специальных односторонних и двухсторонних трефо-фрезерных станках. Режущим инструментом являются либо резцы, установленные на оправке или в шпинделе станка, либо специальные трефо-фрезерные головки.
Если прокатные валки для передачи вращения имеют на торцах плоские лопатки с вырезом, то при обработке этих лопаток необходимы следующие операции:
I. Разметочная - нанести осевые линии.
II. Строгальная - строгать лопатку-
ПІ. Разметочная - разметить зев.
IV. Сверлильная-обсверлить зев.
V. Слесарная - выбить обсверленную часть зева. .
VI, Расточная - на расточном - станке фрезеровать зев по внутреннему контуру.
Последнюю операцию можно выполнять также на переносном поперечно-строгальном станке. Выбор того или иного станка определяется наличием оборудования, размерами зева и экономичностью. Для примера ниже приведен технологический процесс обработки ступенчатого вала, показанного на фиг. 46. Материал вала - хромистая сталь 20ХА с пределом прочности ав = 65 кг/мм2- Заготовка - поковка, полученная методом свободной ковки. Припуски выбраны по нормативам.
Последовательность операций при обработке следующая: I. Разметочная - разметить лопатку.
II. Расточная - фрезеровать торцы, свести осевые линии, наметить центра и центровать.
6 Заказ 222
III. Токарная - обточить в размер, подрезать торцы и уступы
IV. Разметочная - разметить шпоночный паз.
V. Фрезерная - фрезеровать шпоночный паз.
Фиг. 46. Ступенчатый вал и его заготовка.
VI. Шлифовальная - шлифовать шейки.
VII. Токарная - обработать галтели и подрезать торцы и уступы в размер.
VIII. Слесарная - снять заусенцы.
Этот ТП включает следующие операции:
Обработка торцов, центрирование
Токарная обработка (точение) шеек валов
Предварительное шлифование
Фрезерование шпоночных пазов
Фрезерование шлицев
Обработка резьбы
Термообработка
Исправление центровых отверстий
Чистовое шлифование шеек вала
Шлифование шлицев
Калибрование резьбы и зачистка заусенцев
Промывка
Контроль
1.2.1. Обработка торцов вала и центрирование
В единичном и мелкосерийном производствах торцы обрабатывают на токарных и фрезерных станках. Центрирование выполняется на сверлильных, токарных, револьверных и горизонтально-расточных станках.Центрирование может производиться или двумя инструментами (спиральным сверлом и зенкером), или же одним комбинированным центровочным сверлом. Угол конуса сверла обычно равен 60 0 , однако, для тяжелых заготовок валов его увеличивают до 75 0 или 90 0 .
В ряде случаев у режущих инструментов выполняют дополнительную фаску с углом 120 0 , которая предохраняет центровое отверстие от забоин при случайном повреждении торцов вала.
В серийном и массовом производствах применяют фрезерно-центровальные полуавтоматы, на которых одновременно фрезеруются 2 торца (позиция 2 на рис. 1.3.), затем центруются 2 отверстия (позиция 3).
Рис. 1.3. – Схема обработки вала на фрезерно-центровальном полуавтомате.
1.2.2. Обтачивание валов
Токарная обработка валов обычно включает черновые и чистовые операции. При черновом точении снимают большую часть припуска, работая с большей глубиной резания и большой скоростью движения подачи.В единичном и мелкосерийном производствах обтачивание выполняется на токарных универсальных станках. При обработке ступенчатых валов используются различные схемы резания, например, представленная на рис. 1.4.
В схеме на рис. 1.4., в суммарная длина перемещения резца , т.е. меньше, чем в схеме на рис. 1.4., а. Однако, число рабочих и вспомогательных ходов больше.
Рис. 1.4. – Схемы обтачивания валов
При выборе схемы резания стремятся получить максимальную производительность и минимальную себестоимость операции. При этом учитывают размеры вала, способ простановки и контроля размеров, допуски и другие факторы.
Иногда при большой разнице в диаметрах ступеней стремятся как можно дольше не ослаблять вал и ступени наименьшего диаметра обтачивать в последнюю очередь.
При обтачивании длинных не жестких валов применяют неподвижные или подвижные люнеты. Неподвижный люнет устанавливается на станине станка. Подвижный люнет движется на суппорте и его кулачки следуют за резцом (рис. 1.5., а).
Если же необходимо обеспечить соосность обработанной поверхности с поверхностью 2 (рис. 1.5., б), то кулачки люнета располагают впереди резца на поверхности.
Рис. 1.5. – Схема обтачивания вала с использованием люнета
В настоящее время в мелкосерийном производстве используются станки с ЧПУ. Они позволяют автоматизировать цикл обработки, использовать повышенные режимы резания, повысить производительность, применить многостаночное обслуживание, сократить дефицит высококвалифицированной рабочей силы, уменьшить брак, сократить сроки подготовки производства.
В крупносерийном и массовом производствах для обтачивания валов применяют многорезцовые и гидрокопировальные станки и полуавтоматы. Обычно они имеют 2 суппорта – продольный и поперечный, служащие для подрезания торцов , растачивания канавок и фасонного точения.
Суппорты могут работать одновременно. На многорезцовых станках в случае необходимости применяют обтачивание с врезанием и последующей продольной подачей (рис. 1.6., б).
Рис. 1.6. – Схема обтачивания вала на многорезцовом полуавтомате
По сравнению с универсальными токарными станками, многорезцовые станки позволяют повысить производительность за счет сокращения длины рабочего хода, одновременной работой резцов, а также за счет устранения затрат времени на смену резцов, поворот резцедержателя и холостые перемещения суппорта.
На продольном суппорте гидрокопировального станка устанавливается 1 резец, который настраивается на размер только по одной шейке вала. Получение остальных размеров обеспечивается копиром и следящей системой. Одновременно сокращается число измерений, применяется более высокий режим резания, чем при работе с ручным включением подач.
Валы обтачиваются за один или несколько рабочих ходов, при этом смена копиров производится автоматически за счет поворота барабана с копиром.
В тех случаях, когда вал может быть обработан на гидрокопировальном и одношпиндельном многорезцовом полуавтомате, выбор оборудования делается на основании технико-экономического анализа.
При этом учитываются следующие соображения:
При многорезцовом обтачивании с делением длины обработки, длина рабочего хода меньше, чем при копировальной обработки.
Время наладки и подналадки гидрокопировальных станков значительно меньше, чем для многорезцовых станков.
Количество резцов и режимы резания на многорезцовых станках часто ограничиваются податливостью заготовки и недостаточной мощностью станка. На гидрокопировальном станке можно работать с большими скоростями подачи главного движения резания.
В связи с изложенным производительность гидрокопировальных станков во многих случаях выше.
На точность многорезцовой обработки влияют погрешности относительного расположения и неодинаковый износ резцов. При обработке одной поверхности несколькими резцами на границах участков образуются уступы. На гидрокопировальных станках эти погрешности отсутствуют, поэтому удается получать более высокую точность размеров и меньшую шероховатость.
1.2.3. Отделочная обработка наружных цилиндрических поверхностей
Для отделочной обработки наружных цилиндрических поверхностей применяют тонкое точение, шлифование, полирование, притирку, суперфиниш, обтачивание роликами и т.п.1.2.2.1. Тонкое точение
Тонкое точение чаще применяется для отделочной обработки заготовок из цветных металлов и сплавов , реже для заготовок из стали и чугуна. Объясняется это трудностями шлифования цветных сплавов вследствие «засаливания» шлифовального круга.Обработка производится алмазными, композитными, металлокерамическими резцами и резцами, оснащенными твердыми сплавами, при высоких скоростях главного движения резания, малых скоростях движения подач и глубинах резания.
Тонкое точение позволяет получить 6…7 квалитет точности обработки и шероховатость поверхности мкм.
Производительность обработки выше, чем при шлифовании. В крупносерийном и массовом производствах для тонкого точения применяют специальные быстроходные станки высокой точности и виброустойчивости.
1.2.2.2. Шлифование
Оно является основным методом чистовой обработки наружных цилиндрических поверхностей. Преимуществами шлифования является возможность исправления погрешностей заготовки после термообработки. При обычном тонком шлифовании осуществляется обработка по 6-7 квалитету точности, при шероховатости поверхности 1,2…0,3 мкм.Тонкое шлифование дает 5 квалитет точности и шероховатость 0,16…0,8 мкм. Оно осуществляется малозернистым кругом при большой скорости его вращения, малой скорости вращения заготовки, малой глубине резания.
Шлифование осуществляется на кругло- и бесцентрошлифовальных станках с продольной подачей круга или по способу вращения (рис. 1.7.)
А – с продольной подачей; Б, В – по способу (методу) вращения
Рис. 1.7. – Схема шлифования на кругло-шлифовальном станке:
Шлифование по способу вращения более производительно, применяется в крупносерийном и массовом производстве при обработке цилиндрических и фасонных поверхностей.
Для одновременного шлифования нескольких шеек используются специальные станки, работающие несколькими кругами с целью сокращения вспомогательного времени при шлифовании, применяются устройства активного контроля, позволяющие измерять заготовки в процессе шлифования, а также устройства автоматической остановки станка при достижении заданного размера.
При бесцентровом шлифовании (рис. 1.8.) заготовка помещается между двумя шлифующими кругами, из которых один (большего диаметра) является шлифующим, а с другой – ведущим.
Рис. 1.8. – Схема бесцентрового шлифования
Шлифующий круг 1 вращается со скоростью 20-35 м/с, ведущий круг 2 – со скоростью 20-30 м/мин. Заготовка 3 ничем не закрепляется, но поддерживается опорой 4 со скосом, направленным в сторону ведущего круга.
Сила сцепления заготовки с ведущим кругом больше, чем со шлифующим. Это объясняется следующими причинами:
Увеличение силы резания при уменьшении скорости вращения круга
Изготовление ведущих кругов на связи, увеличивающей коэффициент трения между кругом и заготовкой.
При бесцентровом шлифовании с продольным движением подачи заготовки ось ведущего круга не параллельна оси шлифующего круга. Благодаря этому без специального механизма подачи обеспечивается перемещение заготовки со скоростью где
- скорость вращения ведущего круга.
С увеличением угла скрещивания осей кругов производительность обработки возрастает, но качество поверхности ухудшается, поэтому обычно
.
Для повышения точности обработки иногда выполняют сквозное шлифование за несколько рабочих ходов. В крупносерийном и массовом производствах обработка может выполняться последовательно на нескольких станках, соединенных в автолинию.
При бесцентровом шлифовании по способу врезания оси кругов чаще всего параллельны. Сначала ведущий круг отводится от шлифующего, и заготовка устанавливается на опору, затем ведущий круг подводится к заготовке и осуществляется поперечная подача до получения заданного размера.
По сравнению со шлифованием в центрах бесцентровое шлифование имеет следующие преимущества:
Отпадает необходимость центрирования заготовки, что особенно важно для деталей, обрабатываемых на револьверных станках и автоматах;
Значительно уменьшаются припуски на обработку, т.к., благодаря использованию в качестве технологической базы обрабатываемой поверхности, устраняется влияние на припуск погрешности зацентровки;
Отпадает необходимость использования люнетов при шлифовании длинных и тонких валов;
Бесцентрошлифовальные станки сравнительно легко автоматизируются и встраиваются в автолинию;
Обеспечивается более высокая производительность, чем при шлифовании в центрах;
Благодаря простоте управления станком, высокая точность достигается при средней квалификации шлифовщика ;
Погрешность обработки, вызываемая износом круга, в 2 раза меньше, чем при шлифовании в центрах, т.к. износ круга непосредственно отражается на величине диаметра заготовки, а не на величине радиуса.
1. Затраты времени на наладку и регулировку таких станков достаточно велики и окупаются при больших партиях заготовок. Поэтому бесцентровое шлифование чаще всего применяют в автотракторной и подшипниковой промышленности.
2. шпоночные пазы, канавки, отверстия, разрывы обрабатываемой поверхности препятствуют нормальной работе и даже делают её невозможной.
3. При бесцентровом шлифовании трудно обеспечить круглость обрабатываемой поверхности.
4. Затрудняется достижение соосности шлифуемой поверхности с другими ранее обработанными поверхностями.
1.2.3.3. Полирование и суперфиниш
Полирование мягкими кругами из войлока, фетра или лентой ведется при высоких скоростях инструмента, на поверхность которого наносится смесь мелкозернистого абразивного порошка и смазки. Полирование обеспечивает малую шероховатость поверхности (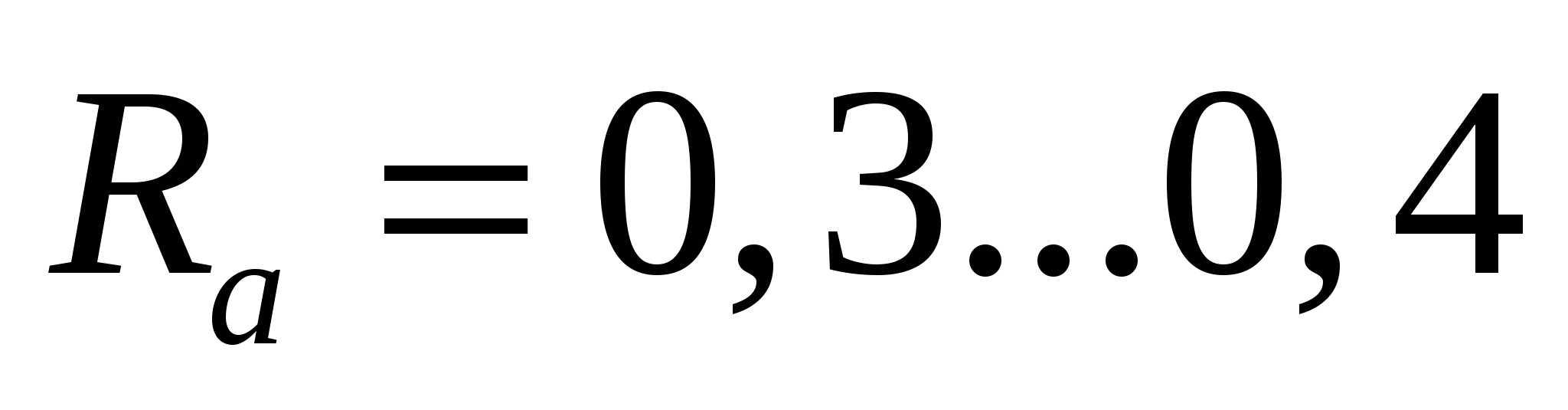
Суперфиниш (отделка колеблющимися брусками) реализует принцип неповторяющегося следа, который заключается в том, что ни одно зерно абразива не проходит дважды по одному и тому же пути. Для этого, кроме вращающейся заготовки, с небольшой скоростью (1-2,5 м/мин) и продольного перемещения брусков (рис. 1.9.) им сообщают от 200 до 1000 колебаний в минуту с малой амплитудой.
За счет колебательных движений, малой зернистости брусков и малого давления обеспечивается малая шероховатость заготовки ( мкм).
Рис. 1.9. – Схема обработки вала абразивными брусками.
Процесс ведется с применением смазочно-охлаждающей жидкости и протекает следующим образом: в начальный момент площадь контакта брусков с обрабатываемой поверхностью мала и давление бруска оказывается значительным, что вызывает интенсивный съём металла. В дальнейшем бруски прирабатываются, давление уменьшается, и процесс резания теряет свою интенсивность.
Суперфиниш не улучшает макрогеометрию заготовки, поэтому предварительная обработка должна обеспечить правильную геометрическую форму детали. Припуск под суперфиниш обычно не оставляют.
1.2.4. Обработка резьбы
1.2.4.1. Нарезание резьбы резцами и гребенками
При нарезании резьбы на токарных станках заготовке сообщают вращение , а резцу – перемещение вдоль оси заготовки с подачей на оборот, равной шагу резьбы. Точность шага определяется точностью кинематической цепи станка, а точность профиля резьбы – точностью заточки и установки резца. Поэтому в процессе обработки токарь обычно контролирует ?????????????????????.При нарезании резьбы за несколько рабочих ходов движение поперечной подачи резца может осуществляться, например, по схемам, показанным на рис. 1.10. (а,б). При использовании схемы (а) обеспечивается лучшее качество обработанной поверхности, а при работе по схеме (б) упрощается форма срезаемого слоя, облегчается процесс резания и удаления стружки. Поэтому иногда черновую обработку выполняют по схеме (б), а последний слой срезают по схеме (а).
Рис. 1.10. – Схемы резания при обработке резьбы.
При нарезании резьбы одним резцом за несколько рабочих ходов его режущая кромка быстро притупляется и её форма искажается, поэтому рекомендуется для нарезания резьб с крупным шагом использовать 2 резца – черновой и чистовой, или же применять резьбонарезные гребенки. Благодаря уменьшению числа рабочих ходов, гребенки обеспечивают повышение производительности обработки. Недостатком стандартных гребенок является то, что их нельзя использовать для работы «в упор», т.е. для нарезания резьб, расположенных рядом с шейками большего диаметра.
Обработка резьбы на токарных станках производится обычно в следующих случаях:
При нарезании резьбы на заготовках, предварительно обточенных на том же станке, т.к. при этом сокращается вспомогательное время и повышается точность относительного расположения поверхностей.
При изготовлении точных длинных винтов.
При нарезании резьб большого диаметра или нестандартного шага и профиля, если приобретение специального высокопроизводительного инструмента не оправдывается из-за малого объема выпуска.
При нарезании прямоугольных резьб.
Увеличение производительности резьбонарезания за счет увеличения скорости главного движения резания во многих случаях оказывается затруднительным из-за сложности быстрого отвода резца, обрабатывающего резьбу, примыкающую к уступу.
В крупносерийном и массовом производствах резьбу часто нарезают на специальных полуавтоматах, обеспечивающих автоматизацию цикла многоходовой обработки. В мелкосерийном производстве целесообразно использовать станки с ЧПУ.
1.2.4.2. Фрезерование резьбы охватывающей резцовой головкой
Нарезание резьбы охватывающей головкой производится на токарно-винторезных и резьбофрезерных станках. Твердосплавные резцы 1 (рис. 1.11.) закрепляются в резцовой головке и вращаются со скоростью 150-450 м/мин. Головка устанавливается под углом к оси заготовки в соответствии с углом подъема резьбы и за каждый оборот медленно вращающейся заготовки перемещается вдоль её оси на величину шага. Наибольший эффект достигается при обработке крупных резьб.Рис. 1.11. – Схема нарезания резьбы охватывающей головкой.
1.2.4.3. Нарезание резьбы плашками и самораскрывающимися головками
При нарезании резьбы на токарно-револьверных и агрегатных станках в качестве инструмента могут использоваться плашки. Держатели плашек позволяют инструменту свободно перемещаться на небольшую величину или, как говорят, самоустанавливаться в продольном направлении. Это исключает срыв резьбы при несовпадении скорости движения плашкодержателя вдоль оси заготовки и скорости навинчивания плашки на заготовку.Основной недостаток плашек – необходимость свинчивания их после окончания нарезания резьбы, что снижает производительность и качество обработки.
При обработке резцовыми самораскрывающимися головками свинчивания не требуется и производительность значительно повышается.
1.2.4.4. Фрезерование резьбы дисковыми и гребенчатыми (групповыми) фрезами
Фрезерование дисковыми фрезами (рис. 1.12.) применяется для обработки крупных резьб при достаточно больших объемах выпуска. При этом обработка выполняется за 1-3 рабочих хода. Заготовка медленно поворачивается, а вращающаяся со скоростью главного движения фреза перемещается вдоль её оси с подачей на оборот, равной шагу резьбы.Рис. 1.12. – Схема фрезерования резьбы.
По сравнению с точением преимуществом фрезерования является более высокая производительность, возможность многостаночного обслуживания и использования рабочего невысокой квалификации.
Фрезерование гребенчатыми (групповыми) фрезами применяется для получения коротких наружных и внутренних резьб с мелким шагом.
В отличие от обработки резьб дисковой фрезой оси гребенчатой фрезы и заготовки параллельны (рис. 1.13.). Длина фрезы обычно на 2-3 шага превышает длину резьбового участка заготовки.
Рис. 1.13. – Схема фрезерования резьбы гребенчатой фрезой.
В начале обработки вращающаяся фреза перемещается в радиальном направлении и врезается в заготовку на глубину профиля резьбы. При этом за 1 оборот заготовки фреза перемещается вдоль оси на шаг резьбы (движение подачи
). Фрезерование происходит за 1,2 оборота заготовки. Причем вначале обработки 0,2 оборота необходимы для врезания фрезы, а в конце – для зачистки следов врезания.
1.2.4.5. Накатывание резьбы
Накатывание резьбы применяется в крупносерийном и массовом производствах. Помимо высокой производительности метод позволяет получить благоприятную упрочненную поверхностную структуру металла, т.к. волокна материала пластически деформируются, а не перерезаются.Резьба накатывается плоскими плашками или накатными роликами.
На плоских плашках (рис. 1.14.) имеется прямолинейная резьба (развертка резьбы) с такими же профилем и углом подъема как и у накатываемой резьбы. Резьба накатывается за один двойной ход ползуна. Число двойных ходов в минуту достигает 280.
Рис. 1.14. – Схема накатывания резьбы плашками.
Накатывание резьбы одним роликом применяется на токарных и револьверных станках и автоматах из-за односторонней радиальной силы. В этом случае возможен изгиб заготовки.
Поэтому большее распространение получило накатывание резьбы двумя роликами с радиальным движением подачи (рис. 1.15.).
Накатывание резьбы может также производиться двумя-четырьмя роликами с продольной подачей при постоянном межосевом расстоянии. По производительности накатывание роликами обычно уступает накатыванию плашками.
Рис. 1.15. – Схема накатывания резьбы роликами.
За очень редкими исключениями обработка всех видов валов строится при применении центровых станков и в этом случае технология состоит из следующих операций: отрезание заготовок, подрезание торцов и центрирование, в дальнейшем производятся токарные операции на центровых токарных станках, чаще всего на многорезцовых станках стандартного типа, после вытачивания заготовки выполняется операция рифления, а затем все шлифовальные операции, фрезерование шпоночных канавок производится чаще всего перед операциями шлифования вала.
После окончания всей механической обработки валов приходится проводить слесарную зачистку шпоночных канавок, вследствие их искажения по ширине после шлифования из-за затягивания кромок. Поэтому некоторые заводы предпочитают производить фрезерование шпоночных канавок, в особенности если выполняются канавки для полукруглых шпонок после шлифования вала. В этом случае, вследствие некоторого поднятия кромок, также приходится выполнять операцию ручной зачистки, т. е. снятие фасок, однако эта операция менее трудоемка, чем в первом случае, кроме того, уменьшается опасность порчи вала при зачистке.
Вся токарная обработка вала производится , как правило, в две установки на многорезцовых токарных станках, обтачивая за каждую установку часть вала. Кроме того, в зависимости от конструкции вала и состояния оборудования, производят еще иногда чистовое протачивание вала и несколько коротких токарных операций, носящих характер доделки, в том числе подрезки торцов выточки галтелей, канавок ц т. д.
Операция накатывания рифления зачастую производится на обычном токарном станке, при помощи одного или двух накатных роликов, укрепленных в специальной державке. Ролики производят накатывание при продольной подаче будучи прижатыми к валу в такой степени, чтобы за один проход образовывалось рифление полного профиля.
Операции шлифования производятся на обычных центровых круглых шлифовальных станках. Большинство поверхностей шлифуются при продольном перемещении изделия по отношению к кругу и лишь в отдельных случаях применяется более производительный способ шлифования широкими кругами, в соответствии с шириной обрабатываемой поверхности, при поперечных подачах.
Фрезерование шпоночных канавок производится на простых горизонтальных фрезерных станках. При изготовлении канавок для шпонок с большим успехом применяются небольшие ручные фрезерные станки с рычажным управлением. Несмотря на свою простоту и примитивность, такие фрезерные станки оказываются очень удобными и высокопроизводительными при подобного рода кратковременных операциях.
При изготовлении длинных и тонких валов перед шлифованием вводится операция правки, производимая либо на прессах с ручным или механическим приводом, либо на малых гидравлических или пневматических прессах. Контроль всех размеров в процессе производства осуществляется при помощи жестких предельных калибров и шаблонов. За исключением проверок на биение и при операции правки индикаторные приспособления почти не применяются.
Недостатки описанной технологии сводятся в основном к следующему :
1) применяемое оборудование и способы изготовления обладают невысокой производительностью и отстали от современных способов массового производства;
2) в качестве исходного материала применяется в большинстве случаев сталь в виде черных некалиброванных прутков, что приводит к необходимости протачивать также и среднюю часть вала, имеющую наибольший диаметр. Одно это обстоятельство, увеличивая трудоемкость обработки приводит к потерям материала, минимум в 15-20%;
3) операции отрезки заготовки, протачивания торцов и засверливания центров производятся на обычном оборудовании, предназначенном для работы в серийном производстве и поэтому обладающем невысокой производительностью, при сравнительно большом удельном весе ручного вспомогательного времени. Так, например, засверливание центров чаще всего выполняют на вертикальных сверлильных станках в два перехода, т. е. каждую сторону вала самостоятельно, поворачивая вал;
4) токарные операции тоже производятся на недостаточно производительном оборудовании универсального назначения. Особым недостатком применяемых многорезцовых станков является их малая приспособленность к быстрой смене настройки с одного типоразмера вала на другой, что приводит к большим потерям времени при переналадках. Особо следует остановиться на применяемом способе производства рифления. При существующем способе накатывания на токарных станках предварительно проточенных валов невозможно выдержать достаточно точно размеры диаметров и избежать недопустимых колебаний в размерах и отступлений от необходимой прямолинейности рифления. Последнее требуется для правильной посадки сердечника ротора (якоря). Наконец, практикуемый способ шлифования узкими кругами при продольной подаче является малопроизводительным. Нужно отметить, что, как правило, даже там, где это вполне возможно и рационально, как, например, при шлифовании шеек, станки не снабжаются приспособлениями для измерения шлифуемых размеров в процессе работы, т. е. на ходу станка, а для проверки размеров станок останавливается.
Следует указать, что очистка и промывка вала в процессе обработки, в частности перед окончательной шлифовкой, и в готовом виде в действующей технологии не предусматривается. В таком виде выглядит самый распространенный процесс центровой обработки валов.
Существует, однако, и совершенно отличный процесс бесцентровой обработки валов , обладающий рядом преимуществ по сравнению с центровым способом и приводящий к значительному уменьшению трудоемкости обработки. Этот процесс с большим успехом применяется при изготовлении валов в производстве автотракторного электрооборудования.
При бесцентровом способе исходным материалом обязательно должен быть калиброванный и тщательно выправленный пруток . Первая операция - полное вытачивание вала производится на прутковом автомате. Для того чтобы при протачивании избежать искривления длинных валов, последние поддерживаются при помощи роликовых люнетов. В последующие операции обработки валов, производится предварительное шлифование на бесцентровых шлифовальных станках, причем первые операции выполняются при сквозной подаче изделий, на двух-трех последовательно стоящих станках.
В дальнейшем производится накатывание рифления . Эта операция в производстве автотракторного электрооборудования выполнялась отлично от того, как это делается на других электромашиностроительных заводах. Для обеспечения правильности размеров диаметров и соблюдения одинаковой прочности запрессовки различных валов последние перед накатыванием обязательно проходили шлифование по своему диаметру при этом размеры выдерживались по третьему классу точности. Операция накатывания выполняется на мощном резьбонакатном станке горизонтального типа. Наряду с очень высокой производительностью этого способа накатывания, обеспечивается также полная прямолинейность рифления, что в некоторых конструкциях машин является безусловно, необходимым.
Действительно, если на рифленый вал производится на прессовка сердечника ротора, то отдельные его листы в процессе прессования неизбежно стремятся следовать форме и направлению рифления. Поэтому, если рифления имеют хотя бы очень незначительные искривления и идут по крутой спирали, то все пазы сердечника должны повторить кривизну рифлений.
Известно, что искажения в форме пазов совершенно недопустимы, особенно при машинной обмотке якоря. Не следует думать, что если якорь электрической машины должен иметь косые пазы, то и рифление может иметь соответствующий наклон. В действительности у всех без исключений конструкций якорей и роторов рифление должно быть возможно более прямым, а необходимый скос пазов получается в процессе запрессовки применяя соответствующие наклонные направляющие ножи в приспособлении для прессования.
Часто отсутствие на заводе возможности изготовить валы с абсолютно прямым рифлением вынуждает пользоваться другими, значительно более дорогими способами крепления сердечника на валу и, в частности, применять для этой цели шпонки.
Для рифления валов необязательно применять станки с плоскими плашками и поступательным рабочим ходом, а можно с успехом пользоваться и другими типами резьбонакатного оборудования. После накатывания рифления валы проходят шлифовальные операции на бесцентровых шлифовальных станках, частично при продольной, но, главным образом, при поперечной подаче.
Одновременно обязательно шлифуется также и наружный диаметр рифленой поверхности с целью выдержать размер в пределах третьего класса точности и несколько притупить верхушки отдельных зубчиков, обеспечив тем самым одинаковую величину натяга и высокое качество прессового соединения.
Способ бесцентровой обработки требует меньшего числа операций чем центровой , и, в частности, отпадают все заготовительные операции — отрезание заготовки, протачивание ее торцов и центрирование. Применяемое в этом случае оборудование обладает также более высокой производительностью. Прутковый автомат для вытачивания вала требует меньшего обслуживания со стороны рабочего, чем многорезцовый токарный станок. Качество валов, полученных обоими способами, примерно одинаково. При бесцентровой обработке валов, имеющих несколько уступов по длине, величины их биений могут быть выдержаны в пределах требуемых допусков.
Возможно, Вас так же заинтересует:
Рабочая программа автор матвеева по физической культуре
Учебная программа по предмету Образовательная программа по предметам
Программы. Практикум для учителя. Как написать рабочую программу по фгос ООО Программы по предметам общеобразовательных школ
Матвеев программа по физической культуре 1 11
Презентация на тему "сергий радонежский"